
11 minute read
Quality components for the automotive industry

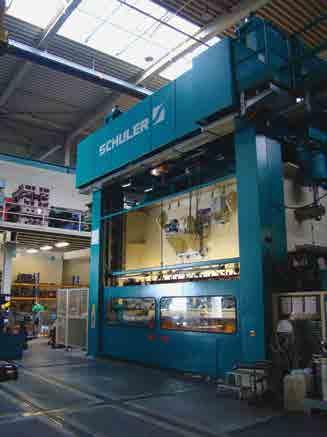
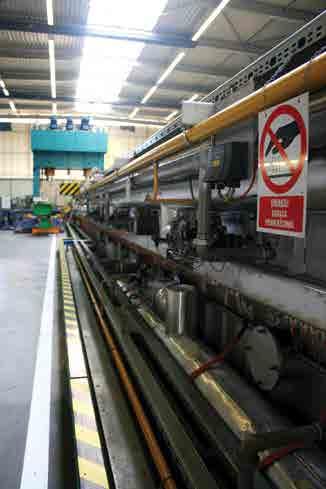
QUALITY COMPONENTS
FOR THE AUTOMOTIVE INDUSTRY
Gedia Poland, a company from Nowa Sol, Poland, is a part of Gedia Automotive Group and develops and manufactures components for car bodies. In its production process it uses the latest technology called hot forming.
GEDIA Automotive Group is a global, private company with headquarters in Attendorn, Germany. Its origin dates back as far as 1910. For more than 30 years the group’s core interest has been focused on the global automotive industry. GEDIA has specialised in the development of body press parts and welding components for cars and trucks. Front end, floor and assembly, or rear end – GEDIA delivers custom-made press parts and welded assemblies for every part of the car body.
The group’s annual turnover in 2013 is estimated as more than €400 million. It employs about 2700 people worldwide. GEDIA Automotive Group includes locations in Poland, Spain, Hungary, and China. It has joint ventures in Mexico and the USA as well as engineering centres in France and Sweden.
In 1998 it built its first production plant in Nowa Sol, Poland, which specializes in cold and hot forming. Ten years later Gedia opened its second production unit in Nowa Sol - Assembly (GPL2). A great selection of components
“Nowadays, Gedia Poland is the group’s biggest company, with its annual sales estimated as €200 million and with 1200 employees,” says Ryszard Gongor, the Gedia Poland managing director. “From the very beginning the Gedia Group has had very serious investment plans for our company and we have been benefiting from our parent organisation’s know-how. This back up has allowed us to achieve our current position.
“We deliver car components to more than 200 automotive manufactories. European car manufacturers account for approx. 90 per cent of our customers. Among them are major brands such as Audi, BMW, Chevrolet, Daimler, Fiat, Ford, GM, Mini, Opel, PSA, Porsche, Scania, Seat, Skoda, Suzuki, Vauxhall, Volvo, Valmet and VW. Our products portfolio is huge and includes about 1400 various components. Such diversification protects us from the fluctuations of the market. On the other hand, it is also a major challenge for us due to the high degree of complexity of our offer,” adds Mr Gongor.
Some like it hot
Gedia Poland is a leading European manufacturer of components produced by hot forming technology. It is the GEDIA Group’s first production facility, which uses this technology and the first company of this kind in Poland. The hot forming line was launched in Nowa Sol in June 2012.
“Hot forming is a process dependent on temperature and time. Parts are formed in their soft state at elevated temperatures and then quenched in the tool,” explains Mr Gongor. “Components made by hot forming are stronger and they may have complex shapes. Furthermore, the springback effect is reduced. Springback occurs when a metal or alloy is cold-worked and the material has a tendency to return partially to its original shape due to the elastic recovery of the material. Hot formed components can
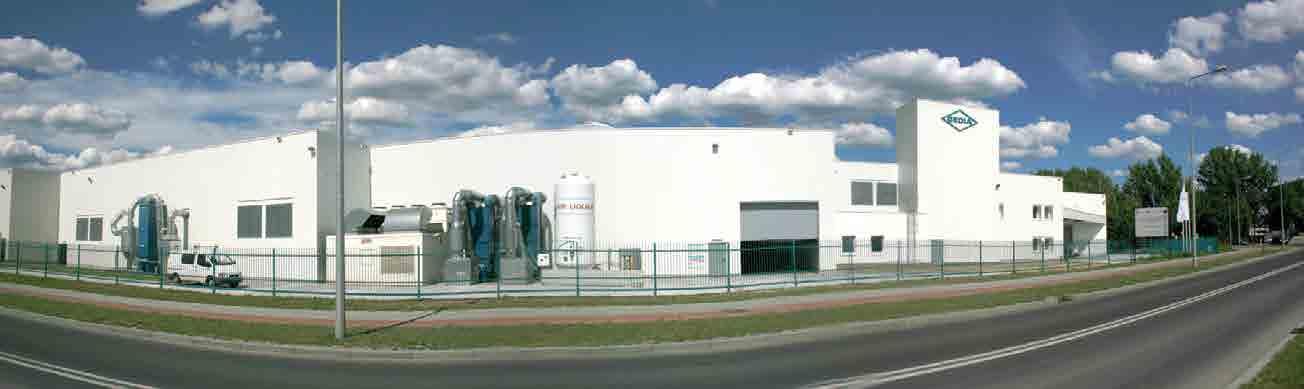

BMW i3: The world’s first premium electric car has Novelis aluminium under body structure
Novelis supplies its innovative automotive alloy Novelis AdvanzTM c300 for the under body structure of the BMW i3, BMW’s latest sustainable, emissionfree mobility platform. This aluminium sheet has been specifically developed for automotive structural body applications with high crash performance requirements. It offers good formability, a strength level equivalent to high strength steels (on a weight-specific basis) and an extraordinary energy absorption capacity. The BMW i3 was officially unveiled last summer as the “world’s first premium electric car”, with a carbon passenger compartment characterized by the use of high-quality, sustainable materials.
