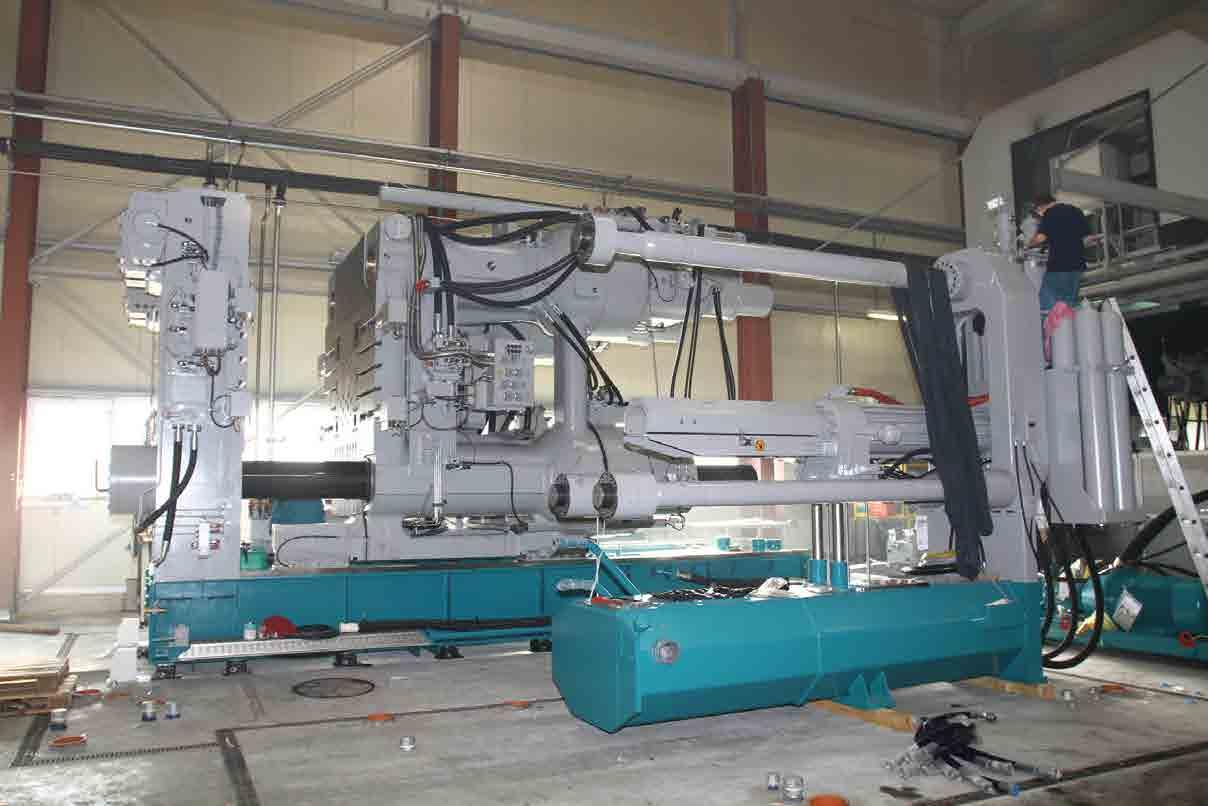
5 minute read
Masterpieces in aluminium and magnesium alloys
DGS, a leading manufacturer of aluminium structures and specialised components for the automotive and allied industries, continues to strengthen its global presence.

Handbrake systems, gear shifters, automotive body parts, mechanical device parts or construction equipment – everywhere you find light metal components with high requirements for dimensional accuracy and wear and stress resistance.
DGS Druckguss Systeme AG ranks among the world leaders in the production of large-sized structural castings made of aluminium. With a total workforce of some 750 employees and three plants in Switzerland, the Czech Republic and China, the company produces die-cast parts made from aluminium, magnesium or zinc.
The company, that was established in 1925 as a trial laboratory for the die-casting department of Bühler AG in Uzwil, Switzerland, has grown into a full system supplier. Its headquarters in St. Gallen house the centralised R&D as well as the aluminium


casting production, including structural castings and magnesium. Automated equipment and processes make DGS the partner of choice in the field of medium and large series production. Its additional offering of FEM calculations and logistics expertise round off the package.
Cutting edge production technology
DGS has extensive know-how and its multifunctional machinery allows it to handle various aluminium and magnesium alloys in the common die-casting processes, even under vacuum. It has vast experience in casting, machining, heat treatment, assembly and coated surfaces, realised by over 50 diecasting machines with locking forces from 200 to 3200 tonnes.
Further production sites are located at Liberec, Czech Republic, for the production of aluminium castings and structural casting; and in Nansha, China – a facility for aluminium castings including structural and magnesium castings and the assembly of handbrake systems.

