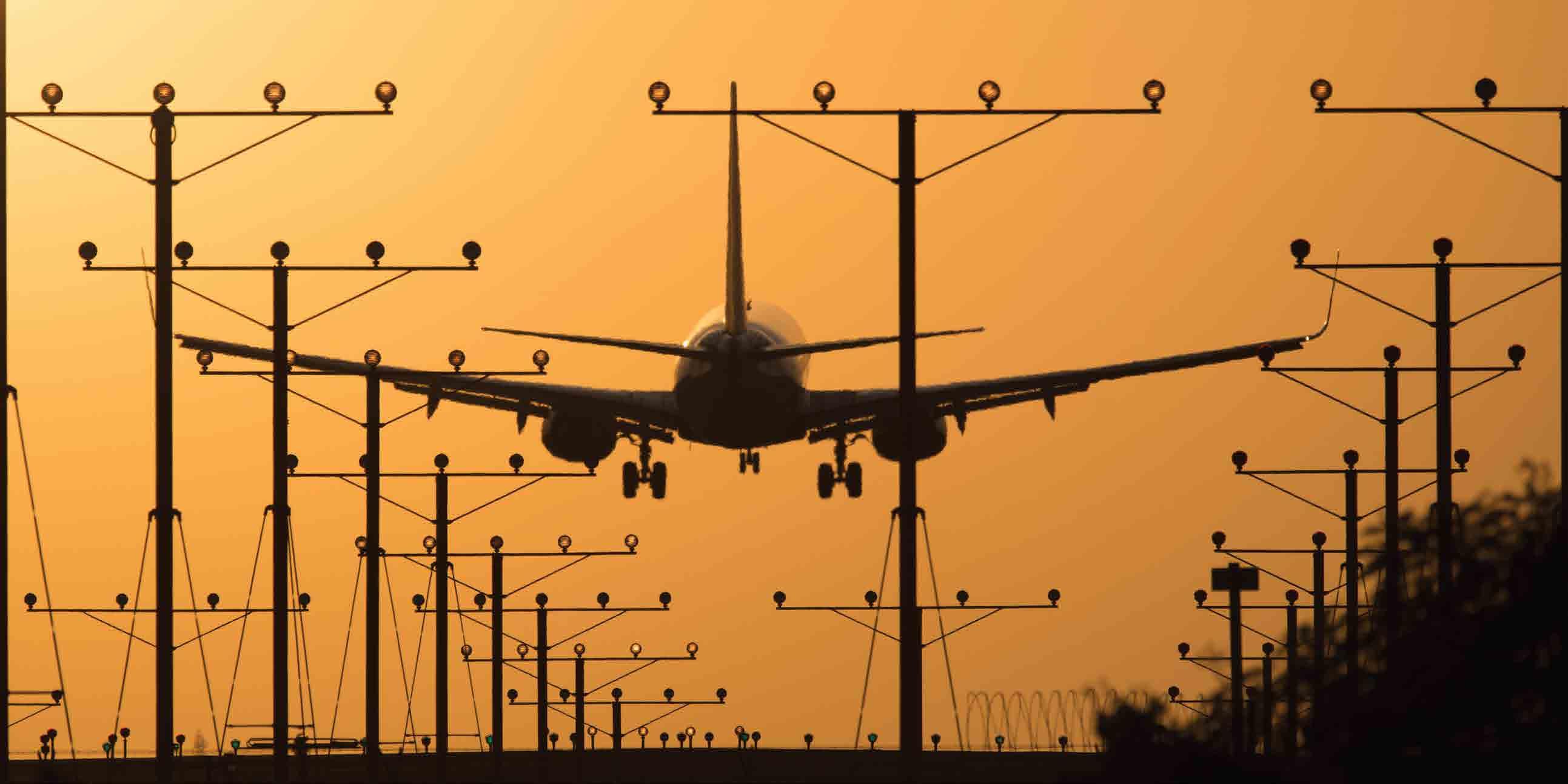
14 minute read
At the leading edge Asco
AT THE LEADING EDGE
Last October, in a speech on inward investment into the USA, President Barack Obama referred to the Belgian aerospace company Asco as offering an excellent example of the kind of high technology manufacturing investment that was helping to revitalise the US economy. He was thinking specifically of Asco’s start-up of production at a new facility in Stillwater, Oklahoma, just over a year after the acquisition of the site.
“Asco currently realises some 40 per cent of its turnover in North and South America so the US was the obvious choice for a new production site to better serve our aircraft manufacturing customers in both regions and to accelerate our growth in these dynamic markets,” explains Asco President and CEO Christian Boas. “We settled on the Oklahoma location because it is geographically central in the USA and is home to a cluster of aerospace companies. Stillwater itself is the site of the Oklahoma State University, which has an excellent reputation in aerospace and R&T, and to the Meridian Technology Centre, which offers excellent facilities for training and development.
