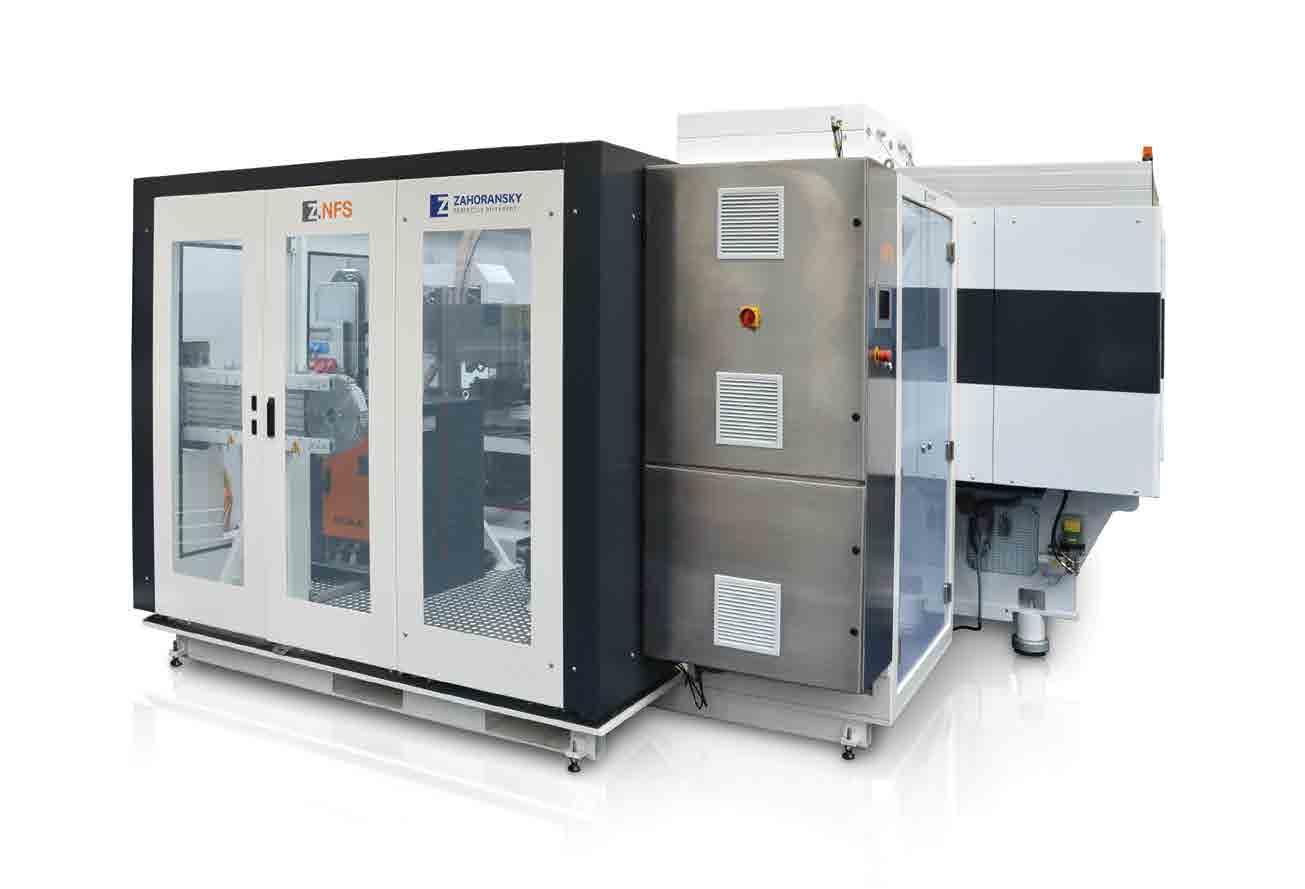
4 minute read
World-beating manufacturing systems ZAHORANSKY
WORLD-BEATING
MANUFACTURING SYSTEMS
ZAHORANSKY is the global leader in the development and manufacture of sophisticated equipment for the manufacture of toothbrushes, household and industrial brushes, injection moulds and medical devices. Philip Yorke talked to Gerhard Steinebrunner, the company’s managing director about its unique, innovative products and move into new markets.
