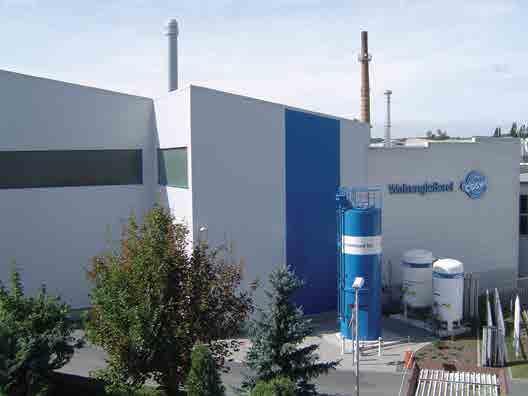
4 minute read
Optimisation at every stage of production Coswig
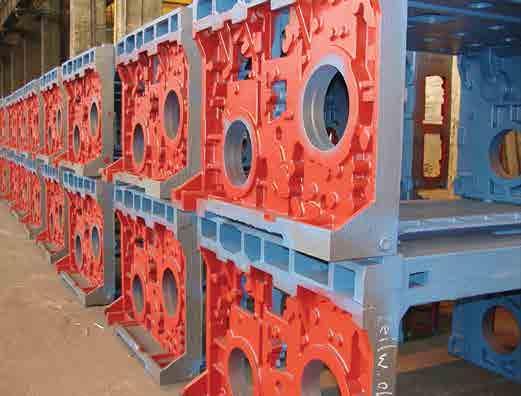
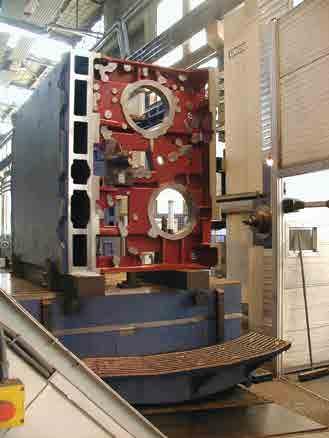
OPTIMISATION AT EVERY STAGE OF PRODUCTION
Walzengiesserei Coswig GmbH is a leading European foundry that specialises in steel rolling, hand moulding and machining for a diverse range of industries and applications. Philip Yorke talked to Marko Schulter, the company’s sales director, about its major investments in new plant and further expansion in the world’s fastest growing markets.
Coswig foundry was founded in Germany in 1892 and through consistent investment in new plant and technology has grown to become a pre-eminent, European mill foundry. In 1996 the company was acquired by the DIHAG Group, which further leveraged its competitive edge and added to its overall R&D capabilities.
Today, based upon its comprehensive and sophisticated manufacturing capabilities, the company can offer a high level of flexibility, which in turn allows it to react quickly to the changing needs of the market and its customers. Optimisation of all Coswig’s stateof-the-art production processes has been the key to its on going success. Outstanding mould quality is supported by a variety of mechanical and metallographic tests at the company’s own measurement, analysis and simulation programme facilities near Dresden. Coswig foundry’s diverse range of products cover all customer-specific requirements for specialised products such as high quality steel rolls and rings, pistons and plungers and hand-moulded castings for an infinite range of industrial applications.
Innovation and quality driving sales
Throughout its long and successful history the company has made innovation, quality and customer service its key priorities. In order to maintain the high standards that are synonymous with Coswig, it continues to invest heavily in the latest machinery and technology.
Schulter said, “We are a privately owned company which gives us a competitive edge when it comes to providing customer service and flexibility. We operate a continuous programme of improvement in order to stay at the top of our profession. In 2009 we invested more than €30 million in the foundry to increase manufacturing capacity and this was achieved with the latest state-of-the-art equipment. This investment boosted our production to over 60,000 tonnes per year, which virtually doubled our turnover. Most of our products are in the middle to big range of castings with more than 30 per cent of our orders requiring products in the 50 tonnes and upwards range.
