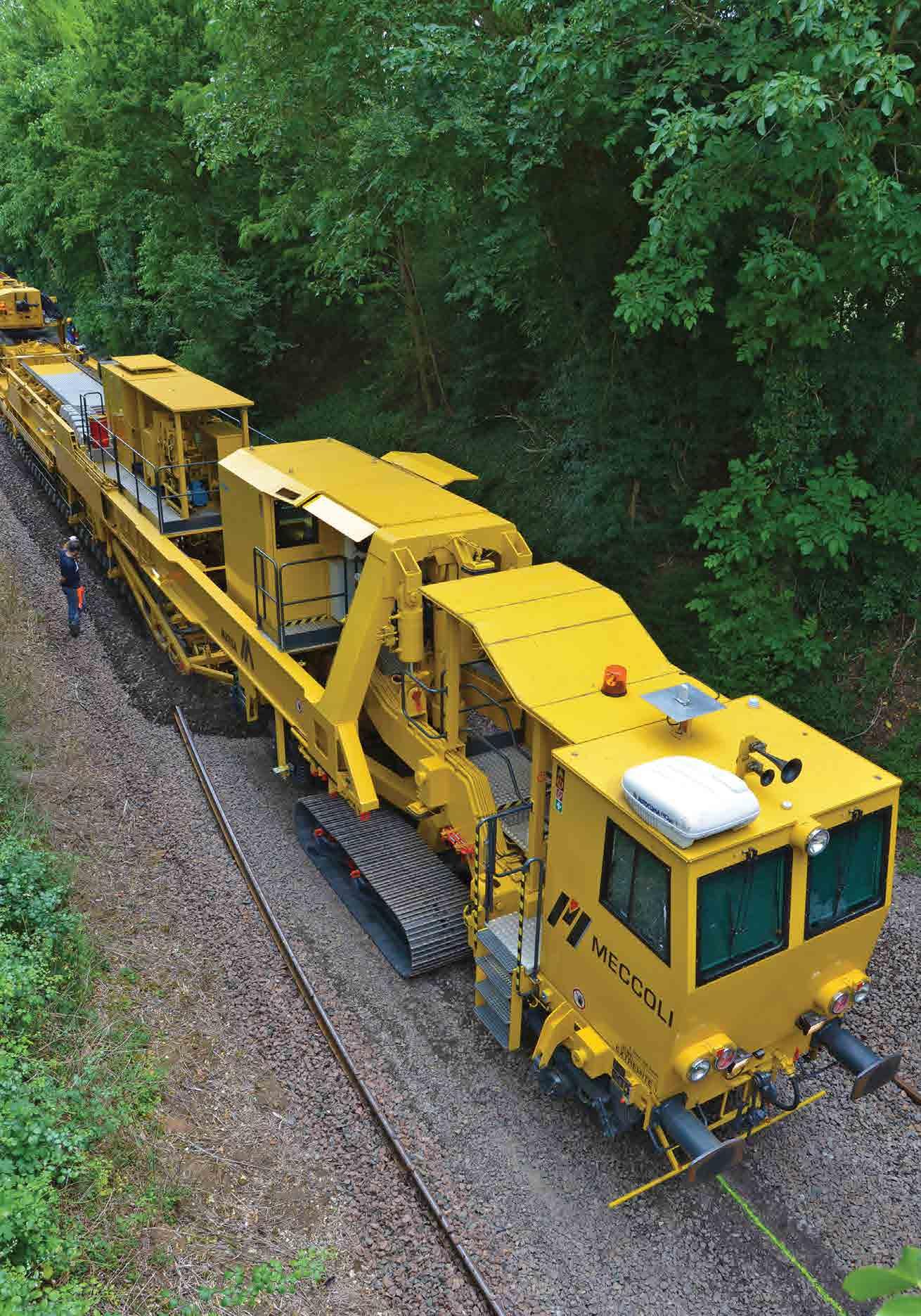
5 minute read
Matisa takes its expertise to InnoTrans Matisa
MATISA TAKES ITS
EXPERTISE TO INNOTRANS
A record number of exhibitors and visitors at InnoTrans provided Swiss railway maintenance machine specialist Matisa with the ideal forum for meeting both existing and potential customers. Felicity Landon reports.
