
8 minute read
High tech milling systems Fidia
HIGH TECH MILLING SYSTEMS
The days of milling process collisions due to machine errors during production are over, thanks to the software and numerical controls offered by Fidia SpA, as Barbara Rossi discovers when talking to the company’s high speed milling division communication area manager, Mr Piliego, and to its co-funded research manager, Mr Tamburini.
Fidia SpA has grown and evolved in a significant way over the years, after being founded by its current CEO Mr Giuseppe Morfino in Turin in 1974. At the start, its activity was entirely focused on the production of numerical controls for complex form milling. In the 1980s the company had already grown in terms of staff and turnover, and had opened a series of foreign branches, while the 1990s saw the introduction of numerical controls for high speed algorithms and the start of its own high-speed milling machine production. This led the company, which has always had an international vocation, to reorganise itself in two areas, namely electronics and mechanics, opening two mechanical manufacturing sites, respectively in Turin and Forlí. This was followed by the establishment of the first Chinese branch, of a solely commercial and support nature, just like the other foreign sites. The first decade of the 21st century saw the company being listed on the Milan stock exchange and acquiring Sitra Automazione, a company based in the north western Italian town of Alessandria and specialised in the production of inverters and spindles. This was followed by the opening of a second Chinese site, as well as by the development of a third Italian manufacturing plant also based in Forlí.
Today Fidia SpA has a worldwide staff of 360, eight foreign branches, three manufacturing sites, electronics production taking place at its Turin headquarters (San Mauro Torinese), a turnover of €45m and a joint-venture in China (whose manufacturing is solely for the local market). High-speed millers (HSM), generating about 70 per cent of turnover, form Fidia’s core business, but the company is also specialised in numerical controls and digital drives, milling heads, accessories and software.
