
4 minute read
Expanding fibre technology Buckeye Technologies
EXPANDING FIBRE TECHNOLOGY
Buckeye Technologies is a global leader in the manufacture of speciality and non-woven fibre materials. Philip Yorke reports on a company that continues to extend its range of innovative products and set new standards in sustainable production.
Buckeye Technologies was founded in Ohio, USA in the early 1900s as the cottonseed crushing division of Proctor & Gamble. Today Buckeye is an independent public company that leads the field in the development and manufacture of value-added, cellulose-based products for high-end niche markets worldwide. The company’s unrivalled expertise in polymer chemistry and fibre science enables it to offer the broadest range of products and most innovative solutions available on the market anywhere in the world.
Today the company is headquartered in Memphis, Tennessee. Over the years it has established a major presence in Europe. The centre for its European operation is based at Steinfort in Germany, where the company has two air-laid non-woven production lines which together produce more than 35,000 tonnes a year of speciality non-woven fibre products.
Buckeye Technologies Inc. operates six modern manufacturing plants worldwide and employs more than 1000 people, of which 250 are based at its Steinfort facility. The company is listed on the New York stock exchange and in 2011 recorded sales of more than $1 billion.
Focus on innovation and sustainability
The demand in Europe for baby wipes, kitchen and bathroom cleaning wipes, moist toilet tissue and femcare products continues to see strong growth. All of these consumer products are based on the air-laid non-wovens technology, for which the Steinfort plant is famous. Buckeye is the only manufacturer in the world that provides cellulose-based products made from both wood and cotton, using advanced wetlaid and airlaid technologies. This combination enables the company to offer a broader range of cellulose-based speciality products than any other company in the world.
Buckeye Technologies is the leading supplier of unique fibre solutions to a broad array of global markets and the company is clearly focused on developing new, optimised fibre solutions particularly for the ‘absorbency’ market and for industrial applications. The company’s ongoing commitment to optimising fibre product technology has resulted in the launch of its ground-breaking customised fibre: Ultra Fiber500®. This was developed for industrial applications and is a revolutionary, custom-modified cellulose polymer which is used in the concrete industry for minimising possible cracking in concrete. In addition, it provides a smooth and blemish-free surface that readily accepts decorative finishes such as stains and dyes.
Buckeye Technologies also leads the pulp and paper industry in its achievements in energy saving and the sustainable management of its forestry operations. At Steinfort and other individual facilities, the company’s sustainability initiatives are making a significant difference. As a certified practitioner in the field of sustainable forest management, Buckeye contributes to the renewability of its forest resources and the continuing balance of the carbon cycle.
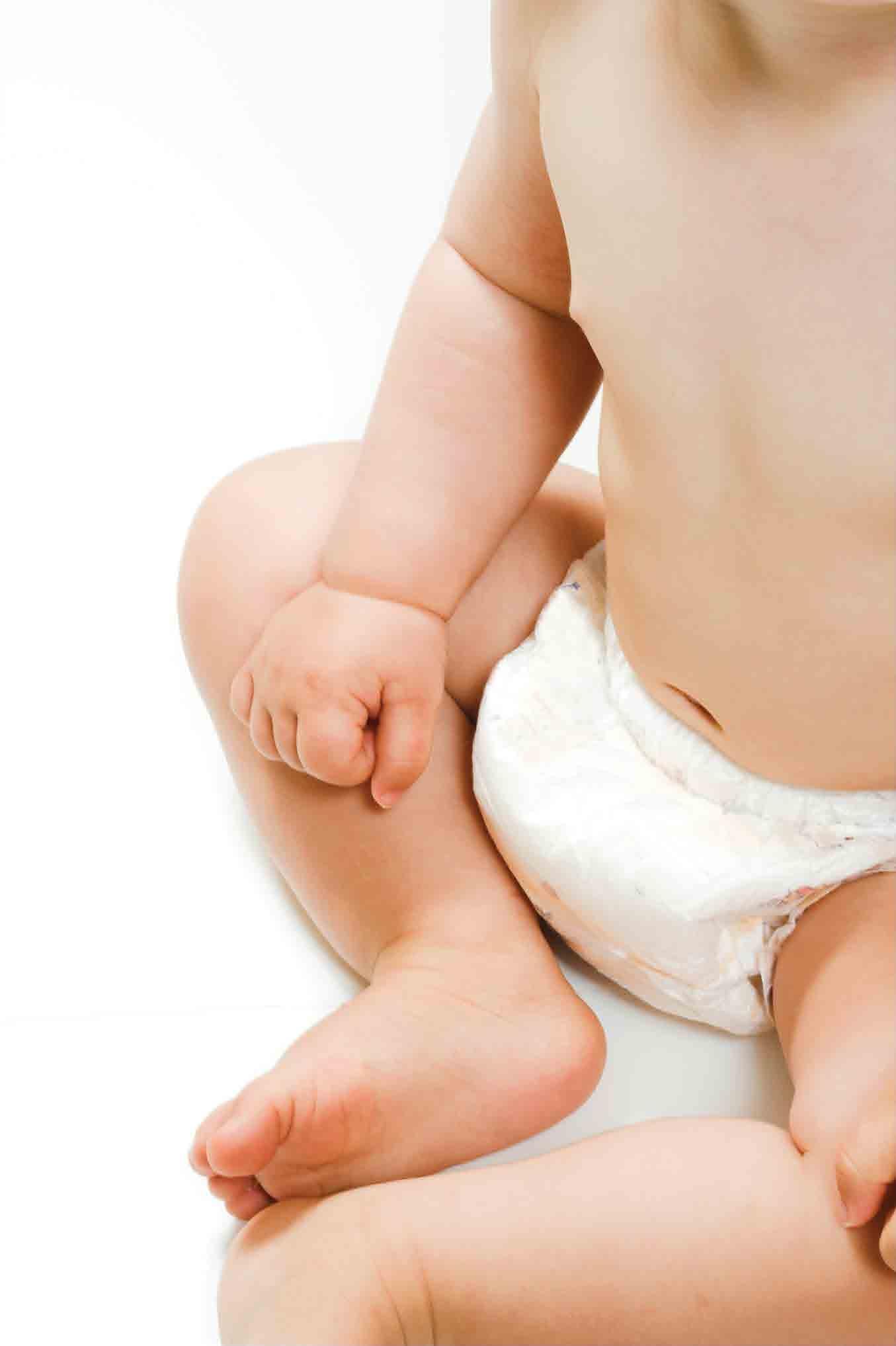
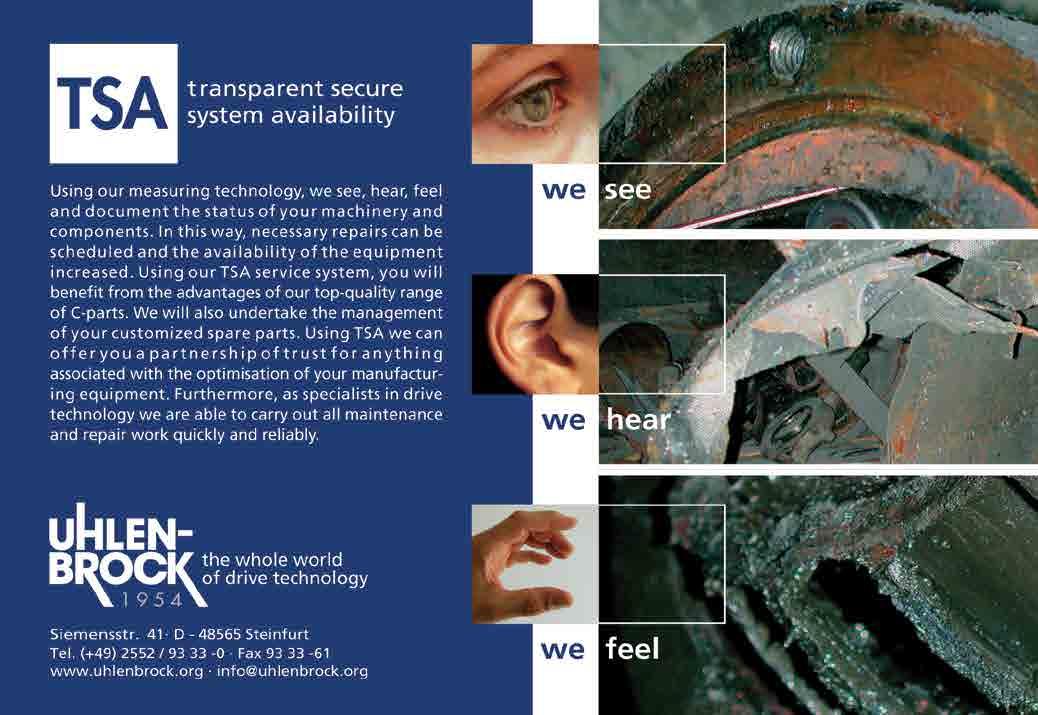
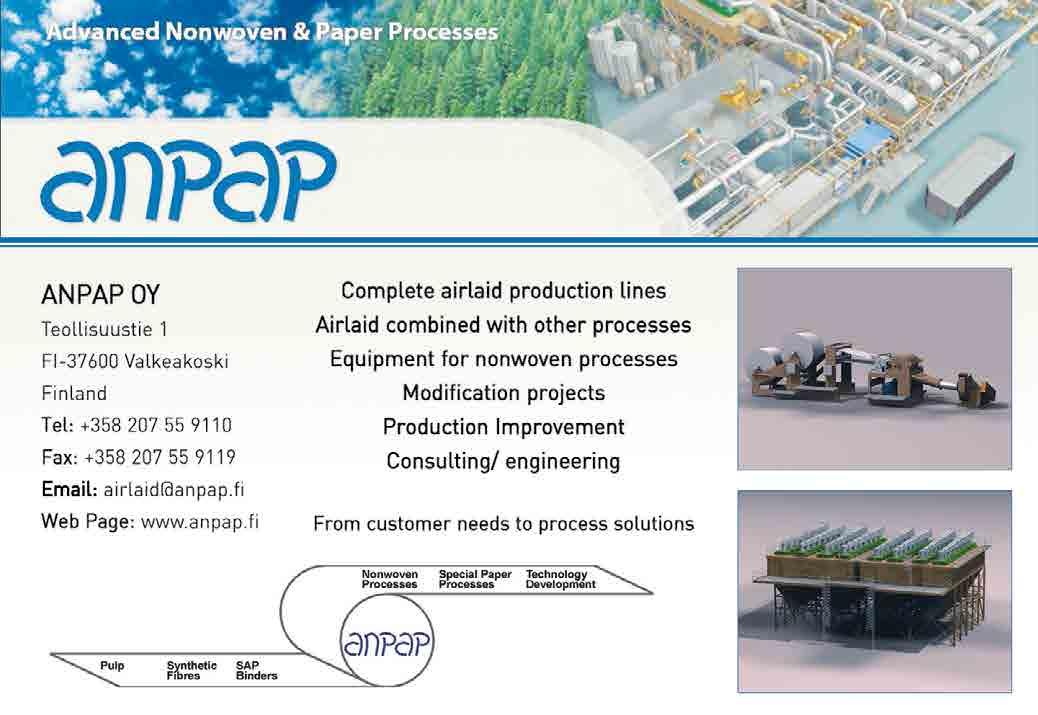
