
6 minute read
Mission accomplished JEB
MISSION ACCOMPLISHED
JEB Engineering Design Ltd is part of the international JEB Group and a global technology leader in the development and manufacture of complex, high quality machine tools, component assemblies and individual components. Philip Yorke talked to the production manager, John Talbot, about its growing portfolio of products and how it accomplished a major R&D breakthrough by developing the world’s most advanced non-lethal training ammunition.
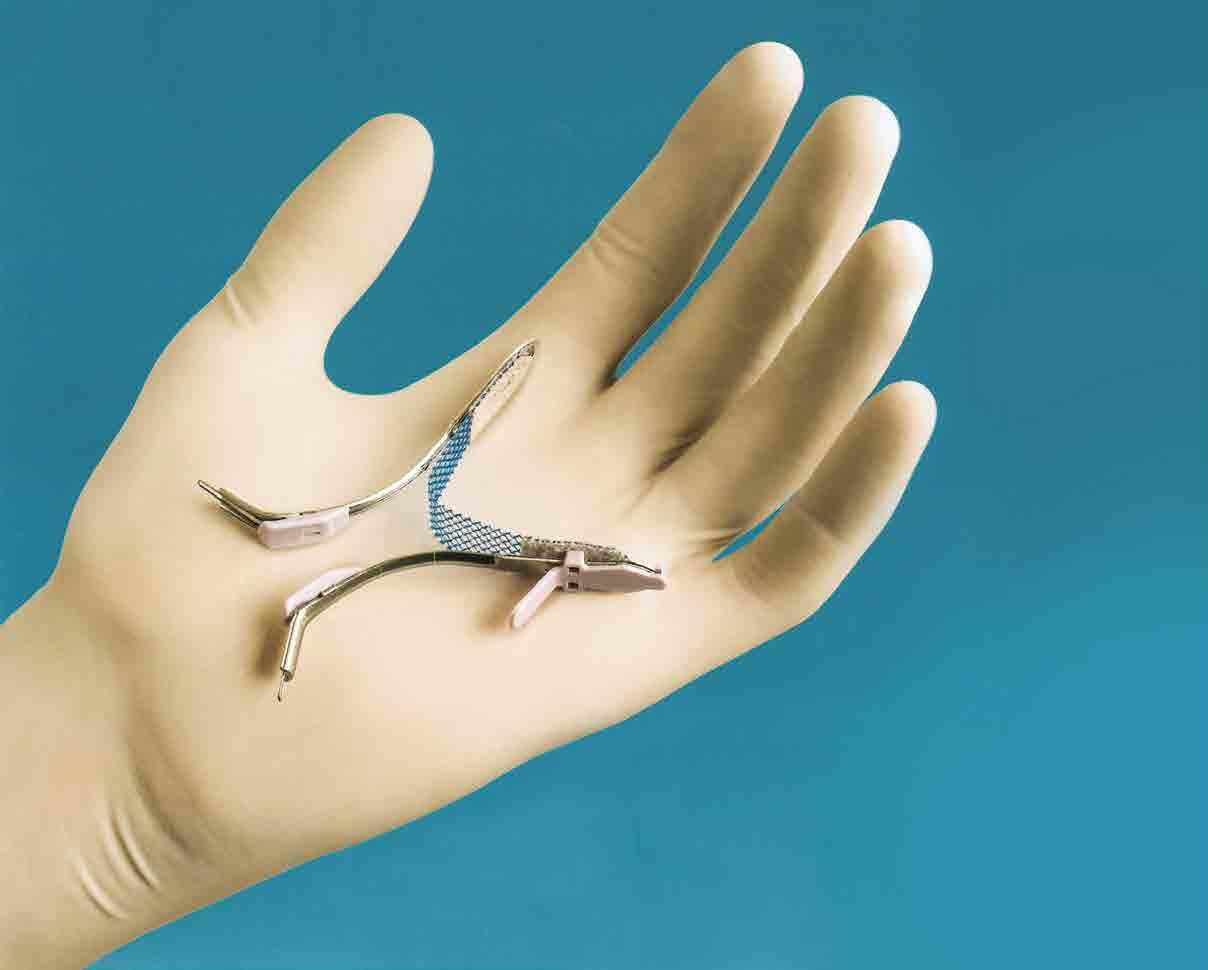
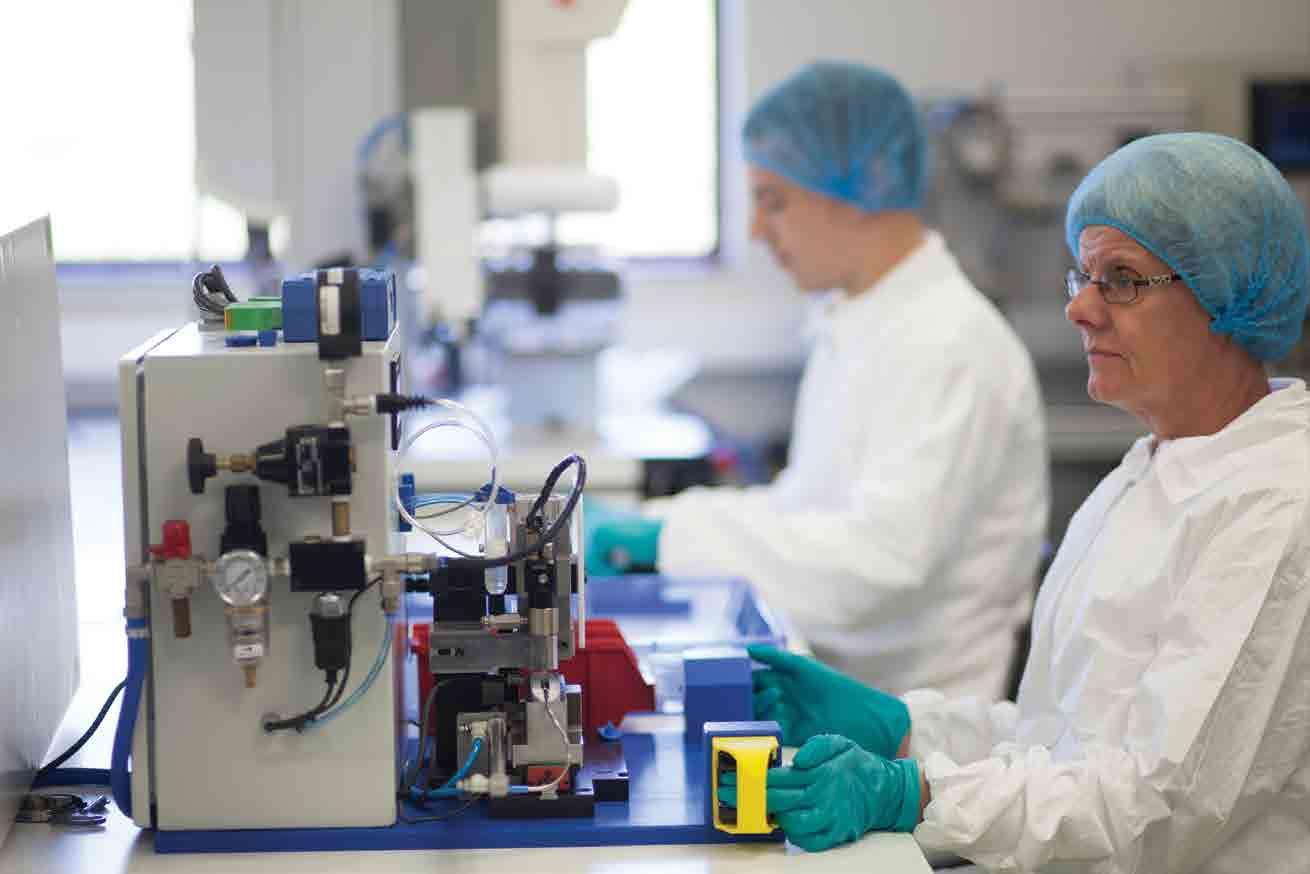
From the outset JEB has benefited from its commitment to quality, innovation and the continuous drive of its management team. The company was founded in rural Suffolk, in 1972 by John James, Eric Bone and Barry Littlewood, whose combined initials form the company logo. Following consistent growth through the years, the company has established itself as a global market supplier of high quality machine tools, metal stamped components and assemblies for the Electronics, Medical and Munitions industries. JEB has continuously built upon its design and tooling capabilities, together with the unrivalled success in the utilisation of Bihler Vari-slide automatic forming machines.
