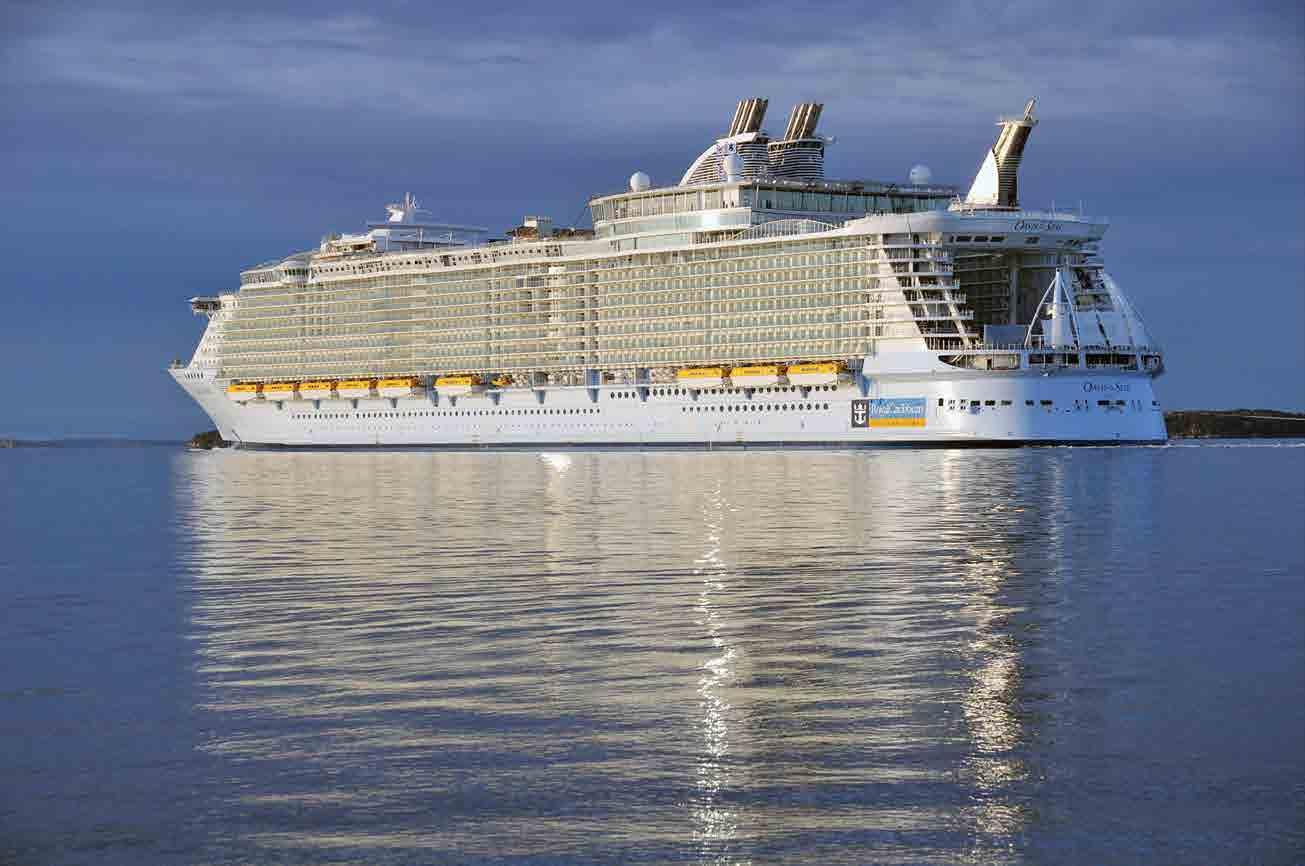
12 minute read
Energy efficient power solutions Wärtsilä
ENERGY EFFICIENT POWER SOLUTIONS

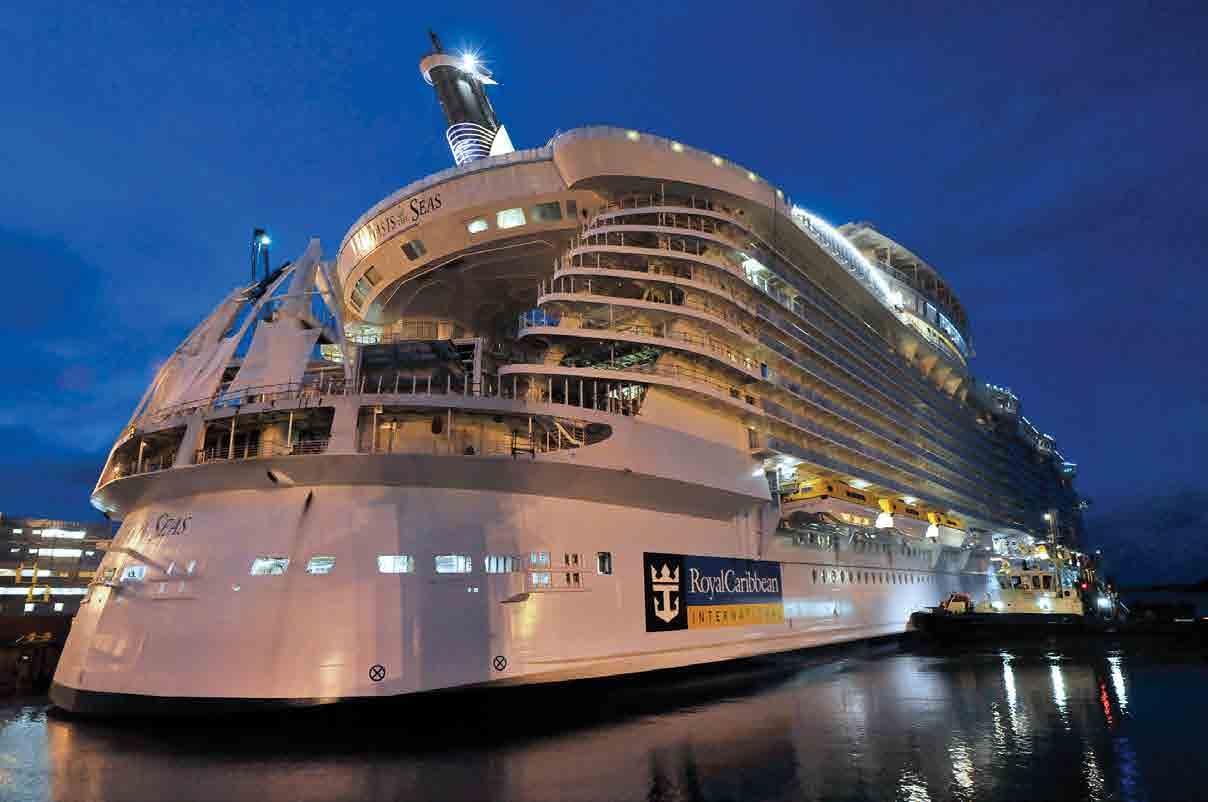
The Finnish company Wärtsilä is a world leader in power solutions such as engines for ships and power plants for electricity generation. The company is also a major supplier of heavyduty engines for the production and transport of oil and gas.