In terms of HSM, the company has a wide range of sizes and models of five-axes vertical millers. The last series developed in 2008 is Gantry which, given the large dimensions of its models, is particularly important because it extends the applicability of Fidia machines to pieces of a size up to 20 metres and more.
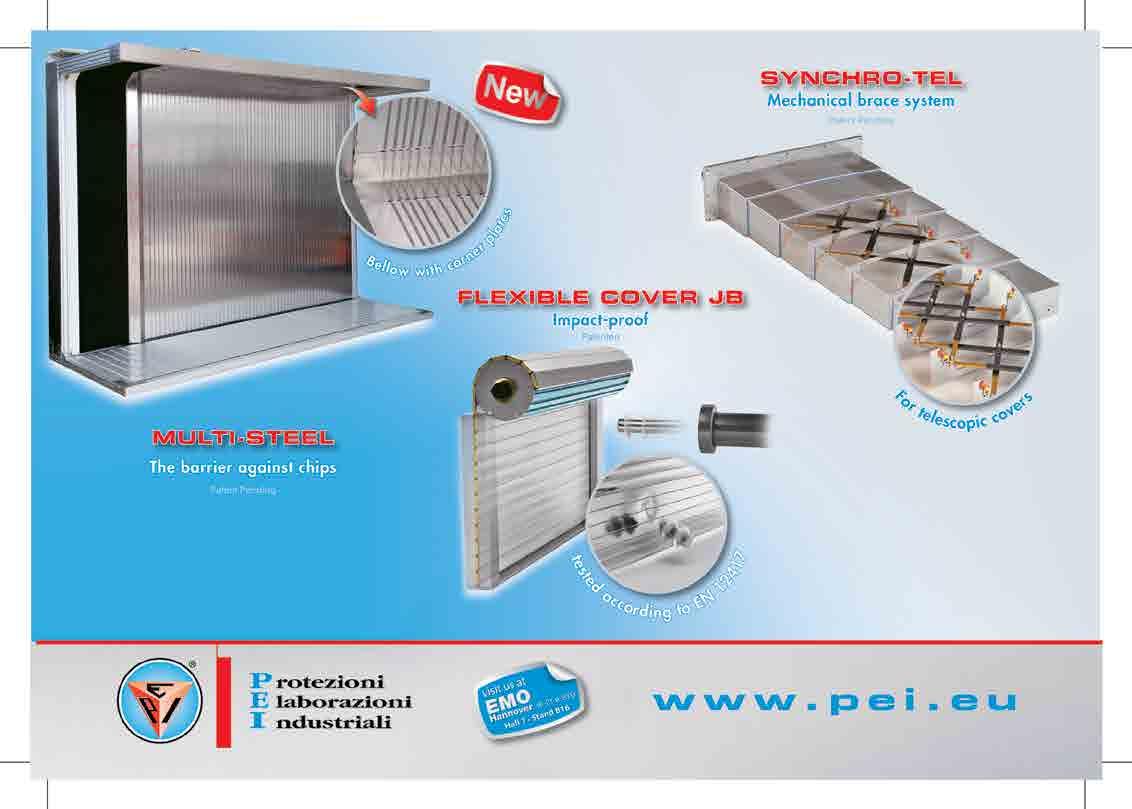
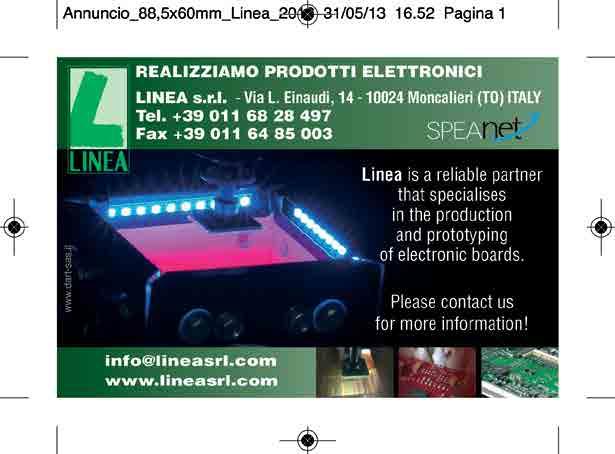
Stöber
New, high efficiency rack and pinion drives with innovative pinion bearing for machine tool
A new compact solution is developed from Stoeber Antriebstechnik -Germany. The ZTRS drive are based on a Servofit precision gearboxes with integrated supporting bearing, that increased significantly the power density.
The additional supporting bearings permit to reduce very strong the load on the bearings of gearboxes. Due to this highly stiff design is achieved a very high drive tilting moment, an increasing of linear stiffness and reduced linear backlash.
Also one of the important Italian machine tool manufacturer like Fidia is using this innovative solution that permits maximum feed forces.
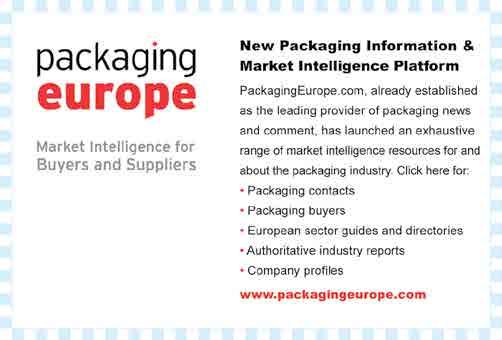
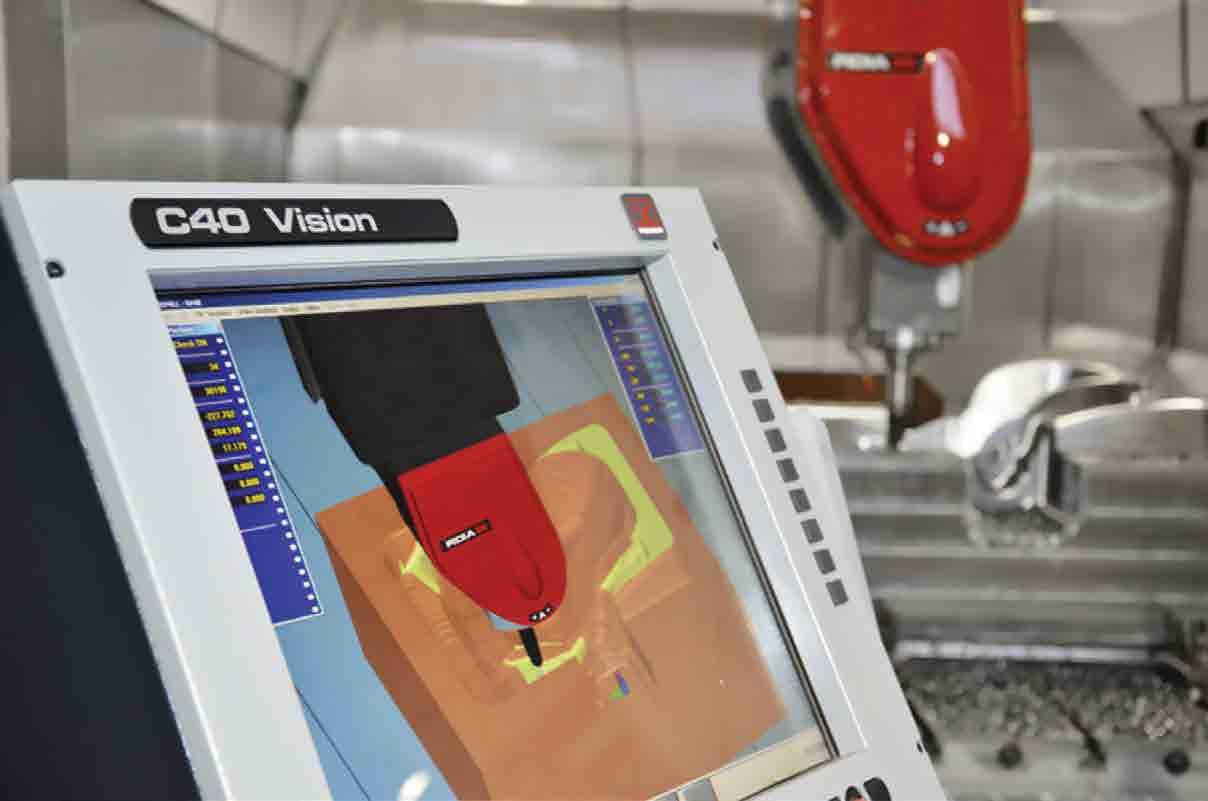
The company has a vast range of clients and works to find solutions to their needs. For instance, all the milling heads produced are proprietary and have been developed by Fidia to fulfil the needs of particular products and sectors (automotive and aerospace in particular). In terms of multi-axis numerical controls for high-speed milling of complex forms, the company’s offer is very wide and top of the range. All these controls are equipped with two totally independent processors, with two different and separate operating systems. Fidia also produces accessories and software, which can be included as extra optional features to its numerical controls, in