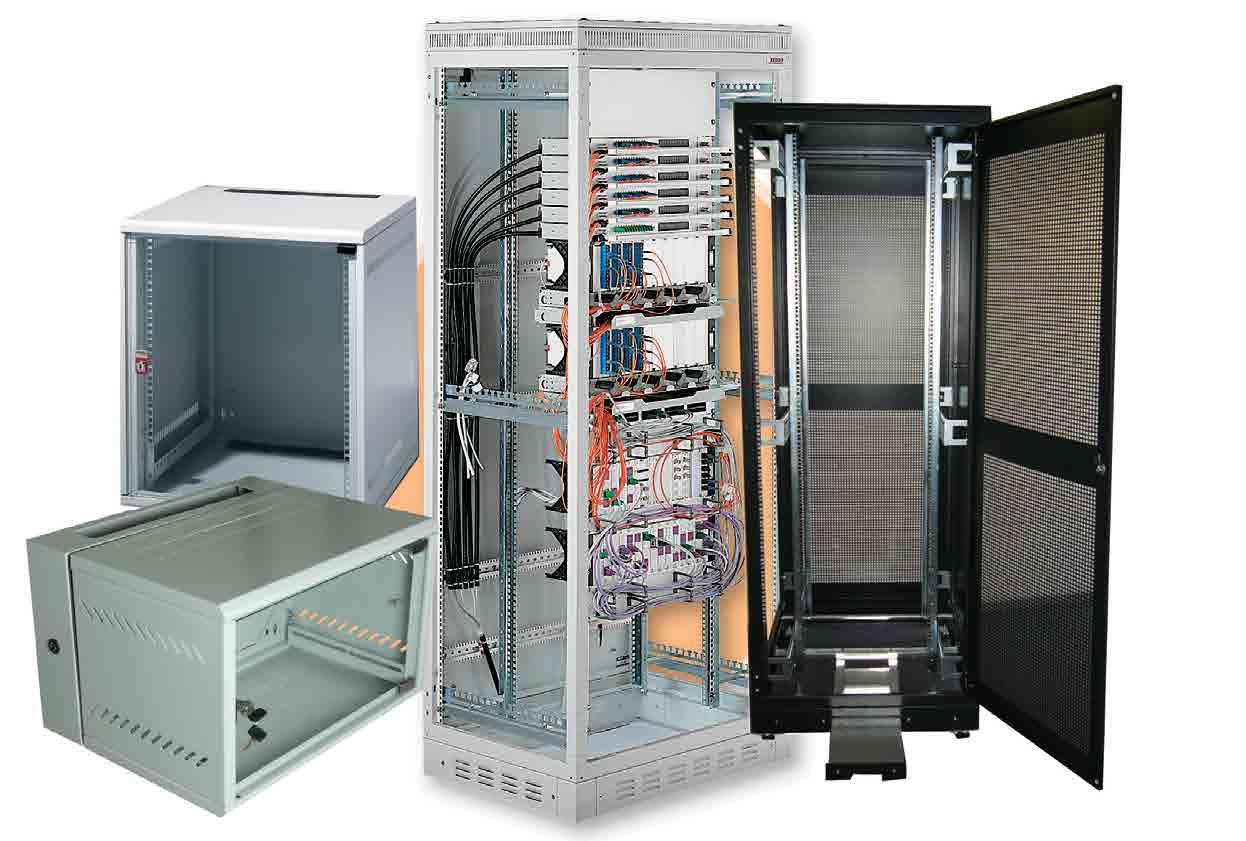
5 minute read
Going the extra mile Eldon Group
GOING THE EXTRA MILE
The Eldon group delivers enclosure systems engineered to boost the success of its clients’ businesses. Industry Europe looks at the solid success behind this globally operating company.
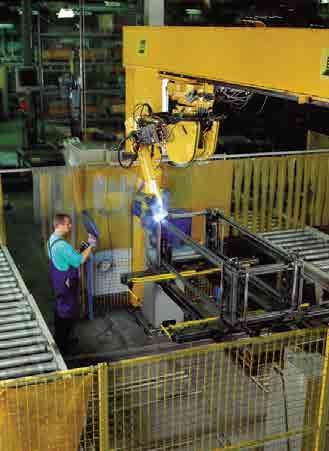
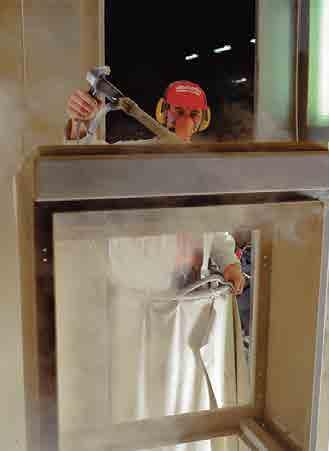
The Eldon Group focuses on the development and manufacture of enclosures, switchgear and electrical distribution systems. Owned by EQT Partners since 1999, Eldon was originally Sweden-based but now has its headquarters in Madrid and employs 450 people.