The company is fully QA certificated to ISO 9001 and ISO 13485 and operates in the UK from its two state-of-the-art manufacturing plants in Mildenhall, Suffolk, and at Oldham, Lancashire. A milestone was achieved when JEB acquired a major shareholding in a small company in 2003 known as UTM, with a mission to provide safe training ammunition that would allow military, law enforcement and professional training organisations to ‘train as they fight’ in authentic training environments and disciplines.
Multi-disciplined technology
Today JEB prides itself in providing innovative solutions for the manufacture and assembly of a wide range of quality products that rely on the latest multi-disciplined technologies.
From a single source, JEB can not only optimise products for manufacture, but also handle new product development from an early design stage through to commercialisation. The company has many years’ experience in tool and jig design with in-house tooling facilities for metal or plastic components and their subsequent assembly. This is supported by a broad range of engineering skills, quality management and regulatory support for the validation of its manufacturing processes.
JEB has developed its business around three core skill areas: Metal Stamping, Injection Moulding and High-End Assembly. In each area the company applies the same high standards and production values. John Talbot said, “Much of our success stems from our early days when we began by making machine tools for Bihler automatic forming machines. This led us to making tools to allow us to produce components in-house, as a sub-contract component manufacturer. Through time, we then became the agent for Bihler in the UK. Barry Littlewood, our CEO, set up Bihler in America in 1976 and continued to develop the business in the UK. Today, JEB provides multi-disciplined solutions for the manufacture of components and assemblies, through to the high volume production of training munitions”.
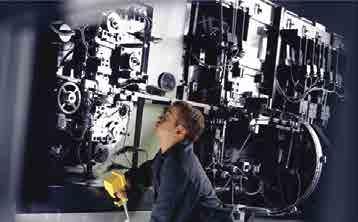
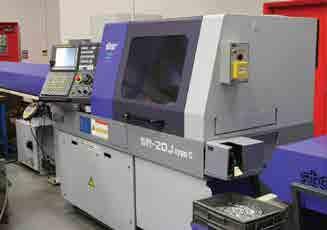
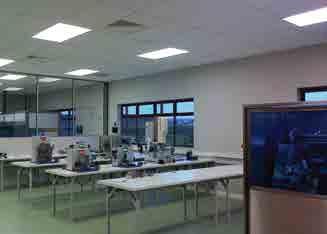
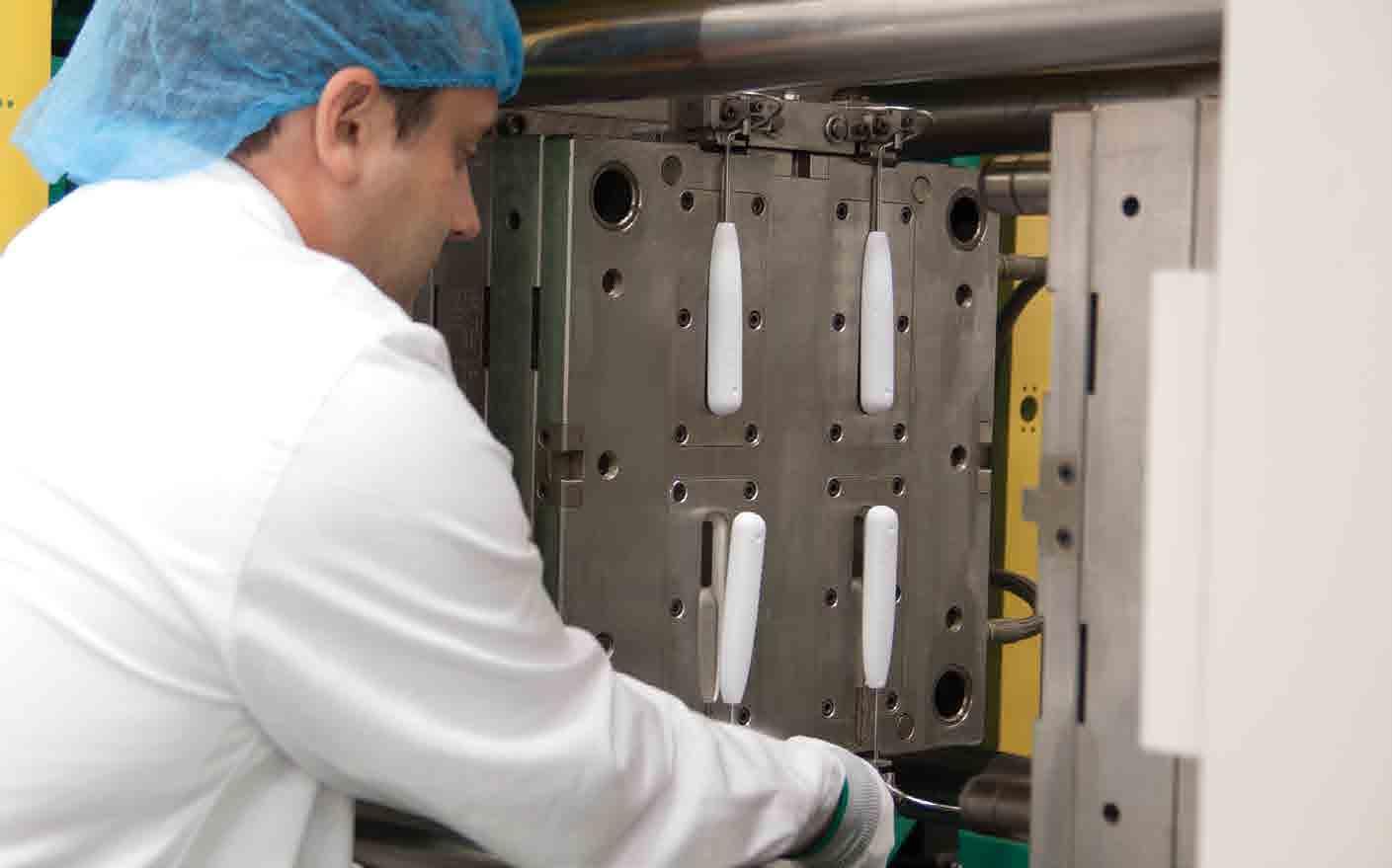
