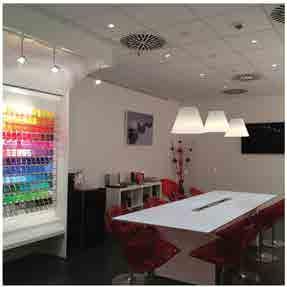
8 minute read
In full colour Ampacet
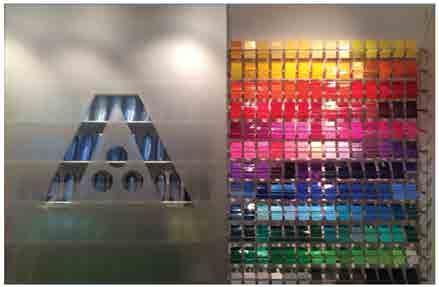
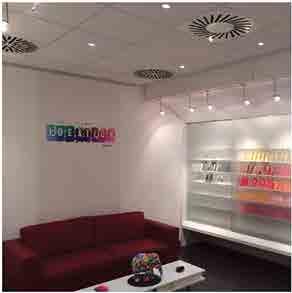
IN FULL COLOUR
Since 1937, Ampacet’s Masterbatch technology has enhanced the value of a broad range of plastic products, giving them the right look and function. Ampacet’s Masterbatch range of Black, White, Colour and Additives are used in almost every polymer plastic process and application. Abigail Saltmarsh reports on Ampacet’s