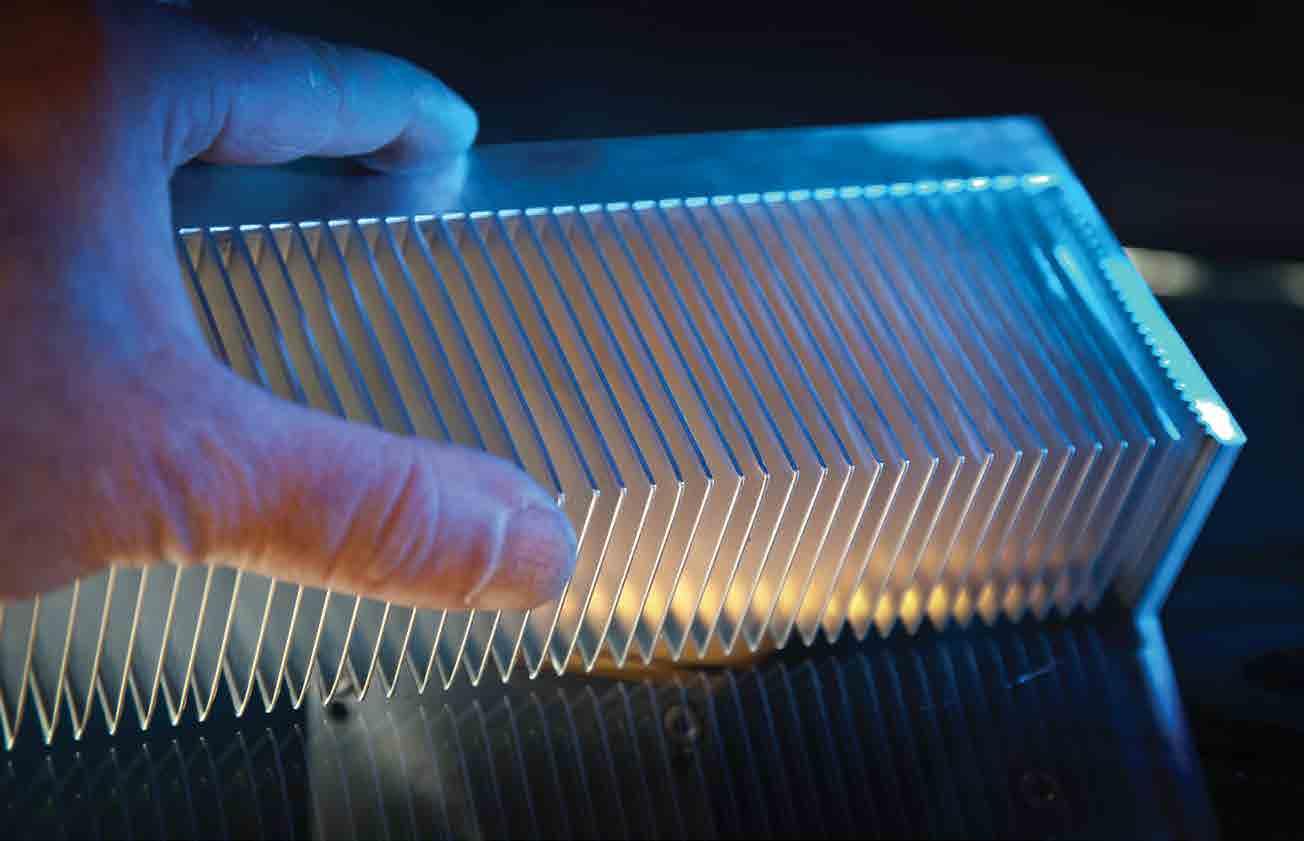
4 minute read
Masters of complex extrusion technology
Martinrea Honsel is a technology leader in the production of complex aluminium profiles. Philip Yorke talked to Hans Juergen Schulte, the company’s sales manager, about its development of novel alloys and unrivalled capabilities for the production of complex lightweight geometries and cost-effective solutions.
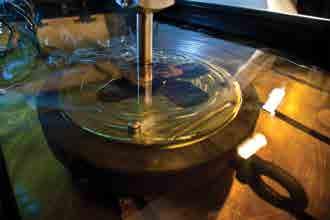

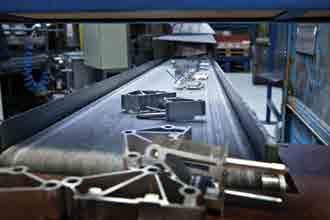

Martinrea Honsel can trace its roots back to 1908 when Fritz Honsel founded “Fritz-Honsel Gravieranstalt und Formenmacherei” in Werdohl, Germany. Initially the company focused on the manufacture of fabricated permanent mould and high pressure die castings before making the strategic decision to move also into extrusion profiles. It was in 1958 that Honsel’s first state-of-the-art extrusion plant was built on its original production site in Meschede, Germany.