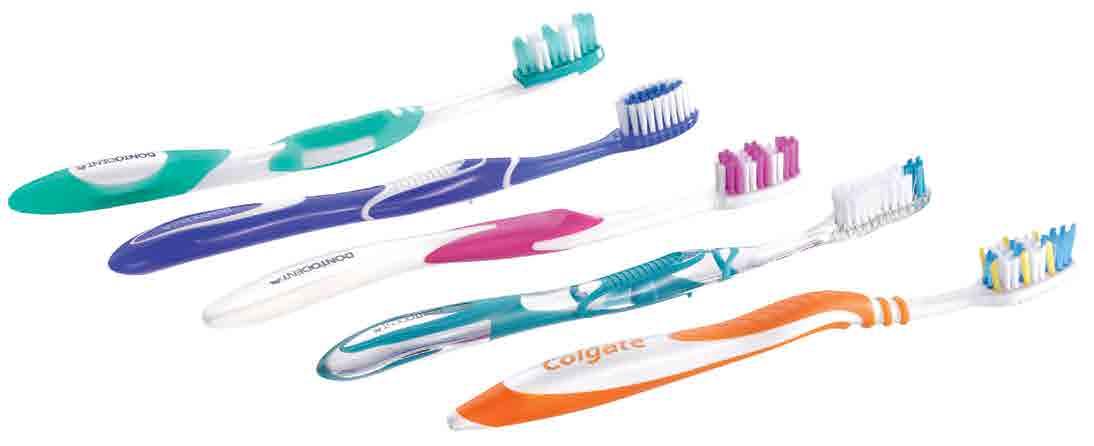
ZAHORANSKY was founded in Germany in 1902 by Anton Zahoransky and it opened up a new era in brush production when he developed the world’s first reliable tufting tool for a drilling and tufting machine for brushes. Since then the company has remained an independent, family-owned business and has grown to become a global market leader that offers complete business solutions in the field of machine building and automation technology. Currently the company operates four distinct divisions: Mould making, Systems technology, Packaging machines and Brush machines.
Today the ZAHORANSKY Group is present in 10 locations in six countries with global representation and branch offices worldwide.
In 2013 the company employed over 600 people and recorded revenues of more than €70 million. Expanding product portfolio
ZAHORANSKY manufactures a diverse range of machines that are capable of producing a wide variety of products from small interdental brushes, mascara and hair brushes and tooth brushes, to brushes for personal care. In addition the company’s portfolio includes hand brushes, brooms, hard brushes, as well as WC and dish wash brushes for household use. However, the company is expanding its product portfolio further with particular emphasis on the medical industries where its advanced technology can play an important role.
Steinebrunner says, “Our automation technology leads the field and this is endorsed by the blue chip companies that rely on our hightech equipment. This includes companies such as P&G, GSK and Unilever. We have become a one-stop-shop where companies like this rely on us to set up a complete production line. We are the clear global brand leaders in most of our chosen disciplines and especially when it comes to the manufacture of toothbrushes where every second toothbrush in the world has been made on a ZAHORANSKY machine.
“Companies such as P&G (Oral-B, Gillette), Freudenberg (Vileda) and Johnson & Johnson are all long-term customers of ours. The quality and reliability of our machines is widely acknowledged, which is supported by the fact that they have an operational life of up to 30 years. We have developed the most sophisticated technologies and the most reliable equipment in the world. Our products are at work in other industries too with companies such as Wilkinson and Siemens, and all these multi-nationals have their own culture and special requirements, so by nature we are very customer focused.”