Expanding in China
A key milestone in the company’s international development was its establishment of a subsidiary in China in 2007, launched to meet the needs of its Far Eastern automotive customers in their local markets.
In order to boost its commitment to China’s vehicle sector, DGS Druckguss Systeme has now built a new die-casting plant with increased capacity in Nansha. One of the first local suppliers to manufacture structural parts for Mercedes-Benz vehicles, the greenfield plant can help automakers produce lightweight vehicles with lower carbon dioxide emissions. There are also plans to establish its own R&D department at the plant in the future.
Anchoring its expansion strategy on the new plant, DGS Druckguss Systeme aims to sustain, even increase, its 30 to 40 per cent annual growth rate in China.
“We established our business here to follow our customers. It is a localisation from Europe. We serve our traditional European customers that require the same product and same core competence in their factories here as they do in Europe,” says CEO Andreas Muller.
DGS Druckguss Systeme also enters into joint ventures with innovative companies, such as Engineered Control Systems, to pioneer new die-casting applications and develop and produce complete systems such as shifter or braking systems.
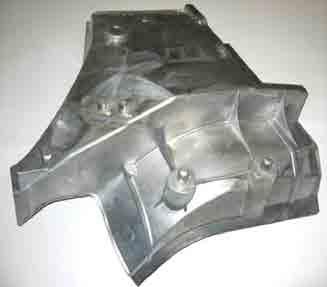
“We are willing to invest in China and transfer our technology and know-how. The longterm perspective is that the plant will be able to develop and grow independently. We see the Chinese plant becoming the second-largest plant in the group within the next few years.”
Die casting with record dimensions
At the end of 2013 DGS AG produced what is probably the largest die casting made in Europe, with outer dimensions of 2050 mm x 1230 mm x 54.5 mm. The part serves as a frame mount for an innovative solar collector made by Hoval, a producer of solar power installations. The new module is equally suited for rooftop as well as for in-roof installation. Despite its dimensions, the finished part weighs just 6400 grams. The frame is designed to resist wind speeds of up to 140 km/h and snow loads of up to 700 kg/ m2. A further requirement is that under all circumstances the tightness of the gasket protecting the solar modules must be ensured in order to prevent water infiltrations.
Compared to a welded construction made from profiles, the new casting solution offers several advantages as a result of the integration of attachments such as edge reinforcements, consoles and stops. This saves the customer complex and costly welding operations. Furthermore, the special aluminium alloy used for the part does not need surface protection.
Ensuring a uniform quality of casting despite the die’s extremely long flow paths of over two metres represented a challenge of its own. Particular attention was paid to avoiding warping owing to the shrinkage of the massive sprue on the one hand and to the ejection and die-cutting on the other hand. Ensuring the exact function of the cutting die when stamping the contour, despite having to cut edges two metres in length, proved to be equally challenging.
Such large frames for photovoltaic panels are a growing business segment for DGS. In addition to its traditional business fields the company is therefore increasingly active in the manufacture of components for the renewable energy sector, as well as for the hybrid and electric vehicle industry. n
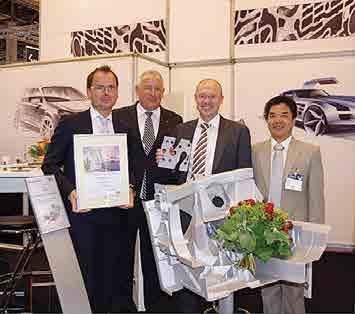
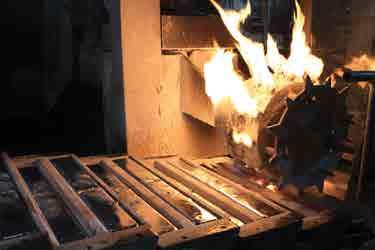

SAKER Ltd is the strong, dynamically-developing company and it has been ranked among the signifi cant processors of the non-ferrous metals and waste metal. The company was founded in the year 1992 and it bases on a tradition and the experiences obtained by longtime activities in an area of treatment with the waste metals. The company has been adapting to the increasing hard requirements of the suppliers and customers by investing in the modern technologies, high-quality technical background and by the team of the highly-qualified experts.
In 2006 was founded the branch factory Alusak – production of aluminium alloys. The fi nal product are Al-ingots destined as enter material for the foundries. Production capacity is 1800 tons/month.
www.saker.cz
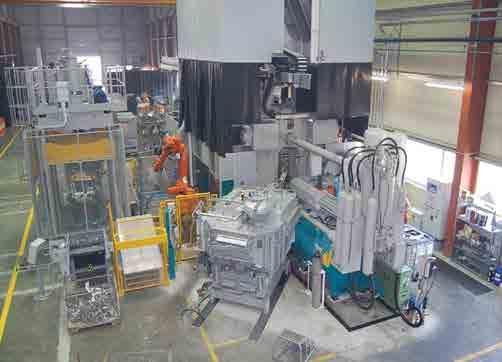
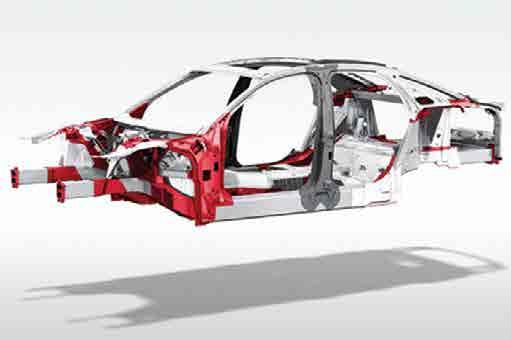