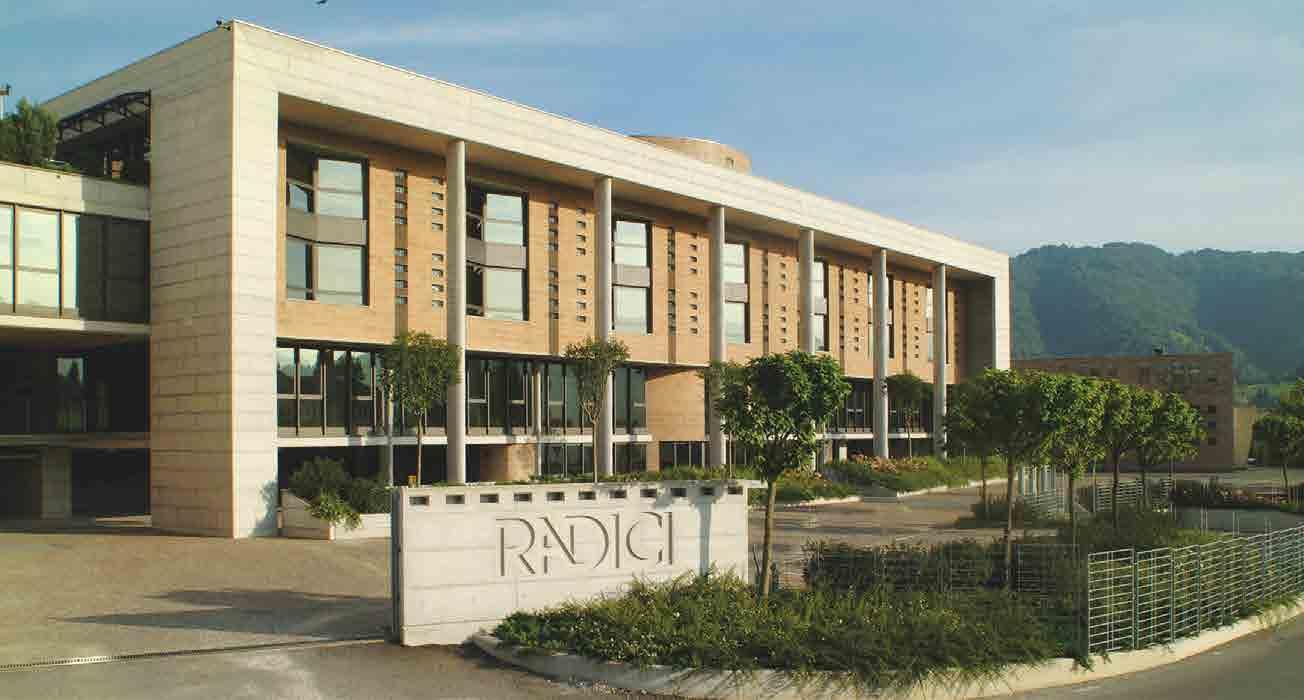
6 minute read
Under your feet and over your head
In addition to offering innovative products, specialist in spunbonded non-woven fabrics and yarns for artificial grass, Tessiture Pietro Radici SpA, is focused on being a positive force in terms of economic, social and environmental responsibility. Barbara Rossi speaks to its MD, Mr Enrico Buriani.
