
6 minute read
Cutting-edge aerospace technology Asco
Asco Industries is a global leader in the design and manufacture of wing movables (Slat & Flap support systems) for commercial, regional and military jets. Philip Yorke talked to Ivan Remels, the company’s CCO, about its latest investments in the US, its drive to enter new market sectors and strategy for further global expansion.
CUTTING-EDGE AEROSPACE TECHNOLOGY
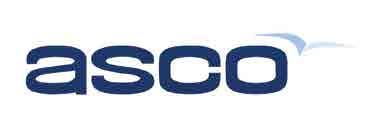
Asco Industries is a global leader in the design and manufacture of wing movables (Slat & Flap support systems) for commercial, regional and military jets. Philip Yorke talked to Ivan Remels, the company’s CCO, about its latest investments in the US, its drive to enter new market sectors and strategy for further global expansion. Asco Industries was founded by Emile Boas (senior) in Zaventem, Belgium in 1954 and began life as a supplier of components for a broad spectrum of military applications. However, when his son Roger Boas took over the management of the company it turned its focus towards the aerospace industry which today is the only market sector that the company serves. Currently the company is managed by Christian Boas, the third generation descendent of the founder. His leadership has heralded a major expansion programme for the company. As a result, Asco Industries has made a major leap forward supplying its products to virtually all of the biggest and newest commercial jetliners, such as the Airbus A380 and A350XWB, the Boeing 787 ‘Dreamliner’, Bombardier ‘C-Series’ and Embraer E-Jets. In addition to winning contracts on all commercial Airbus (320) singleaisle and Boeing (737) narrow-bodies, as well as the larger business jet manufacturing companies such as Bombardier, Dassault and Gulfstream.
Today Asco Industries is continuing to set itself ambitious targets for future growth and expects to almost double its turnover in the next couple of years. This means the $300 million annual turnover it achieved in 2011 will increase to over half a billion US$ by end of 2015. Staff levels will also increase importantly from the 1,300 people currently employed at its key manufacturing sites in Belgium, Germany and Canada. Innovative technology leading the field
Asco is constantly looking for new and innovative high-tech solutions to support its customers’ own research and development programmes. In partnership with its clients and academia, the company has produced countless award winning products. This strong partnership approach has helped Asco to become a major player within the International Aerospace community. The company places a high priority on building strong relationships with its customers in a way that benefits all parties and enables it to deliver cutting-edge, high quality, cost-effective solutions.
Asco is a third generation family business and, as such, the company has always been aware of its responsibilities towards its employees, customers and suppliers, as well as to the wider community. This broad culture of commitment has helped Asco to build steadily upon its leading global position
in ‘high-lift’ wing devices, movables deployment mechanisms and support systems for today’s modern jetliners. The company is very committed to the continuous development of new technology to improve the aerodynamics of future aircraft in a way that results in substantially enhanced performance, greater fuel economy and reducing its overall ecological footprint.
Remels said, “Our ability to produce in high performance/speed, very complex, high-precision aircraft components from high-strength materials sets us apart from our competitors. This is because such hard metals, primarily titanium, are very difficult to machine to the tolerances required. In fact last year our consumption of titanium material (forgings and plate) solely for the aerospace industry exceeded 1,000 tons, making us – beside engine applications – a world leading user of this unique raw material. Furthermore, as composites are featuring more and more in new aircraft design, these need to be married successfully with metal components. Favourably for us, this is perfectly doable with titanium, not so evident with more conventional metals and alloys. Such new interface and hybrid technology will keep ASCO well ahead of future competitors and enhances our status as the supplier of choice in our sector.”
