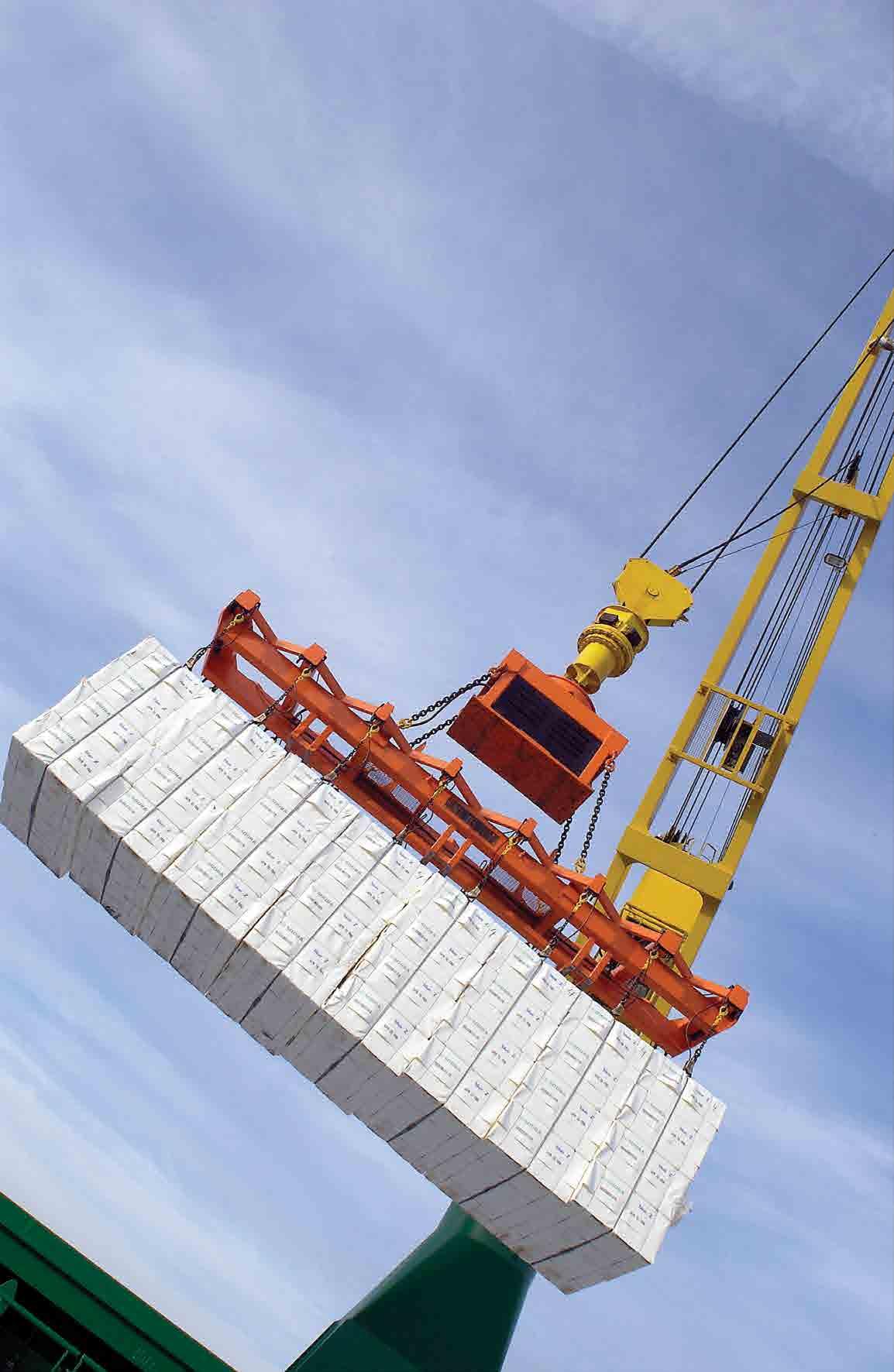
6 minute read
The future power of pulp Sodra
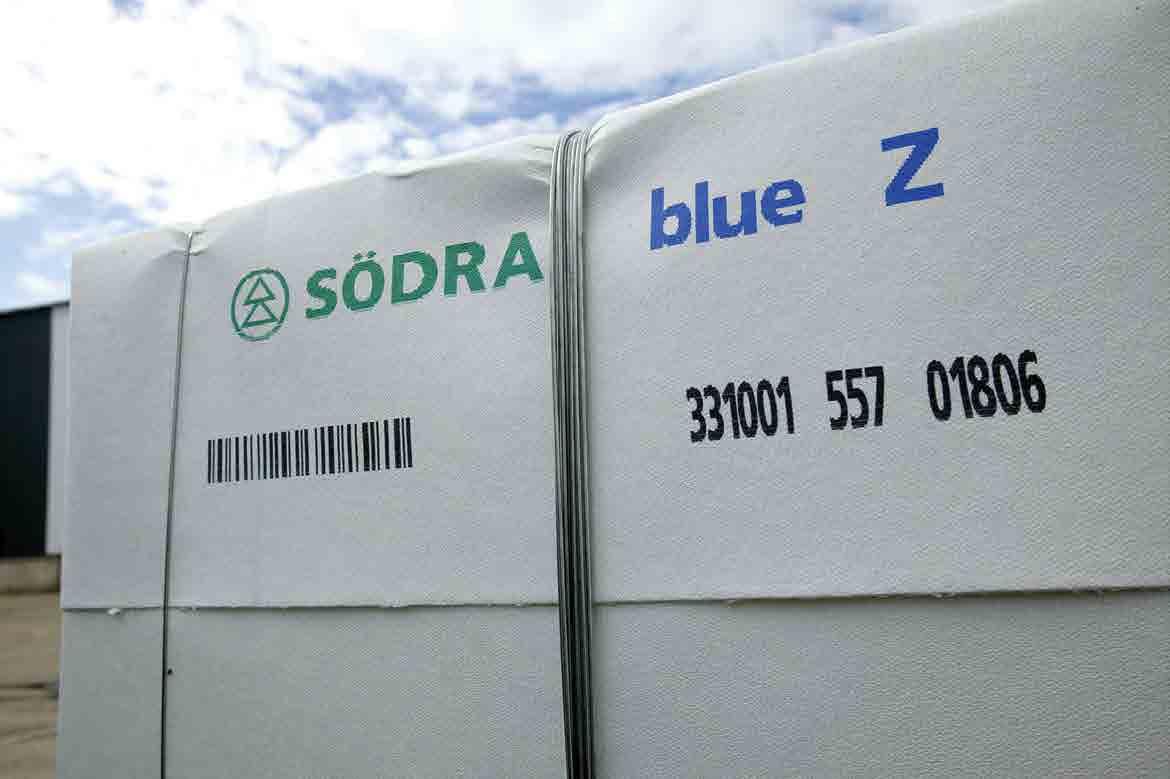
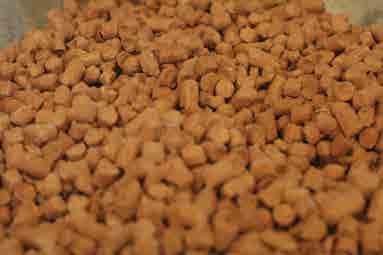
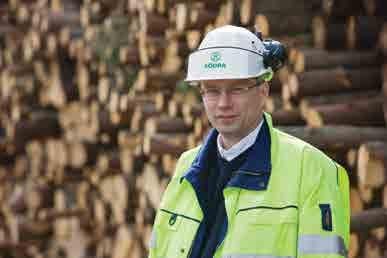
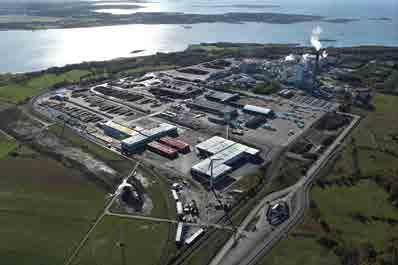
THE FUTURE POWER OF PULP
Sodra is one of Scandinavia’s largest economic cooperatives and is a market leader in the manufacture of paper pulp and biofuel products. Philip Yorke talked to Jonas Eriksson, the company’s plant manager, about its increasing role as a power provider and its ambitious plans for expansion of its pulp mill facilities.
Sodra was founded in Sweden in 1938 and more than 51,000 forest owners in Southern Sweden are members of the economic association that is now celebrating 75 years of successful operations. Together its members own more than half of all the privately held forestry in the area. Sodra is also a major employer in the region with over 3800 people working for the group in roles ranging from forestry management and environmental conservation, to accounting, sales and new product development.