The group has a global presence, with representation in 45 countries, giving it the local technical and service support skills to ensure the success of its clients wherever they are. Founded in 1922, Eldon has been operating for over a century so its success is built on solid foundations. Production facilities
All Eldon’s products are sold under the Eldon trademark and manufactured at plants in the UK, Romania and India. These state-of-the-art plants are focused on supplying mission-critical, quality-approved standard enclosure and accessory solutions, as well as standard special solutions, for a broad spectrum of power distribution and control applications to different industries, including machine building.
The most recent of Eldon’s manufacturing facilities was opened in Brasov, Romania, in 2007. Here the group manufactures standard wall mounted as well as floor-standing enclosures in both mild and stainless steel, accessories and parts. Meanwhile its factory in Rotherham, UK, manufactures its complete range of stainless steel enclosures. Lastly, the factory in Umbergaon in India manufactures standard wall-mounted and floor-standing enclosures, plus terminal boxes, as well as standard specials.
Unique solutions
Eldon’s wall-mounted, floor-standing and console solutions are available in a variety of materials, including mild or stainless steel, aluminium, fibreglass-reinforced polycarbonate, GRP, ABS and polyester. Furthermore its full range of accessories includes fixing systems, thermal management, multiple shelving and door configurations, baying, hinging and smart cable management. This is in addition to a number of general purpose devices including lights, door switches, power sockets, signal towers, din rails, cage nuts and screws.
The company is able to adapt its solutions to meet the exact needs of clients in any industry sector. It will modify its standard enclosures to incorporate custom hole patterns and different colours and dimensions. Up to 85 per cent of Eldon’s sales are of ‘standard’ products, with the balance made up of products with small or large modifications, or totally new ideas.
“We try to make sure in our basic products that we are continuously looking at new materials and solutions and ways of doing things, to solve the customers’ problems,” says a company spokesperson. “The trend in the business over the past 10 to 20 years has been that, as electrical components have been getting smaller and smaller, so the enclosures
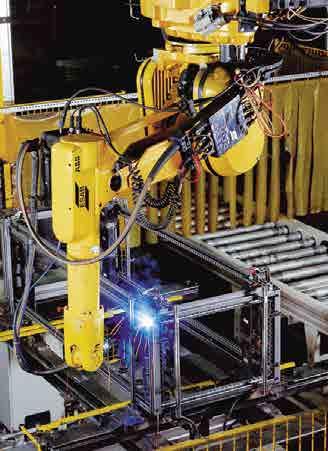

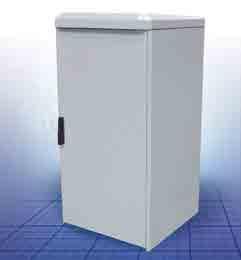
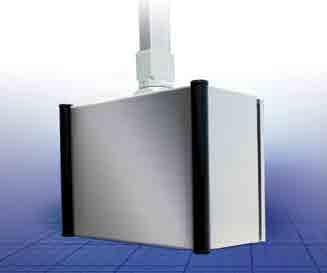
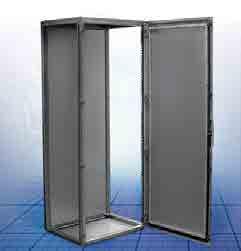
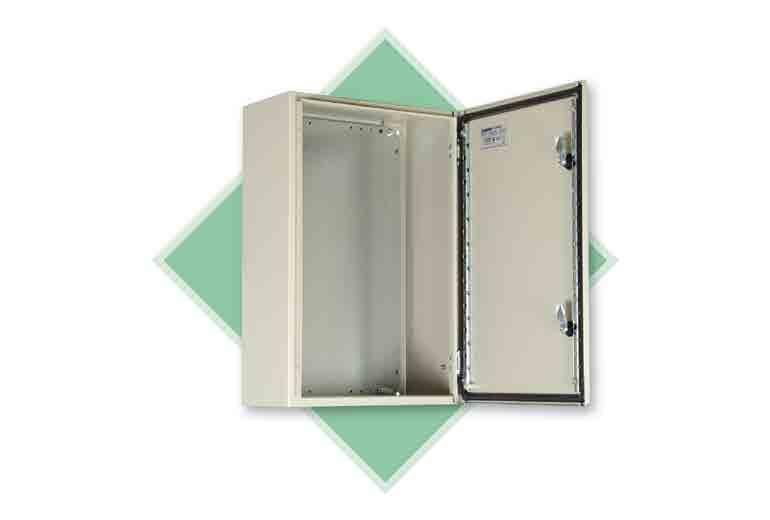
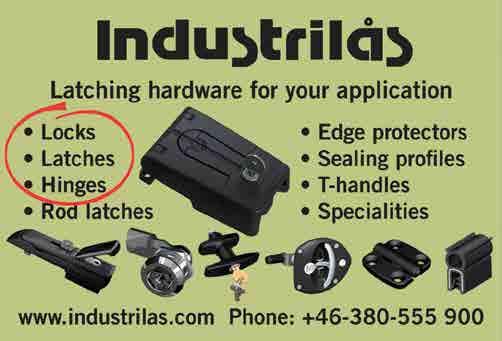
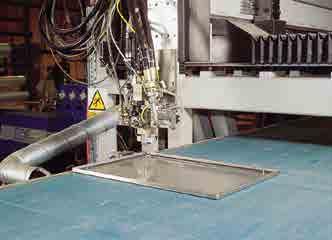
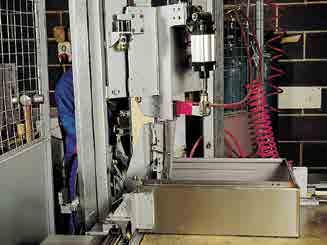
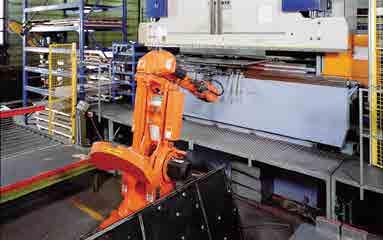