continued European success and the company’s ongoing strategy for global expansion.
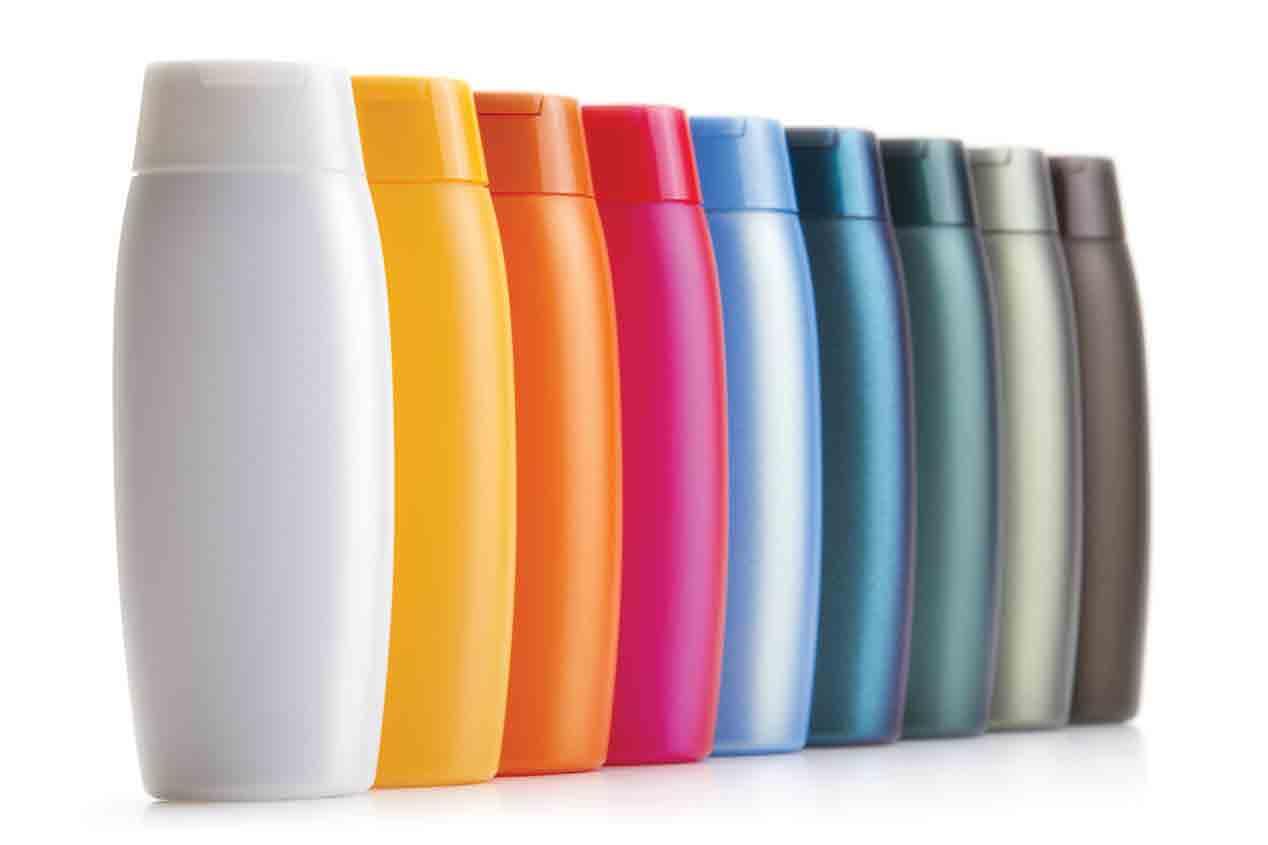
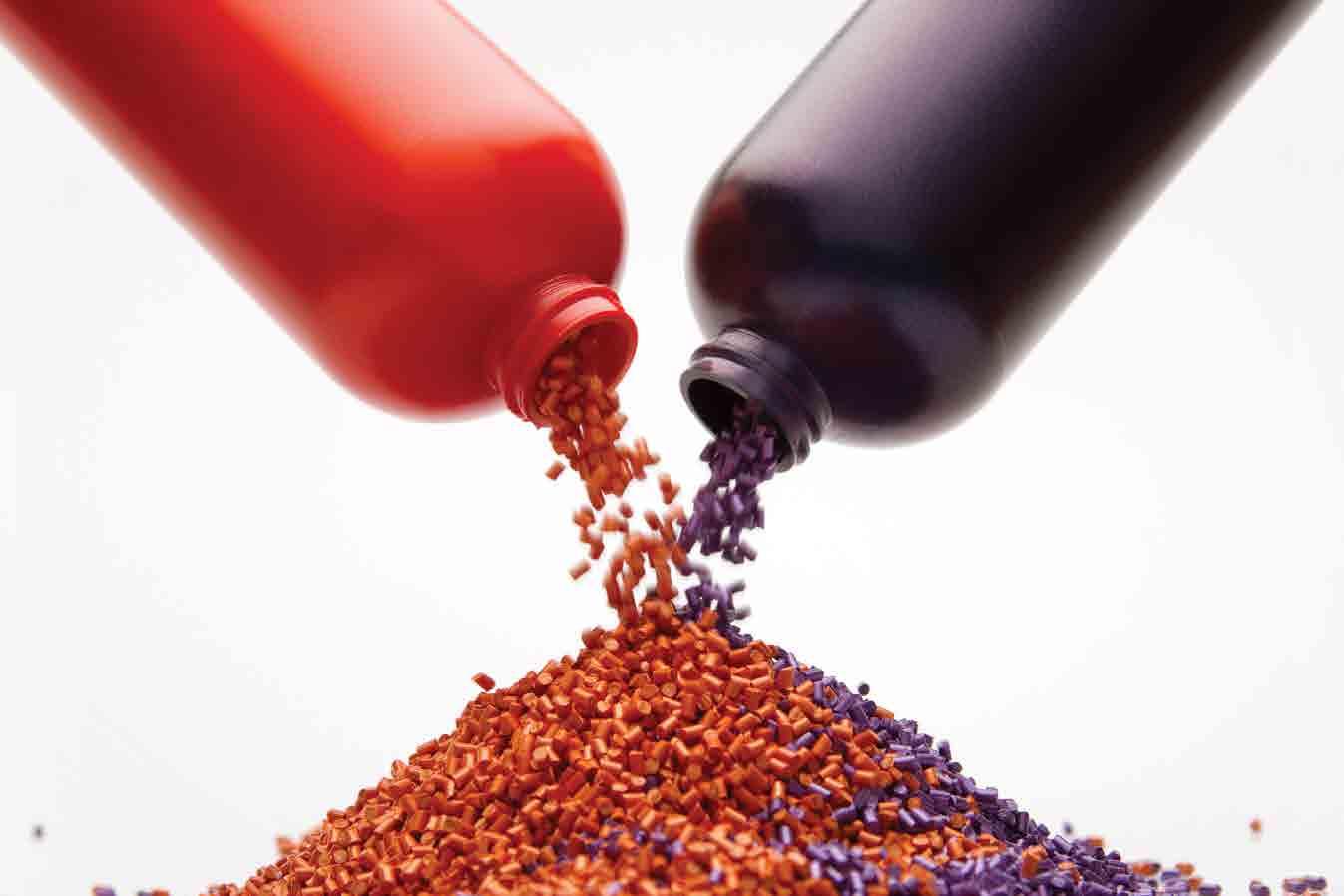
The game has changed for Leading Masterbatch producer Ampacet, according to Philippe Rey, director of marketing and business development EMEA. “The company is now not only recognised as a well-established global player but also has a good reputation for its broad portfolio and its unequivocal insistence on excellence.