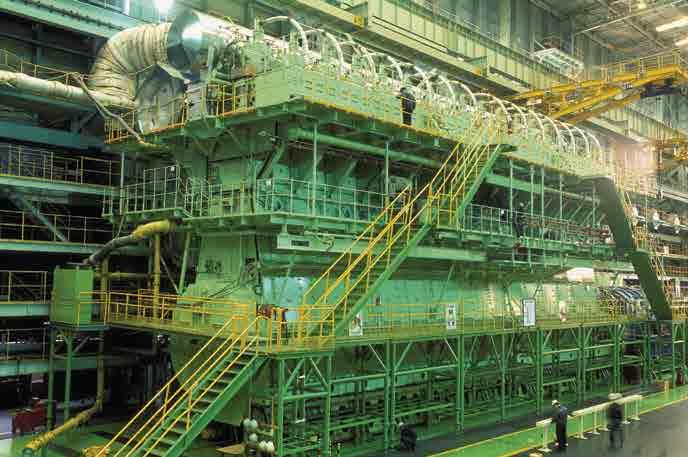
Wärtsilä produces complete lifecycle powers solutions for the marine and energy markets, including power plants for oilfields, engines for crude oil pumping and compression solutions for gas gathering and processing. As a means of power generation, Wärtsilä’s engines provide a higher level of efficiency than traditional alternatives. “Compared to gas turbines, our engine technology is very efficient. A 10-megawatt gas turbine has a 30 per cent electrical efficiency, but a 10 MW unit from Wärtsilä gives you an electrical efficiency of about 45 per cent,” said a company spokesperson.
In 2013 the group’s net sales totalled €4.7 billion with approximately 18,700 employees. It currently has operations in more than 200 loations in nearly 70 countries around the world.
Technology leader
In the oil and gas industry, the consequences of a fault can be ruinously expensive. Wärtsilä’s engines are therefore designed and built for continuous reliability. Production is based at the company’s factories in Vaasa and Trieste. “We supply the whole world from these factories,” said a company representative. “We developed the first heavy fuel oil engine back in the 1970s. We continue to develop the technology of our engines in order to improve their ability to run on complex fuels.”
The acceptance of complex fuels is one of the key advantages of Wärtsilä’s engines, which are designed to use the fuel from the well. The engines can run on different kinds of fuels, both the crude oil from the well and the associated gas. Wärtsilä’s engines function in desert temperatures as well as in cold climates and can be powered by a combination of liquid and gaseous fuels.