Buckeye’s Steinfort plant now manufactures products under the FSC (Forest Stewardship Council) and the PFC chain of custody certification. In fact, since 2006 the company has reduced its reported air emissions by almost 20 per cent while reducing overall waste products by a further 15 per cent, and reducing the quantity of effluents from its facilities by 5 per cent. John Crowe, chairman and CEO of Buckeye Technologies, commented: “We have embarked on a sustainability strategy that embraces the importance of protecting the environment and resources for future generations, while leveraging long-term business and shareholder value.”
Improving the quality of semi-finished products
The entire output of the Buckeye Steinfort facility is based upon semi-finished products, which are delivered to converters for branded and non-branded products. The company operates three state-of-the-art airlaid non-woven plants in total, two of which are located in North America and the other of which is based at Steinfort. The German facility is focused on the requirements of the European market, especially for products such as kitchen and bathroom cleaning wipes, and femcare products.
However, it is the fluff pulp that is used in products such as nonwoven materials for femcare products, wipes, table-top items, food pads and incontinence products that is seeing the strongest growth in Europe. These product groups are also benefiting from the company’s ongoing investment in R&D. Fluff pulp is one of the optimised grades of value-added products produced by the company. High quality fluff pulp is manufactured at its extensive facilities in Florida, before being freighted to Germany in a wholly integrated process.
