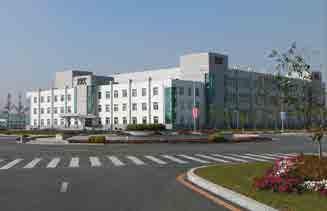
4 minute read
Magnetic technology leader Vacuumschmelze
MAGNETIC TECHNOLOGY LEADER
Vacuumschmelze GmbH, a manufacturer of advanced magnetic materials and related products for the automotive and many other industry sectors besides, continues to expand its range of world-leading products.
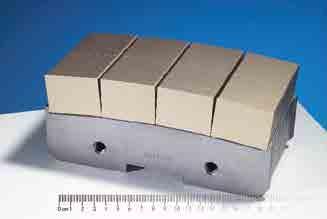
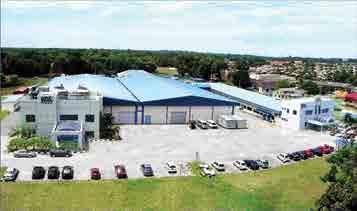
Established in 1914, Hanau-based Vacuumschmelze GmbH has seen continuous expansion and a long-term dedication to staying at the very forefront of innovative materials development, resulting in annual sales of €325 million and over 3800 employees in 50 countries.
Although particularly well-known for its materials for the automotive industry, many multi-national industry sectors use Vacuumschmelze products as an integral element of their optimised production. The magnetic alloys that are melted in VAC’s main production facility in Hanau are used in communication and medical technology, the space industry and for clocks and watches.
The company’s product range is divided into semi-finished products in the form of tapes, strips, round rods and wires that can then be further processed by the customer to create cores, components and permanent magnets. The company also produces winning products for optimised production such as the innovative adhering varnish VACCOAT 20011, which represents a completely new coating and manufacturing process for segmented sintered neodymium iron boron magnets, also known as NdFeB magnets). New product innovation
Vacuumschmelze has increased its development and manufacture of new products and solutions. Some of these were showcased at the electronica trade show, which took place in September 2014. Its current sensors now feature advanced integration of electronic components thanks to the development of a new highly integrated circuit. This new 4648-xxx family of sensors are fully compatible with their predecessors.
At this year’s CWIEME (Coil Winding, Insulation & Electrical Manufacturing) trade fair in May, the company took the opportunity to present its impressive range of core stacks for electric motors. Core stacks of its VACOFLUX 48 alloy can now be manufactured with a significantly reduced strip thickness of 50µm. In addition to this premium technology for ultra-advanced requirements, it also presented stamped lamination stacks from VACODUR 49 as cost-optimised alternatives for large production runs.