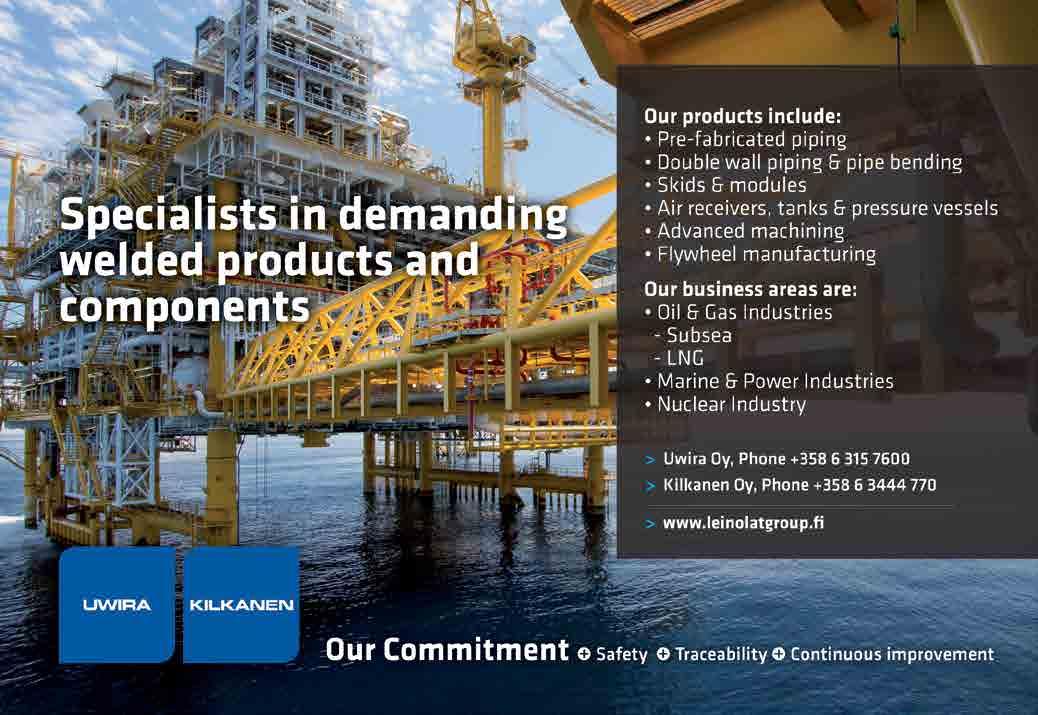

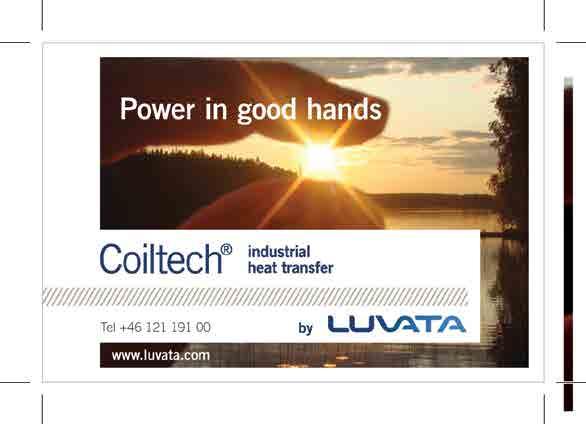
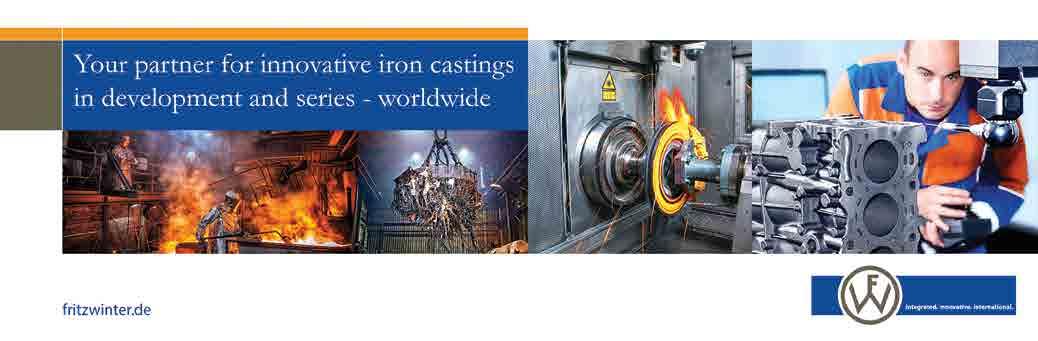
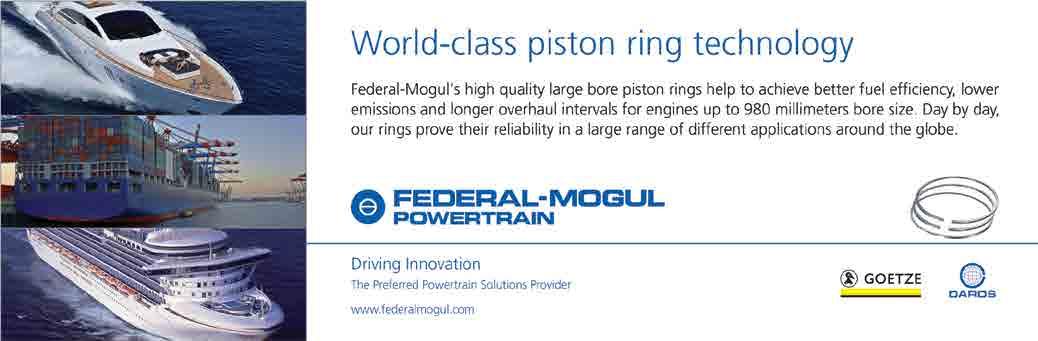

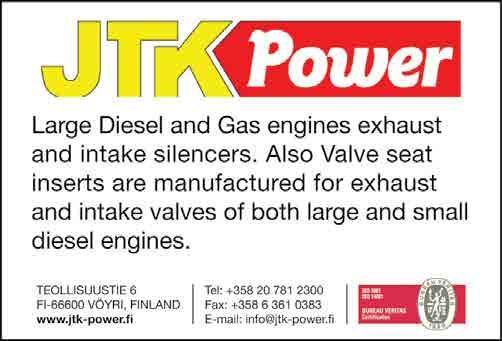

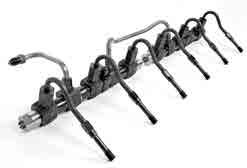

Common Rail Piping System
High-quality large engines increasingly rely on Common Rail System technology as it is key technology enabling significant improvements.
No matter whether the engines are used to power ships, locomotives, large commercial vehicles or gen-sets, with common rail piping systems from NOVA SWISS®, modern engines become cleaner, quieter and on top of that, help to protect the environment.
NOVA SWISS® Common Rail Piping Systems are designed for today’s sophisticated engines running on diesel, gas or in dual fuel mode, offering total fl exibility because of its modular design. It can be adopted to virtually any engine’s requirement.
