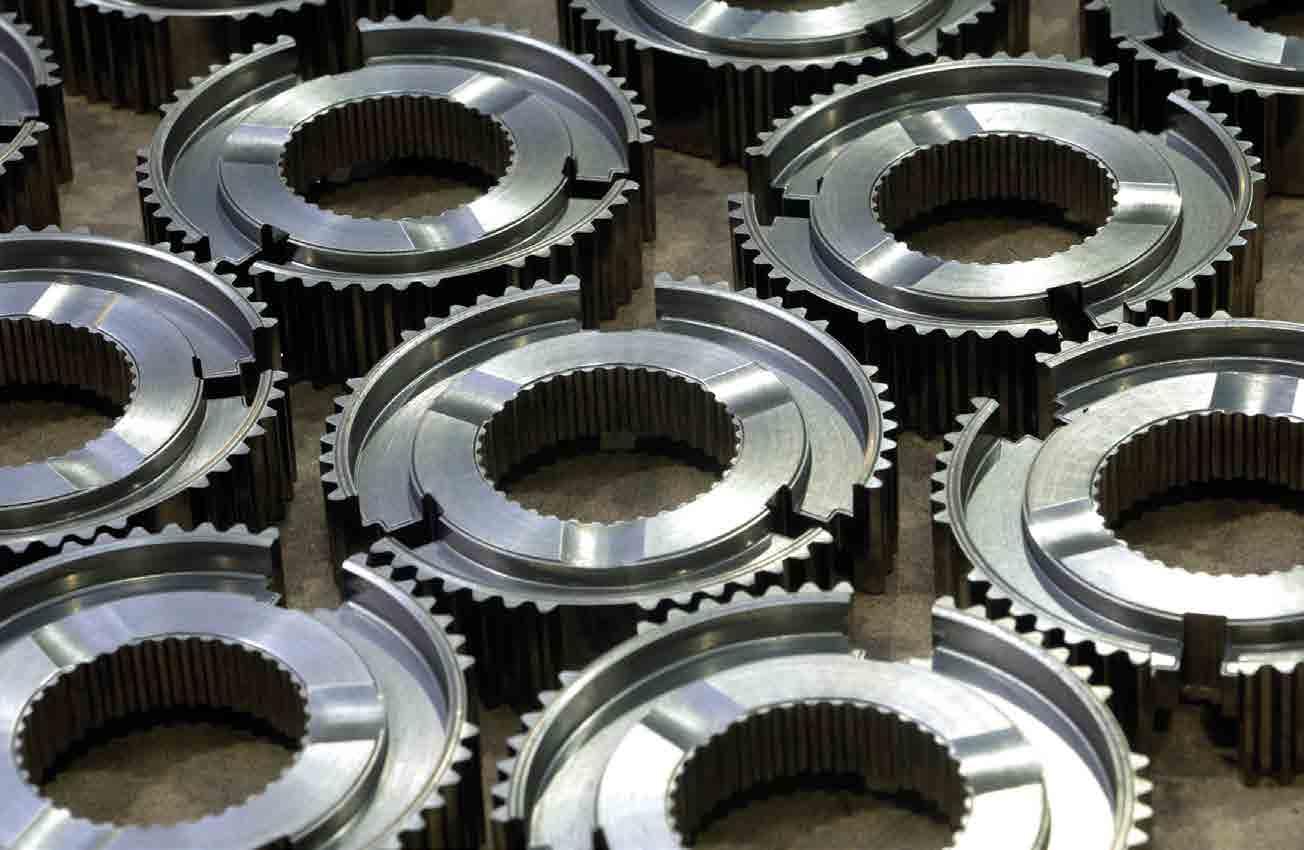
4 minute read
Precision powder metal parts GKN Sinter Metals
PRECISION POWDER METAL PARTS
GKN Sinter Metals is one of the world’s leading manufacturers of metal powder precision components. Industry Europe looks at the company’s production profile, latest news and strategies for continued success.