Furthermore, Vacuumschmelze’s technical developments in the field of CoFe alloys are already well-known in the world of motor racing and have also demonstrated their superiority in ‘junior’ competitions. The new VACSTACK core stacks, containing VACOFLUX 48 laminations, are installed in the new racing car entered by ETH Zürich in the Formula Student Electric championship.
Staying green
With each new development, Vacuumschmelze is compounding its commitment to offering ‘Advanced materials – the key to progress’ – its vision and marketing slogan that is present across its website and literature. As the company leads the way in developing, manufacturing and distributing green technologies for the benefit of its wide-ranging client base, its technical know-how and continuous innovation is clearly evident.
Many materials and semi-finished products originating from Vacuumschmelze have already proven their excellence in the field of renewable energy, particularly as the new current sensors used in solar inverters have been created at Hanau. These sensors help to monitor the output alternating current from solar systems in the power supply and the direct current element. Compared to typical Hall element compensation sensors, the many advantages of the VAC current
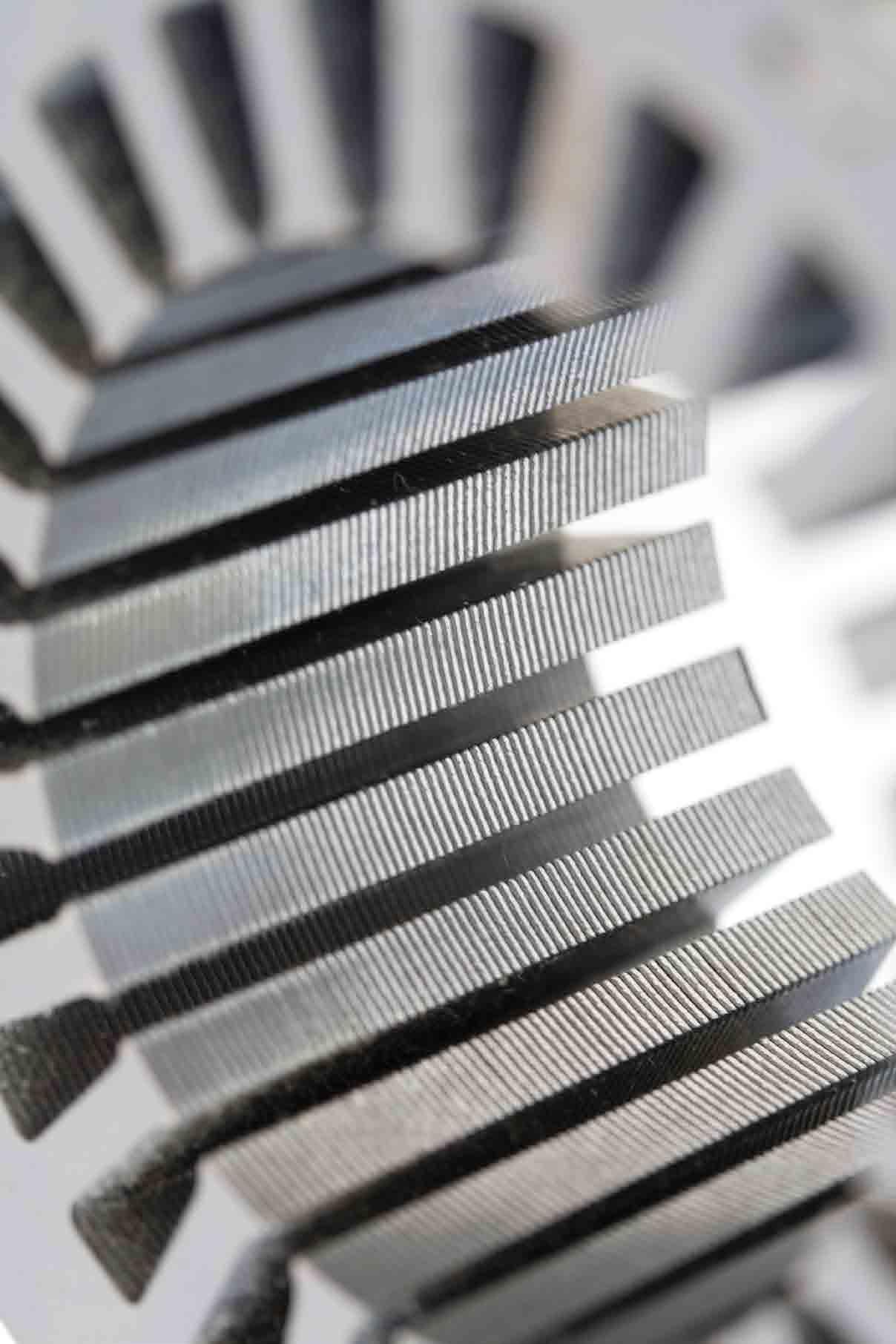

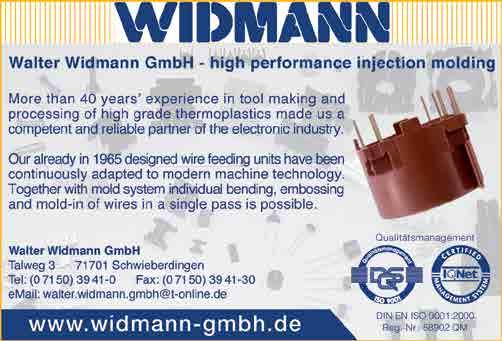
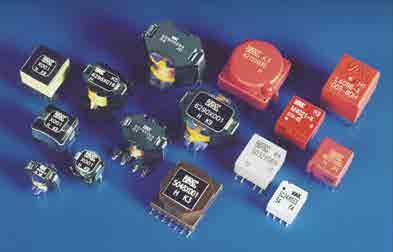
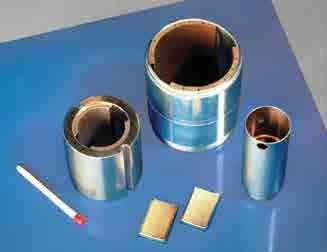
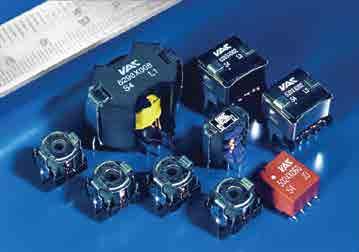
sensors include a very small offset current with negligible temperature drift and barely measurable long-term drift along with exceptional accuracy.
In April 2014, Swiss scientist Andre Boschberg and his Solar Impulse team presented their new aircraft in which they plan to fly around the world in five stages in 2015 using nothing more than solar power. Solar Impulse 2, or SI2, is the successor to the first Solar Impulse craft, HBSIA, which notched up major milestones including solar-powered night flight and crossing the North American continent. Both aircraft are constructed using materials manufactured by Vacuumschmelze, with specific properties that significantly enhance the performance of the highefficiency electrical motors.