InnoTrans, recognised as the world’s leading business meeting place for technology, is held in Berlin every two years. This well-established, international trade fair for transport technology took place for the tenth time, from September 23–26 2014, and was attended by 138,872 trade visitors from more than 100 countries. Innovations in rail technology were presented by 2758 exhibitors from 55 countries and all available space on the exhibition grounds at Berlin ExpoCenter City was occupied, with displays covering a net area of 102,843 square metres.
Among the exhibitors was Matisa, the Swiss pioneer in track maintenance work mechanisation. Founded in 1945, Matisa was a forerunner in creating the machines that would enable the mechanisation of railway maintenance. The first tamping machine was developed that year and the company today maintains that pioneering spirit, and its passion for innovation and research.
Based in Crissier, near Lausanne, Matisa offers a complete range of machines and services. The quality, reliability and performance of its tampers, ballast regulators, ballast cleaners, track laying and renewal machines, as well as the accuracy of its track measuring vehicles, are recognised worldwide. “The intrinsic quality of our machines is complemented by the high level of service provided by Matisa Customer Service, which supports those machines right from the design stage and throughout their working life,” says Mr Grossniklaus.
Long-term connection with InnoTrans
When InnoTrans first launched, Matisa would attend the biannual event as a visitor – but that has changed in recent years, as sales and marketing director Roger Grossniklaus explains.
“Initially, InnoTrans focused on rolling stock, locomotives, passenger wagons, trams and metro, so it was not really our business,” he says. “However, we went there from the start as visitors. Many of our customers were there, so it was a really useful place to meet them.