“Ten years ago we were perceived as a commodity player,” he explains. “We were seen as a company that could only offer black and white Masterbatch. Now, however, we are not only seen as a company offering a full product range; Black, White, Additives and Color Masterbatch, but it is much more about adding value and creating speciality products for our customers.”
For many years now Ampacet has been classed as a leader in the Masterbatch industry. The company’s success is down to its ability to partner suppliers and customers and to create Masterbatch formulations that help bring products quickly to market and satisfy the needs of its customers to the best of its ability.
New state-of-the-art European headquarters
Ampacet’s history dates back to 1937, when the American Moulding Powder and Chemical Corporation were formed in Brooklyn, New York. Since then, the privately owned company has grown to such an extent that it currently operates 24 sites globally, produces in excess of 400,000 tonnes annually and sells its products in more than 90 countries.
Ampacet has four research and development centres – two in the Americas, one in Asia and one in Europe – and the latest developments at the company have seen the opening of a new state-of-the-art European headquarters, as well as new production capacity and a new European Ideation centre at Dudelange, in Luxembourg. The investment of approximately €25 million includes the installation of a new production line and an increase in capacity of approximately 30 per cent in terms of related production lines in Europe.
“The site also offers the possibility for further increases in capacity,” says Christian Tourtier, director of Manufacturing. “The new Dudelange plant also includes the latest environmental and manufacturing technologies to ensure production of the highest quality Masterbatches, respecting the international standards of ISO 9001.”
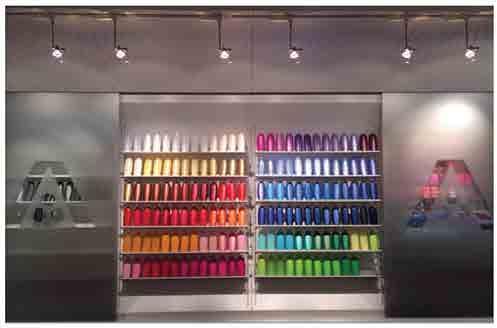

CREATE VALUE BY ANTICIPATING THE NEEDS OF CUSTOMERS
Founded in 1924, Daikin has a turnover of roughly 13 Billion euros with more than 56,000 employees operating in 209 companies worldwide with 28 subsidiaries in Japan and 181 internationally. Daikin Industries, Ltd. has become a global company with its Air-Conditioning systems and Fluorochemistry businesses at the core. Daikin Industries is the world leading manufacturer of air conditioning and uorochemical products. Fluorinated gases are strategic to A/C. is gives a unique and strong position to Daikin Industries. Daikin is securing its production through the integration of key raw materials and the addition of new production capacity. Daikin has integrated its own raw material (Fluorspar). Daikin o ers more than 1.800 kinds of uorochemicals as uoroplastics, uoro- elastomers, uorocoatings, uorocarbon gases, uorochemical intermediates, water and oil repellents, additives, ne chemicals, mold release agents…
DAIKIN PLASTIC ADDITIVES
Fluorine compounds exhibit many unique properties like Chemical, heat and ame resistance, wateroil repellency, low gas permeation, non-stick… anks to these unique properties Daikin o ers a wide product range of plastic additives. is product segment includes Polymer Processing Aid (PPA), MPA Anti Drip, Unidyne Anti Fogging- Repellents, Micro Powder. e laboratory for R&D and technical service is located in France. Its focus is to develop new products to satisfy customer needs: to help our customers in the evaluation of our products and to give advice to optimize their production.
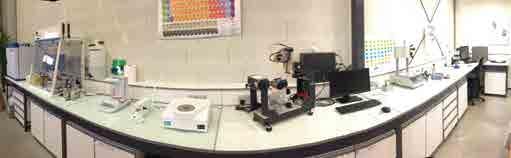

Polymer Processing Aid (PPA’s)
Daikin PPA’s are based on the latest generation of uoropolymers developed and are tailored to improve extrusion properties of polymers such as LLDPE, mLLDPE, HDPE, PEX, PP, PET, PBT, PA and others. Main bene ts to use PPA’s (directly incorporated in resins or via masterbatch) are: • Melt Fracture Elimination (sharkskin) • Gloss improvement and haze reduction • Gel reduction during extrusion • Die build up reduction • Waste reduction and productivity increase • Improve processing of LLDPE rich blends.
By adding Daikin PPA’s at a level of only 500 ppm, a dynamic coating is created inside the extruder to reduce friction and modify the velocity pro le of the extrudate.