VAC’s ULTRAVAC 44 V6 alloy was used in the stator and rotor of the aircraft’s motors. In addition, magnet systems bonded together from small blocks of VACODYM were used. By assembling magnet systems from small individual magnets, eddy current losses in the rotor can be reduced and motor efficiency can be increased to 98 per cent. Forward focus
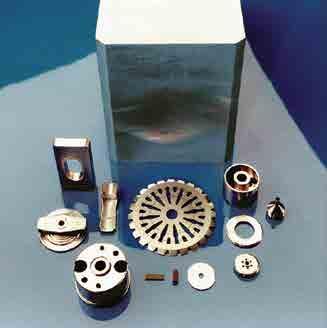
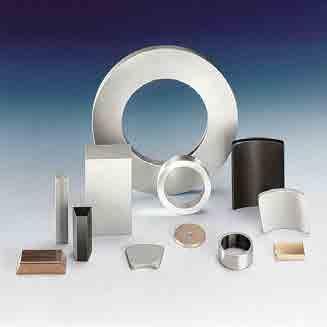
Expansion across the global market sectors it serves will continue to be a priority for Vacuumschmelze. Its production sites in Germany, Malaysia, China and Slovakia are able to draw on the economic benefits of each location and its dedicated R&D team at Hanau gives the company a clear operational definition.
Looking ahead, the company will continue to diversify its product range to support its plans for further global expansion. Participation in trade fairs will also continue to be an important part of its promotional activities. n
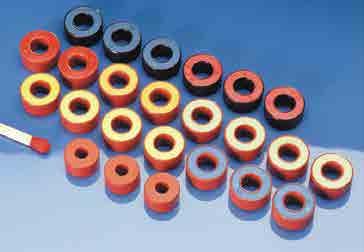

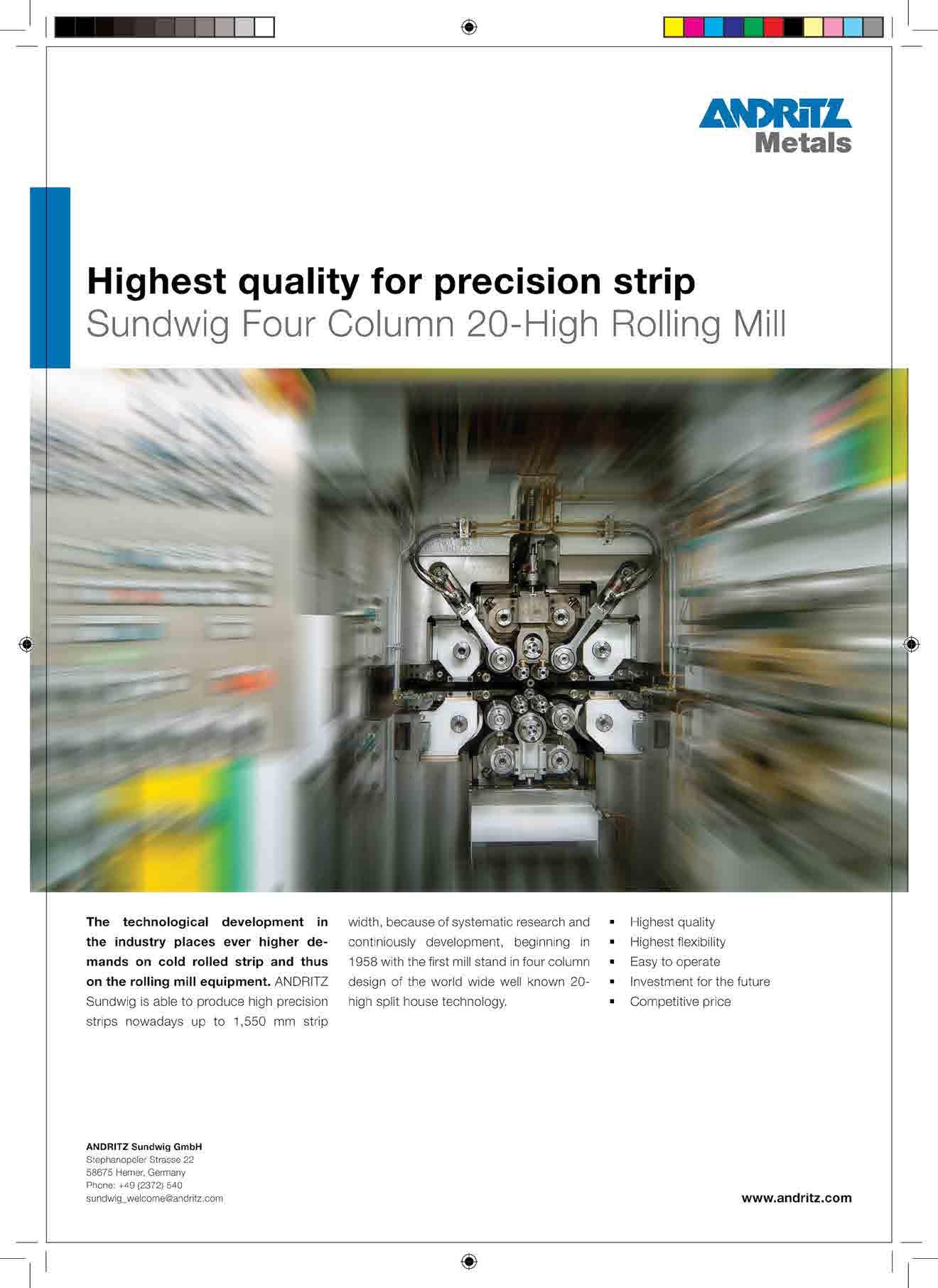