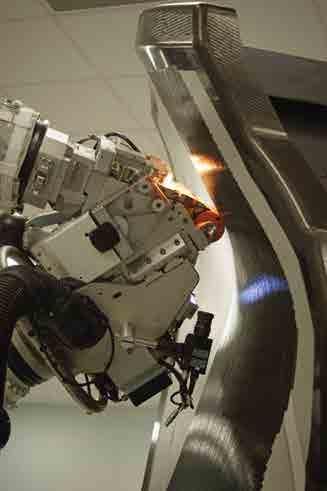
3 minute read
Technology spotlight Advances in technology
NEWS
TECHNOLOGYSPOTLIGHT
Advances in technology across industry
ThyssenKrupp develops world’s first rope-free elevator system
The era of the rope-dependent elevator is now over, 160 years after its invention. ThyssenKrupp places linear motors in elevator cabins, transforming conventional elevator transportation in vertical metro systems. MULTI elevator technology increases transport capacities and efficiency while reducing the elevator footprint and peak loads from the power supply in buildings. Several cabins in the same shaft moving vertically and horizontally will permit buildings to adopt different heights, shapes, and purposes. The first MULTI unit will be in tests by 2016.
Now, the long-pursued dream of operating multiple cabins in the same elevator shaft is made possible by applying the linear motor technology of the magnetic levitation train Transrapid to the elevator industry. MULTI will transform how people move inside buildings.
In a manner similar to a metro system operation, the MULTI design can incorporate various self-propelled elevator cabins per shaft running in a loop, increasing the shaft transport capacity by up to 50% and making it possible to reduce the elevator footprint in buildings by as much as 50%. Using no cables at all, a multi-level brake system and inductive power transfers from shaft to cabin, MULTI requires smaller shafts than conventional elevators, and can increase a building’s usable area by up to 25%.
The significant extra space available is only one of MULTI’s advantages. Although the ideal building height for MULTI installations starts at 300 metres, this system is not constrained by a building’s height. Building design will no longer be limited by the height or vertical alignment of elevator shafts, opening hitherto unimagined possibilities for architects and building developers. Visit: www.thyssenkrupp.com
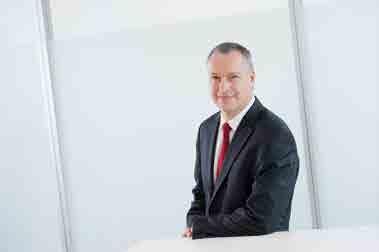
Lockheed Martin pursuing compact nuclear fusion reactor concept
The Lockheed Martin Skunk Works® team is working on a new compact fusion reactor (CFR) that can be developed and deployed in as little as ten years. Currently, there are several patents pending that cover their approach.
While fusion itself is not new, the Skunk Works has built on more than 60 years of fusion research and investment to develop an approach that offers a significant reduction in size compared to mainstream efforts.
“Our compact fusion concept combines several alternative magnetic confinement approaches, taking the best parts of each, and offers a 90% size reduction over previous concepts,” said Tom McGuire, compact fusion lead for the Skunk Works’ Revolutionary Technology Programs. “The smaller size will allow us to design, build and test the CFR in less than a year.”
After completing several of these designbuild-test cycles, the team anticipates being able to produce a prototype in five years. As they gain confidence and progress technically with each experiment, they will also be searching for partners to help further the technology. Visit: www.lockheedmartin.com
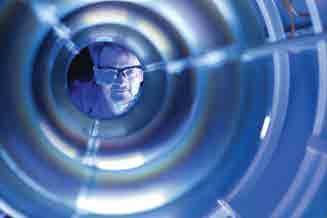
GKN Aerospace leads new research to progress wing technologies
GKN Aerospace is to lead a challenging 13-partner, 27-month, £30m future wing research programme, backed by the UK’s Aerospace Technology Institute (ATI). The VIEWS (Validation and Integration of Manufacturing Enablers for Future Wing Structures) programme will bring promising wing design, manufacture and assembly technologies near to market readiness, whilst selecting some novel technologies for further development.
VIEWS will progress technologies that have emerged from the recently completed STeM (Structures Technology Maturity) research programme. Also led by GKN Aerospace, STeM has identified processes that could reduce by 20% the cost of manufacture and assembly of a typical composite box structure.
The work of the new VIEWS programme will span manufacturing and assembly processes including: identifying and defining future manufacturing requirements to produce novel wing architectures; assessing tools that will improve product and process design and enhance the flow of production; progressing a variety of emerging composite and metallic manufacturing and assembly technologies and processes; and studying innovative inspection and repair tools. In the final stages, the partner companies will produce test demonstrators to validate the maturity of key technologies.
The VIEWS team includes four industrial partners: GKN Aerospace, Bombardier Aerospace, Spirit AeroSystems, and GE Aviation; five of the UK’s high value manufacturing catapult centres: the National Composites Centre, the Manufacturing Technology Centre, the Advanced Manufacturing Research Centre (the University of Sheffield),the Warwick Manufacturing Group (the University of Warwick) and the Advanced Forming Research Centre (the University of Strathclyde); and the Universities of Nottingham, Bath, Bristol and Sheffield Hallam. Visit: www.gkn.com