Sodra’s main products are paper pulp and biofuel products, but in recent years the company has also become a significant producer of electricity, and sells its surplus for domestic and commercial consumption. Today the company produces more than 425,000 tonnes of paper pulp per year and employs over 3800 people. In 2012 Sodra exported 92 per cent of its paper pulp products and recorded sales of around SEK 17 billion.
Leading the field
Sodra leads the field in paper pulp production in the Nordic region and is planning to extend its lead still further. The company plans to increase manufacturing capacity at its Varo pulp mill from 425,000 tonnes of pulp, per year to 700,000 tonnes. The environmental licence required for this expansion has already been applied for and the company anticipates that the permission to proceed with the new mill will be granted early in 2014. The increased capacity will result in more efficient production and pave the way for the company’s long-term growth and profitability for its members.
Mr Eriksson said, “Part of our commitment to our members and the environment is our ongoing investment programme to enhance our efficiency and productivity. We are also continuing to diversify and have developed several important new income streams since 1972 by extending the versatility of our production processes. For example, we began with pulp production in 1972 and by 2002 we were able to provide power for our local town’s district heating. In 2007 we began producing ‘green’ electricity on a commercial scale and in 2002 we moved into dried bark production as part of our biofuel offering as many households use bark as biofuel. Then finally in 2013 we diversified again into the manufacture of pellets as it offered another significant economical biofuel income stream. As far as energy
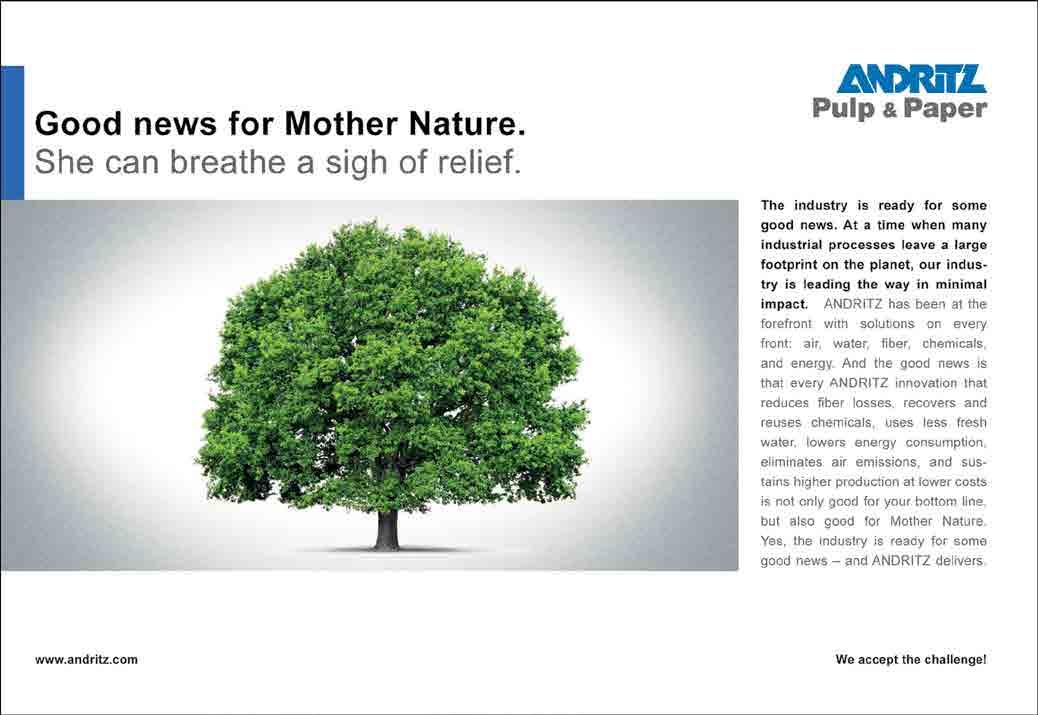
is concerned we are currently generating more than 1500 GWh of energy surplus to our needs, which is sufficient to meet the demands of over 75,000 family homes.
“However, our most ambitious expansion programme to date is the planned development of our pulp mill facility at Varo which will almost double current capacity. We are very fortunate in that all our raw materials come from sustainable forestry locations within 120km of our plant and therefore the fibre content quality is very consistent. This in turn means we are able to guarantee a consistently high standard of raw materials, and in addition it offers us a very reliable source of raw materials.
