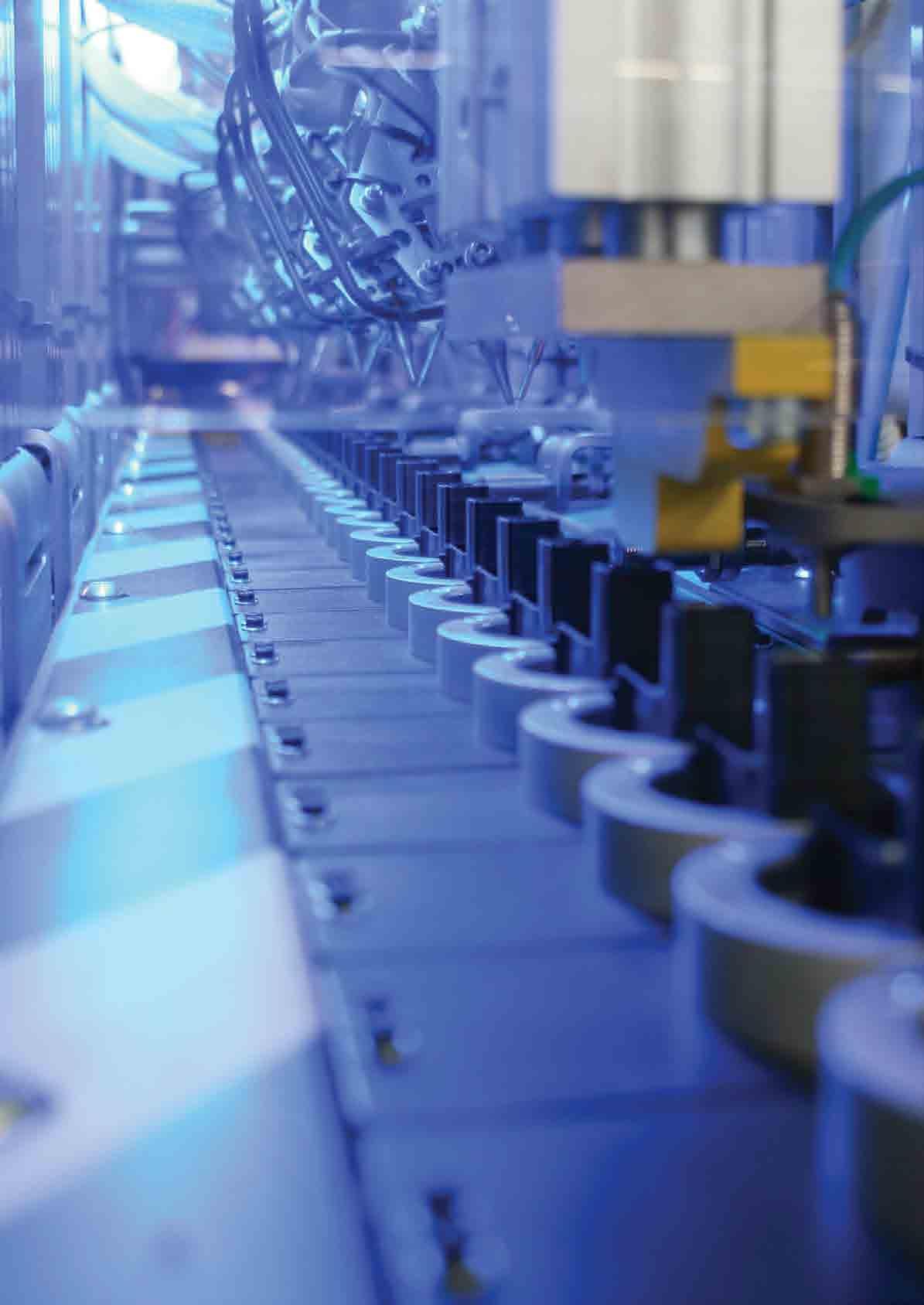
7 minute read
The true all-rounder of construction specialists
The company holds various patents in this field and the first actual application of this stateof-the-art technology has been for the BMW electric car and scooter.