Voestalpine
The voestalpine Group is one of the leading partners to the automotive industry in Europe, with its top-quality steel based products. Headquartered in Linz, voestalpine is represented by over 500 group companies and locations in more than 50 countries. Voestalpine Rotec Group is specialist in the production and further processing of precision steel tubes, and they are expanding their existing subsidiary in Poland. Located in Środa Śląska, since 2001 the factory processes tubular components used in the automotive industry including anti-vibration elements, chassis components, steering columns, airbag tubes and car seat structures. The company employs over 180 people, with annual sales over €27 million. As a result of the dynamic development of the automotive market in this part of Europe the company took a decision to increase its production capacity in Poland. The investment project is taking place on the Legnica Special Economic Zone, directly neighbouring the existing manufacturing facility. The construction of the factory and installation of new production lines to further increase the production portfolio, are expected to be completed in the first half of 2015, so that mass production can begin from mid-2015. Voestalpine Rotec will invest a minimum of €6 million and employ several dozen new employees by 2020.
Poland Tokai Okaya
The metal stamping parts manufacturer Poland Tokai Okaya Manufacturing (PTO) offers a wide range of advanced presses in a variety of sizes, thicknesses and shapes. PTO is highly experienced in the use of many kinds of materials from steel and aluminium to stainless steel. It also provides a number of additional services including design, welding, pressure welding, washing, assembly and many others besides.
Muhr Metalltechnik GmbH & Co. KG
As a medium-sized family-run company based in Germany in Wenden Muhr Metalltechnik GmbH & Co. KG has continually expanded its manufacturing capacities to the extent that we are now able to offer our customers fully integrated and optimized solutions from component design right through to large batch production.
For production of numerous components made of steel and aluminium for the automotive and heating industry there is a highly modern tool shop as well as industrial facilities and storage space on a roofed area of about 45,000 square meters.
Product range
The wide product range enfolds mainly stampings and pressing, blank outlines for hot forming, strut braces, welding assemblies as well as seats for specialpurpose vehicles and radiators. The machinery park enfolds mechanical- and deep drawing presses from 200t till 1,100t / 2D- and 3D-Laser as well as several welding machines. As a quality-conscious supplier to the automotive industry, our business operations are certifi ed as conforming to ISO/TS 16949 and DIN ISO 9001 standards.
GEDIA Nowa Sol & Muhr Metalltechnik/ MM Systemy
GEDIA and Muhr Metalltechnik united by their successful long-term cooperation, which is going to intensify by building a new plant in the Polish town called Kąty Opolskie near to Opole.
Since the opening of the polish affi liate MM Systemy, located in Kąty Opolskie, in October 2014, numerous stamp parts have been produced by 400 tons and 1000 tons transfer presses especially for the GEDIA plant in Nova Sol. Over the next few years MM Systemy is planning to create more than 30 new jobs.