required have also been getting smaller. However, they still emit a lot of heat, so the requirements of removing heat from the enclosure are getting bigger. So you have to have good thermal solutions with fans, air conditioning, etc. We have to be a solutions type of partner to the customer.”
There are three key customer types served by Eldon – electrical wholesalers, panel builders and OEMs – manufacturing products such as CNC machines, lathes and other machinery that needs electrical controls and, therefore, an enclosure for the controls.
Recent success
Eldon can count many of the major European players amongst its clients. For example, in February this year (2013) Bombardier installed its floor cabinets in LKAB’s mine in Kiruna to house the latest control system, called OCS950, for trains, points and signals on railway traffic. Mines, subways and common rail systems are examples of possible areas where this control system can be used.
The first contact between Eldon and Bombardier was established in 2009 in order to jointly examine how to develop and homogenise the existing control systems to be more efficient and better. Until today, these solutions have, to some extent, been country specific and varying. Multiple control systems and a variety of cabinet solutions were used.
Bombardier wanted to develop a smarter and more efficient system in a series of base cabinets. These will form the basis for OCS950 over the world. To develop a unified system which is equivalent and standardised across the globe was a priority.
“We were actively looking for a flexible supplier that was willing to work with us to develop a really good solution for our new and improved OCS950 system. It is also very important to be able to supply us with cabinets of the highest quality with fairly short lead times. Eldon has shown that they are willing and able and to do that and we have a very good and constructive cooperation,” says Benny Slotteborn, product manager, Rail Control Solutions (RCS) at Bombardier.
The requirements for the new enclosures are high. They should be uniform in the structure of the interior so that they can be easily customised for the needs at each railway project. Eldon meets the needs of the system using modules that are added to a basic configuration of OCS950.
Logistics demands
Eldon works with distributors around the world in order to cover all of its markets. There is a central warehouse in each of the four key countries – Sweden, Spain, the Netherlands and the UK. Products are manufactured and sent to these warehouses, to be shipped to distributors or direct to customers.
It is working continuously on new markets, where it has two types of operation. First, it has its own sales people and warehousing and it is supplying directly to customers. Secondly, it is working with one exclusive distributor or agent who is serving that country. It has dedicated distributors doing the job that it is doing in its more local markets and that is really growing. It is finding more and more global channels for its products. n