“We bought a 66,000m2 building there, formerly operated by Mercury Marine, in 2012 and the first $100m phase of our investment will be completed early next year. We are setting up a state-of-the-art production facility that will incorporate processes such as machining, heat and surface treatment and assembly in a vertically integrated plant that will offer our American customers a one-stop-shop. We have been supplying major customers such as Boeing, Bombardier and Embraer from our plants in Belgium, Germany and Vancouver for many years but the Oklahoma site will not only significantly increase our production capacity but will also reduce lead times and inventory and increase our flexibility in responding to the rapidly growing aircraft production rates of the major plane makers.”
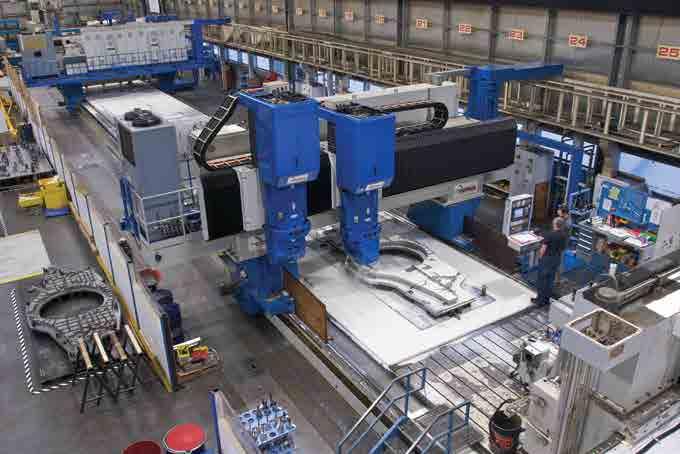
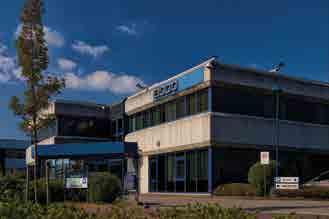
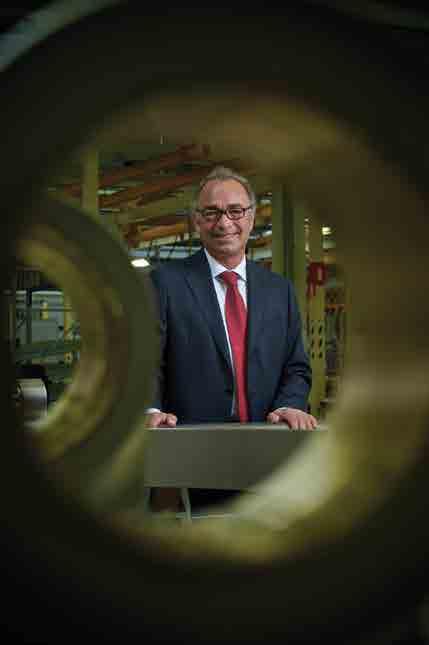
Celebrating its 60th anniversary this year, Asco is a world leader in the design and manufacture of wing components that allow jet airliners to take off and land safely. Peter Mercer went to its headquarters outside Brussels to meet CEO Christian Boas.
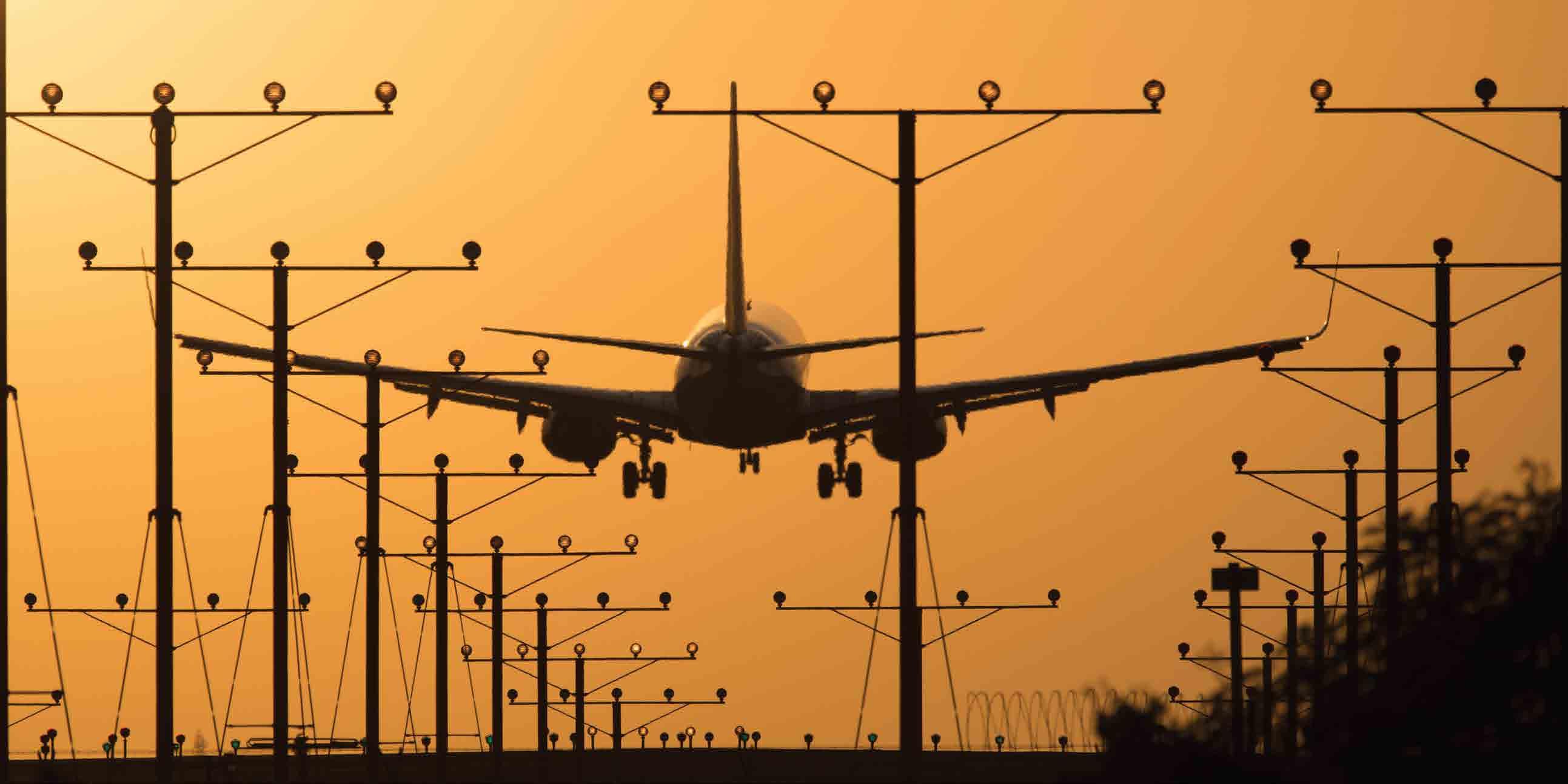
60 years of engineering excellence
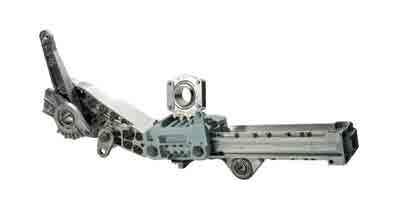
Asco is known throughout the aerospace industry as a world-class designer, developer and manufacturer of high technology operating and support mechanisms for the slats and flaps on aircraft wings as well as other complex assemblies and structural components. This year it celebrates its 60th anniversary, having been started in Brussels in 1954 by Emiel Boas as a trading house for car spares. It is still a family controlled company; today’s CEO Christian Boas is the grandson of the founder. By the mid 1960s Asco was renovating mechanical parts for the military vehicles of the Belgian army and by