As well as being Tier1 and Tier 2 suppliers for OEMs, Meta System supplies the OES market through importers, head offices of automotive manufacturers, or their regional or national equivalents. Geographically, Europe is the first market of the company, with obviously, due to the link to automotive manufacturers, a strong presence in Germany, where all the three main automotive players are served, followed by France and Italy. Italy is mainly significant in terms of Italian clients that distribute the products abroad. Markets in which the company is present with its products and which will further develop in the future include North Africa and Malaysia. Brazil is another market supplied, albeit indirectly through Italian intermediaries. Things work slightly differently for the telematics market, where Italy plays an important role, due to the link with the insurance sector. A growing pattern for telematics products is also been experienced in the UK, as well as in South Africa, while in the future scope for growth in this area will be particularly significant in Russia.
When talking about future developments, Mr Simonazzi says, “These are the market segments within whose boundaries we will carry on operating in the future, with the telematics range experiencing a particularly important growth. In terms of the OEM production we do not expect surprises, as here planning times are longer, and we already have the contracts for the period 2014–2020. At least for the next few years, growth in production for the OEM sector will still be due to European automotive manufacturers, mainly German, French and Italian. Certainly further OEM development will require an increase of our critical mass. We’ll see what action to take with regard to this, depending on the opportunities that will arise. In future, we will develop in terms of new products and new markets. Whilst in the telematics sector we will acquire new clients and new geographical markets, with regard to OEMs we will look for new clients, but this also means taking advantage of the new opportunities arising from existing clients, in terms of new vehicles and platforms, which for us is equivalent to acquiring a new customer.” n
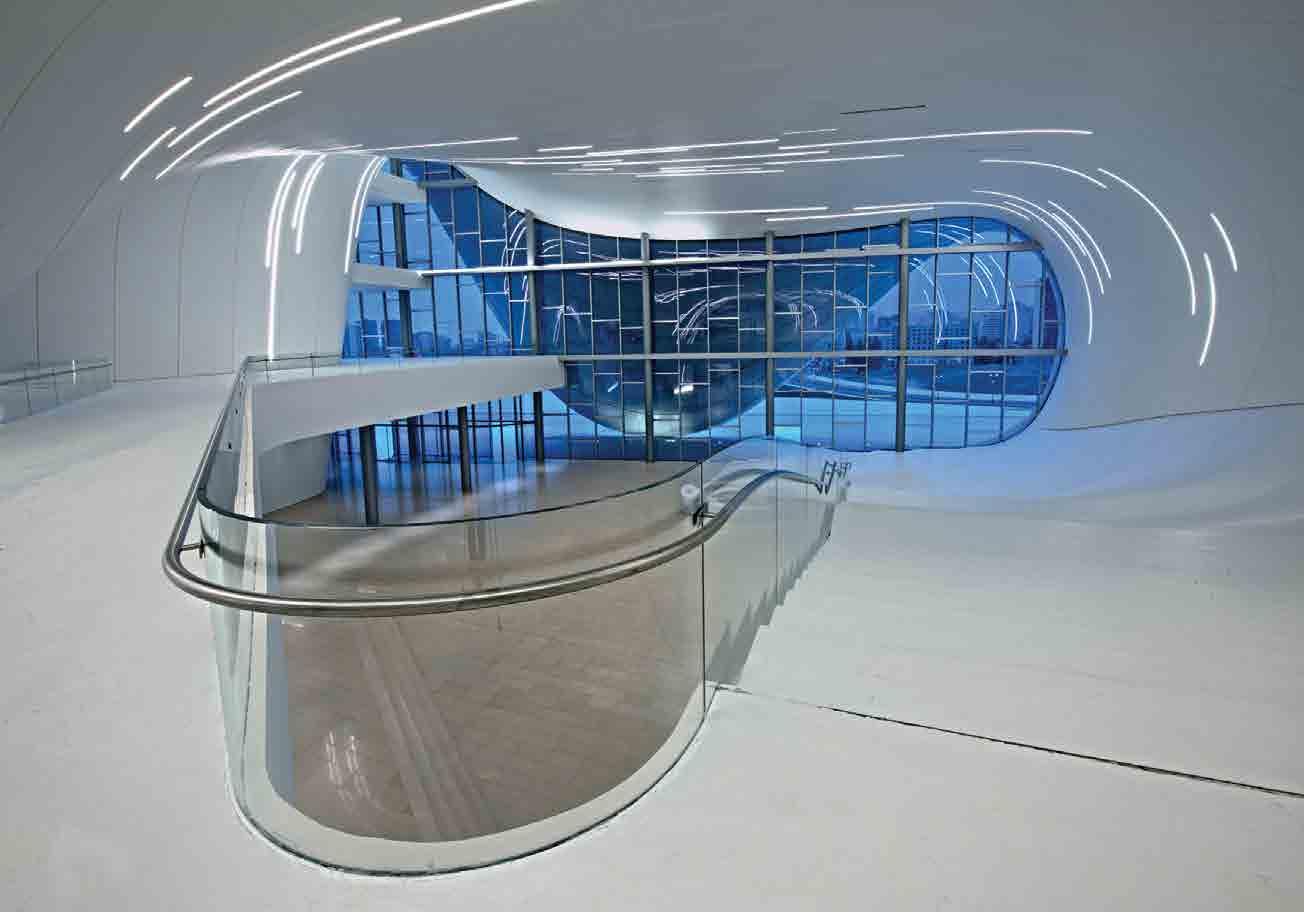
Lindner is a global leader in the design and manufacture of individual modular solutions for interior fit-out and the building envelope. Philip Yorke talked to Helmut Lang, the company’s main board director for commercial development, about its dynamic growth and the latest innovations, such as graphite ceiling systems, which are changing the face of modern construction.
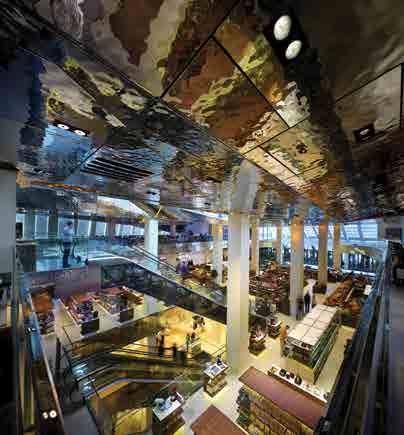
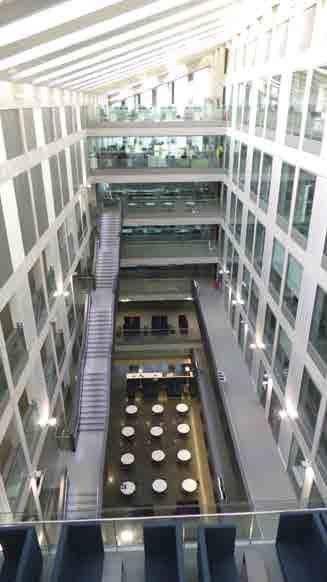
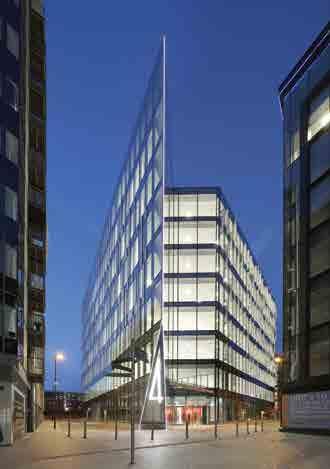