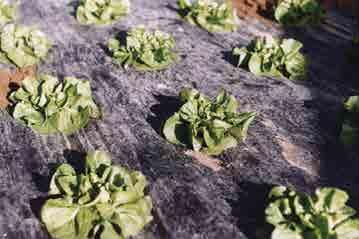
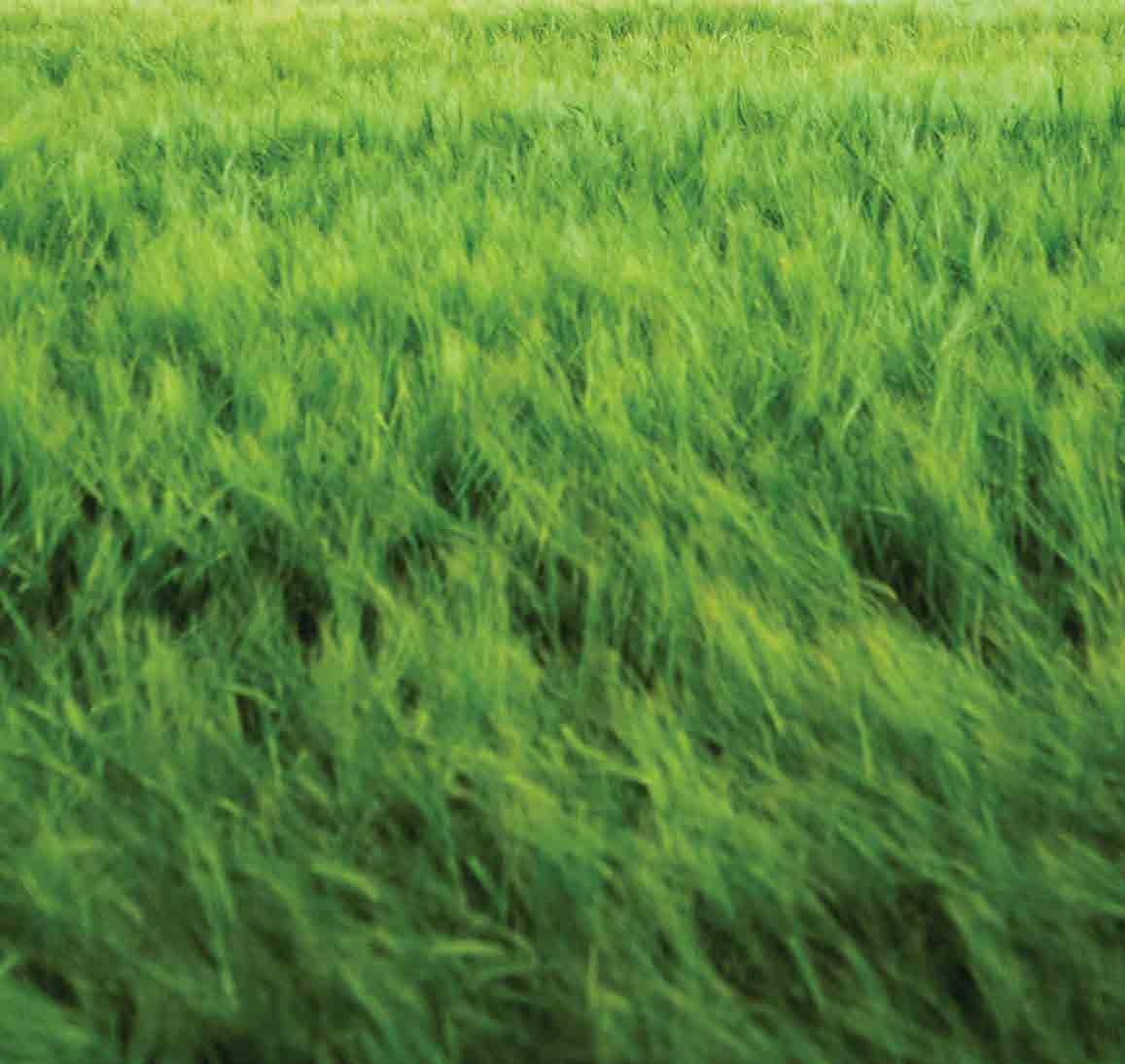

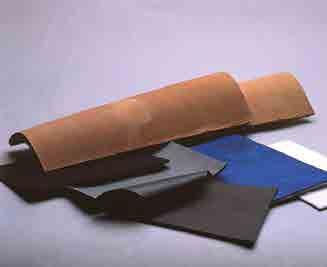
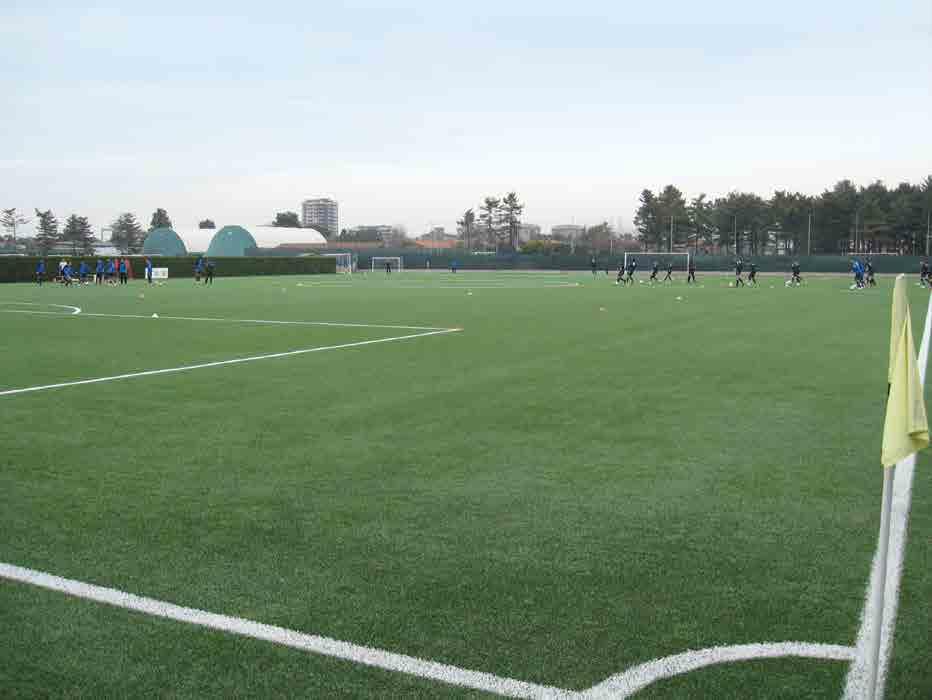
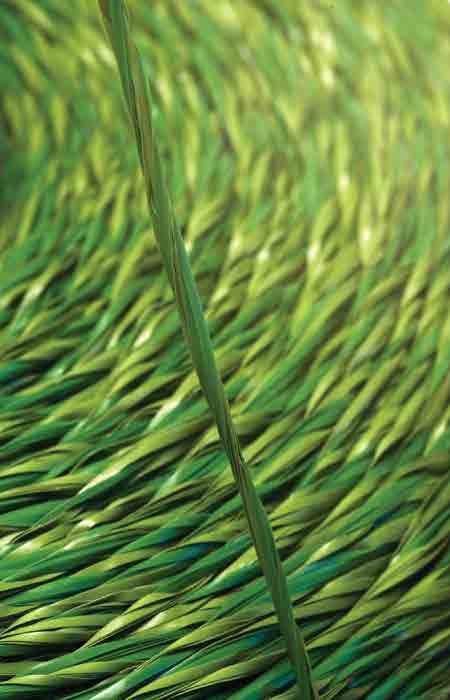
Tessiture Pietro Radici SpA belongs to the RadiciGroup, one of the most active Italian chemicals companies at an international level.
Tessiture Pietro Radici has a special role in the group, being its historical antecedent, established in the 1940s, and hence the entity from which the group expanded. The company shares its location with the group’s headquarters in Gandino, 20km from the northern Italian town of Bergamo, where it was first set up and where the Radici family still resides.
RadiciGroup, a leader in nylon chemicals, has a range of activities: its diversified businesses are focused on chemicals, plastics and synthetic fibres. The group turned over €1.2 billion in 2011 and employs about 3500 people worldwide. In fact, while the RadiciGroup, as its name suggests – Radici does indeed mean roots – is strongly rooted in the Bergamo area where it was first born, over the years it has also acquired a real international dimension. Today the group has production and sales sites in Europe, North America, South America and Asia and its products are used in applications such as apparel, sports, furnishings, automotive, electrical/electronics, home appliances and consumer goods. RadiciGroup, with its chemicals, plastics and synthetic fibres business areas controlled by parent company Radici Partecipazioni SpA, is part of a larger industrial group that also includes textile machinery and energy businesses.