Mr Eriksson added, “Another important milestone was the installation of a new turbine in 2007, which enhanced our efficiency and since then we have been able to deliver green electricity from the steam created from our boilers. Our 63MW backpressure turbine from Skoda runs at 85 bar and 485 degrees Celsius. We have three basic softwood pulp products that we market worldwide. We produce tissue on a very large scale and this market is growing, we also produce speciality papers as well as fine papers.
“Another unique aspect of our production facilities is that we have our own saw mill located adjacent to our pulp mill plant which again adds significantly to our company’s overall efficiency.”
It is worth noting that because electricity is generated and used more efficiently at Sodra’s plants it means that a greater share of green electricity can be supplied to the open market. Even forest felling operations make a direct contribution to biofuel production as during the felling process a growing proportion of waste products are recovered to create biofuel.
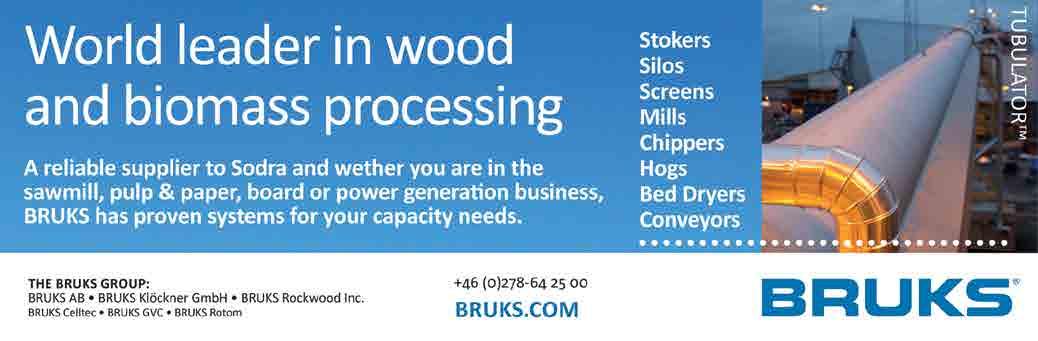
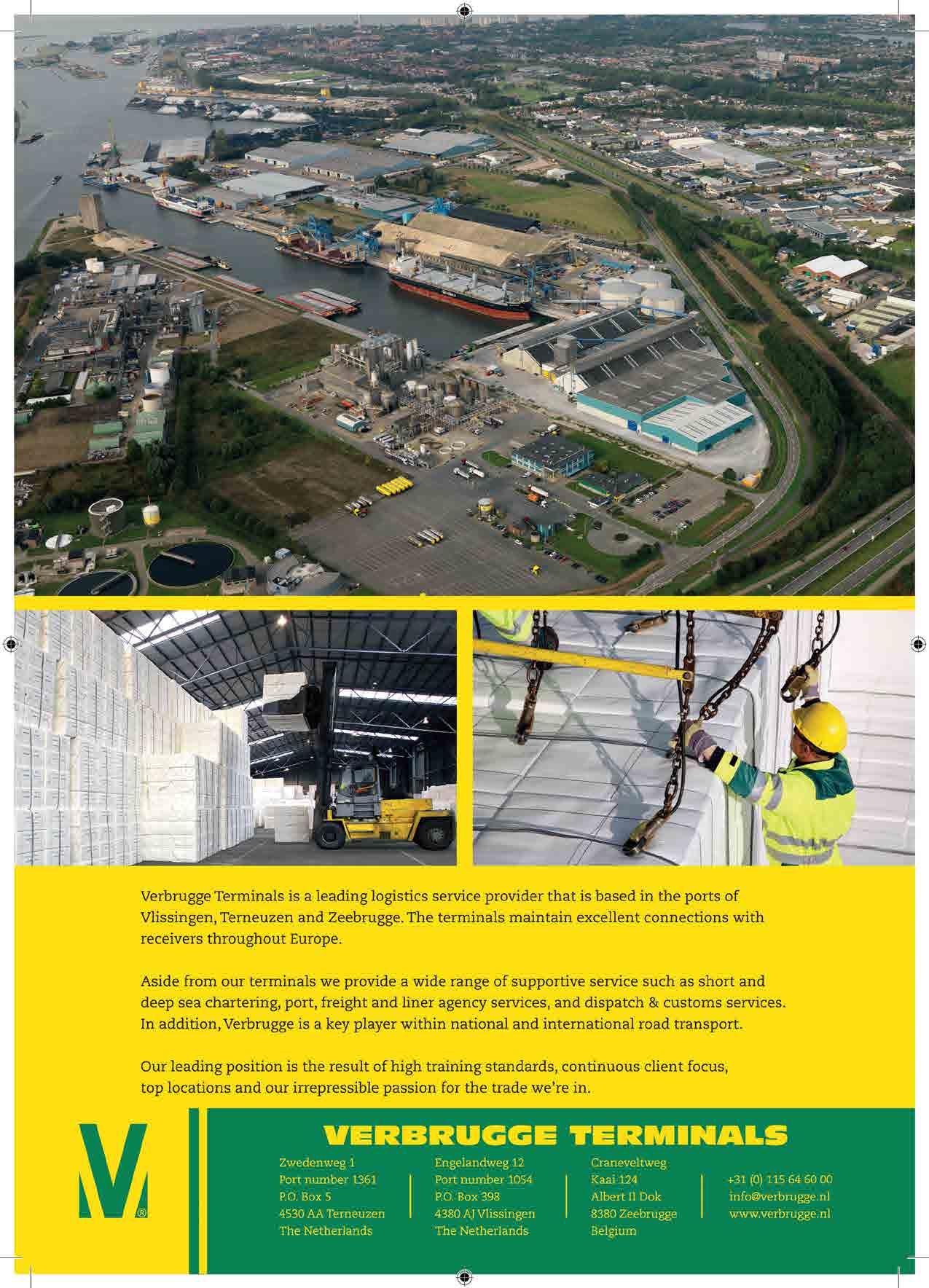
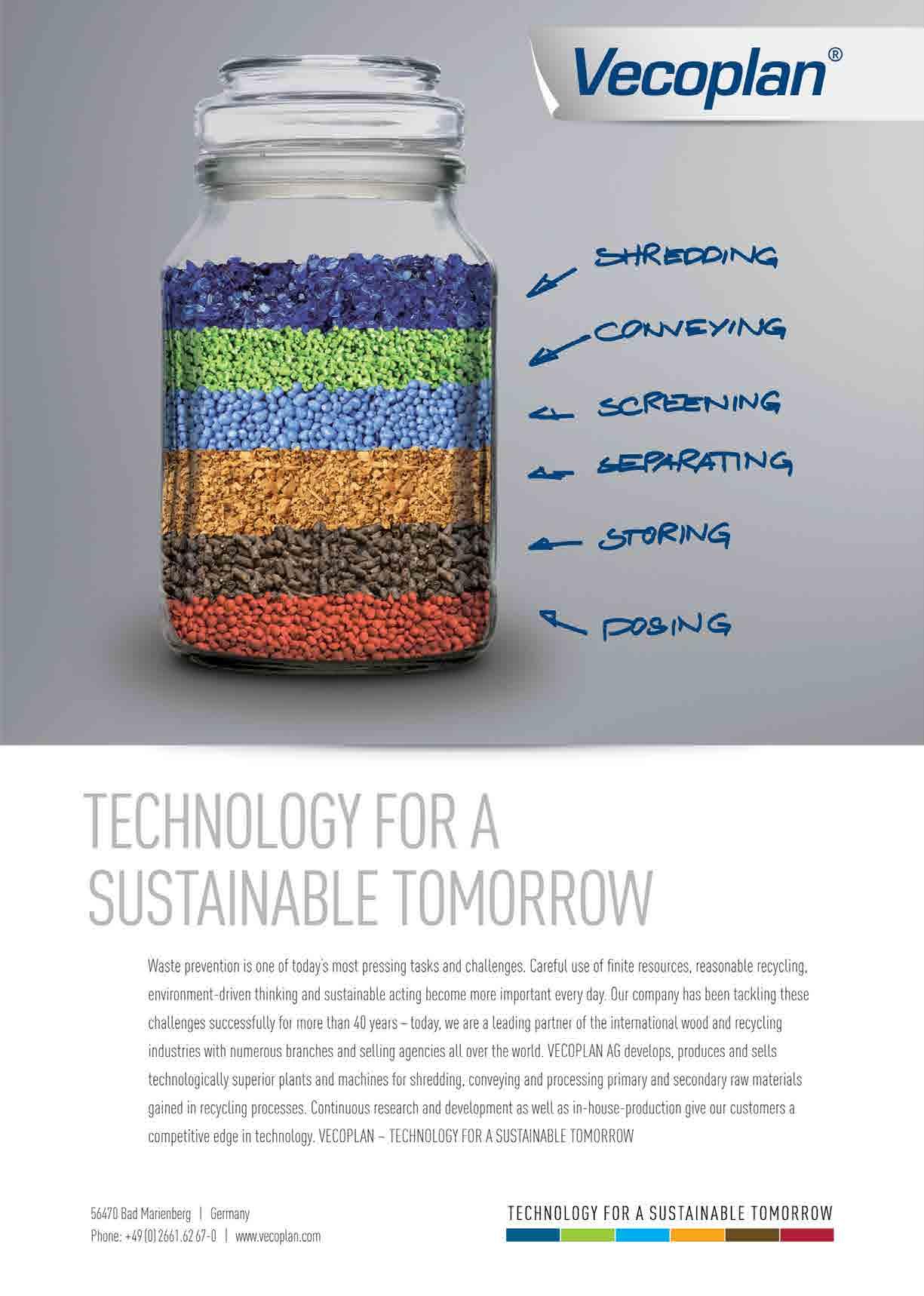
Research, the key to remaining competitive