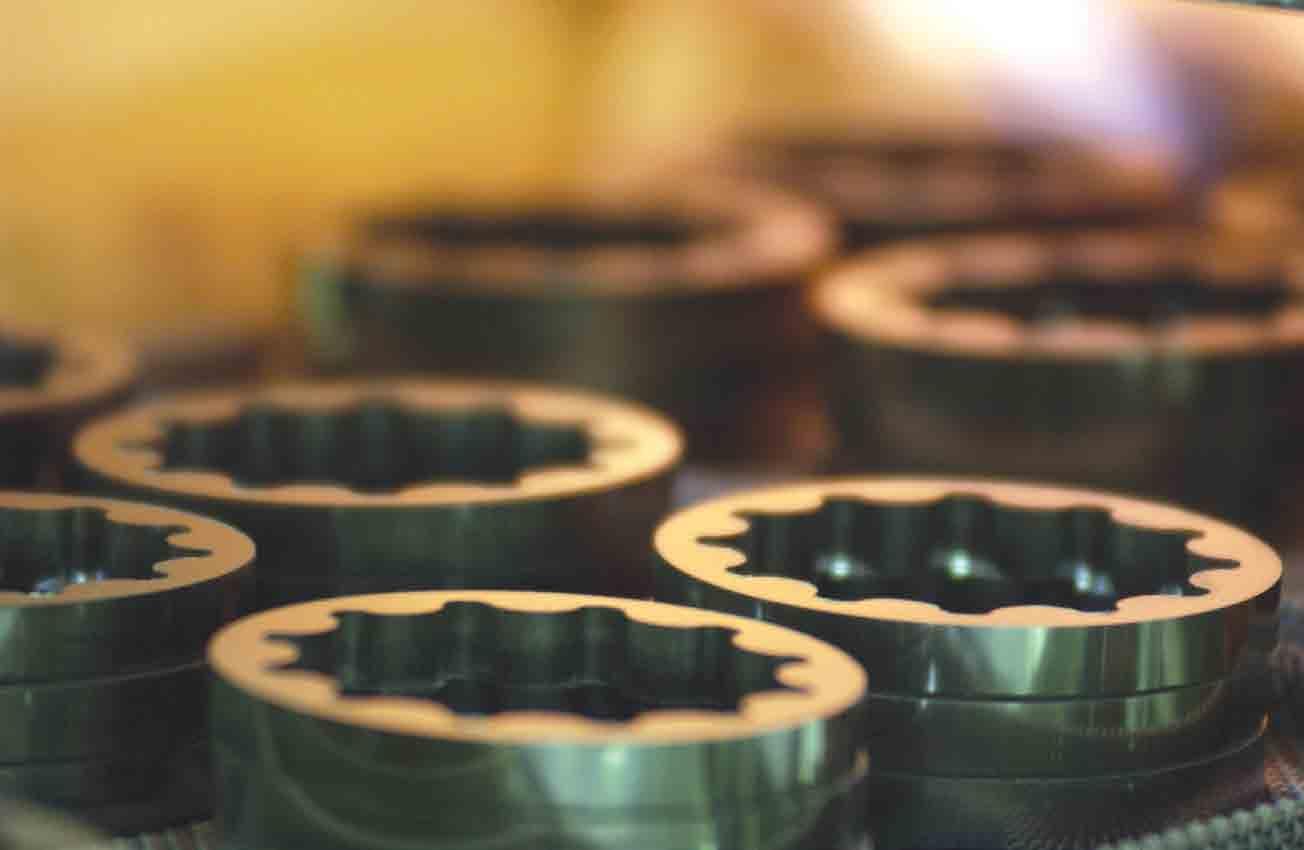

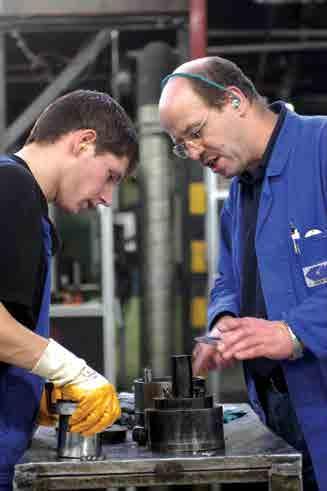
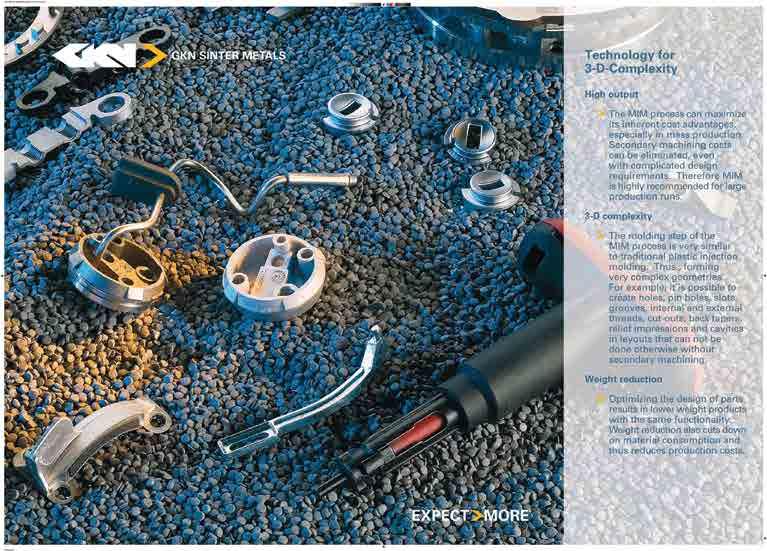
GKN Sinter Metals, a wholly owned subsidiary of GKN plc, has around 6500 employees worldwide operating from approximately 30 locations in 15 different countries in Europe, North and South America, southern Africa and Asia. The global headquarters of the company is in Auburn Hills, Michigan, in the USA. But all of its marketing activities are masterminded from its offices in Bonn, Germany.