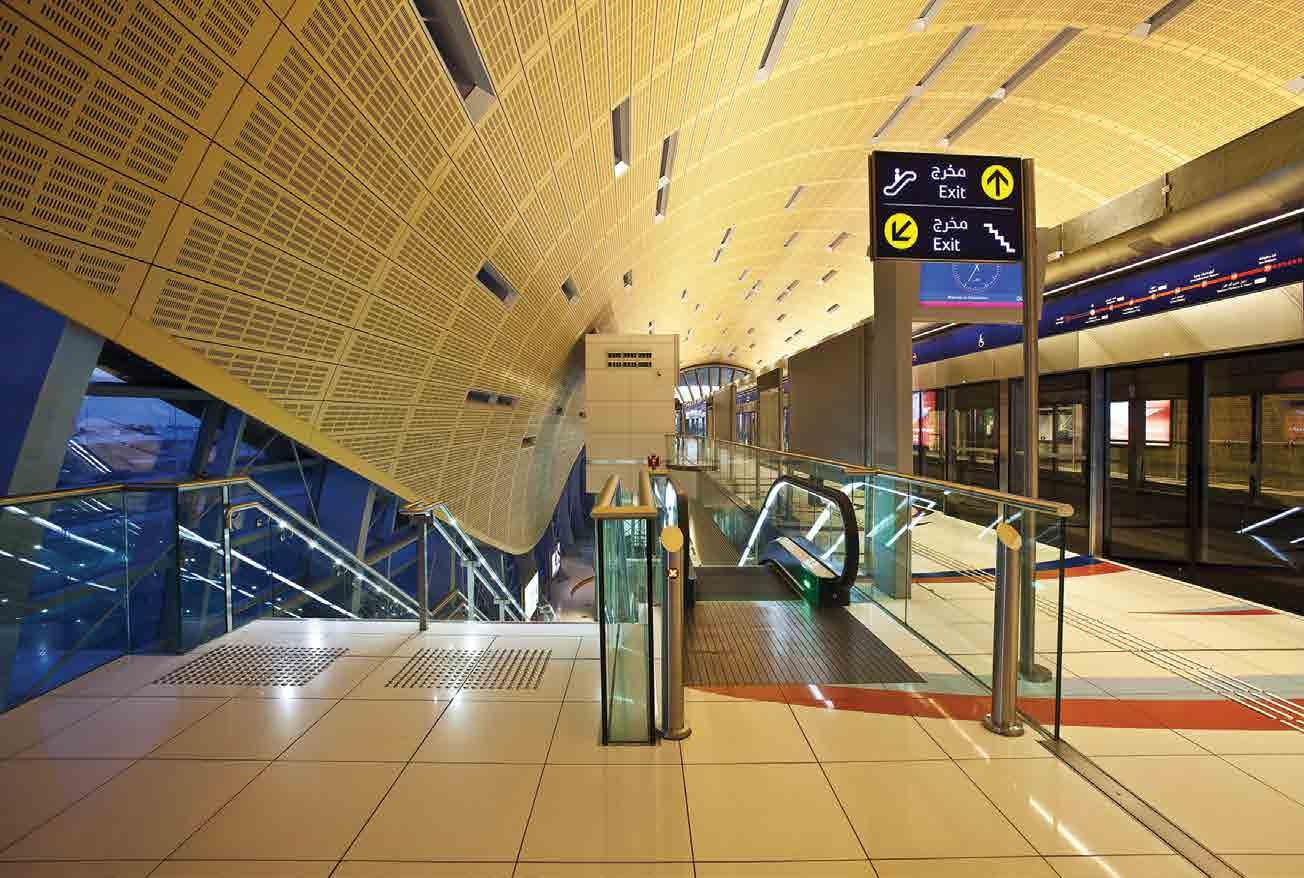
The Lindner Group is one of the world’s leading companies for interior fit-out, facade construction and industrial insulation projects. The company was founded in Arnstorf, Germany in 1965 by Hans Lindner who had a vision: this was to offer the construction industry ‘seamless’ solutions for entire buildings. By now, this vision has become a reality and is endorsed by the company’s involvement in many of the world’s most prestigious developments. These include major installations at international airports, railways, hospitals and hotels, as well as in leading concert halls and even luxury cruise liners.
Today the company’s unparalleled expertise makes Lindner the partner of choice for the supply of customised interior solutions. These are sometimes combined with the management of the complete building envelope, insulation and construction-related services, which is represented by the company’s inimitable range of capabilities, “Concepts-ProductsService”. With a current workforce of more than 6000 people, the family-owned Lindner Group operates state-of-the-art production plants and subsidiaries in more than 20 countries worldwide, from Atlanta to Zagreb. This also includes specialist companies such as the envelope experts Lindner Facades Ltd and Prater Ltd in London as well as Lindner Saudi Arabia Ltd offering industrial insulation services.