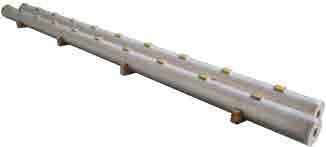

Pipes and Manifolds for gas engines
NOVA SWISS® gas pipes and manifolds are custom made. The sheathing concept sheaths simply and cost-effective and thereby conforms to classification societies.
The precise design allows simply assembly on engine. • engineered to your needs • sheathed and unsheathed up to DN80 • up to 500 bar operation pressure • stainless steel, other materials upon request • classification society compliant • accredited welding processes
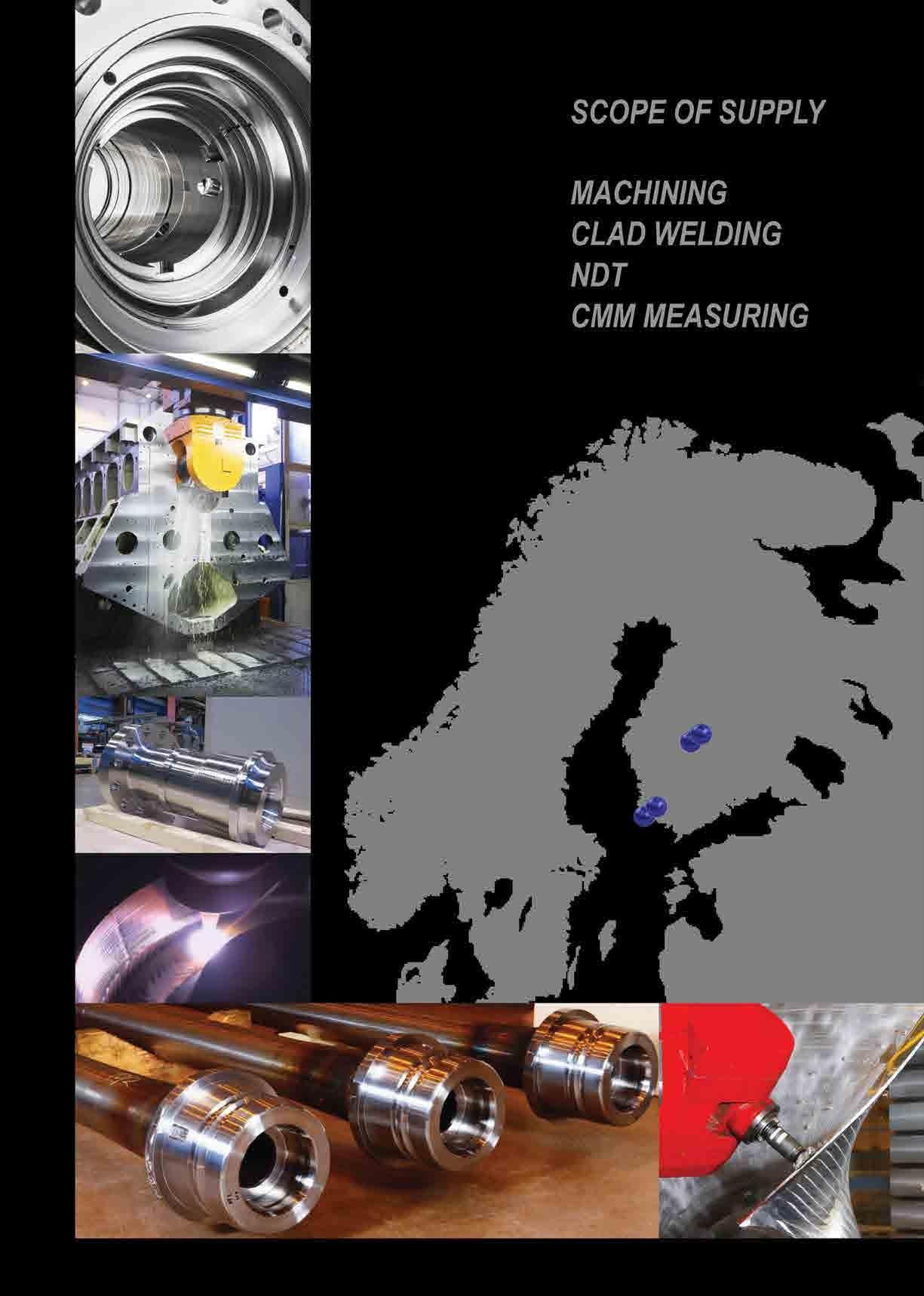
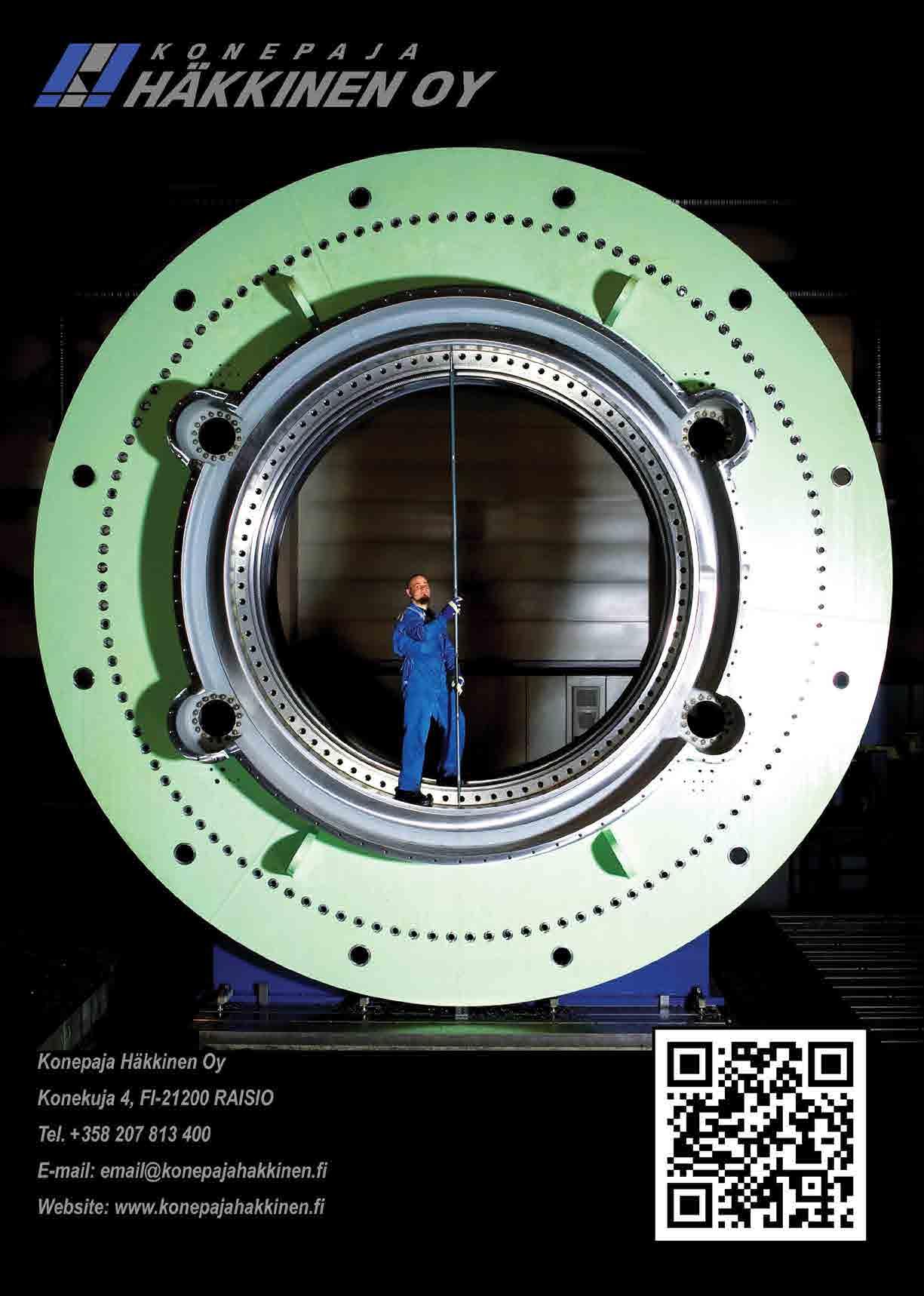
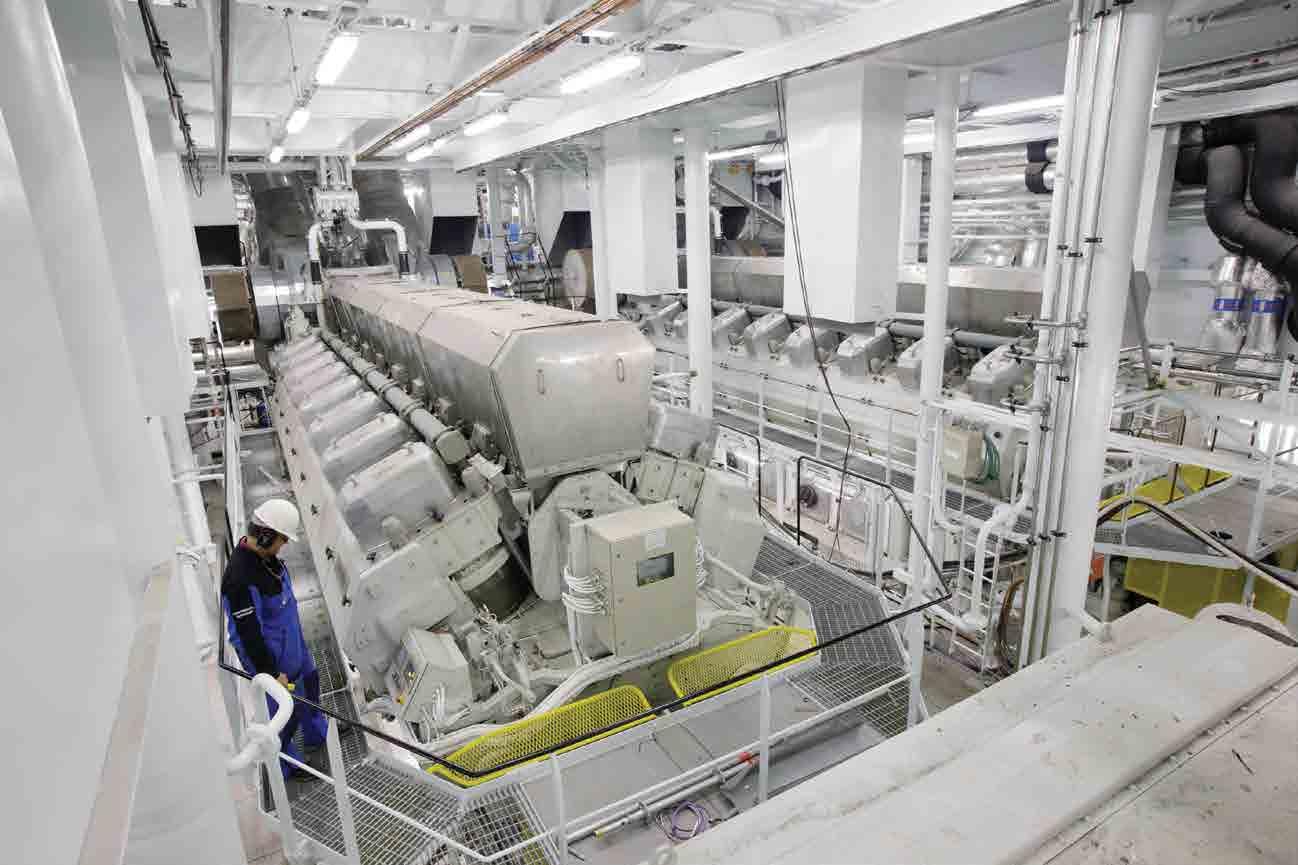
Because an oil well’s output is variable, Wärtsilä offers engines that can be adjusted to burn gaseous and liquid fuels in different ratios. The quality of the fuel changes over time but with our technology the engines will cope with these changes.