the 1970s it was supplying Alvis of the UK with suspension, gearbox and turret components for the Scorpion and Scimitar light tanks. It went on to establish a leading position in the armoured vehicle industry, producing suspension components for British, German and US main battle tanks as well as complete aluminium shells for troop transport vehicles.
Asco’s break into the aircraft industry came in 1979 when it became a member of the Belairbus management company that was set up by the Belgian government to help its aeronautical industry to participate in the European Airbus programme that had begun in the early 70s with the launch of the A300. Asco was approached by the Belgian company Sonaco, which was involved in airframe work, to supply slat tracks for the wings of the new Airbus 310, the 200+ seat aircraft that went on to mark up more than 250 deliveries.
Slat tracks allow the slats on the leading edge of aircraft wings to be extended and retracted on take-off and landing, Slats enable the wing to operate at a higher angle of attack, increasing lift and making possible shorter take-off and landing distances.
From the beginning Asco realised that supplying the aircraft industry with even the smallest part was a business unlike any other and it now needed more than ever to stay true to its motto ‘Do it right from the start’. It had only a weekend to draft its offer for the A310 slat track contract and even when it had acquired the latest machine tools from Germany it took nine months between receiving the raw material and delivering the finished part. Today things happen a bit faster – Asco can provide a set of parts for an Airbus A330 in just five days. And for a set for the massive A380, it must take into account a total of 2500 components.
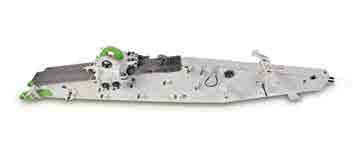

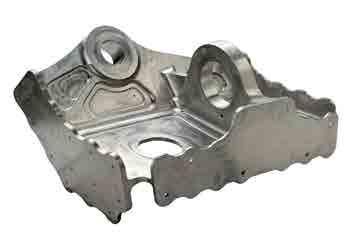
New needs need a new approach.