Since those formative years the company’s reputation for high-quality, innovative extrusions has grown and has attracted many of Europe’s leading OEMs, as well as their tier-one and tier two suppliers. Today, after the majority acquisiton of Honsel by Martinrea International Inc. in 2011, Martinrea Honsel’s extrusion plant employs around 250 people and in 2012 recorded sales of more than €70 million.
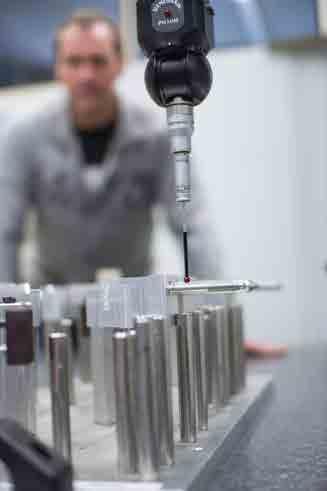
Delivering a competitive advantage
Today Martinrea Honsel is a technology leader in the development and production of full, semi-hollow and hollow aluminium profiles. These include extruded profiles with very complex geometries, close tolerances and special mechanical properties. The company works in close partnership with its customers in order to develop the most energy-efficient, lightweight engineering solutions. With many decades experience in advanced extrusion technology, Martinrea Honsel offers unique know-how that provides its clients with the competitive advantage they need to remain at the forefront of their business sector.
Mr Schulte said, “Over 60 per cent of our business is dedicated to supplying the automotive industry’s leading OEMs and their contractors. However, our other two business units are also very important to us, and both the mechanical engineering and electronic divisions are continuing to see consistent growth. Our company’s speciality is its ability to achieve ever finer tolerances and enhanced precision in lightweight extrusions, while at the same time developing new technologies that optimise the performance of our products. We are a relatively small producer by international standards with a capacity of around 18,000 tonnes per year. However, this must be seen in context as we do not compete with the big, high-volume standard-component producers.
“As technology leaders in our field we are niche providers at the top end of the market. We offer our customers in-depth knowledge and unique, high-tech facilities, as well as specialist know-how that provides them with exceptional results. For example, we have been the partner for the development of the profiles for the space frame technology for the Audi A8 which meant the development of a revolutionary crushable new alloy designed to meet the company’s latest challenging specifications. We deliver smaller quantities

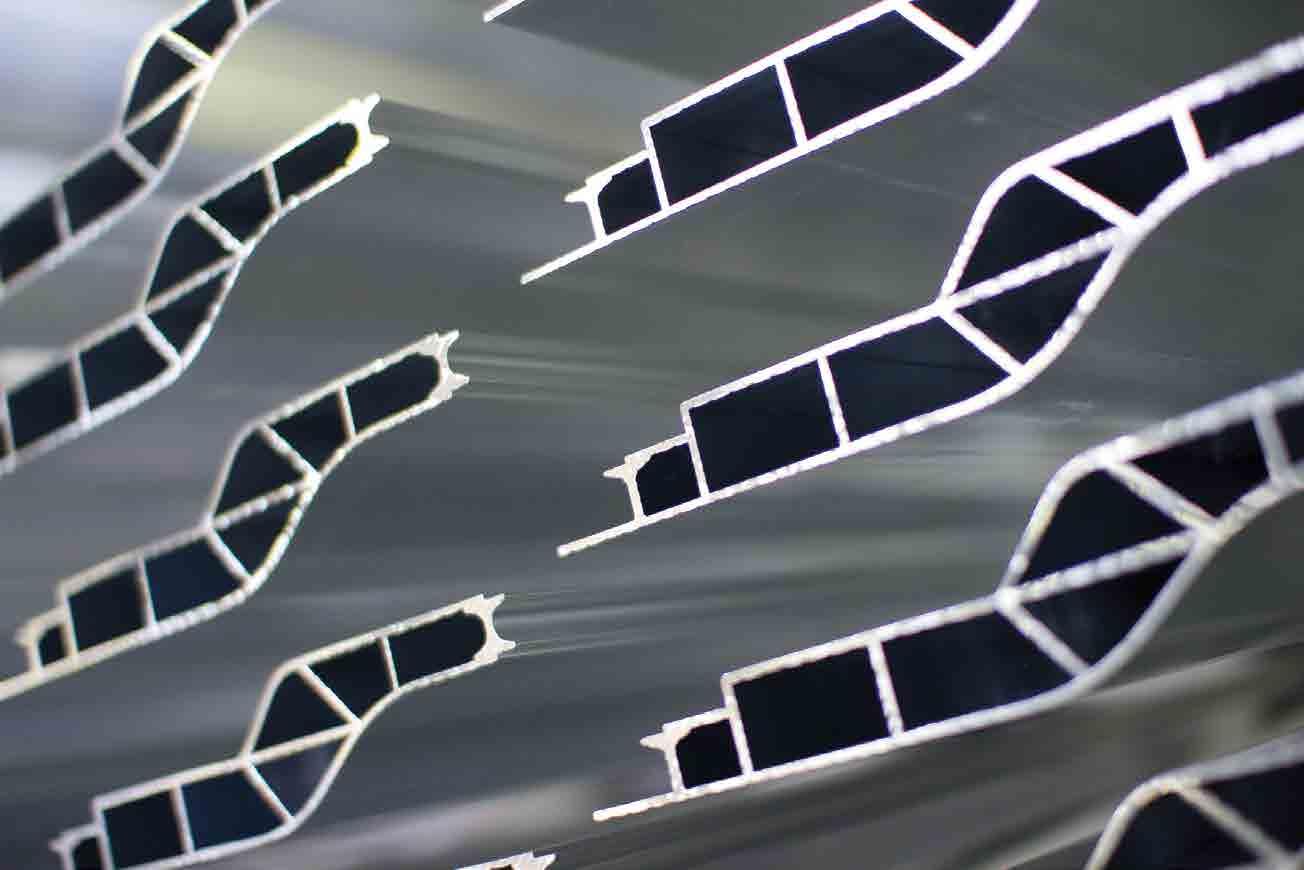
for specialised markets and are therefore able to develop more sophisticated parts and solutions. In addition, we have our own die shop for extrusion dies to ensure that we have the knowledge of die construction in house as an essential supposition for the production of high-quality extrusions.