Minimising emissions
Environmental efficiency is also key for Wärtsilä and one of its recent projects have been aimed at minimising emissions. In September this year (2014) it initiated the HERCULES-2 research project alongside MAN Diesel & Turbo, another leading European engine manufacturer. This follows on from the original 2004 HERCULES R&D programme to develop large engine technologies.
The HERCULES-2 project is aimed at developing a fuel-flexible marine engine that is optimally adaptive to its operating environment. The work will focus on four areas of integrated R&D divided into Work Package Groups (WPG), as follows: WPG 1 – a fuel flexible engine; WPG II – new materials (for engine applications); WPG III – an adaptive powerplant for lifetime performance; and WPG IV – a near zero emissions engine.
This work will build upon and surpass the targets of the previous HERCULES projects by going beyond the limits set by the regulatory authorities. By combining the very latest technologies, and through the use of integrated solutions, the new project aims to achieve significant reductions in fuel consumption and exhaust emissions. The project includes several full-scale prototypes and shipboard demonstrators that will speed the development of commercially available products. This co-operation between Wärtsilä and MAN Diesel & Turbo will also involve a number of other European companies, as well as universities and research institutions.
Utilising recovered gas
A particularly significant innovation from Wärtsilä is its GasReformer – an efficient and flexible solution for utilising associated gas or VOCs recovered from oil production. With this solution, gases that were previously considered as waste can now be converted into a valuable source of energy. Together with the Wärtsilä dual-fuel (DF) engines, this is the most efficient and flexible solution for utilising gas or VOCs.
The main application area for this is in offshore oil and gas production. Here, the traditional way to get rid of associated gas or even recovered VOCs (volatile organic compounds) is either flaring, venting, or burning in boilers or gas turbines with high operational costs and low efficiency. The GasReformer has been developed and designed to meet the standards of the oil & gas industry and is the first of its kind in the world.
The GasReformer technology is based on steam reforming (SR), a catalytic process known from the petrochemical industry and refineries, where traditionally hydrogen is produced from various hydrocarbon feeds.
A milestone order