Innovation is about more than simply working with new composites and new alloys. What is important here is the approach taken by the aerospace industry, and the technologically expedient and cost-effective machining solutions being developed. Product ideas must lead to competitive series-production solutions. It is only in this way that machining can contribute towards higher profitability and, consequently, competitiveness. And this is where we come in! We offer the most comprehensive range of metal cutting tools in the world for metal and composite materials, and for many years, we have been developing innovative and flexible solutions for machining in aerospace technology. Even though new composites and alloys are becoming increasingly difficult to machine, our boring, milling, turning and threading solutions are setting standards.
www.walter-tools.com
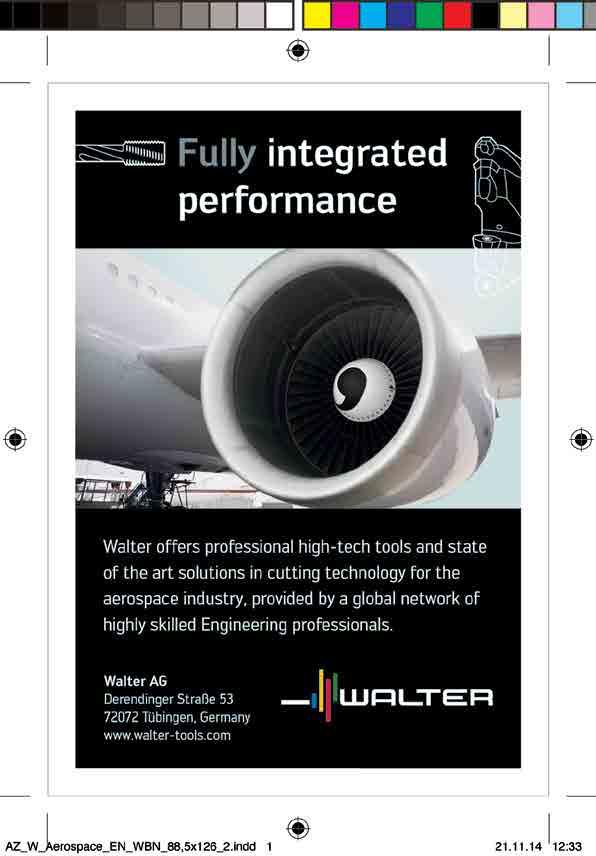
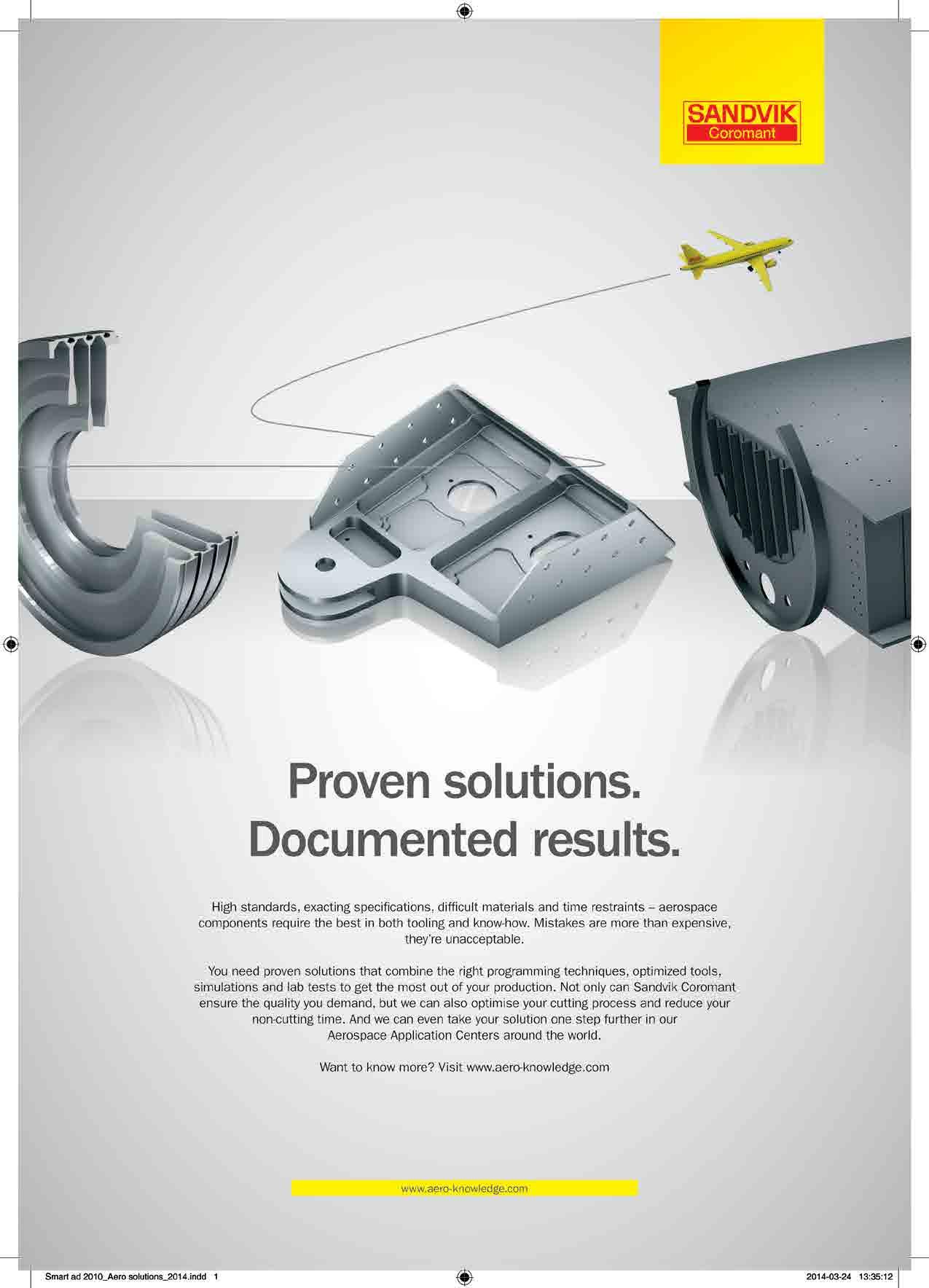
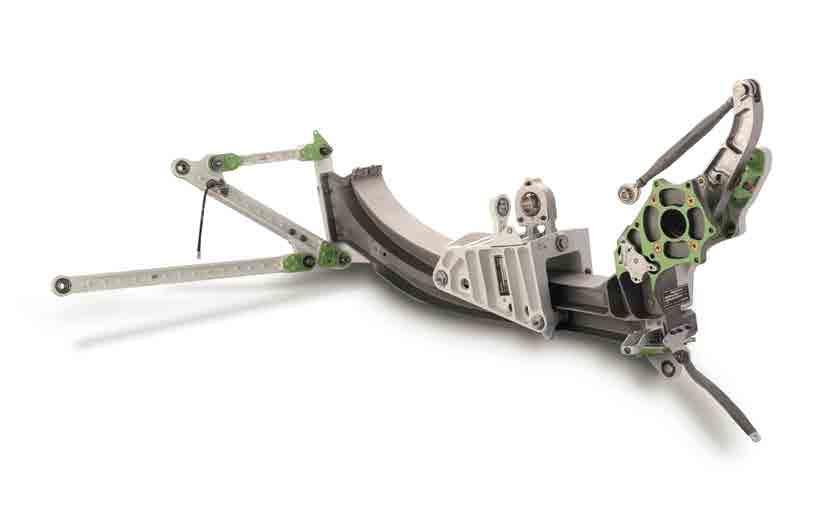

Take off
The A310 was produced in relatively small volumes and the real transformation of Asco into an aerospace company came with the launch of the A320 in the late 1980s. For this aircraft, which was equipped with electrical rather than hydraulic flight controls, Asco was responsible for the complete manufacture of the parts – nickel based steel slat rails and a rack and pinion system – including surface treatment and destructive and non-destructive testing. It also manufactured the torque tubes for the carbon brakes of the landing gear. This programme turned out to be of a completely different scale – up to now around 10,000 A320s have gone through Airbus’ order book and the production rate is scheduled to reach 46 aircraft a month by 2016.
“Since the A320 launch, Asco has been involved in all the Airbus programmes, including the A330, A340, A380 and now the A350,” says Christian Boas. “In fact since the mid 1990s we have supplied parts for every western commercial aircraft model in the 50 seat plus range. We quickly established ourselves as the world leader in leading edge slat mechanisms but we also recognised the need to diversify and broaden our capabilities. So for the Airbus A380, for example, we manufacture and supply carriages for the trailing edge flaps, pylon brackets