Continuous investment in technology and innovation has led to a product that is superior in quality to any other similar product on the market. The raw material used in the manufacturing process also has a big influence on the physical properties of the airlaid non-woven material and as a result, Buckeye’s superior fluff pulp optimises fluid management in its diverse range of product applications.
Enhancing both its productivity and quality is the company’s latest investment in new plant and technology at its Florida based ‘Foley’ operation. The cost of the new, cutting-edge facility is around $80 million and will increase high-end speciality wood pulp capacity by over 42,000 tonnes. The all-new plant is scheduled to be fully operational by December 2012, and the entire investment will be funded from cash flow generated from Buckeye’s global operations. n
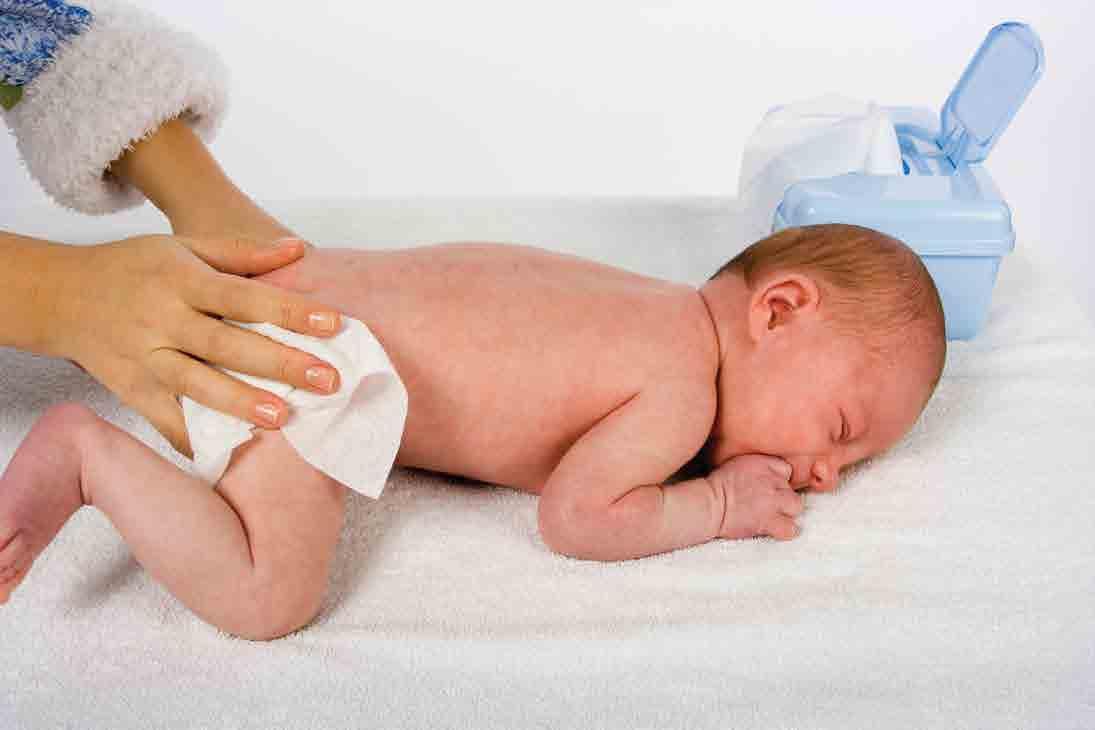
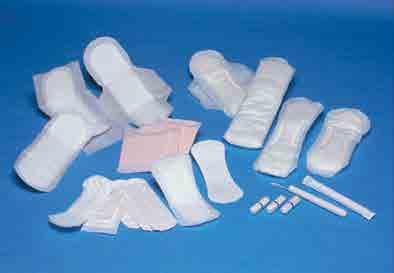

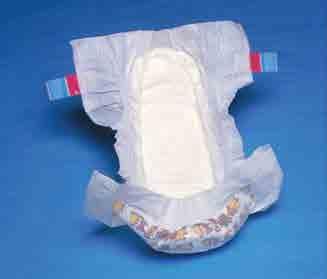