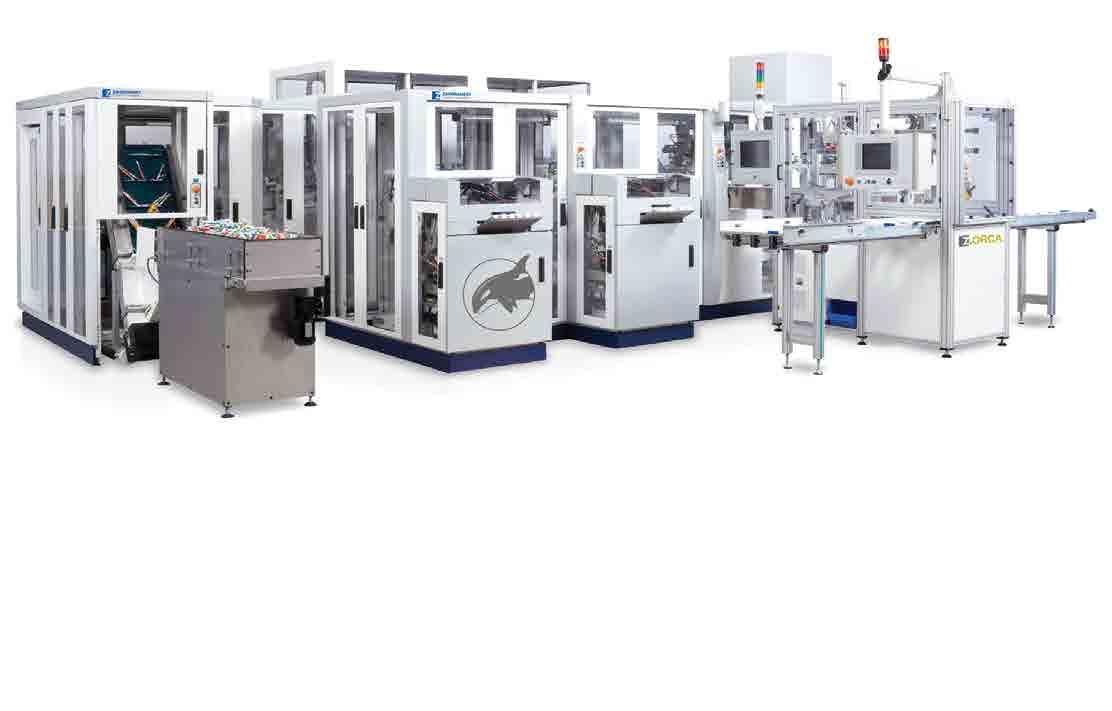
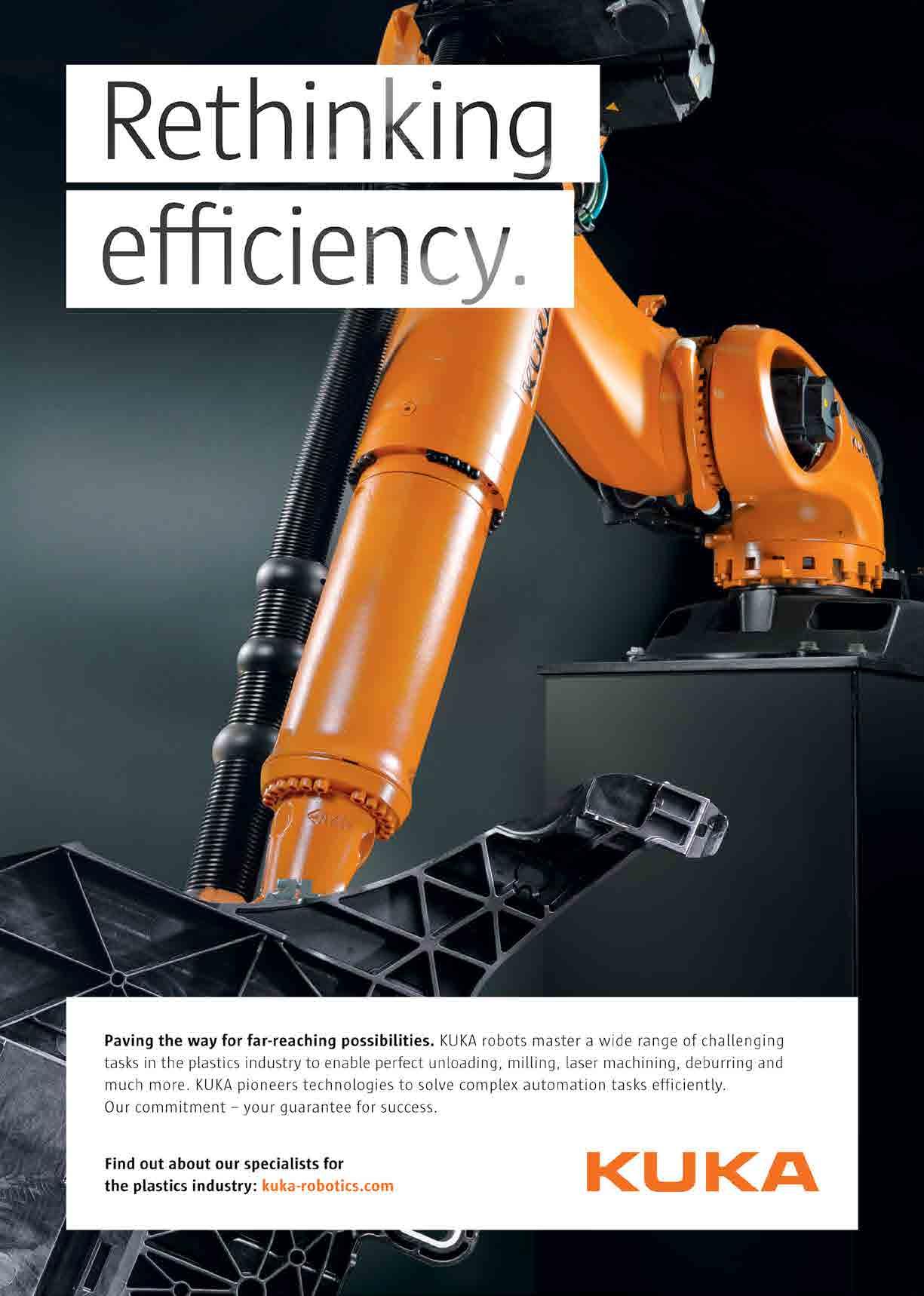
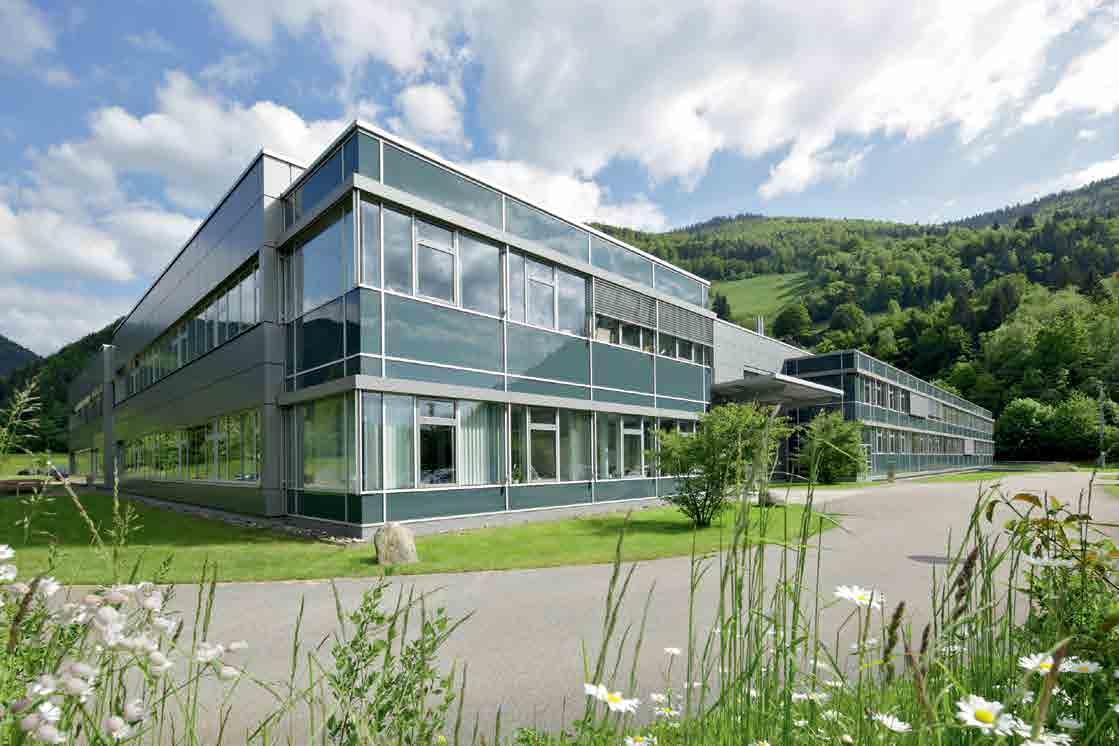
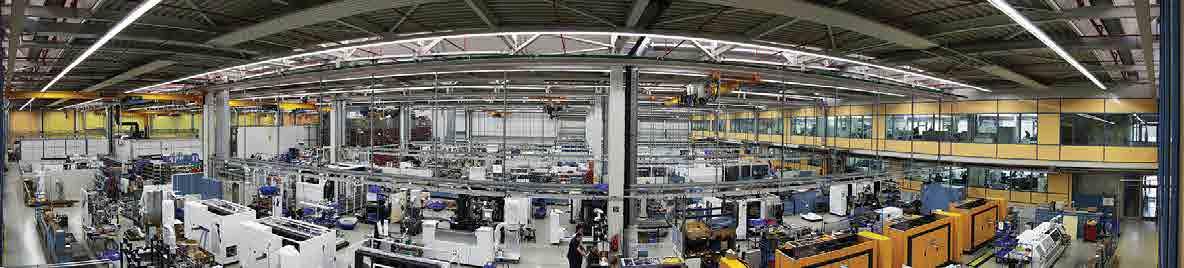
Steinebrunner adds, “We see our future growth coming from the industrial automation sector for our mounting processes. We also offer our advance technology to other industries that require robotics including the packaging industry. Recently we have seen significant growth in the demand for our needle-feeding systems for the medical industry.
“Around 80 per cent of our entire R&D is conducted in-house, including prototyping and testing, and much of the balance is coming from our close collaboration with our customers. We are also proud of our track record when it comes to after-sales service and technical support. Our customers benefit from online access for trouble- shooting and they also can rely on our very fast spare parts service as well as a global network of engineers who are on stand by to fly out to any location the same day if required. We also keep to our delivery dates and our ecofriendly processes are continually upgraded. In fact in India we are the top-rated company for operating the most environmentallyfriendly ‘green building’ in the country.”