Innovative system solutions driving sales
Whether it is outstanding functionality combined with modern architecture and design, or unique innovative solutions, Lindner’s projectspecific designs are guaranteed to meet a client’s exacting requirements. For example, the design of amenities such as exclusive lounges, modern offices, medical facilities and auditoria are all based on over 45 years of experience in the use of environmentally friendly, state-ofthe-art technologies and comply with the most stringent international quality standards. Also the wide range of products like facades, floor and ceiling systems, partitions, heating and cooling technologies and construction-related services from green building consulting to scaffolding, makes the Bavarian company the partner of choice.
Lindner’s high-capacity production facilities ensure that customers receive optimised products and services, on time, every time. Through detailed planning and implementation processes, Lindner is selected to erect iconic buildings all over the world. The implementation of Copenhagen’s Danish Radio Concert Hall, the roofing of London’s Olympic Velodrome and the complete fit-out of the Dubai Metro Line are just a few recent examples of these global prestige projects.
Mr Lang said, “Design, innovation and our unrivalled experience have kept us at the forefront of our industry. To underscore the importance that we attach to new product development, we employ more than 200 people at our extensive R&D facilities here in Arnstorf, Germany where we have a stateof-the-art production facility that covers more than 160,000m2. This is our largest global production facility, but we also have similar manufacturing plants in Taicang, China, as well as in the Czech Republic and Slovakia, where we also work to German quality standards. We are definitely not into typical mass production projects.” For example, Lindner has worked in recent times in Azerbaijanian Baku on their new signature building, Zaha Hadid’s Heydar Aliyev cultural centre, for which the company had to develop a corner-free “internal skin” – an adaptable substructure with a three-