As a company, Tessiture Pietro Radici SpA has a turnover of €40 million and about 150 employees; its two registered trademarks are Dylar® and Radigreen®. The former is made up of non-woven spun bonded polypropylene fabrics, while the latter is polyolefin yarn for synthetic grass.
Mr Buriani explains: “when the company first started, in the 1940s, it was manufacturing blankets. Over the years the production focus shifted several times. We have been engaged in our two current strands of activity for about ten years now. Actually the group started with Dylar® in the mid 1990s and with Radigreen® in the mid 1980s. Two different companies were carrying out these activities, which in 1997 merged into us. Since 2004, we have been concentrating solely on Dylar® and Radigreen®.”
Dylar®’s main application sector is construction – roofing in particular – where it is used as a supporting membrane underneath tiles, followed by HORECA, and hygiene and protective apparel. Radigreen®, synthetic grass, is employed in the sports sector, as well as for decorative-domestic purposes (landscaping). In the latter it is used, for instance, in gardens, parks, and wherever else the use of artificial grass is preferred to that of the natural version, also in order to lower or avoid maintenance costs. The company supplies semi-finished products, which are sold to companies which transform them into final applications, for instance in terms of Radigreen® to producers of synthetic grass carpets.
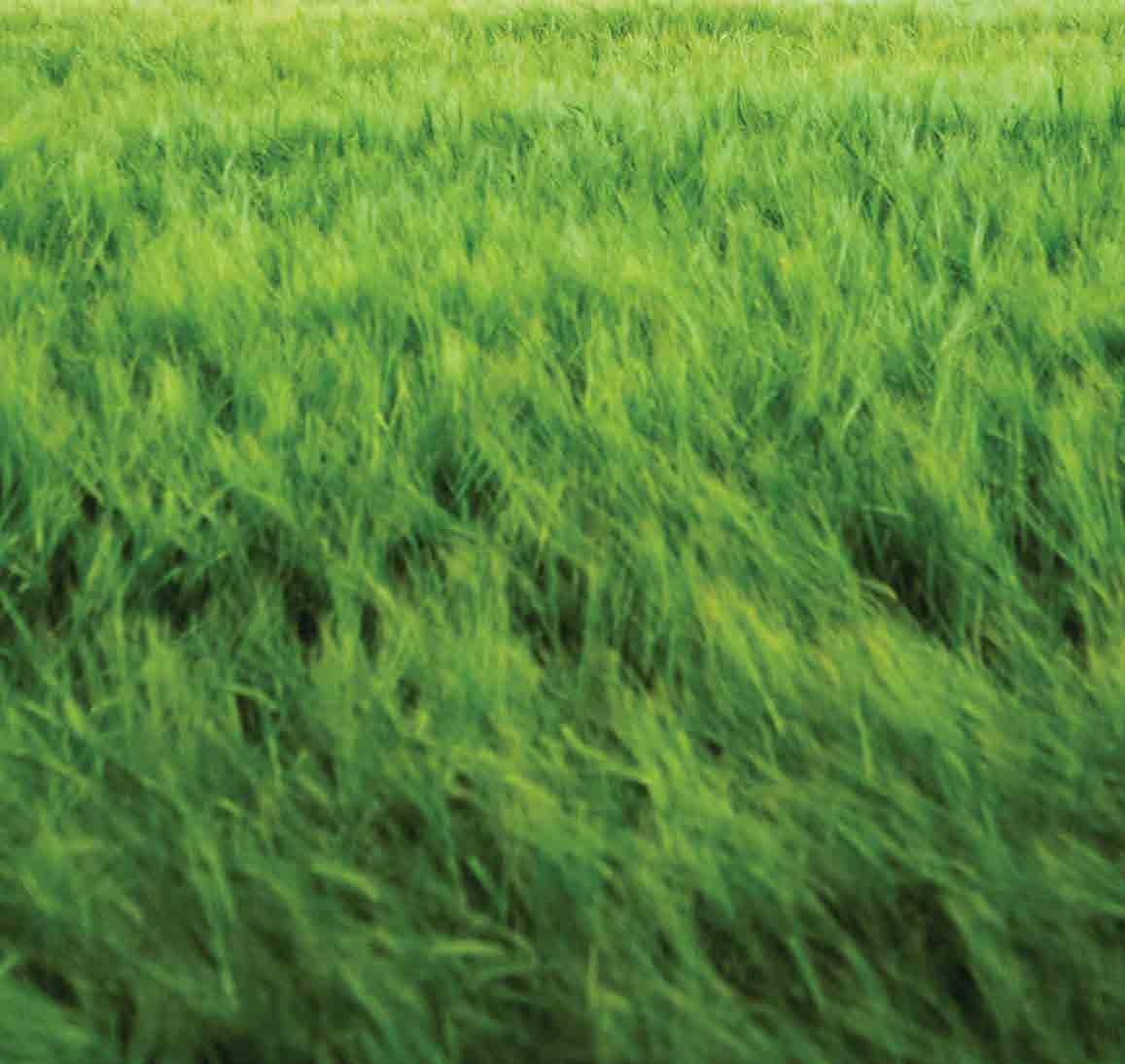
We are more than numbers
“Since the beginning of the new millennium we have carried out investments for the modernisation of our production activities. We are carrying out a progressive modernisation and strengthening of our production capacity so as to maintain our competition levels both in terms of prices and quality. We have our own R&D department which is continuously engaged in updating our product portfolio, in particular for synthetic grass, as this is a field in which product development, alongside product obsolescence, takes place at an extremely fast rate. Our R&D department can avail itself of a dedicated pilot facility, thus being able to carry out its activity, focused on industrial development, independently from production operations. Our commitment to research and
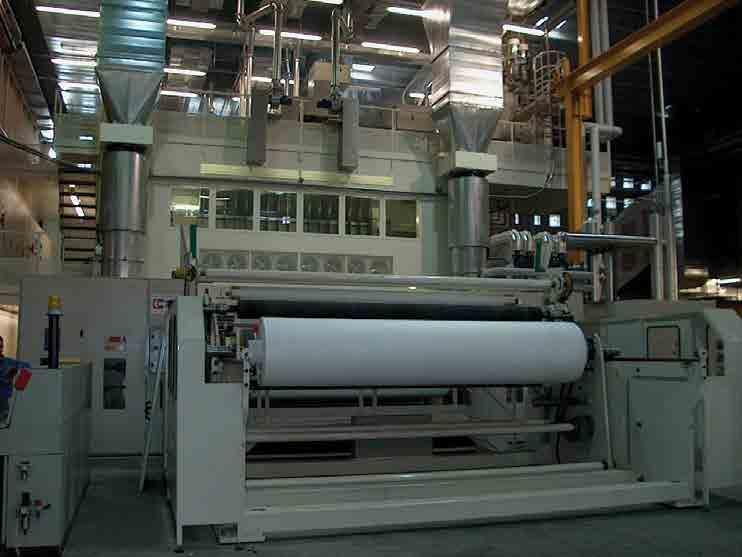
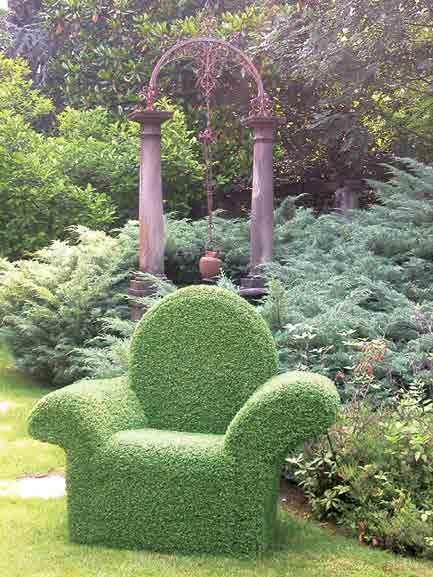
innovation really pays, as 20 per cent of the 2012 synthetic grass turnover derived from new products.