addition to having patented HMS (head measuring system), an automated calibration and measuring device that can be employed for all rotary axes on a machine tool, such as various types of milling heads. The device is able to identify and correct geometrical errors, positioning precision and RTCP parameters.
R&D is extremely important for Fidia and this is the reason why annually the company invests more than 12 per cent of its turnover in this area, to which are dedicated almost 50 staff members. R&D is carried out on a continuous basis and is supported by co-funded research. It concerns all different aspects of the company’s activity, from new materials and control algorithms to business models and supply chain management. Mr Tamburini, Fidia’s co-funded research Manager, explains, “We have been involved in co-funded research for about 20 years, where research projects are co-funded by the European Commission, Italian Ministries or the Piedmont Region.”
ViMill, C40 Vision and Look Ahead version 5
One of the results of the R&D activity is the recently developed, patent pending ViMill tri-dimensional software. This product is able to visually check any possible collision or unexpected movement between tool, head and machine and the actual workpiece, just before pressing the start push button or during the actual milling process. ViMill fills a market hole, because, unlike other simulating products which operate before the actual milling process, thus reducing but not eliminating errors, ViMill is an on-board software, operating just before and during production. When a problem is identified, the milling machine is put on hold and an alert is generated, allowing the operator to decide on the course of action to take. ViMill also safeguards the operator’s manual movements, thanks to a safety buffer with a lower volume limit of a few millimetres placed around the tool and the work piece. Here again, the same warning procedure is activated when the machine enters the security measures.