In 2013 ZAHORANSKY opened a new, purpose-built facility for making injection moulds and machines in India and this will act as the company’s centre for serving its customers throughout the region. The state-of-the-art 2,500m2 building was formally inaugurated in November 2013. Today ZAHORANSKY has manufacturing locations in Germany and Spain and the addition of this new facility will mean that its customers in that region can be supported and served around the clock.
Award winning technology
Throughout its long history, ZAHORANSKY has made innovation a priority and this culture is manifested in every machine that it develops. The company recently won the coveted FEIB innovation award for its unique, fully automatic tuft quality control system. This advanced monitoring system substitutes manual quality control checks with its intelligent algorithm technology that eliminates defective brushes immediately.
The new mechatronic solution from ZAHORANSKY means that during production the tufting force of each tuft is measured and compared to a reference value. If the reading is outside the prescribed limits, the value is logged and displayed on the monitor. The unique system identifies and ejects defective brushes instantly. Furthermore, the sensor systems, hardware and controls have all been developed and manufactured in-house by ZAHORANSKY.
Greater efficiency
The ZAHORANSKY brand stands for reliability, precision and sophisticated technology and is driven by the constantly increasing demands of its customers. As far as improving production efficiency in the injection mould making process is concerned, integrating upstream and downstream working processes cannot be avoided according to ZAHORANSKY. This is precisely where the company’s systems technology is most valuable. Its specialists develop innovative concepts, modules and solutions for the integrated automation of injection moulding production processes, specifically for the manufacture of plastic products in the consumer, medical technology and cosmetic sectors. n
For further details of ZAHORANSKY’s innovative products and services visit: www.zahoransky.com