for the outer engines , the main strut of the nose landing gear as well as the leading edge slat tracks and the droop nose actuators.” The droop nose on the A380 does not involve the actual nose of the aircraft pivoting downwards on landing and take-off, as in the Concorde, but rather the downward rotation of the entire leading edge of the wing between the fuselage and the inboard engines.
In 1995 Asco succeeded in diversifying in another sense when it signed its first contract with Boeing to supply wing components for the new generation 737-600. These included slat tracks, trailing edge flap tracks and flap carriages. The company went to on to supply parts for all succeeding Boeing aircraft, including slat track assemblies and engine fittings from its Vancouver plant and brake rods for the main landing gear for the 777 and, for the 747-8, the torque boxes which attach the engines to the wings. Asco is also playing a major part in the 787 Dreamliner programme, supplying slat tracks and the crown and lower frames of the fuselage section that supports the vertical fin.
In the regional aircraft market Asco supplies both Bombardier – with slat tracks and flap support systems for the C Series – and Brazil’s Embraer – with ribs for the wing main box of the E-Jet.
Production on two continents
Asco’s headquarters and its Belgian production factory is at Zaventem, near Brussels airport, a site that has been home to the company since 1973. Today this facility specialises in the design, development and production of complex prismatic components in titanium and steel up to 2.5 metres in length. Recent investments at Zaventem have included two completely new production facilities equipped with high technology and high performance machining centres and machines for heat and surface treatment. These new facilities represent an expansion of the site from 43,000m2 to 50,000m2 .
Asco Deutschland was acquired in 2003; it was formerly a German family company that had been providing parts, including engine pylons and landing gear boxes, to leading companies in the German aeronautical sector since 1962. Today the site at Gedern, near Frankfurt, is Asco’s centre of excellence for the high speed cutting of large and complex aluminium structural parts and extruded profiles.