This year Wärtsilä received an order to supply Samsung Heavy Industries (SHI) on behalf of a collaboration between SK Shipping and Marubeni with its 6-cylinder 2-stroke dual-fuel engines. This is a milestone order for the marine sector as these will be the first large LNG carriers featuring Wärtsilä’s 2-stroke dual-fuel technology.
Wärtsilä has already supplied more than 150 ships with its 4-stroke, low pressure dual fuel engines. The 2-stroke development was introduced in November 2013. This engine technology combines efficient fuel consumption and low investment costs. The benefits already proven with the Wärtsilä 4-stroke dual fuel engines can now be applied to 2-stroke engines, which are widely popular in merchant vessels. Importantly, both the Wärtsilä 2-stroke and 4-stroke, low pressure dual-fuel engines are compliant with the IMO’s Tier III regulations
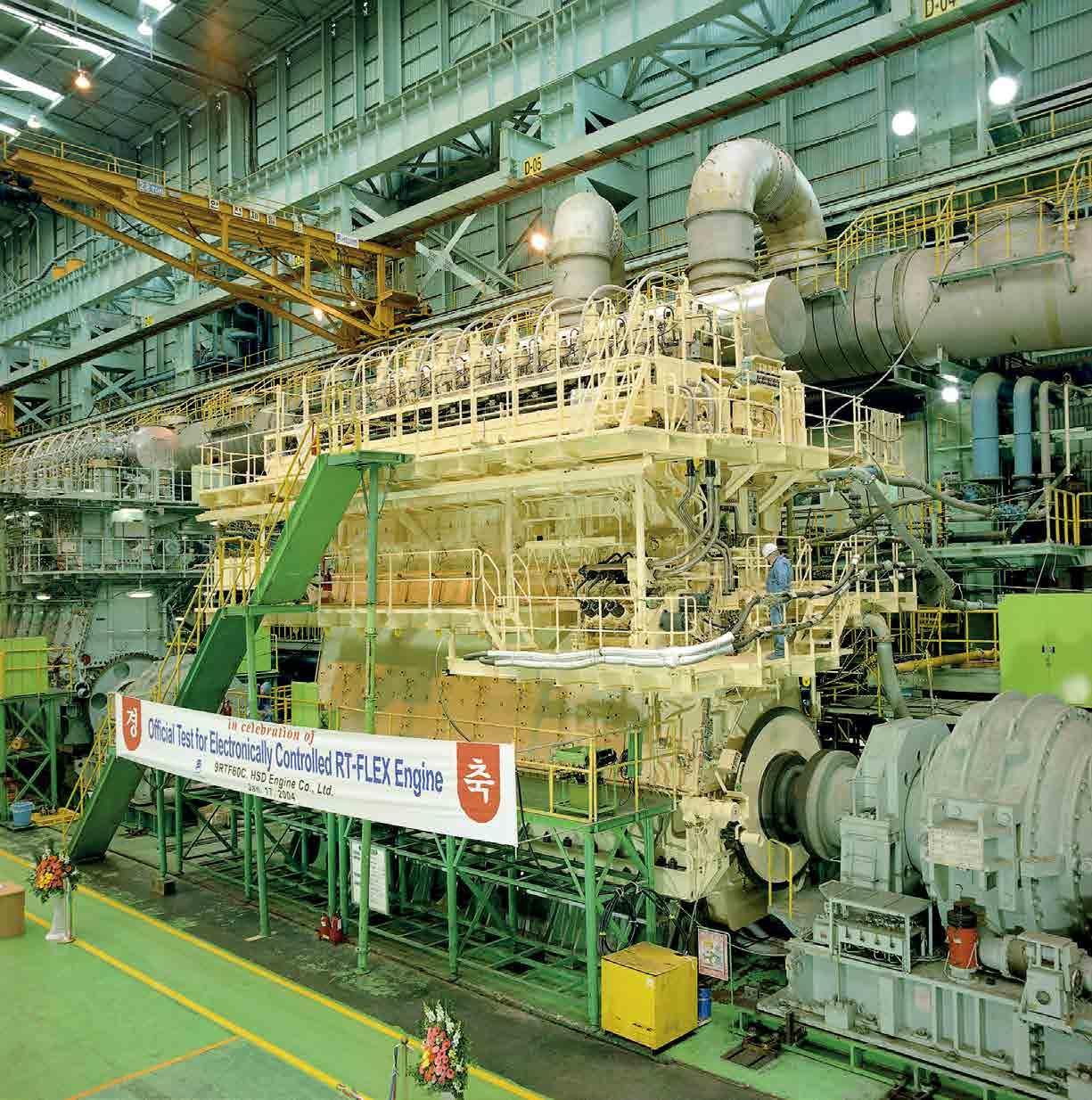
without need of secondary exhaust treatment systems.
The scope of supply for these ships includes two 6-cylinder Wärtsilä X62DF main engines per vessel together with the required electricity generator sets powered by Wärtsilä 34DF dual-fuel engines. The main engines will be built by a Korean licensee and the deliveries are scheduled for the first quarter in 2016. The first ship is due for delivery in the first quarter of 2017.
Major Aquarius order
The company’s recent slew of major orders from the Asian market continued when it won the biggest ever single owner order for Ballast Water Management Systems. A total of 22 bulk carriers, being built by Yangzhou Guoyu Shipbuilding Co. Ltd in China for Singapore-based Pioneer Marine will feature Wärtsilä’s Ballast Water Management Systems (BWMS). These systems will enable the vessels to comply fully with the IMO’s ballast water convention.
Each of the 38,000 DWT vessels will be fitted with two Wärtsilä Aquarius UV BWMS, and the scope of supply also includes the commissioning and sea trials of the equipment. The contracts thus involve a total of 44 Wärtsilä BWMS units, which represents the biggest ever single owner order to date for any BWMS manufacturer. It is expected that all 44 systems will be delivered before the end of 2015.
The Wärtsilä Aquarius UV is one of only four systems tested and approved for fresh water operation under the United States Coast Guard’s AMS (Alternative Manage-
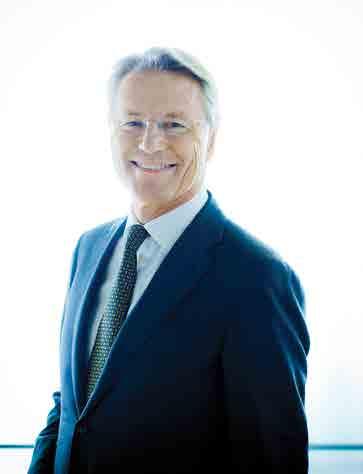
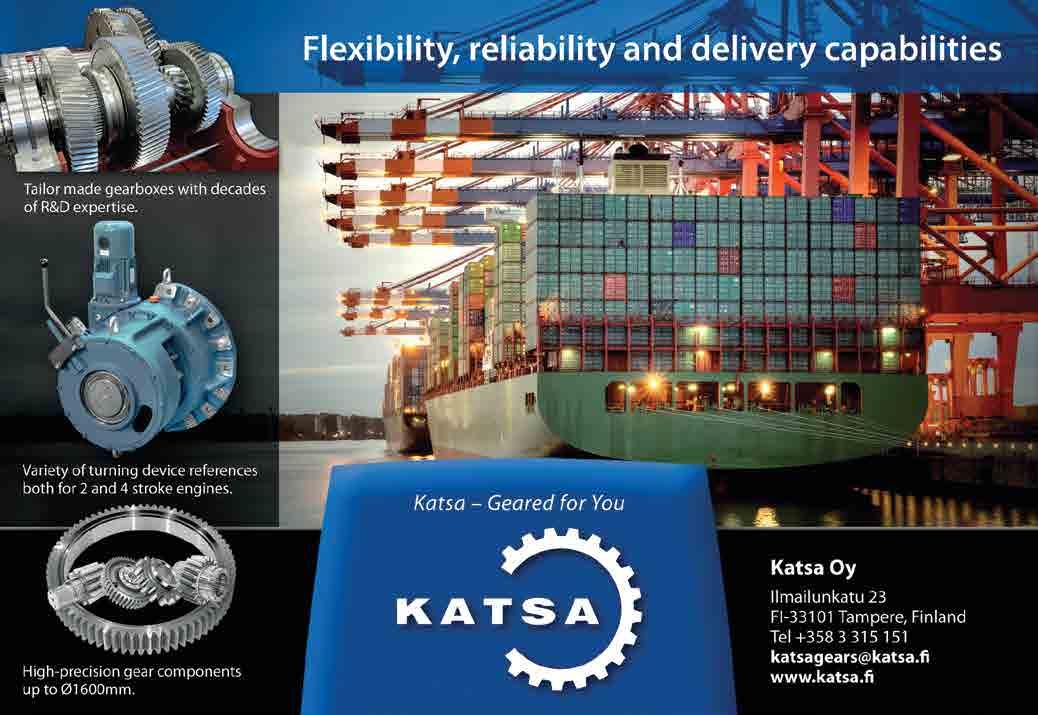
Katsa – Geared for You
Katsa Oy is a power transmission supplier. Over the years Katsa has become one of the leading supplier of high precision gear wheels, variety of turning devices and customized gearbox solutions.