Remels added, “We are not only focussed on the design and build of critical parts for wings of mainly commercial and regional jets, but also heavily involved in build-toprint sub-assemblies for landing gears and aerostructures. Lately we are fast extending our global reach and presence. This is especially evident in South America where ASCO has been selected as partner for the Wing Movables of the E2 second generation of E-Jets for Embraer. We will provide them with advanced technology, tailor-made wing flap and slat support mechanisms. Our Canadian subsidiary moved successfully into the market segment of military aircraft, supplying key
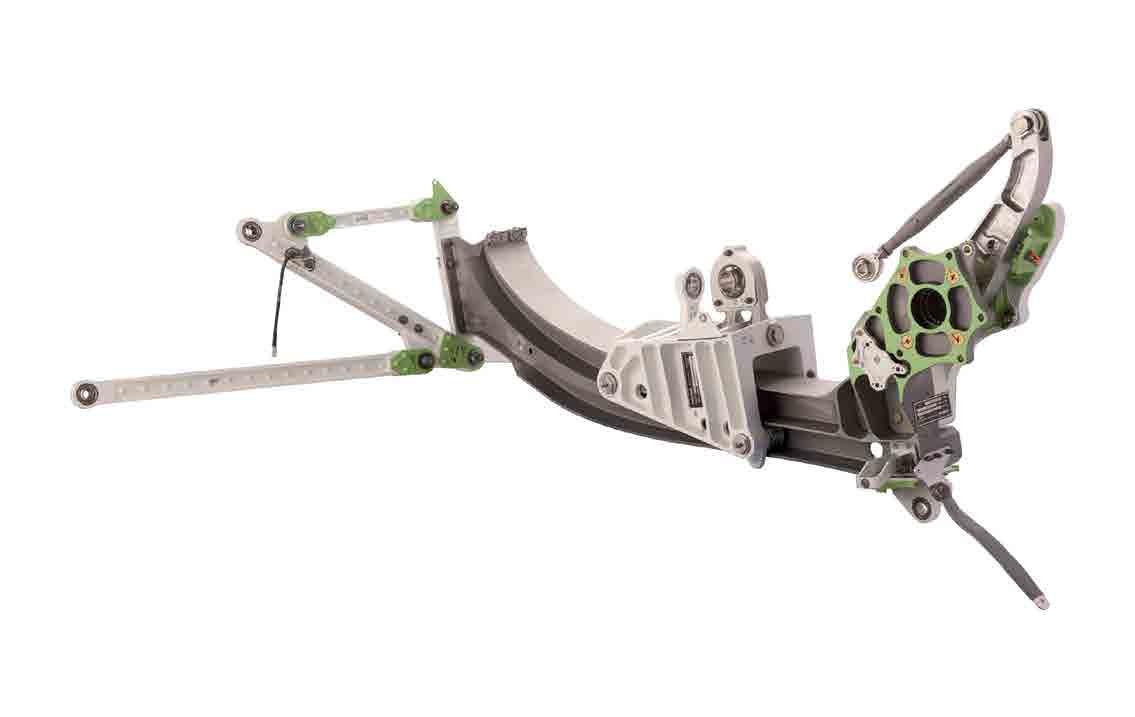
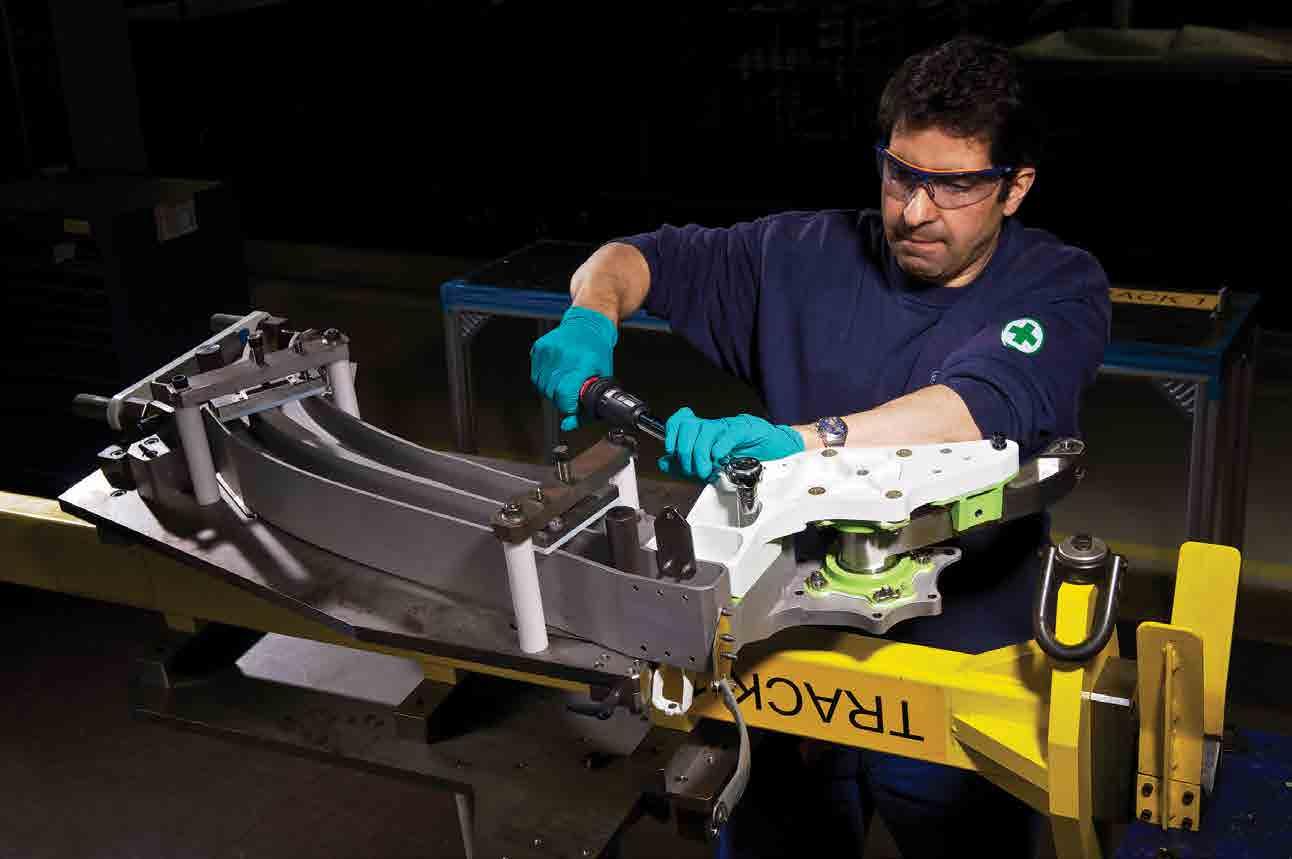

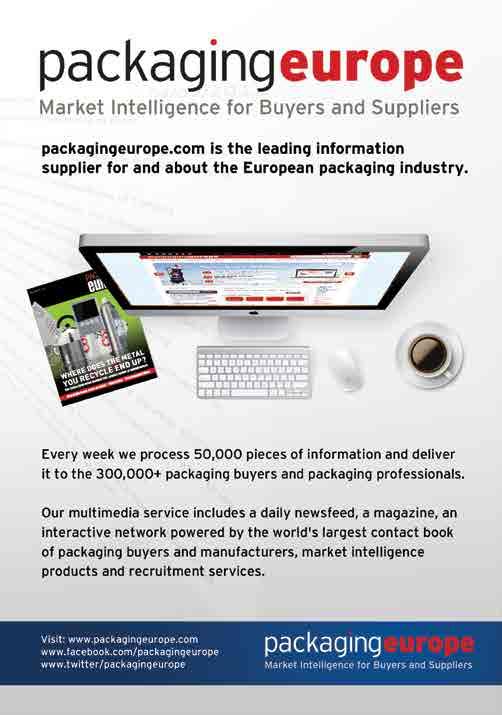
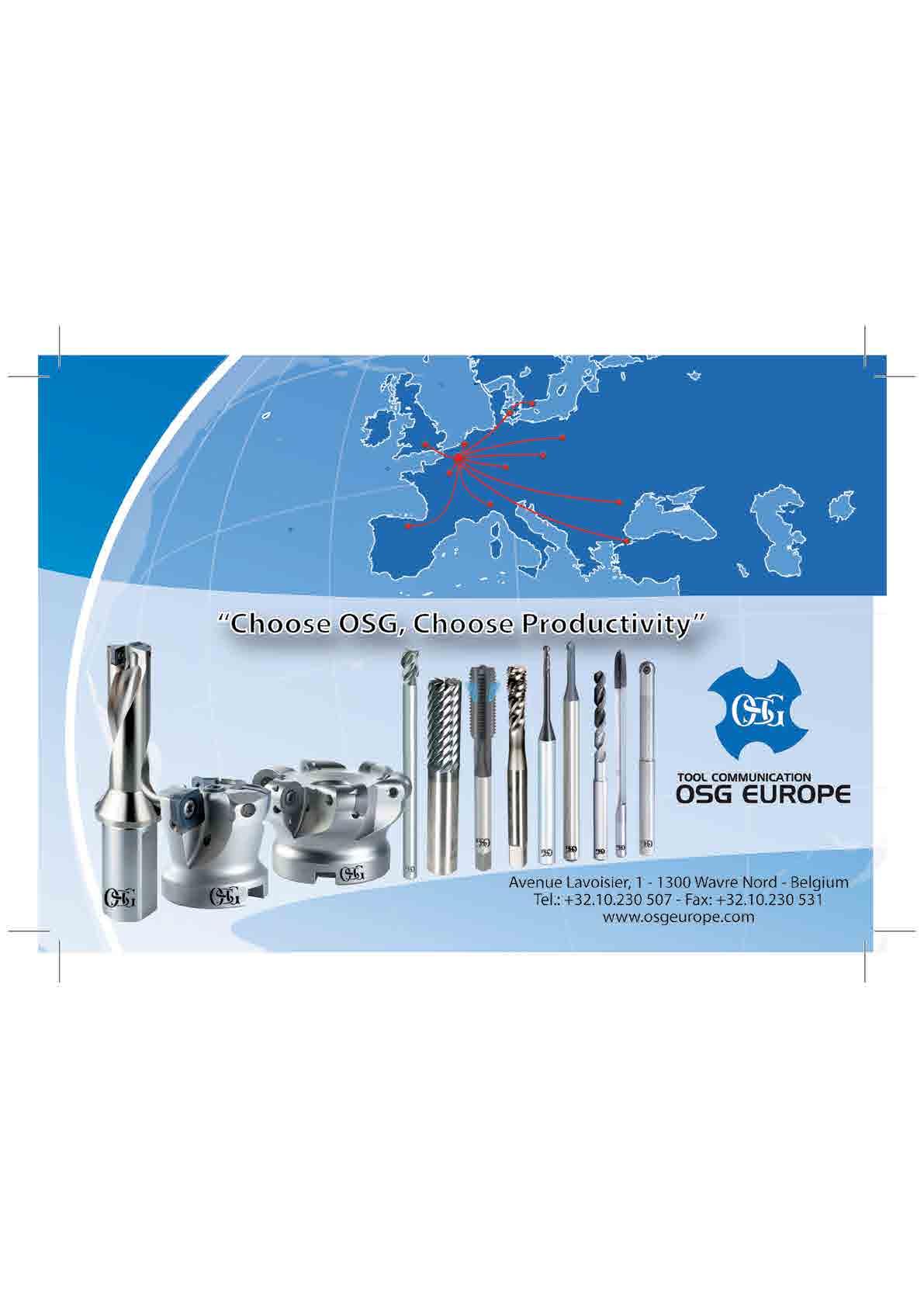

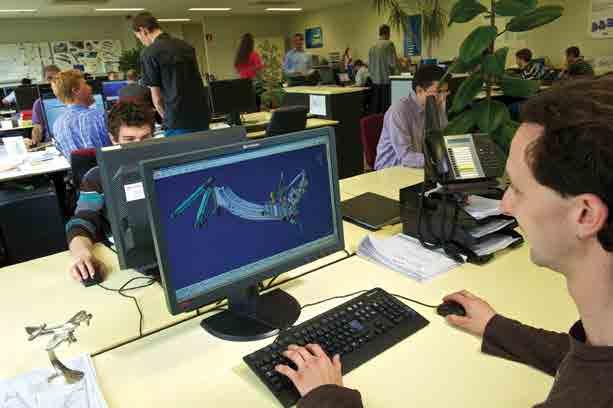
structures for the new Lockheed-Martin F-35 (Joint Strike Fighter). In Europe we operate as an Airbus Military partner on the new A400M tactical aircraft.
“What’s particularly exciting is our latest major investment in a new ASCO plant in Stillwater, Oklahoma which will extend our manufacturing capabilities in North-America. We purchased the site from the makers of Mercury power boat engines; it extends to more than 66,000 square metres. We are completely re-building and re-equipping the complex to suit our specific needs. Main focus is the Asco US customer base, such as Boeing and Spirit Aerosystems. This brand new equipped (one-stop) facility brings ASCO within closer reach of both existing and new local customers. Today we push integration forward in the value chain, aiming for larger work packages, including and capitalizing on our unique design and aftermarket capabilities and services. This success contributes to sustainably maintain our profitable growth momentum. Upon our forward order intake backlog, which at the moment enjoys historical record levels.”