Fidia also offers two control architectures designed to be used by clients who adopt ViMill on board their machines: C20 Vision and C40 Vision. The latter is a totally new numerical control featuring a touch-screen graphic interface, while the former is a new
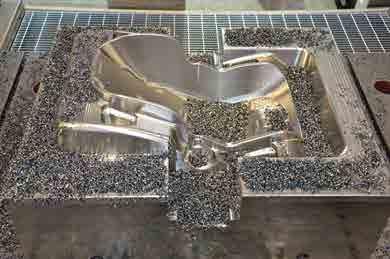
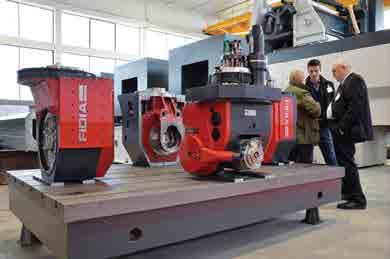
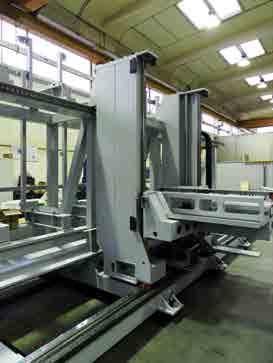
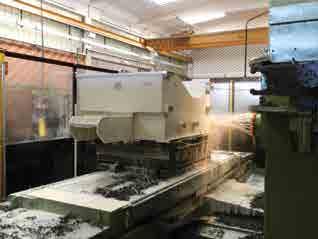
CMI Srl has been active in the engineering industry since 1978. We specialise in machine tools and its production facilities cover an area of 12,000m2 .
The range of services we offer customers is extensive and comprehensive, and includes:
• Carpentry light / medium / heavy • Machining department with advanced machinery •Assembly and wiring of complete groups • Industrial painting • Experienced design and engineering team
Our company co-operates with major customers and has acquired extensive know-how in a wide range of technological fi elds, allowing us to be a point of reference and a competent authority for any kind of customer request.
Via Ponticella, 4 • 29018 LUGAGNANO VAL D’ARDA(Pc) - ITALY Tel: +39 0523 892744 • Fax: +39 0523 891998 E-mail: mario.sgorbani@cmi-piacenza.com • www.cmi-piacenza.com

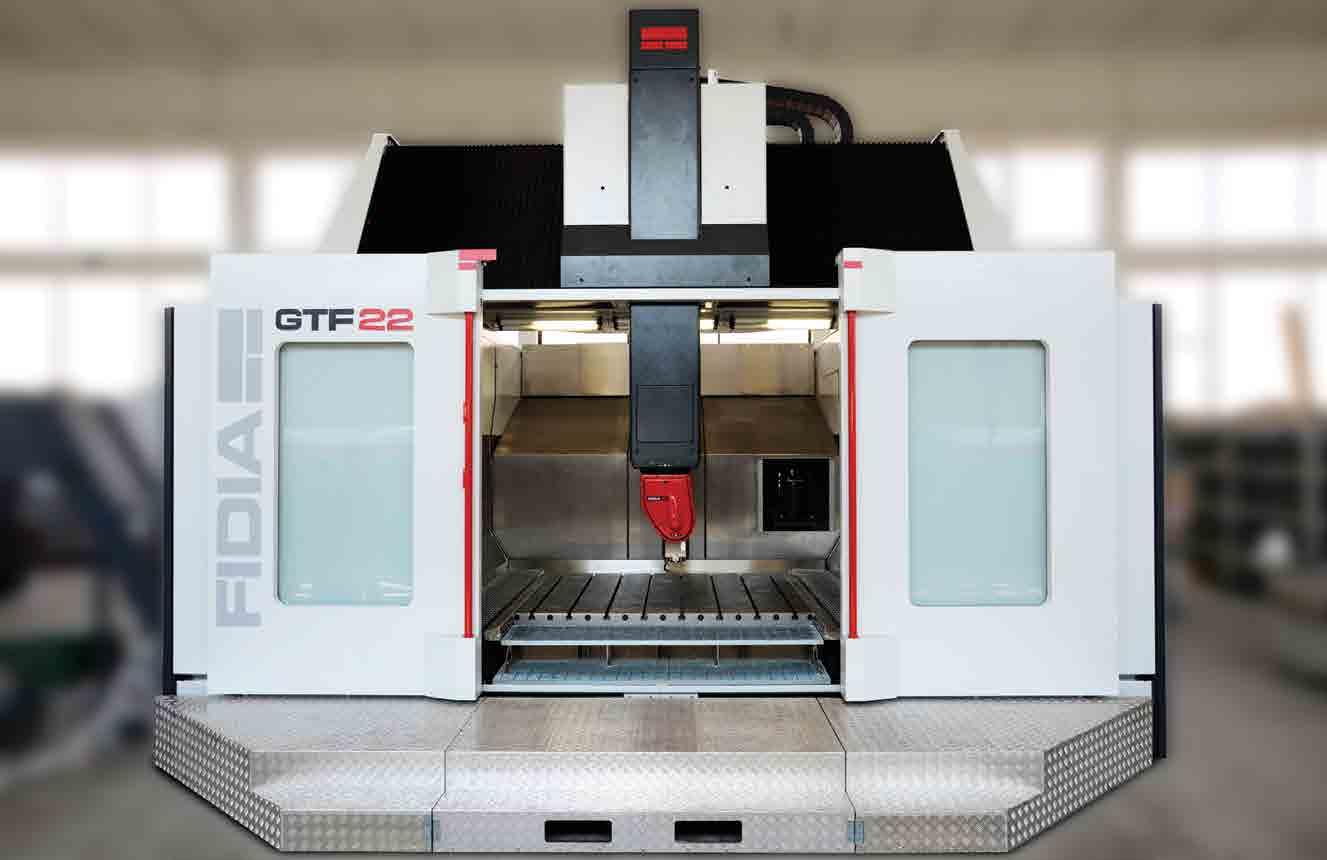
version of an existing numerical control. Mr Piliego also highlighted the new Look Ahead version 5 algorithm. “Since January 2013, this algorithm has been integrated in all of the company’s controls from the entry level Nc 15 to the C40. It offers an interesting performance, as thanks to it, it is possible to obtain an increase of production quality, as well as saving 30 per cent of cutting time.