Sodra believes that ongoing research and development is essential if the company is to remain competitive in the future. It therefore uses its own considerable resources and its partnerships with both universities and research institutes to create opportunities for the efficient development of its products and production processes. This research covers the entire value-chain, from forest improvement to the marketing of new products to its customers. Sodra’s research also aims to develop methods and processes that improve overall production efficiency and thus make the company more competitive.
As a major player, Sodra also has a respect and responsibility for the way the earth’s resources are used. Sustainability is therefore at the heart of everything that the company does from seed growing in the forest to its renewable products. Today Sodra plants three trees for every one that it fells. Furthermore, it sees sustainability as offering a competitive advantage that forms a natural part of its successful business model. n
For further details of Sodra’s diverse, sustainable products and services visit: www.sodra.com

New Solution developed Best practice by VECOPLAN
The plant in Väröbacka in the Swedish province of Halland, south of Gothenburg, was built in 1972 and since than it has been upgraded several times. Recently, the VECOPLAN AG from Bad Marienberg (Germany) has designed, manufactured and supplied the conveyor system for the connection of the existing sawmill to a new pellet plant. With the successful implementation of the project plant and machine builder the growth and success of Södra Cell has been significant supported.
The required output of 100 m³/h is ensured by two loading and unloading conveyors, which can be moved sideways, as well as by a 200 m VecoBelt pipe conveyor for transporting sawdust. This project integrates the VECOPLAN conveyor system into an existing production facility without causing any stoppages to that plant. This was a challenge that could only be tackled by taking in a “roundabout” way. In order to reach the actual installation site, the customer had requested that the existing material delivery routes to the plant be diverted during the construction phase, and that a temporary chip discharge point be incorporated.
For the customer a new steel rope free construction for the VecoBELT was developed by VECOPLAN. The new design is easier to install, economical and above all very flexible. The 200m long conveyor is supported by four Ypsilon pillars in distance of 50 meters. This construction allows the use of the small space between storage places and buildings on the campus without restrictions.
The customer is satisfied: “The cooperation between Mared/ VECOPLAN and Södra Cell went well. We were impressed by VECOPLAN‘s technological competence and service-friendliness,” explained Leif Thoren, project manager at Södra Cell AB.