GKN Sinter Metals offers a complete range of PM (powder metal) products, technologies and engineered solutions. These include sinter metal components, self-lubricating bearings, filter technology, powder metal injection mouldings powder forged components and aluminium sinter metal components. Backed up by global expertise, it is committed to delivering manufacturing and engineering support to ensure its clients succeed.
GKN has long been considered a worldclass supplier and works with some of the top players. For example, this year it was awarded Ford’s prestigious Q1 certification for supplier excellence. As Ford is its largest customer, this represented an important achievement. Earlier in the year another of its important clients, Bosch, awarded it preferred supplier status. Finally, in January 2013 its focus on quality was recognised with three Supplier Quality Excellence awards from General Motors Powertrain.
Automotive strength
As may be surmised from the above, a significant percentage of the company’s sales are accounted for by the automotive sector. Nevertheless, despite the impressive sales figures and the fact that the company is an established player in a highly demanding marketplace, it feels that the merits of powder metals as materials for precision manufacturing are under-appreciated. As such, the company makes efforts to convince a wider audience of the materials’ attributes. The objective is not just to increase the volume of existing applications, but also to help establish new ones.
Briefly, the technique involves forming metal parts by filling moulds with powdered materials, pressing them into shape under forces that may range from less than 100 tonnes to over 350 tonnes and then subjecting the parts to heat treatment. The temperatures involved in the latter can vary from around 500°C to as high as 1200°C for parts that are ‘sintered’, in other words heated until they reach the point where the metal begins to melt.
The advantages of manufacturing with powder metals can be considerable. One of the most important is that parts can be manufac-
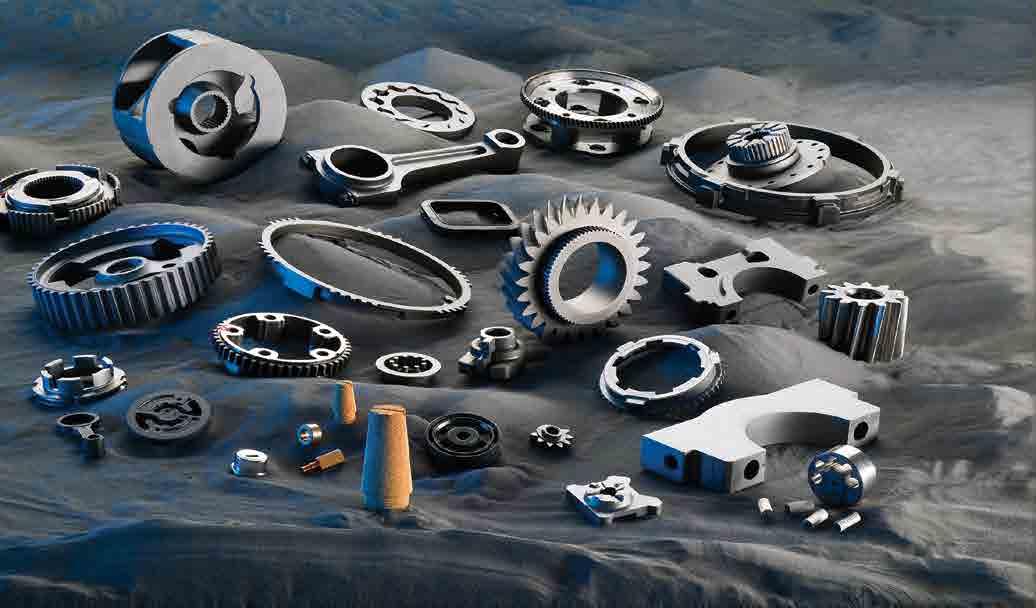

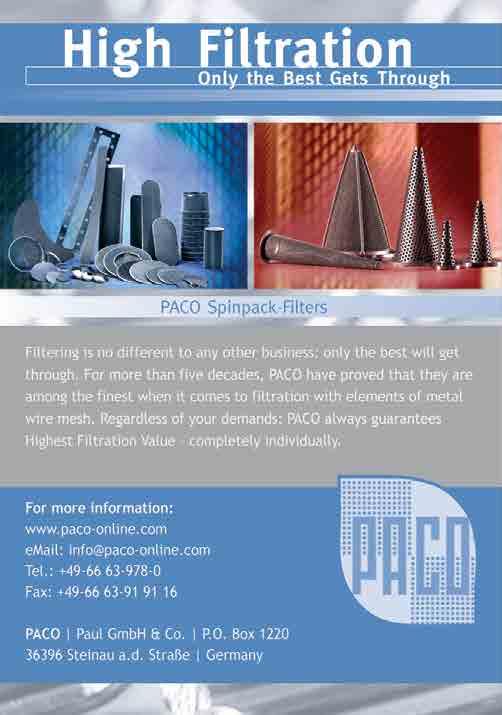
tured to ‘near net’ shape, so that any requirements for subsequent machining processes are minimised. In turn, that means there is very little wastage of the materials. It is an accurate, efficient, cost-effective and environmentally friendly way of manufacturing.
Moreover, the materials involved can also be highly varied. For example, GKN Sinter Metal produces parts made from steel, bronze, aluminium and various alloys. It also makes ‘soft magnetics’ based on a carbon-phosphor mix.
Technical capabilities
Two stages are involved in trying to change this situation. The first is for GKN Sinter Metals to obtain data from existing or potential customers about the performance requirements for specific applications. The second is for it to convince those customers that powder metals can fulfil requirements that are currently met through the use of other, more conventional materials.