“At Coswig we operate two different divisions. The first is dedicated to the steel
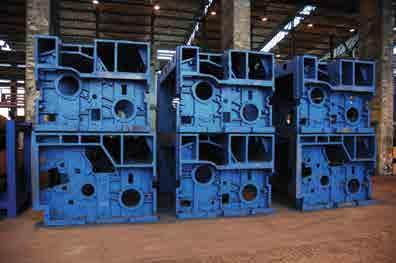
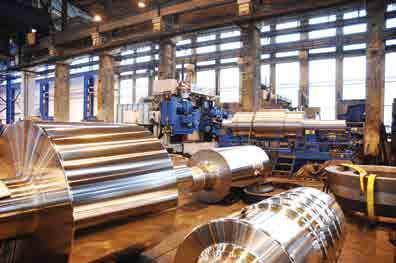
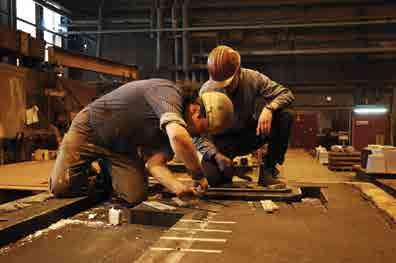
industry with products for the steel rolling sector and most of these products are exported to European countries, the USA, the Middle East, Russia and Asia. Our second division is focused on specialised castings for high-growth industries such as those involved in the renewable energy sector and the mining industry. In the past over 90 per cent of our production has been for our domestic market; however, we have been very successful over recent years in our drive to extend our export levels. Today exports represent more than 50 per cent of our sales.”
Schulter added, “Looking to the future we see that growth is coming from non-traditional market sectors such as renewable energy, gas and oil from countries like Brazil, India and Arab countries as well as from the Chinese market. For the next 10–15 years the market for offshore and onshore ‘wind farms’ will be the main driver for sales of our high quality rotor shafts which have to be made to very