“However, the products being promoted at InnoTrans evolved. About eight years ago, the first suppliers in track maintenance activities exhibited, and it became a bigger thing for our industry from then on. We decided to have our first stand there in 2008, because customers had said it was good to see us but it would be very convenient if we had a base where they could come and find us.”
SwissRail had offered Swiss exhibitors the opportunity to share its stand, and Matisa took up the offer, having a small booth with logo and name, at which to welcome customers.
“It was a very small booth at the beginning but the customers kept coming in bigger numbers! So now we have a larger presence at InnoTrans, because customers have asked for it and the focus of the event has expanded.”
So what did Matisa gain at InnoTrans? “Well, I would say that success at an exhibition is difficult to measure in terms of return on investment, but it is certainly of benefit to us to be given the opportunity to interact
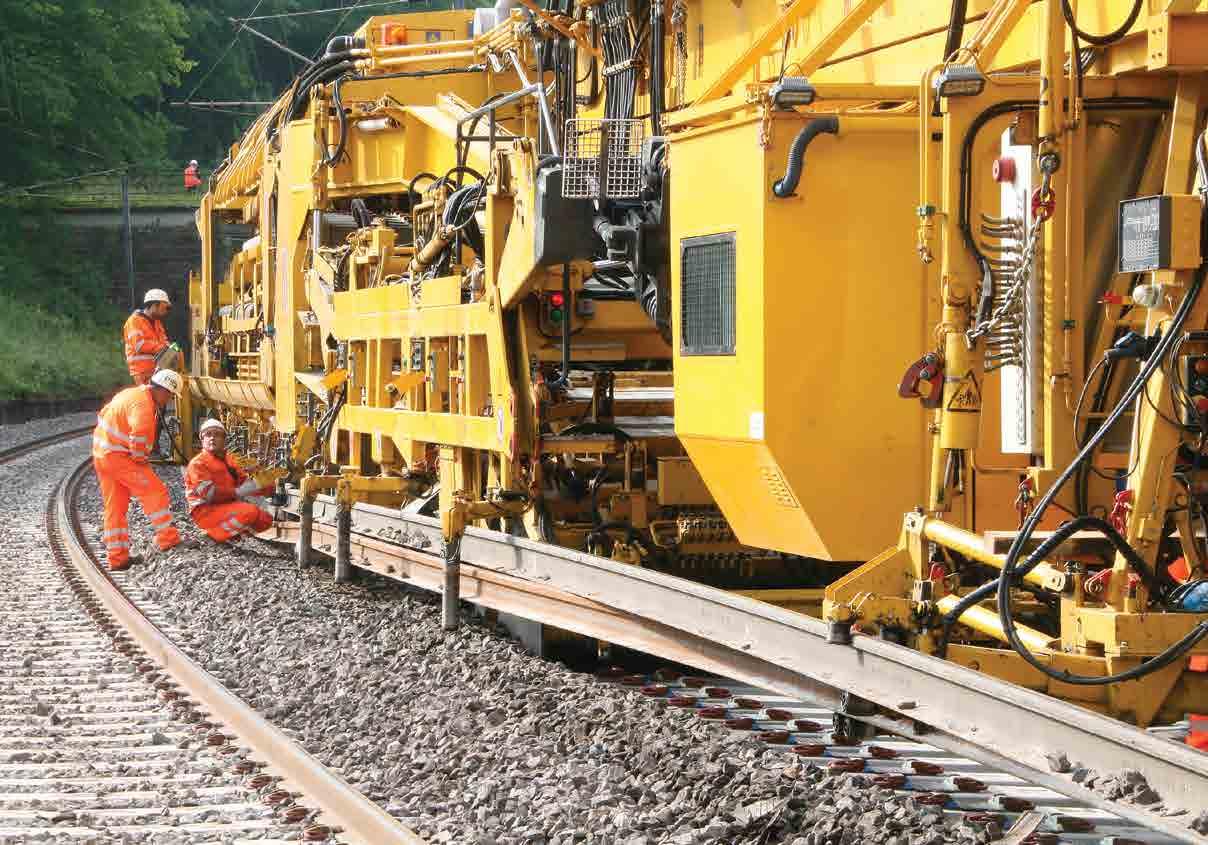
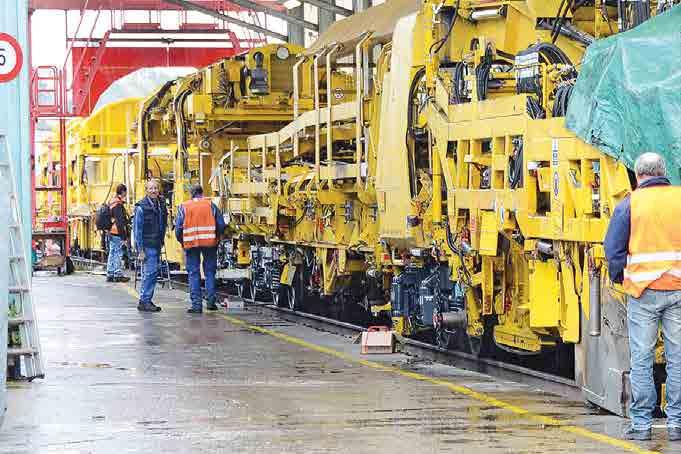
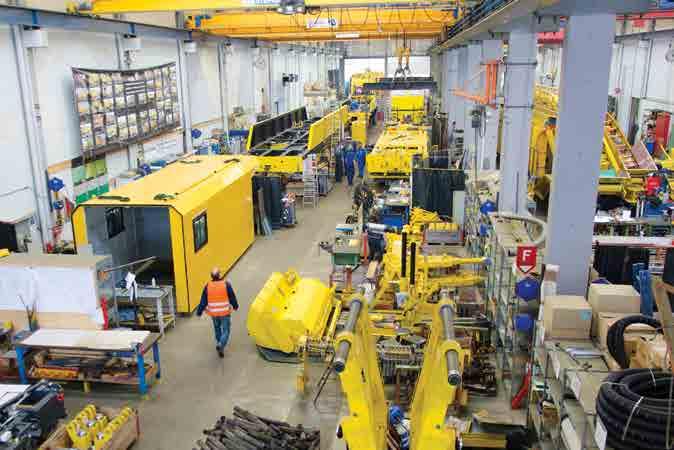

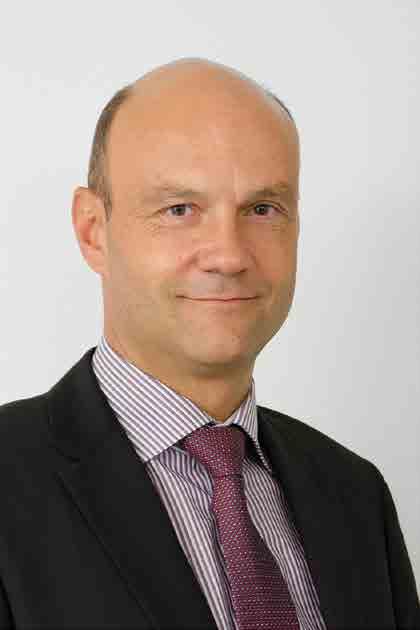
with the industry,” he says. “It is investing to demonstrate to customers that we are still a very large player in the market.
“This year was really busy – they recorded the biggest attendance ever, and we could feel that. There were plenty of customers and a whole range of them. We had visitors who knew us and just called by to say hello. There were others who had read about us and heard about us, and wanted to talk about what we are doing and what sort of equipment we are manufacturing. And there were those who wanted to talk about specifics and discuss the types of machinery they might be looking at in the future.”
Complex machines
The competitive environment in which Matisa operates is complex. First, while it has a range of products and broadly speaking the shape of a machine remains the same, each customer has their own particular way of working, so each machine is adapted and customised to their needs. “So our machines are very specific products,” explains Mr Grossniklaus. “A customer’s decision to place an order isn’t only from the price competition point of view, it’s also from the feasibility and commercial point of view of their operations.