For further information, do not hesitate to visit us: www.muhr-metalltechnik.de and www.mm-systemy.pl
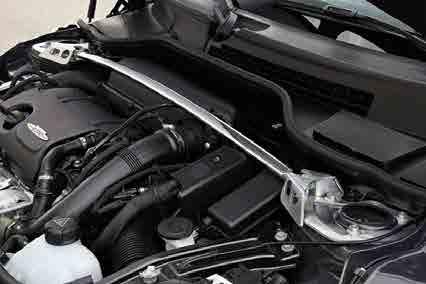
Head Office in Germany, Wenden Dome bar out of polished aluminium for MINI GP II
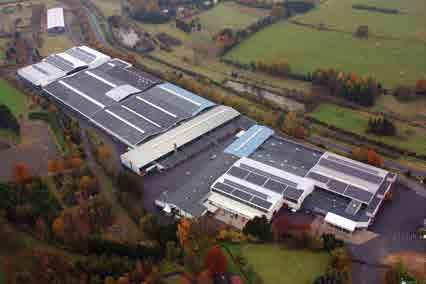
Muhr Metalltechnik GmbH & Co. KG - Everything from toolmaking to serial manufacture
As a medium-sized family-run company based in Germany in Wenden, Muhr Metalltechnik GmbH & Co. KG has continually expanded its manufacturing capacities to the extent that we are now able to offer our customers fully integrated and optimized solutions from component design right through to large batch production. For production of numerous components made of steel and aluminium for the automotive and heating industry there is a highly modern tool shop as well as industrial facilities and storage space on a roofed area of about 45,000 square meters.
As suppliers to the automotive industry we concentrate on the following: • Production of cutting and drawing dies • Series production of pressed steel and aluminium parts which are • processed into welded assemblies • Production of strut braces • Manufacture of seats for special-purpose vehicles
Product range The wide product range enfolds mainly stampings and pressing, blank outlines for hot forming, strut braces, welding assemblies as well as seats for special-purpose vehicles and radiators. The machinery park enfolds mechanical- and deep drawing presses from 200t till 1,100t / 2D- and 3D-Laser, several welding machines. As a quality-conscious supplier to the automotive industry, our business operations are certified as conforming to ISO/TS 16949 and DIN ISO 9001 standards. The world’s leading car manufacturers and suppliers of automotive components rely on the professional experience we have gathered over many years in the sector.
GEDIA Nowa Sol & Muhr Metalltechnik/MM Systemy GEDIA and Muhr Metalltechnik united by their successful long-term cooperation, which is going to intensify by building a new plant in the Polish town called Katy Opolski near to Opole.
Since the opening of the polish affiliate MM Systemy, located in Kąty Opolskie, in October 2014, numerous stamp parts have been produced by 400 tons and 1000 tons transfer presses especially for the GEDIA plant in Nova Sol. Over the next few years MM Systemy is planning to create more than 30 new jobs.
For further information, do not hesitate to visit us: www.muhr-metalltechnik.de and www.mm-systemy.pl
TECHNICAL
TECHNICAL is a manufacturer of machinery and equipment for various industries. The company’s intense activity has resulted in the production of modern, high-level technical machinery, equipment and production lines equipped with advanced electronic control systems and management systems of production processes.
TECHNICAL is well-known producer both in Poland and in Europe. Its machines and equipment are designed primarily for use in the foundry industry as well as in the automotive, glass, metallurgy, mining, ceramics, insulation, refractory, and many other industries.
The main products of our company include: shot blasting machine and turbine mixer. More information about our company and our products are included on website www.technical.com.pl
Our machinery, equipment and complete production lines are sold to Germany, the UK, Denmark, Serbia, Ukraine, the Czech Republic, Slovakia, Russia, Kazakhstan, India, Egypt, the USA.
We are proud to co-operate with a number the European industry leaders, including our regular partner GEDIA POLAND SP Z OO from Nowa Sol.