strict metallurgical criteria and to very tight tolerances. We are increasingly working in close partnership with our customers to optimise design, performance and energy-saving processes. We employ more than 250 people, including our R&D facility, here in Coswig and innovation can be clearly seen in all aspects of our business activities.”
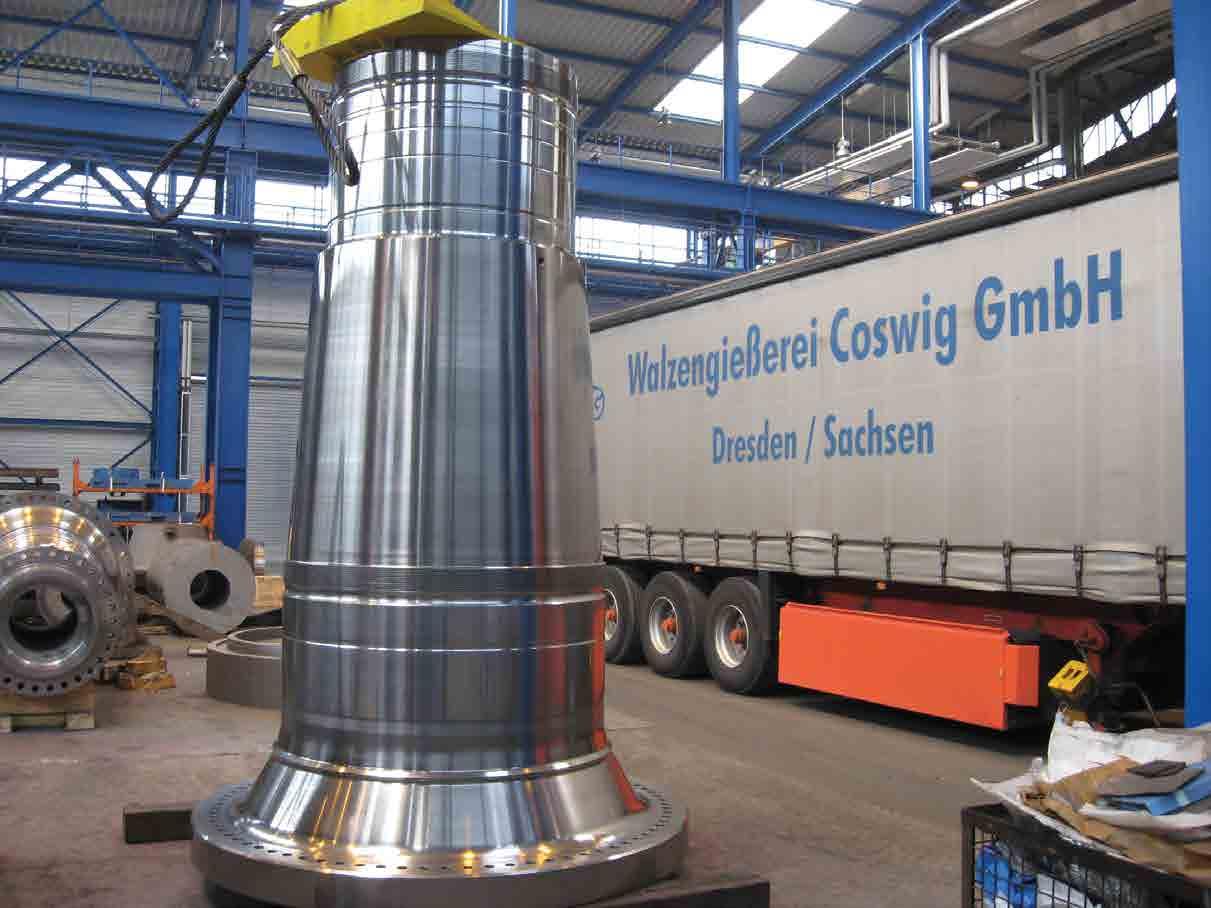
Quality assured
German quality speaks for itself but in Coswig’s case it is further enhanced by the certification of its energy management system according to DIN EN 16001 for the sustainable preservation of the environment. Quality is also guaranteed in many other areas and to ensure its continuing market success the company has consistently upgraded and added to its quality management systems, which cover all aspects of manufacturing, from receipt of the initial order to delivery of the finished products.
Coswig foundry’s continuous improvement in quality is achieved by the consistent involvement of its employees and with the company’s advanced testing, evaluation and production methods. The extensive range of equipment available at Coswig’s testing laboratories includes