“All of our production, both in terms of mechanics and electronics, takes place in Italy and much of it is for the international markets, which we supply thanks to our network of branches. Where we cannot be present with a direct branch, we operate thanks to a service centre. We are always close to our clients to provide assistance, spare parts and other services, both during and after the guarantee period. I think that both our electronics and mechanics production gain from the synergy deriving from the fact that all our production sites are relatively close to each other, as this has also allowed us to rationalise our supply chain, something which is reflected in the final price. Furthermore we can present ourselves to medium to large clients as an only supplier, able to supply a range of products and services.
“In terms of HSM machines our main market segments are aerospace and automotive, while with regard to numerical controls we serve a wider market range, also including energy, marine, white goods, automotive or industrial design prototypes and sheet metal moulding. Overall automotive and aerospace account for about 70–80 per cent of turn over, but the balance between the two varies according to the year. Geographically speaking China is still our main market, although in the last year we have witnessed a re-balance between China and the West. Today, China generates about 60 per cent of turnover, with the remainder originating in western markets, thanks to demand in the USA, Europe and Brazil, but we have clients in all the four industrialised continents. Due to the success of our Gantry series of HSMs and the volume growth that we are experiencing in our mechanics division, we have planned for, the construction of a new 4000m2 production site in Forlí.” n
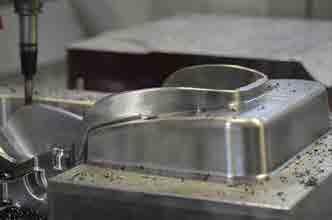
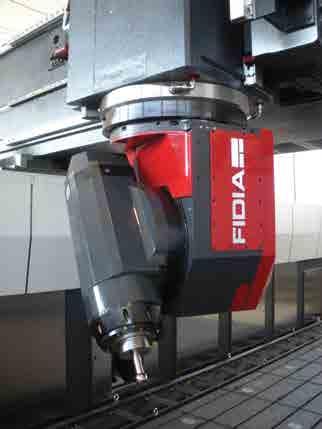
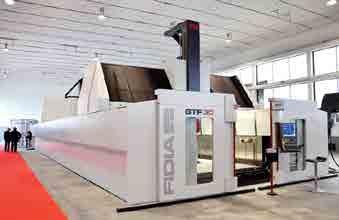