Asco’s Canadian plant specialises in very large complex high speed aluminium and complex hard metal machining and assembly. The facility, in Delta, British Columbia, was acquired in 2003 from a former Boeing supplier just as Asco won the manufacturing contract for the Boeing 777 slat tracks. Today the plant extends to more than 10,200 m2 and has more than 170 employees.
“Our Canadian plant established Asco as a key direct supplier to Boeing, complementing our long-standing relationship with Airbus in Europe,” explains Mr Boas. “It is only a short distance away from the main Boeing Everett assembly facility in Seattle. This closeness to the customer is ever more important as the production rate of commercial aircraft is rising so quickly these days. We already deliver components from Delta to the Boeing plant twice a day and as Boeing is now increasing production of the new 737 to more than 50 aircraft a month, we need to keep pace.”
Asco Canada also produces complex titanium and aluminium components for Lockheed Martin’s F35 Joint Strike Fighter.
Even closer to the Boeing plant in Seattle – in fact just minutes away – is the Asco USA Design Centre, which can deliver rapid

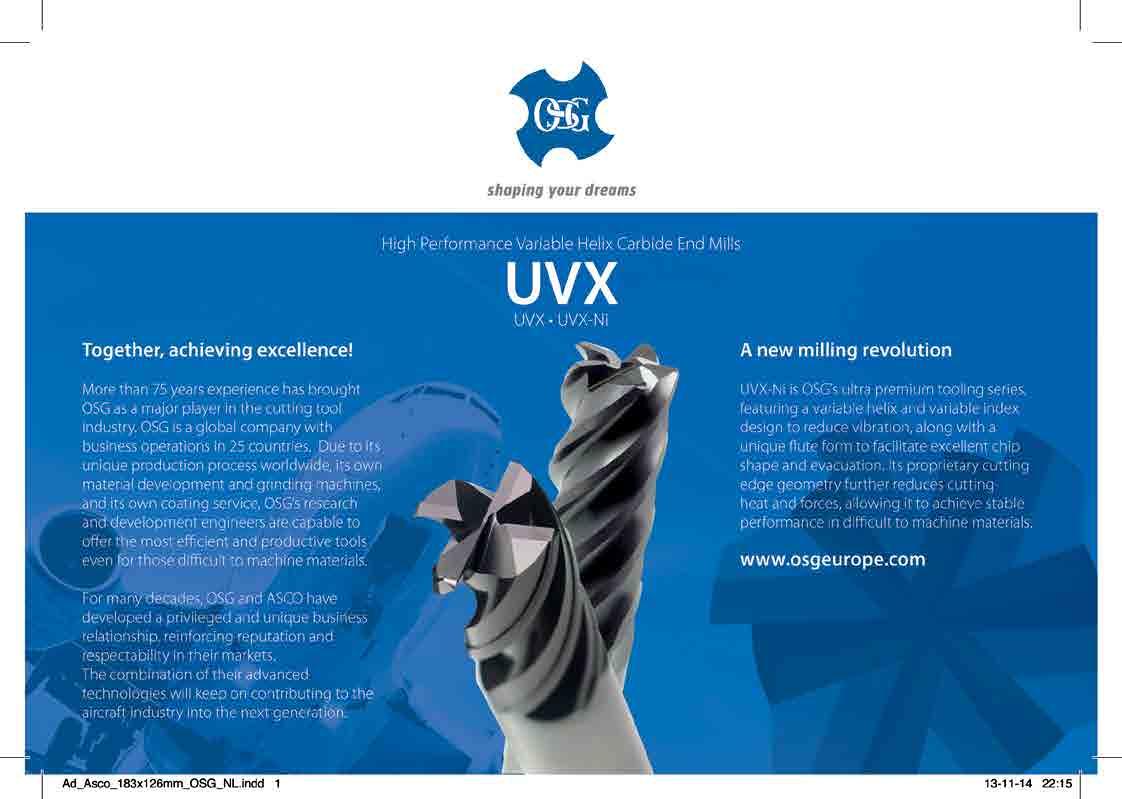