Meeting future expectations today
State-of-the-art ASCO production facilities in Belgium, Germany, Canada and shortly the USA, all reflect its strategy for the future. Provide best industry practices to its customers’ current and future expectations, whilst enhancing mutually beneficial business relationships. Thanks to its very substantial investments in new high-performance manufacturing technologies, Asco is able to master ever-tougher requirements on highly complex components in a variety of materials. The company is vertically integrated with the most modern facilities in machining, heat and surface treatment and sub-assembly lines, supported by its proper well established, globally competitive Supply Chain. Which optimally fulfils its customers’ product and process requirements, not only for today but successfully address any future challenges its clients will face.
All Asco facilities pay special attention to lean operating units, maximally optimized for flow, mastered by modern manufacturing ERP Systems including on-line production tracking, equipment efficiency monitoring and a build-in quality (statistical process control). Uptime of Asco equipment is continuously improved by optimal concept choices (incl. FMS), continuous improvements through its extensive Engineering resources, focus on preventive maintenance programmes and industry-leading fast change-over systems. n
For further information about Asco Industries’ innovative products and services visit: www.asco.be
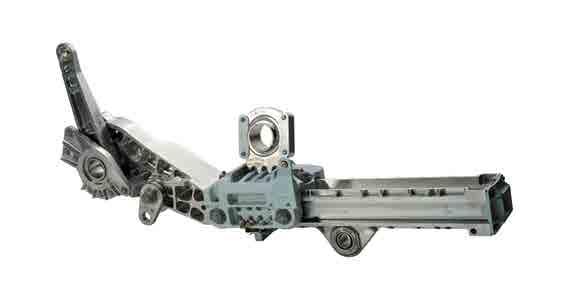
Arthur D. Little
Kurt Baes, Partner at Arthur D. Little and long-term strategic advisor to Asco, adds his perspective: “The company’s top management has transformed the firm into a global integrated player, combining strong production units with corporate functions that have a global footprint. Providing seamless integration of all of its operations provides premium customer value, reflected in Asco’s ability to achieve sustainable growth.”
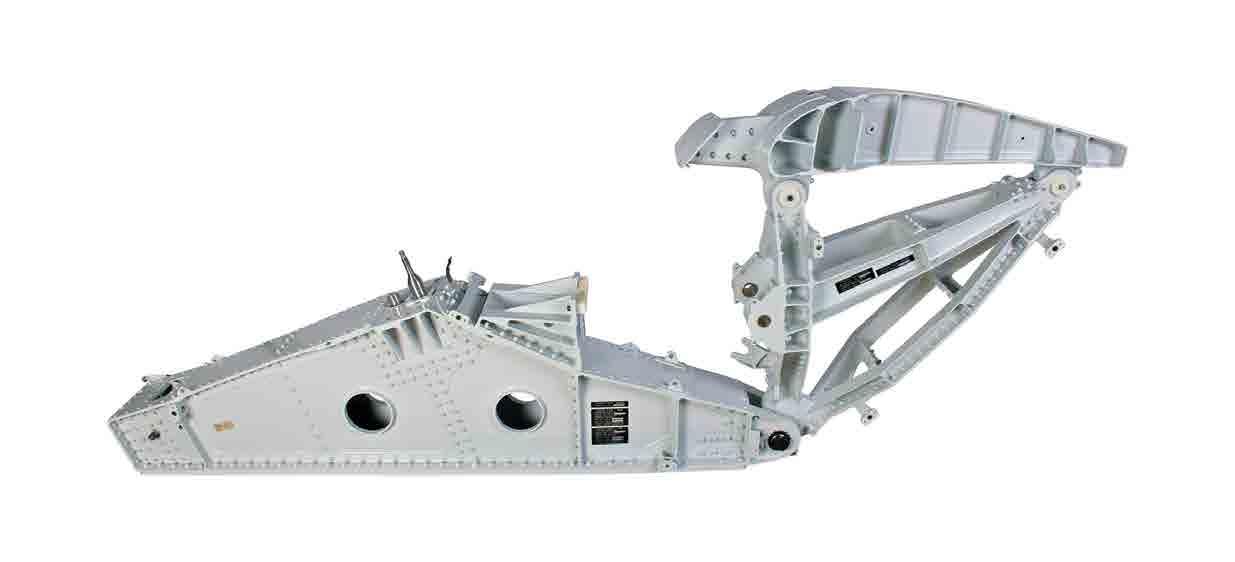