Daikin PPA’s are suitable for many di erent processes such as blown and cast lm, extrusion blow molding, wire and cable, pipe and tubing, ber extrusion among others. Daikin’s shear rate calculator app was developed to select the correct PPA best suited to the processing conditions. First generation Daikin PPA’s were launched in 2008 with DA-310 ST for cast lm and other processes, DA-810 X for blown lm. ese 2 PPA’s are based on a low Mooney viscosity uoroelastomer that is easy to disperse, creating no die build up and small drops with an ef cient rate of 500 ppm. In 2010, Daikin introduced new PPA technology through our third generation PPA: DA-910 for LLDPE and mLLDPE. is PPA is based on a functionalized uoroelastomer combined with low Mooney viscosity, showing similar bene ts to rst generation products but with an e cient rate of only 300 ppm. Based on new research and development, Daikin will be soon introducing new PPA’s in 2015 for additional applications.
Without PPA With PPA
Anti-Drip Additives
Anti-drip additives are used to improve ame retardant formulations. PTFE ne powders exhibit unique behavior by creating a bril network in the polymer. PTFE does not melt when the primary polymer burns. e network shrinks when exposed to ame and prevents dripping. It also reinforces the molten polymer during extrusion and increases polymer melt strength. Testing shows reduced drip and ame propagation and allows products to pass UL94 V0 Quali cation (US plastic ammability standard). PTFE strengthens char formation in resins as well as preventing dripping during combustion. is is particularly useful in wire/cable and building materials applications. ese anti-drip characteristics help to retard ame propagation.
Water/oil repellents
Fluorochemicals can modify surface tension of plastics to be more hydrophobic/ oil repellent or hydrophilic. Examples of typical applications are anti-fog additives for packaging or agriculture lm, oil repellency for bottles and others. Here, for green house lms, surface tension properties create liquid spread on lms: clarity is then enhanced, light transmission is improved and as a result plant growth time is decreased.
Micro Powders
Daikin Micro Powders are based on PTFE technology. Added to speci c resins (thermoplastic engineering resins), micro powders help to improve wear resistance of these polymers. ey also decrease marring, coe cient of friction and improve non stick properties when added to these resins. ese additives are suitable for PC, PA ..
New ideas
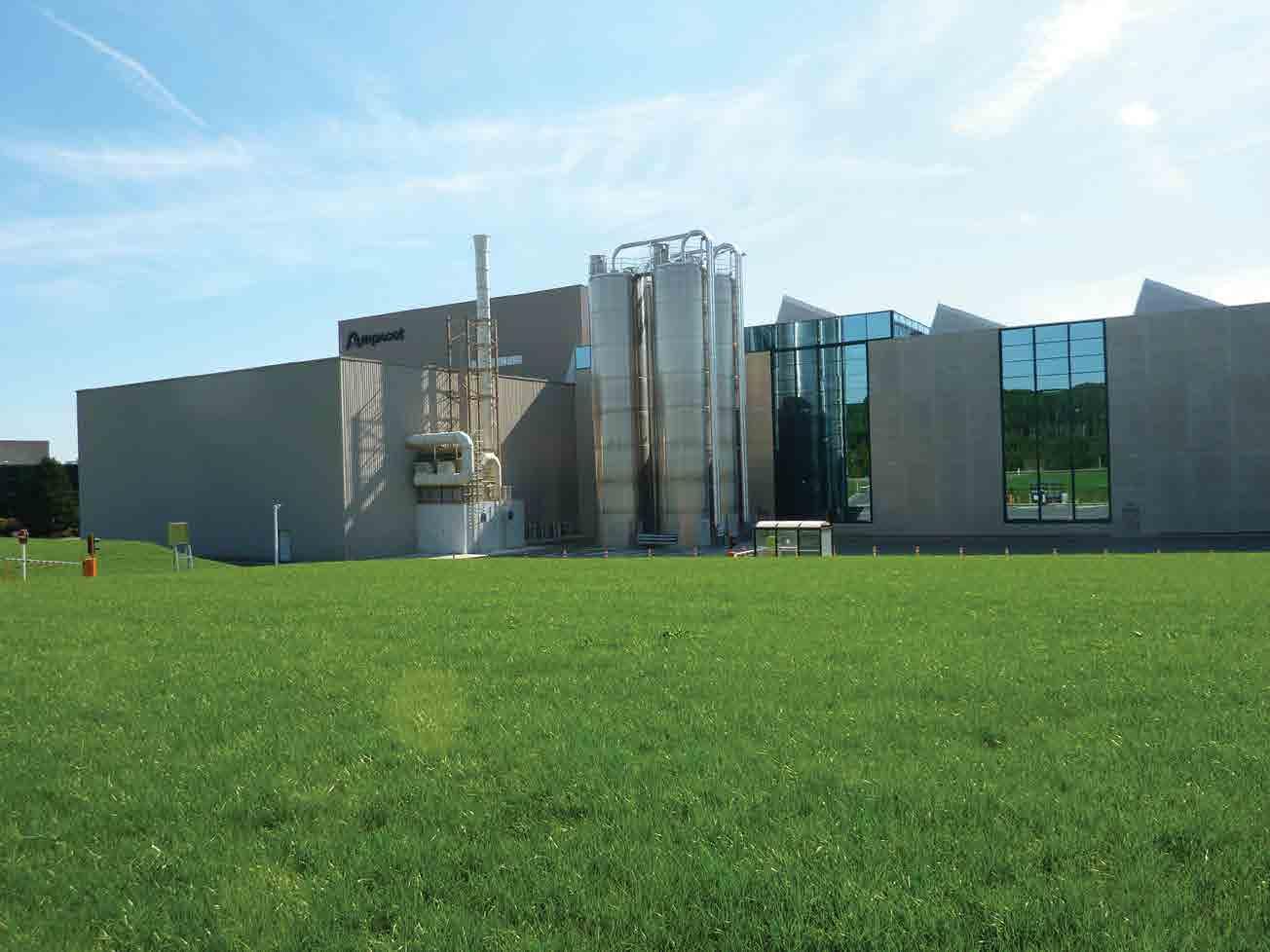
Ampacet’s Masterbatches are used in almost every polymer, plastic process and application. Its customers come from a range of markets, including food and beverage, industrial, hygiene, personal care, cosmetic, textiles, toys, electronics, construction, agricultural and greenhouse films.