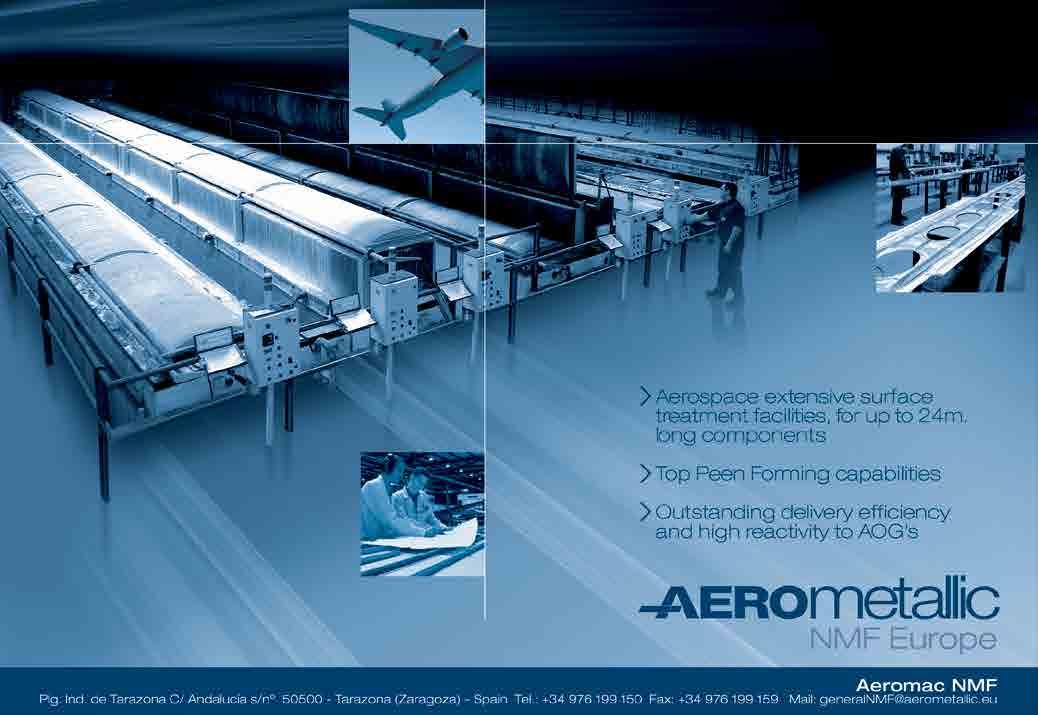
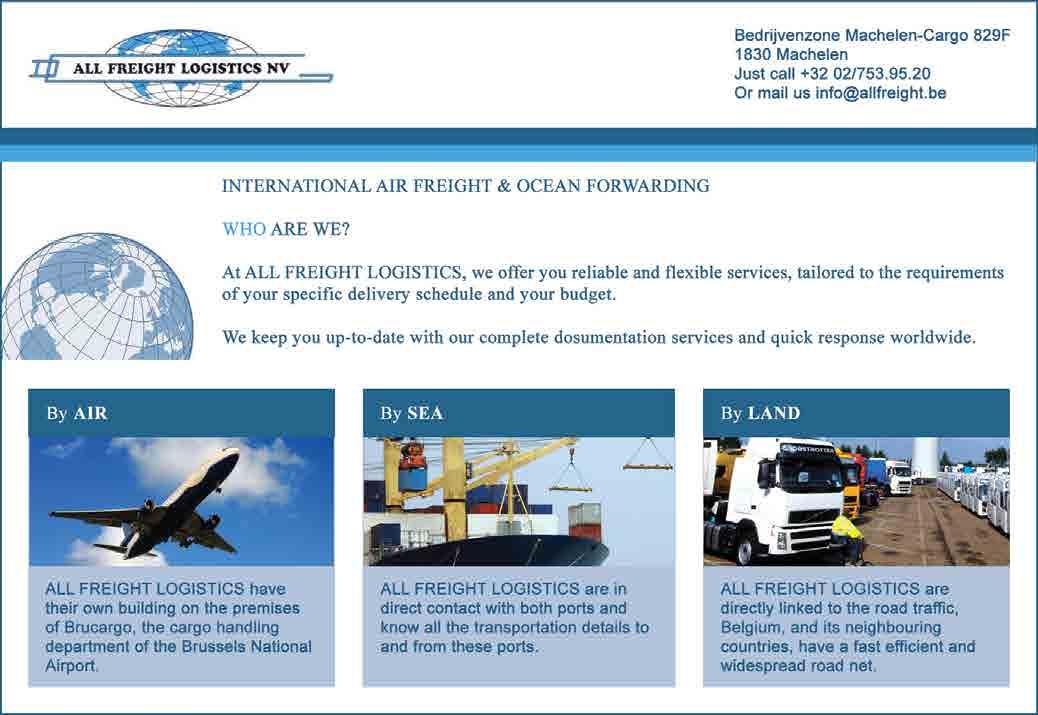
MAKINO: Your first-choice supplier
Makino, a Japanese world leader for advanced technology machine tools, is deeply involved in the aerospace industry with specific equipment dedicated to 5-axis machining of light alloy parts but also complex hard materials such as titanium, the use of which is increasing for the latest aircraft generation. For titanium machining Makino has developed innovative technologies that enable significant increases in cycle time and tool life performances compared to standard machines.
The 5-axis T series, available in three sizes and specifically designed for titanium machining, includes besides their high rigid design the latest Makino technologies such as active dampening, high-flow, high-pressure through-spindle coolant, and Makino’s tried-and-tested Thermal Stabilizer. The latest model (T1) has been designed specifically as multi-purpose machine tool, capable of machining titanium and other aerospace alloys.
One of world leaders for landing gear components manufacture, ASCO has joined the list of Makino customers for titanium machining by investing in T2 machines for flexible manufacturing systems (FMS) at its Belgium plant.