The overall task, though, is not easy. The industry in which GKN Sinter Metals already has a strong foothold, the automotive sector, has extremely complex and exacting validation processes for approving new types of materials in existing applications. It makes little difference that the company may already be a supplier for other types of component.
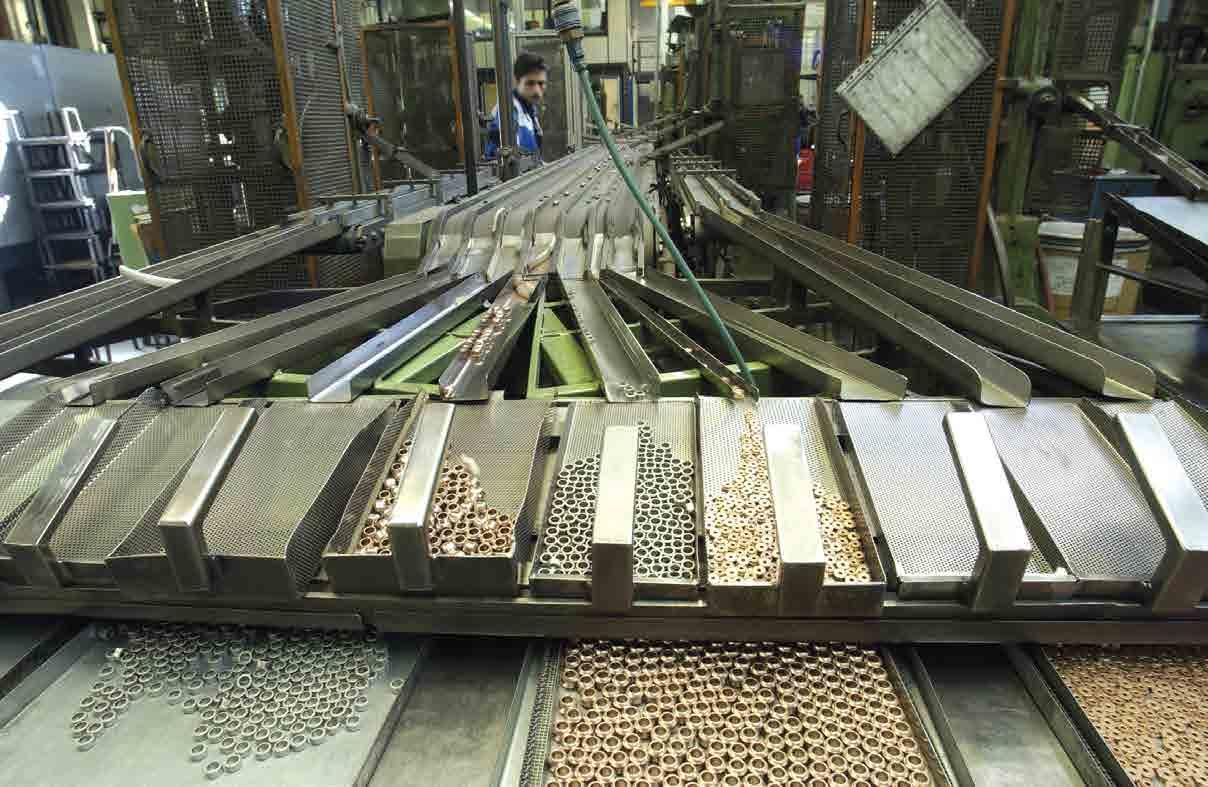
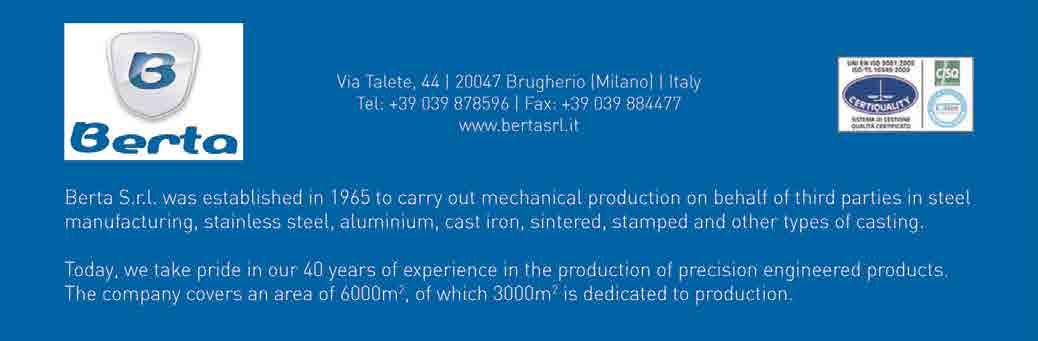
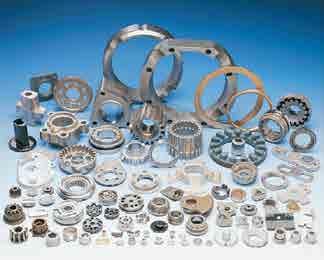
For this reason a key element in GKN Sinter Metals’ strategy is its technical centre in Radevormwald, near Cologne in Germany. The facility’s engineers have the job of demonstrating that powder metals can meet the application requirements of other companies.
The facility boasts a range of specialised equipment including several presses and furnaces, rolling machines for the development of gear prototypes and an environmentally controlled room for precision metrology. The result is a comprehensive ability to produce prototype parts and demonstrate how they perform in simulated real-life conditions.
In parallel with this practical approach, the company also seeks to keep itself at the forefront of new developments in technology. To this end, it operates a worldclass dedicated research and development centre in Europe, and a linked regional facility in America. Both are focused on leading technology development through innovation in support of the company’s vision and goals. n
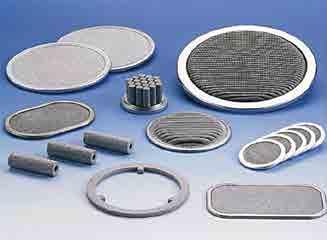
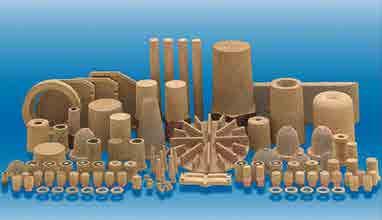