Caroline Scheydecker, senior marketing and communications coordinator, explains that the new Ideation Centre is where product design and engineering come together. “Ideation by Ampacet is a new concept that offers our customers a creative environment where they will journey from an ‘Idea to a Realisation’. Our customers will go through three faster steps – innovation, development & actualisation – and will be surrounded by industry professionals and the latest cutting edge technology. Creative elements will be delivered in a variety of articles in a myriad of effects. With every step, Ampacet will be right there to ensure it utilises its industry expertise to deliver our customers’ final products to the market much more quickly.
A clear focus
Ampacet Europe SA has recently been announced the National Champion in the European Business awards. The company has also seen internal reorganisation, resulting in a greater focus on dedicated segments: Film, Moulding, BOPP and Extrusion.
“We are moving more and more towards focusing on dedicated areas,” says Mr Rey. “This enables us to offer our customers a much more specialised service and to have a better understanding of their development concerns. We have been doing this for the past two to three years and as we grow and move forward we want to strengthen this way of working.”
Continuing to invest
A new distribution centre, due to open at the end of 2014, will see Ampacet extend its reach to customers even further and will enable it to offer even more flexibility.
“This is another important stage in our global expansion strategy,” adds Carine Ringlet, director of Supply chain. “We are located at the heart of Europe, close to motorways that go in every direction.
Ampacet continues to expand in comparison to its peers in the plastics industry. When you look back at the years between 2008 and 2013, when the economic situation was so difficult, we were one of the only companies that continued growing.
“Our success then and now is because we continue to invest. Our target is to keep growing, beyond the industry rate. As a global company we plan to look more to the Middle East, Turkey and Russia and to look for acquisitions as well as organic growth.
“We recently acquired Allied Color and Additives (ACA), headquartered in Australia, and where there are other new opportunities which will benefit us geographically or from a product point of view we will certainly consider them. We are committed to the business segments we focus on and to growing in Europe, the Americas and Asia Pacific as we believe we can have much more global coverage and still offer the same level of excellence to our customers.” n
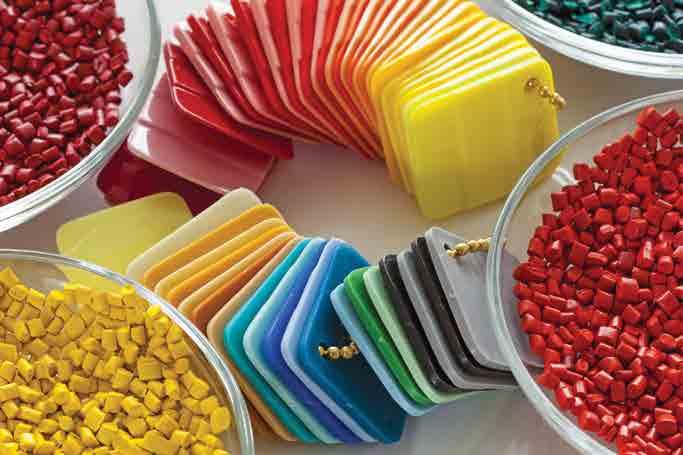