“Our products are sold all over the world and export now accounts for 80 per cent of our production. Our main market is Europe, led by Germany and Belgium. In future the company is going to consolidate its current markets, as expansion of geographical boundaries is somewhat restricted by transport costs, especially, as far as spunbond non-woven is concerned. However, we could start serving new geographical areas if our clients were to relocate. In terms of our non-woven products we will have to evaluate what diversification may be achievable thanks to our technology. In particular we will examine how our technologies can be adapted to the transformation of new materials.”
“With regard to synthetic grass, I have to say that there is a certain market stagnation. In terms of both sports and decorative-residential applications there will be a trend towards a reduction of natural grass maintenance cost, alongside a tendency to exploit public green spaces in a more intensive manner, which would favour the synthetic grass sector. However, this implies an initial investment on the part of sports clubs and councils, which given the current economic difficulties, may prove to be difficult. Obviously this is a problem affecting all of western Europe, although Italy’s suffering is particularly acute. As a company we are perfectly ready to increase our volumes.”
The Group is particularly attentive to environmental sustainability. “Sustainability is a true challenge for our group,” said Filippo Servalli, corporate marketing manager of RadiciGroup. “All along our production chain – that is, from chemicals to plastics and synthetic fibres – we are committed to reporting our corporate responsibility performance according to Global Reporting Initiative (GRI) guidelines. What really counts on the sustainability front is taking action. Concrete action. Our words must be transformed into tangible results. Indeed, throughout the years, our group has been developing and will continue to develop products using renewable source materials, products made with post-consumer recycled waste and products that contribute to lowering CO2 emissions. We use methods such as life cycle assessment to measure and quantify product performance in terms of environmental impact. Furthermore, we are committed to developing and registering Environmental Product Declarations (EPDs) for our products, according to the specific requirements set forth in the Product Category Rules (PCR). Last but not least, in the communities where our production sites are located, we support projects and events on environmental protection themes and strive to raise the environmental awareness of our employees by promoting a shared group culture of sustainability – all the while, respectful of local communities, people and cultures.”
Specifically, Tessiture Pietro Radici SpA, which is already ISO 9000 certified, is working towards obtaining the ISO 14000 and OHSAS 18000 certifications, respectively covering environmental standards and occupational health and safety, which should be achieved by the end of the current year. n
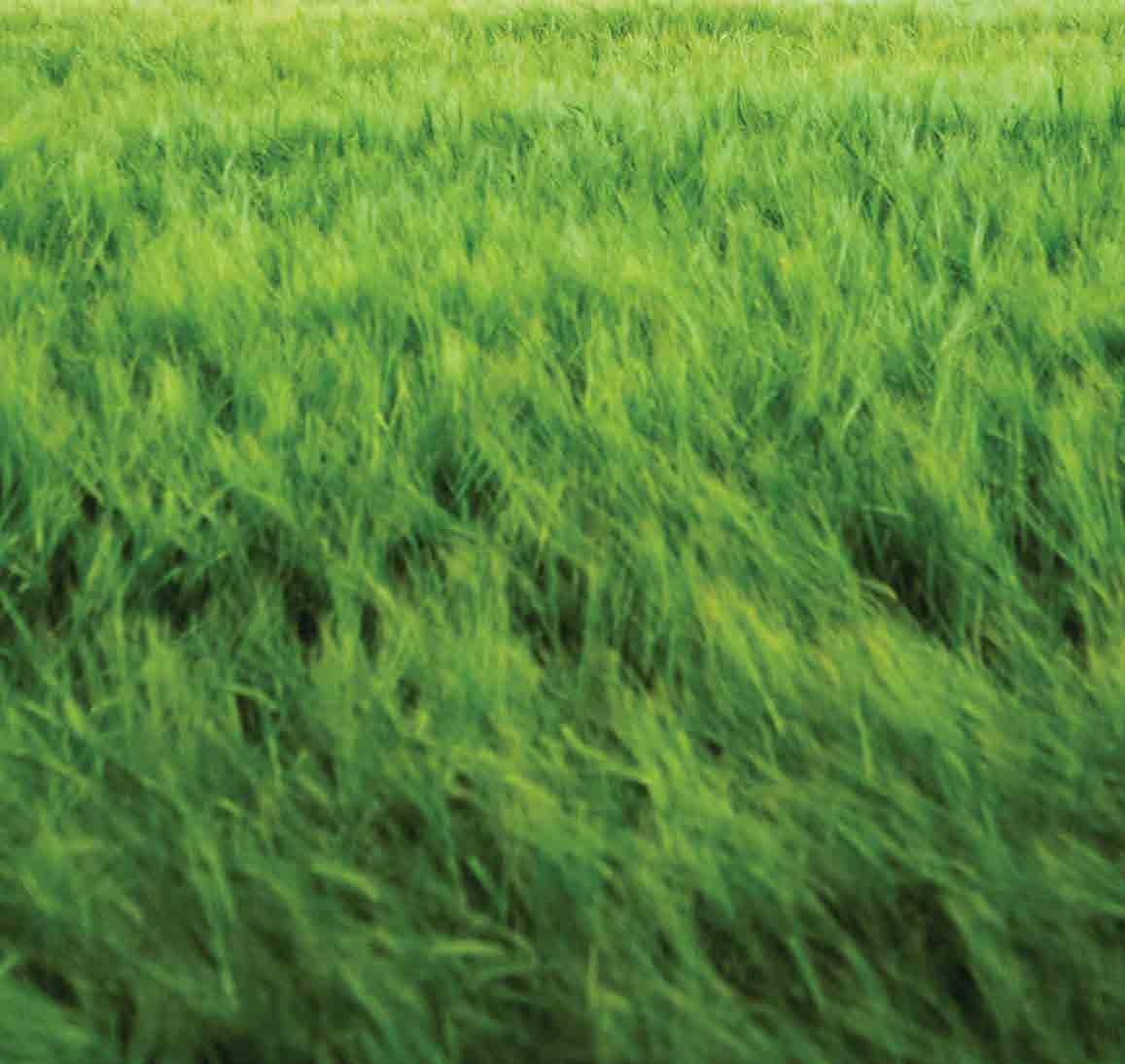
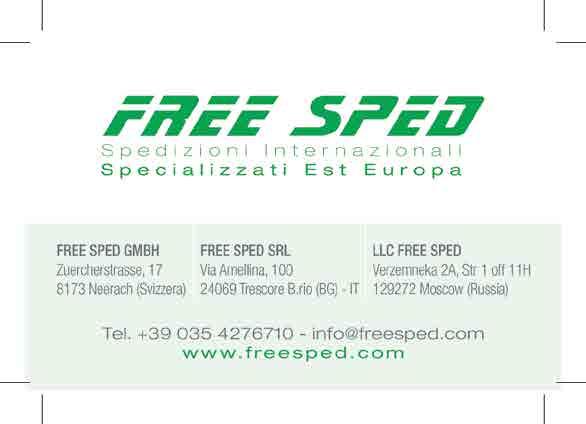
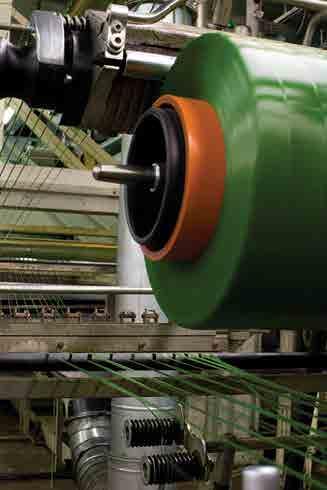