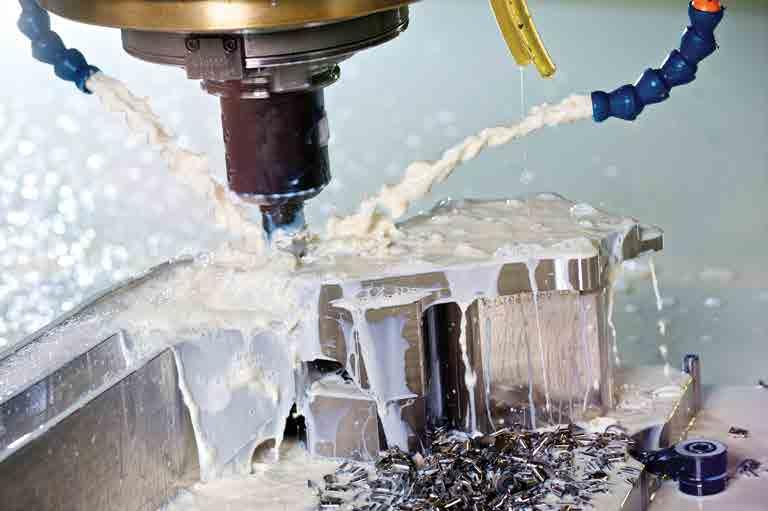

engineering responses both to Asco’s customers and to its local suppliers. There are also Asco offices in Brazil and France.
Developing products, optimising process

The accelerating growth in commercial aircraft production all over the world means that Asco has continually to invest in upgrading capacity, improving productivity and increasing efficiency as well as adapting to the fast-changing technology of aircraft structures. In fact, the world fleet of passenger aircraft is set to double over the next 20 years, which means there will be a demand for more than 36,000 new aircraft in that time frame. At the same time there is pressure to reduce the environmental impact of air travel and to reduce operating costs. That means lighter aircraft that burn less fuel, which means more use of lightweight materials such as composites and constant improvements in aerodynamic efficiency.
“There are essentially two aspects to our future development programmes – working on new products and new materials and improving processes,” says Christian Boas. “Our product-related R&D is currently focused on areas such as new laminar wing profiles, composite technology for structural parts and the use of carbon fibre reinforced plastics. We are participating in the European Union Clean Sky programme to promote greener aviation with, for example, high lift devices for laminar wings. These are leading edge flaps that disappear completely into the lower part of the wing when retracted, so the upper wing surface is clean and smooth with no steps or gaps to disturb the laminar airflow over it. This significantly enhances aerodynamic efficiency and lowers fuel consumption. We are also looking at new composite leading edge devices and new actuation and support mechanisms. There are always new problems to solve – composites, for example, are more and more in demand for long-range aircraft but composites and aluminium don’t work well together and you have to use titanium as an interface.”
To meet the constantly increasing demand for its products Asco also has to continually upgrade its processes – it always needs faster and more reliable machines, more efficient supply chains, greater flexibility and lower costs. In its plants it must optimise the interfaces between machines, equipment and the buildings themselves while within the plants it operates flexible manufacturing systems which enable several machines to be managed by a cell controller unit; surface treatment at its plants is now automated and sand blasting robotised. It is all, as Christian Boas says, to make the whole process ‘leaner, cleaner and meaner’.
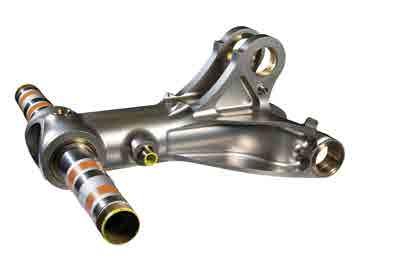
Constantly diversifying
Even though it has full order books for the next five years Asco is constantly looking to diversify and expand its capabilities, its product range and its key markets. “Clearly the core of our business will continue to be with Airbus and Boeing and we are fully engaged in the Airbus A350 XWB programme, for which we are the single source for the slat tracks and hinge arm mechanisms for all versions; we also supply main landing gear titanium attachments,” says Christian Boas. “But we also have long-term contracts to supply leading edge components for Bombardier’s C Series and for Embraer’s E2 and its KC390 military transport.”
The Embraer transport is not the only military project that Asco is involved in. In Europe it is jointly responsible for the trailing edge tracks and components for the huge main landing gear of the Airbus A400M, the large military transport aircraft that has been ordered by seven European air forces. Asco Canada is also producing important titanium components for the Lockheed Martin F-35 Joint Strike Fighter, including a key bulkhead which joins the airframe and the wings.
“Of course, governments have significantly reduced spending on their air forces in recent years but we still see opportunities for the future,” says Mr Boas. “The Belgian air force, for example, is looking for an aircraft to replace its F 16s and there could well be a chance for Asco to benefit from the off-set agreements that the choice of any of the candidates would bring to the Belgian aerospace industry. Contracts for military aircraft ensure a stable, longterm flow of business as well as access to advanced technologies that can often then be used in civil programmes.
“And staying at the cutting edge of aerospace technology is, of course, the key to the success of Asco’s next 60 years.” n