“Our success in the USA has been enhanced by the winning of a major contract against much bigger competition, where we secured the US Department of Defence business for the production of 5.56 training munitions for M16 and M249 Weapon systems. Today our products are distributed worldwide through our network of agents.
“Furthermore, whilst the defence market is very important to us we are seeing strong growth in the medical sector too where we are focused on increasing our market share. In November this year we are having a significant presence at the ‘Compamed Trade Fair’ in Düsseldorf, where we shall be exhibiting in Hall 8A on stand S25. Our colleagues from the US will also be joining us at the exhibition to demonstrate a surgical light product that to date has only been sold and manufactured in the US. In tandem with the exhibition, we shall also be launching our new website that will complement our increasing presence in the market. We continue to employ the very latest technology for CNC machining, laser and ultrasonic welding with associated finishing and de-burring processes. Our Class 8 assembly area supported by a fully automated cleaning and passivation process meet the very high standards required by the healthcare industry.
“We remain very flexible in providing solutions for low to high volume manufacturing, moulding, over-moulding, and assembly processes.”
Talbot added, “Where we score is when someone comes to us with a sketch. We can then take it and develop the product or component right through to commercial manufacture. We continue to drive costs down through providing innovative solutions and a prime example of this was the re-design of a metal clinch form that enabled us to significantly reduce the material thickness of a kettle control component supplied to Strix Ltd, one of our major customers. We are constantly evaluating our processes to stay one step ahead of the competition. We are also proud of our on-going apprenticeship scheme and have recently been awarded Apprenticeship Employer of the Year for a
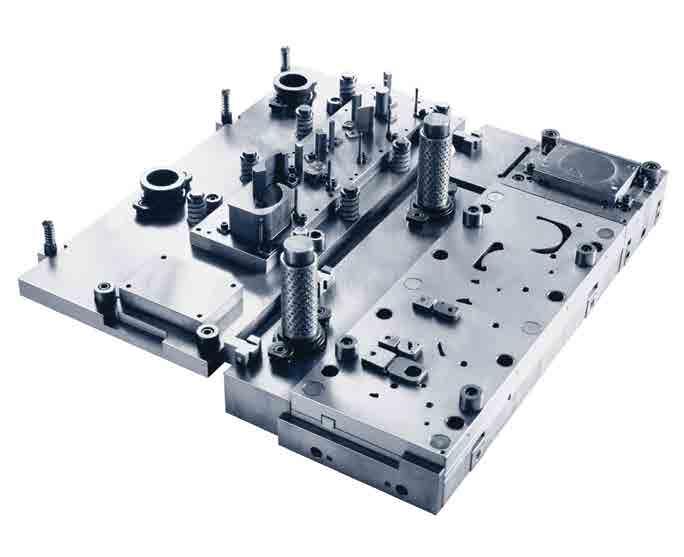
medium sized organisation within our region. Winning this award automatically enters JEB into the National Finals which are also held in November. Today, approximately half of our current workforce has been employed through this scheme.”