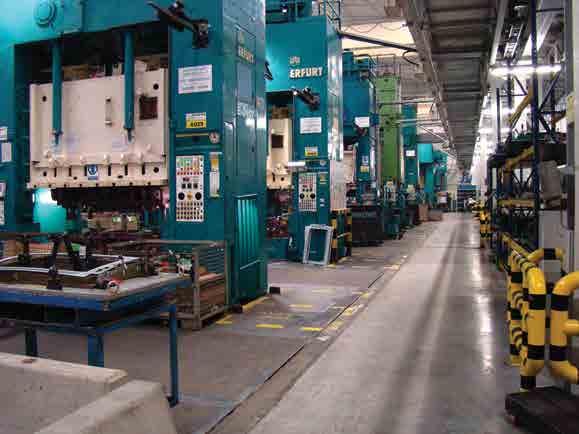
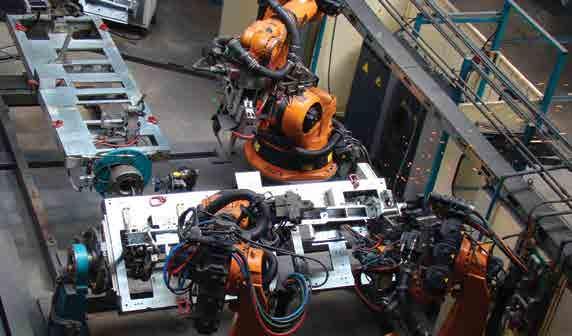
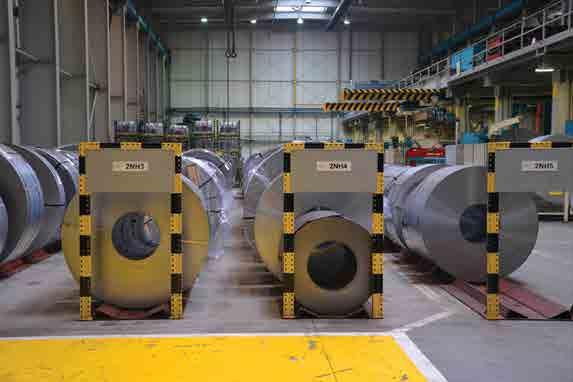
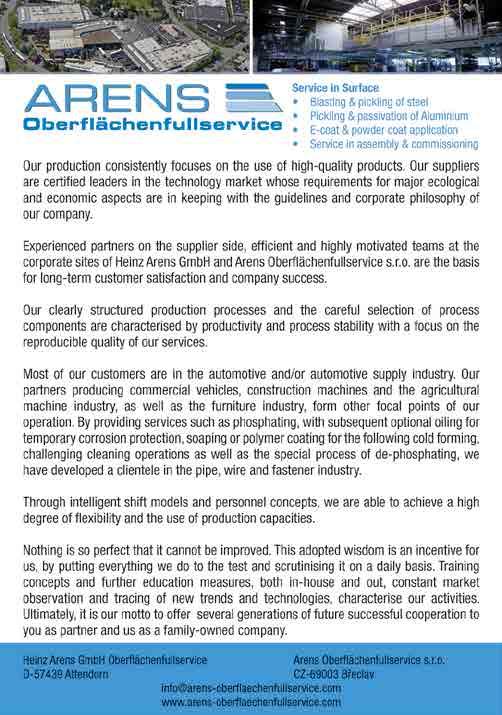
be produced in a much shorter amount of time. Moreover they are lighter than those, which are cold formed.”
Hot forming has become an important process in manufacturing components for the automotive industry, as it meets specific requirements for higher crash safety and lower overall weight. Such car body parts as pillars, front and rear bumper beams, door beams, door sills, roof rails, side-rails, and roof frames are now hot formed.
In January, 2015, the new, second, hot forming production line will be launched in Gedia Poland.
Only the best suppliers
“The quality of the products and services of our suppliers is a decisive factor for the quality of our products. We believe in an active role for the supplier in our production chain, in fair partnership and in a success-oriented cooperation. Because the quality of our products and performances is of crucial importance for the common company success, we are committed to comply with GEDIA´s quality policy. That is why we only supply products of impeccable quality. As for the raw material suppliers, they come from the first league of suppliers, and we cooperate only with suppliers who employ the latest technologies. It is of great importance for us that all suppliers commit themselves to our quality policy. We expect them to meet exactly our delivery dates and quality requirements,” says Mr Gongor.
One company instead of two
Gedia Poland expects a significant event early next year, for which it has made intensive preparations. On January the 1st, 2015 the company will take over 100 per cent of the Gedia Poland Assembly shares.
“In June, 2014 Gedia shareholders adopted a resolution on the merger of both companies operating in Poland, and at the end of August, the boards of both companies have agreed the fusion plan. Now, 12 teams are working on such practical aspects of the takeover as: human resources, IT, finances and technology. We’ll take all the GPL2’s assets and liabilities,” says Mr Gongor.
What is behind the merger of the two companies? “They both operate in the same industry. GPL2 is focused on highly complicated assembling for the automotive industry, such as longitudinals for the Opel Astra IV and body components for the BMW i3 and BMW i8. Furthermore, the companies are reliant on each other, and their production processes are in fact closely linked. The main reason for Gedia Poland to merge with GPL2 was to enable the optimal use of the resources of both entities, to increase the efficiency of the company and to achieve the synergy effect,” explains Mr Gongor. n
www.gedia.com
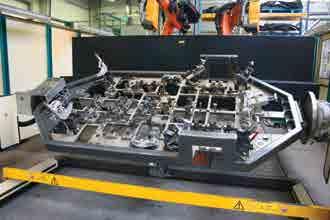
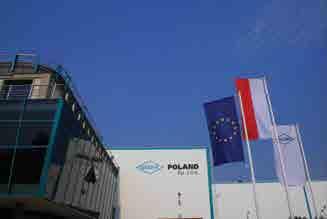