“In addition, we have a range of products and our competition has a range of products which partly overlaps. Therefore, in some areas we may be competing against each other but in others they may have additional products or we may have additional products that they don’t have.”
Matisa recently delivered a B 45 UE universal tamping machine to the Swiss company Scheuchzer. To provide optimum user-friendliness, the machine is fitted with the latest technologies developed by Matisa, in particular a ‘human-machine interface’ using a touch screen and joystick controls for the tamping operators.
The machine is equipped with tools for managing the ballast, notably when renewing the track; it has a front plough and two ballast-removing ploughs. The trailer is fitted with central and lateral ploughs as well as a brush with a vertical conveyor and a hopper. The modular brush shaft can realise three different brushing profiles – in particular a deep brushing, to meet the latest Swiss Railways requirements. The machine is able to tamp tracks equipped with Y sleepers due to the longitudinal mobility of all tamping units and can work on steep slopes, thanks to three motorised axles. It is driven by a C15 Caterpillar engine with a power of 433kW – its low engine rotation speed significantly reduces fuel consumption and noise.
Among recent orders, Matisa is to supply two tamping machines to the London Underground. Due to be delivered in summer 2015, the machines will be specially adapted to allow for gauge and tracking laying differences compared to conventional overground networks.
Meanwhile, in what is a ‘small industry’ in which everyone knows everybody else, Matisa continues to focus on further innovations and on delivering best-in-class products and service in the months ahead. n
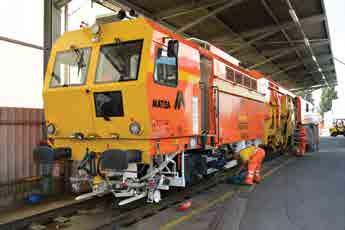

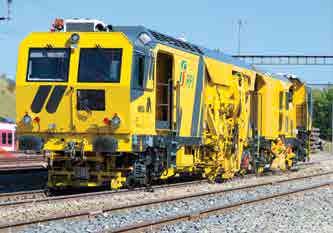