Advanced patented engineering
Following the major shareholding acquisition of UTM, JEB Engineering Design put their exceptional engineering skills to work and developed a completely new aluminium training round that replaced the original UTM zinc round. The new design, quality control and advanced engineering proved highly successful when tested by the US military and achieved a 99.8 per cent reliability rating in 2007 and has done so in every year since.
This makes it the highest rated nonlethal training ammunition on the market with low emission and non-toxic primer options also available.
JEB says that continual advances in manufacturing and product assembly techniques are driving ever greater demands for quality assurance. To respond to these market forces the company uses statistical process controls, to monitor, in agreement with its customer, predetermined parameters. This data can then be analysed and shared. “First class equipment, well trained personnel, sound quality procedures and the overriding desire to ensure customer satisfaction. These are the essential ingredients of our continued success,” commented Talbot. n
For further details of the JEB Group’s innovative products and services, visit their new website at www.jebeng.com

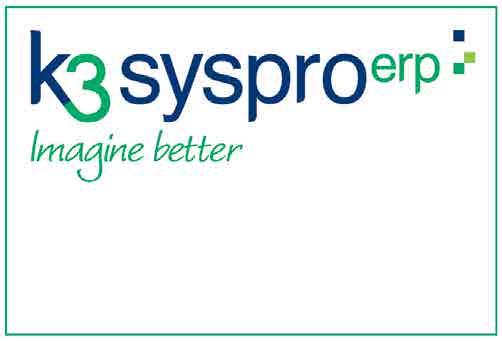
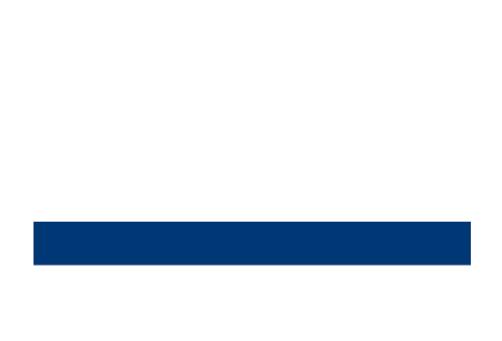
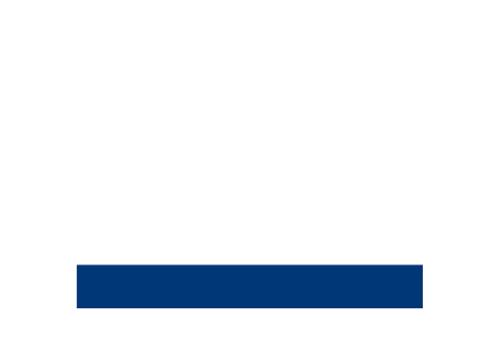
Anopol is the UK’s largest group offering electro polishing, pickling, and passivation and cleaning treatments for stainless steel, nickel and nickel alloys.
With over 40 years experience, Anopol can rightly claim to be the market leader in chemical and electrochemical processing of stainless steel, and other metals, for a wide spectrum of industrial, decorative and functional applications.
In addition to offering sub-contract services, plant and chemicals, Anopol can also supply an extensive range of pickling, passivation and general cleaning products for stainless steels. These are suitable for use by companies who wish to carry out their own processing.
Anopol operates from 2 sites, one in Birmingham and the other in Bordon, Hampshire.
info@anopol.co.uk www.anopol.co.uk