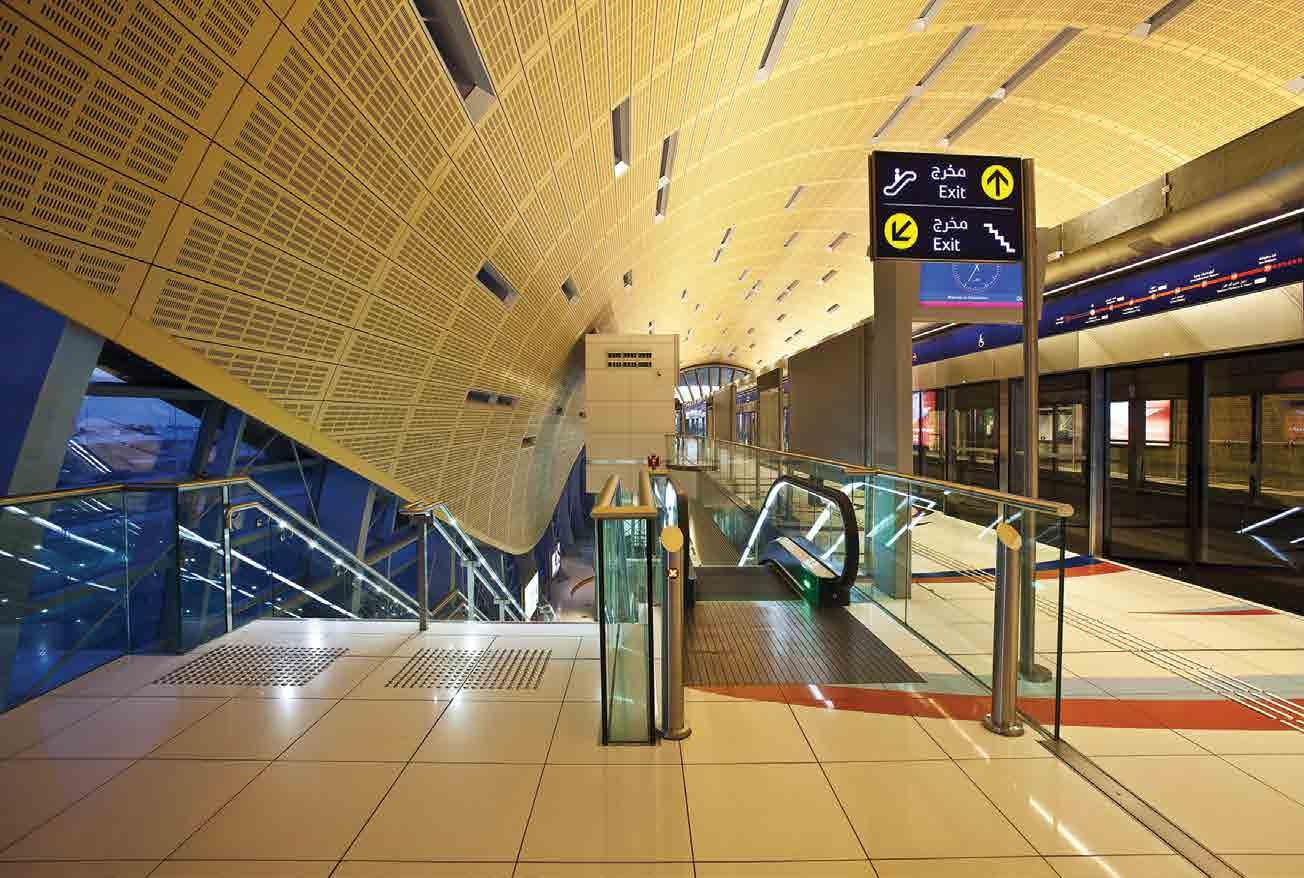
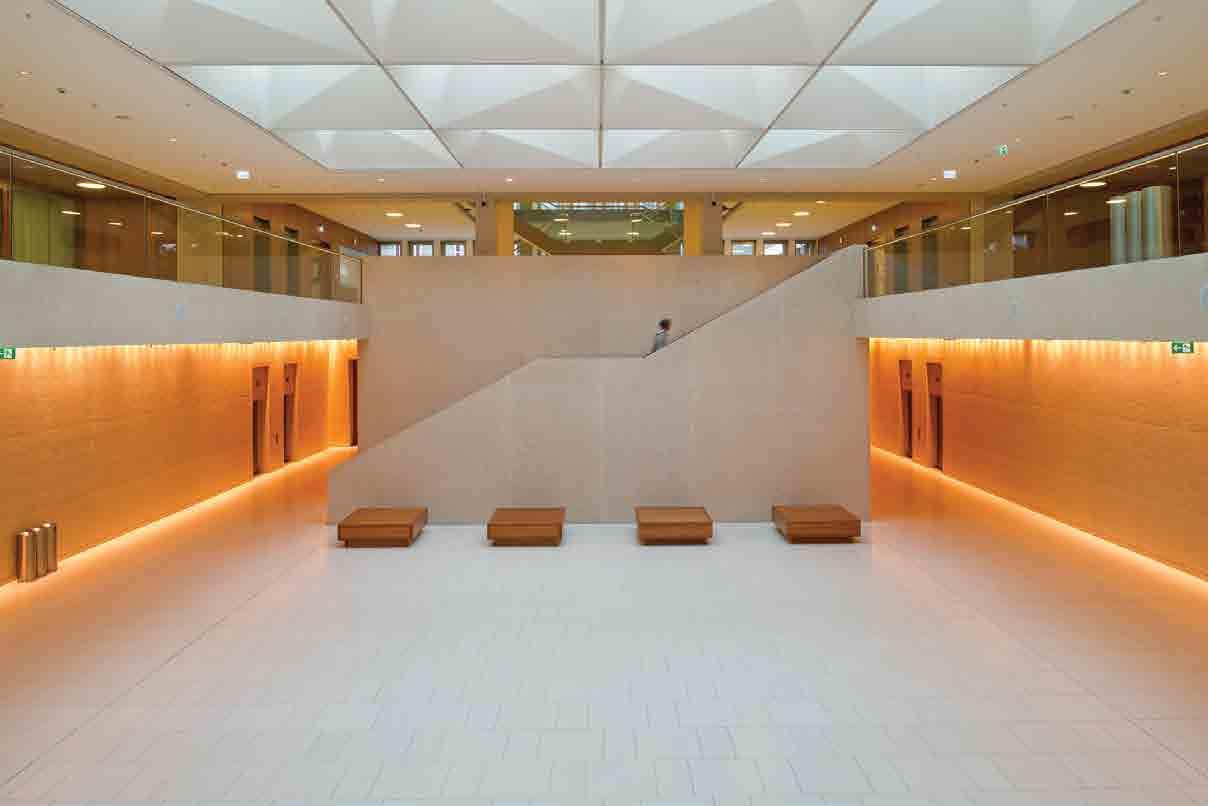
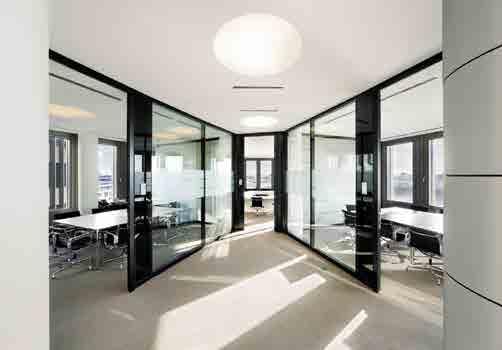
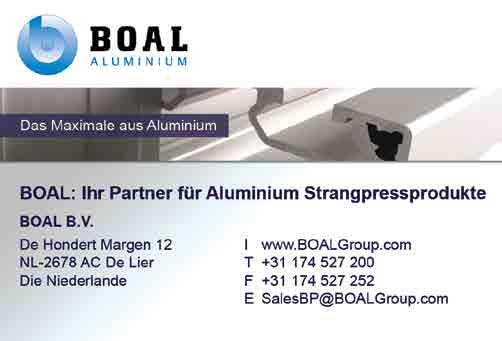
dimensionally curved surface – to transfer the external design into the interior.
Mr Lang added, “As a truly vertically integrated company we can do literally everything ourselves from the initial design concept to the manufacture and installation on-site. In fact we can take care of the entire value chain for customers. This means that our clients only need one supplier and one point of reference, which is a major advantage these days.”
It is an advantage especially acknowledged when it comes to integral planning and implementation processes for large-scale new constructions or high-class refurbishments, sometimes in conjunction with an aspired green building certification. This is when the one-stop-shop Lindner – internal departments would even take care of specialist jobs like building decontamination – creates its added value for the client by reducing the complexity of the enormous task.
Buildings without interfaces and using the latest technologies
Hans Lindner’s original vision of an entire building that is designed and constructed without interfaces has become reality and in a most spectacular way. The Lindner System Buildings combine the highly desirable concept of prefabricated, modular construction with unlimited spatial planning options. This cutting-edge technology means that the building can be adapted to any client’s specific requirements while maintaining the advantage of rapid on-site erection. The system is based upon a heavy-duty steel frame structure that offers unlimited scope: extraordinarily wide unsupported spans and variable ceiling height enable infinite options of reversible floor layouts (dependent on fit-out), a flexible solution tailored to the builder’s individual requirements.