“We work very closely with our clients, our partners and our key suppliers. These include suppliers such as Trimet of Essen or Alumet in Bludenz, with whom we have developed many advanced multi-functional alloys to meet individually demanding specifications. In our mechanical engineering sector we have reduced tolerances for example for linear rails from 0.2 mm to smaller than 0.1 mm. For Volkswagen we developed another very special alloy called EN AW 2618 for their TDi diesel engines. Another example of our innovative research is the development of highperformance heat sinks with a very difficult relation of 18 : 1 between height and distance of the fins. We are able to present the heat sink as a one-piece extruded component. The profile therefore achieves outstanding cooling performance, is light and is more cost-effective than any previous solution.
“We strongly believe that a programme of continuous investment in new plant and technology is vital for the well-being of our company and for our customers, in order to maintain a competitive advantage. We recently invested in the latest, state-ofthe-art furnace for heating billets which offers greater efficiency and flexibility. With the continuing recovery of the automotive industry and the manufacturing sector in general, we see a very positive future ahead for Martinrea Honsel Extrusion Plant.”
Setting new standards in eco-friendly efficiency
The global demand for safer, more powerful and increasingly economical forms of transportation continues to put pressure on the automotive industry’s manufacturers. The reduction in CO2 emissions remains the dominant issue across all manufacturing industries, in particular in the automotive sector. The greatest challenge today is the need to drastically reduce pollutant emissions, but this is against a background of a fast rising number of vehicles in use worldwide. The contribution from Martinrea Honsel lies in its ability to create innovative lightweight engineering solutions that significantly improve the efficiency of modern cars and trucks.
Martinrea Honsel has already proved that its extruded light metal solutions can meet the increasing demands and pressures facing modern vehicle manufacturing for more eco-friendly solutions. With its broad range of alloys, the company fulfils the latest industry requirements such as high strength, ductility, thermal conductivity and machinability. This all adds up to Martinrea Honsel being uniquely qualified to deliver the optimal outcomes and specifications needed by industry today. n
For further details of Martinrea Honsel’s innovative aluminium extrusion products and services visit: www.martinrea-honsel.com
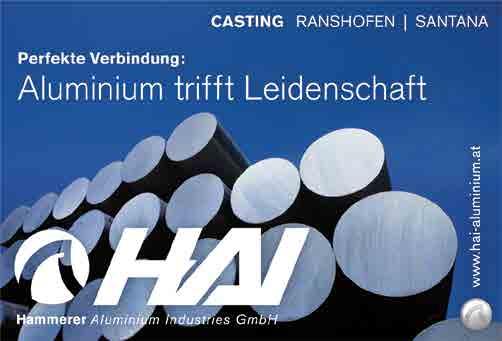