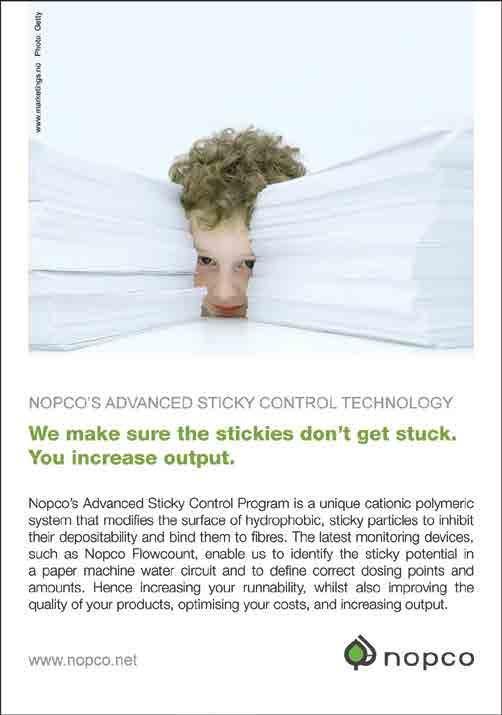
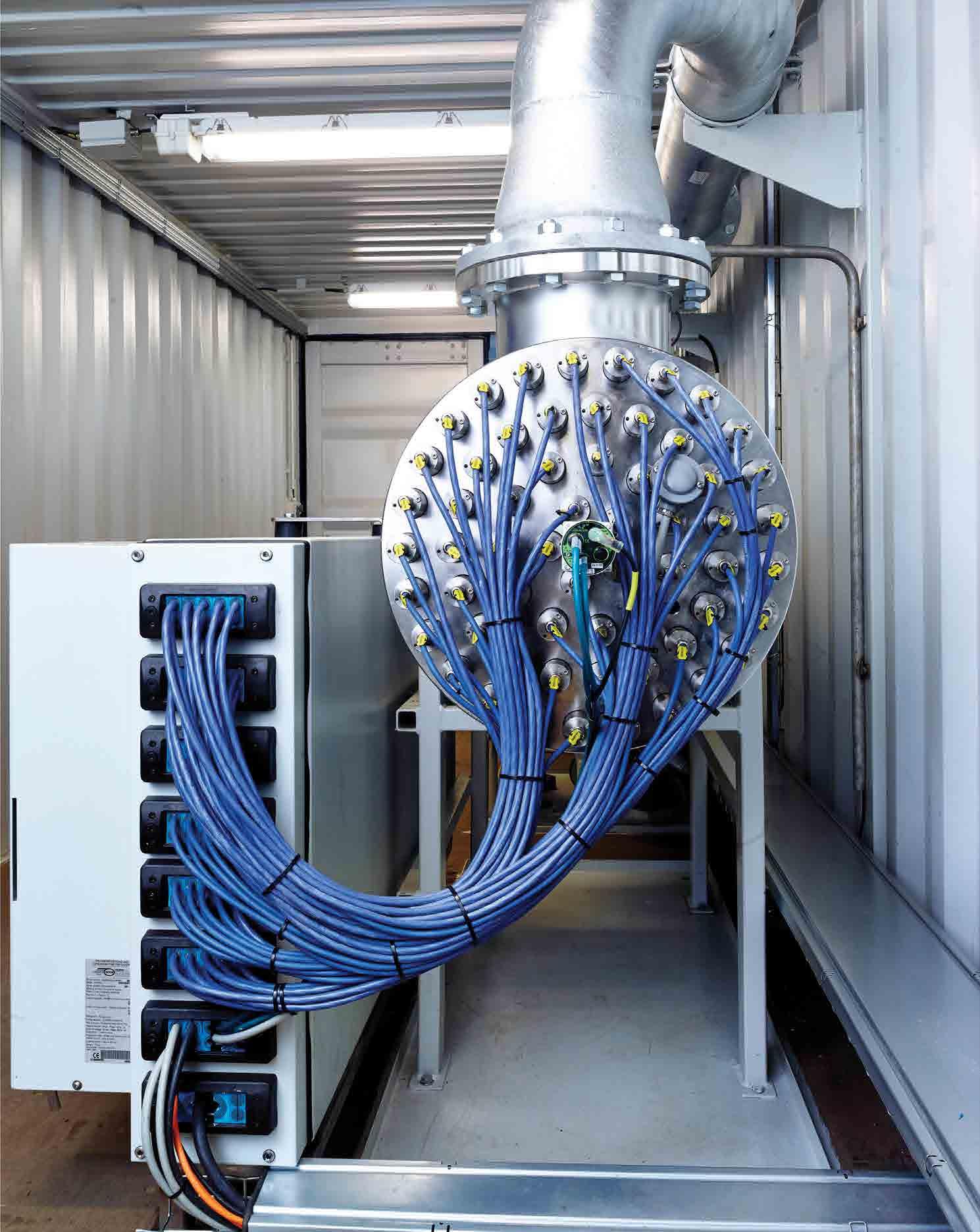