Beside the System Buildings, one of the Lindner Group’s most exciting innovative developments at this time is the unique graphitebased Lindner Plafotherm® chilled ceiling. “This is a ground-breaking development which offers significant benefits to developers in terms of its overall lightness, an accelerated temperature regulation with significant energy savings and enhanced comfort for occupants. We have entered into a joint venture with renowned SGL Carbon to drive this technology forward, which we see as being trend-setting for industrial ceilings worldwide. The natural product graphite and its derivative, expanded graphite, fit perfectly with our commitment to sustainability and our protection of the environment. We are a founding member of the DGNB, the German Sustainable Building Council, and, as a responsible manufacturer, we run numerous internal research projects aiming for a longterm reduction of energy consumption and avoidable emissions.”
The continuous striving for well-balanced, sustainable solutions, based upon resourceconserving high-quality products and customised services is characteristic of the market approach of the Lindner Group. For instance, one of Lindner’s bestsellers, calcium sulphate flooring NORTEC and FLOOR and more®, is made of 99 per cent recycled materials. But it’s much more than just ‘green’. The floor impresses just as much by its versatility and resilience: it can be equipped with integrated heating and cooling technologies or acoustic elements, and it can carry incredibly high weights for decades – a solution individually designed and manufactured for each client. n
For further information about Lindner’s latest innovative concepts, products and services visit: www.lindner-group.com