optical emission spectrometers, carbon-sulphur machines, universal-train pressure and bending machines as well as laboratory heating facilities for sample and heat treatment testing. The company also operates a sand laboratory for the determination of foundry sand characteristics and a metallographic laboratory for hardness and micro-hardness testing procedures.
Other in-house research facilities include ultrasonic and magnetic particle testing equipment and electronic data and imaging archiving services. In addition, it is envisaged that a process of continuous improvement in environmental protection will soon extend to the company’s suppliers and service providers. At Coswig, environmental considerations form important criteria in all decision-making and development processes. Coswig foundry is fully committed to its environmental objectives and successfully applied for the strict environmental standard ISO 14001 in 2005, which has been in operation ever since with the granting of its annual TUV standard certification. n
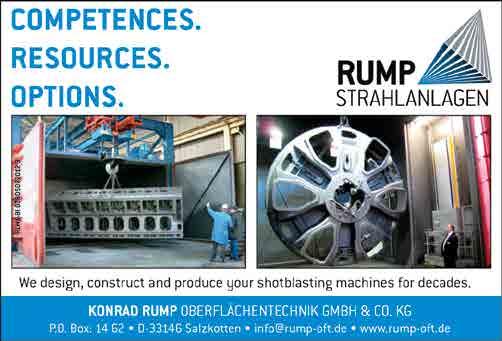
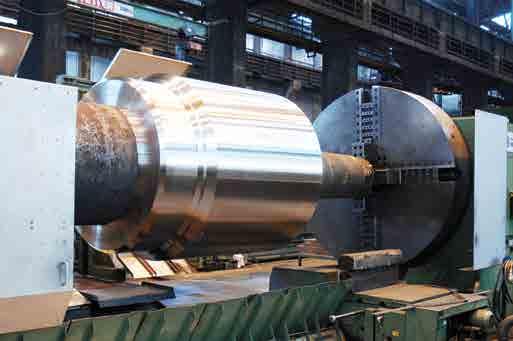
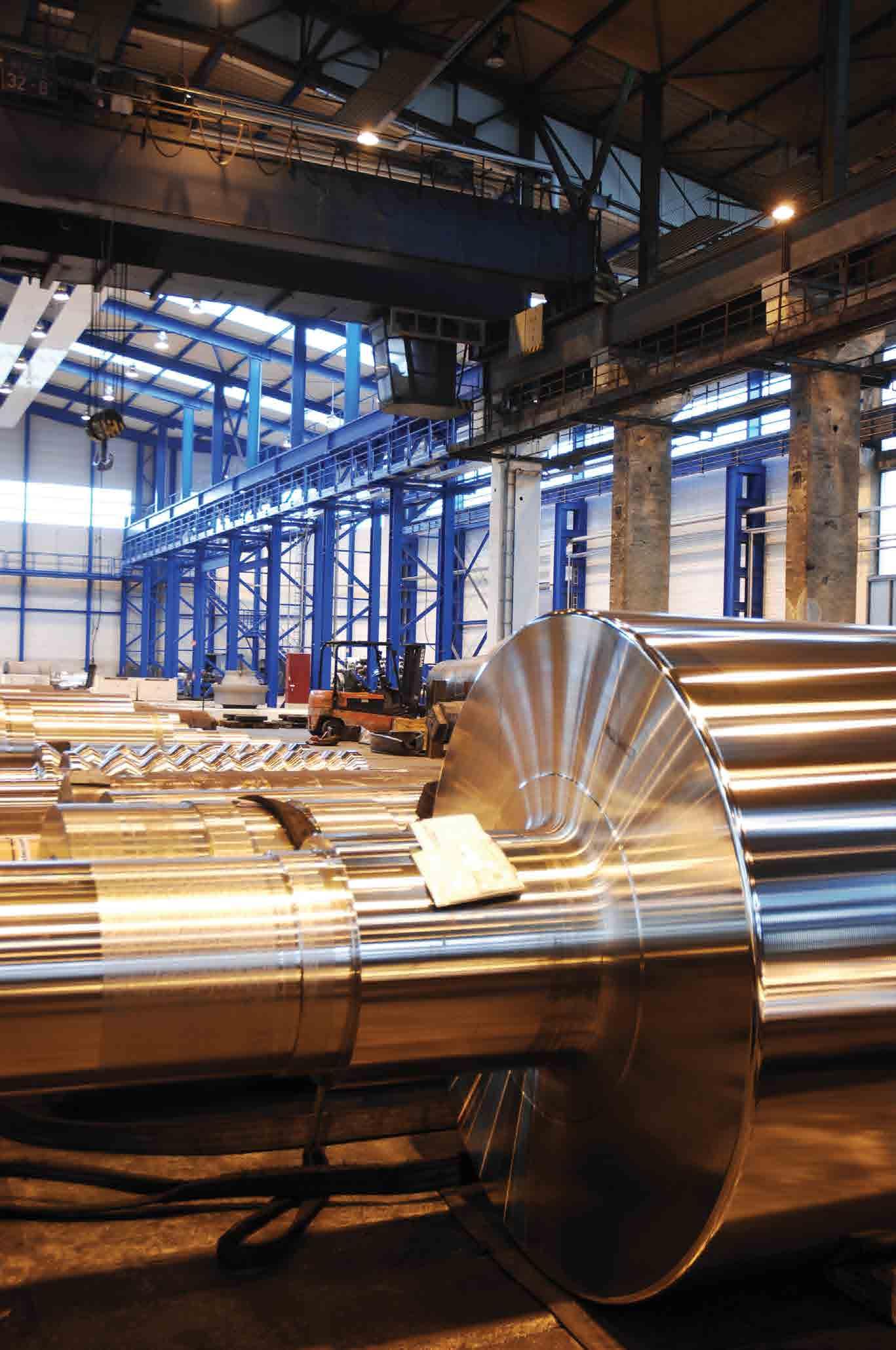