Main customer segments of Katsa are marine & off-shore, vehicles & rail, mining & construction, pulp & paper, steel & metals, energy & wind and general machine building. Typically Katsa’s products are for demanding applications. Integrated engineering, manufacturing and assembly capabilities lead to flexible, cost efficient, reliable and on-time deliveries. Gearbox designs include cylindrical, planetary, conical and worm gear type of gear designs and their combinations. Katsa has references of high-speed gearboxes with several thousands of rpm, but on the other hand there is an extremely large install base of different turning devices with slow speed features. Operated power can vary from low to 3-7 MW depending of the operating speed. Current assembly capacity supports gearboxes up to 15000 kg.
www.katsa.fi/en
Dedicated products
At Federal-Mogul a huge team of large bore engine ring experts solely focuses on the special needs arising from large engine operation at sea, in power generation, rail and other heavy-duty applications. Between these main areas of use, Federal-Mogul covers 2-stroke and 4-stroke engines alike and modifies the rings for heavy fuel oil (HFO), gas or distillate fuel oil (diesel). Federal-Mogul piston rings for large bore engines have exceptionally good durability. In addition to a wide choice of ring materials, Federal-Mogul offers a large range of high performance coatings (e.g. CKS® Chromium Ceramic Coating, GDC® Chromium Diamond Coating, plasma coatings, etc.). By combining process know-how with the long background in ring materials and high performance coatings in many industry applications, Federal-Mogul has the clear advantage.
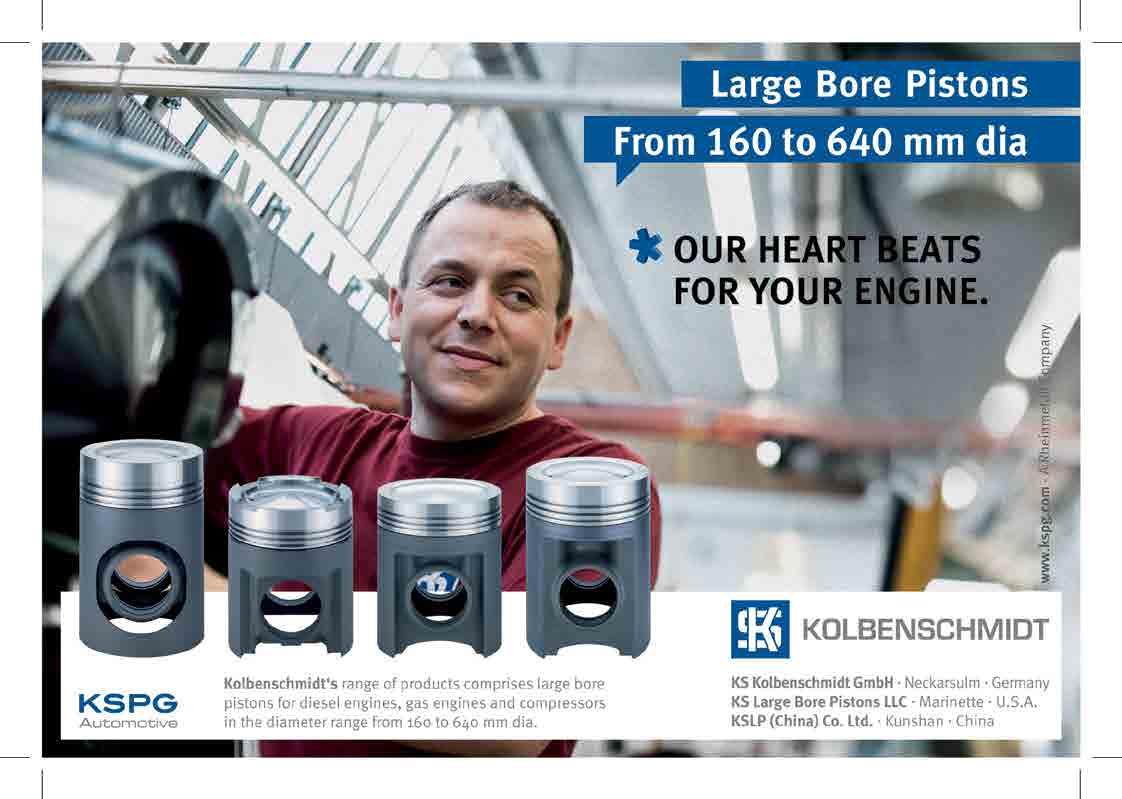
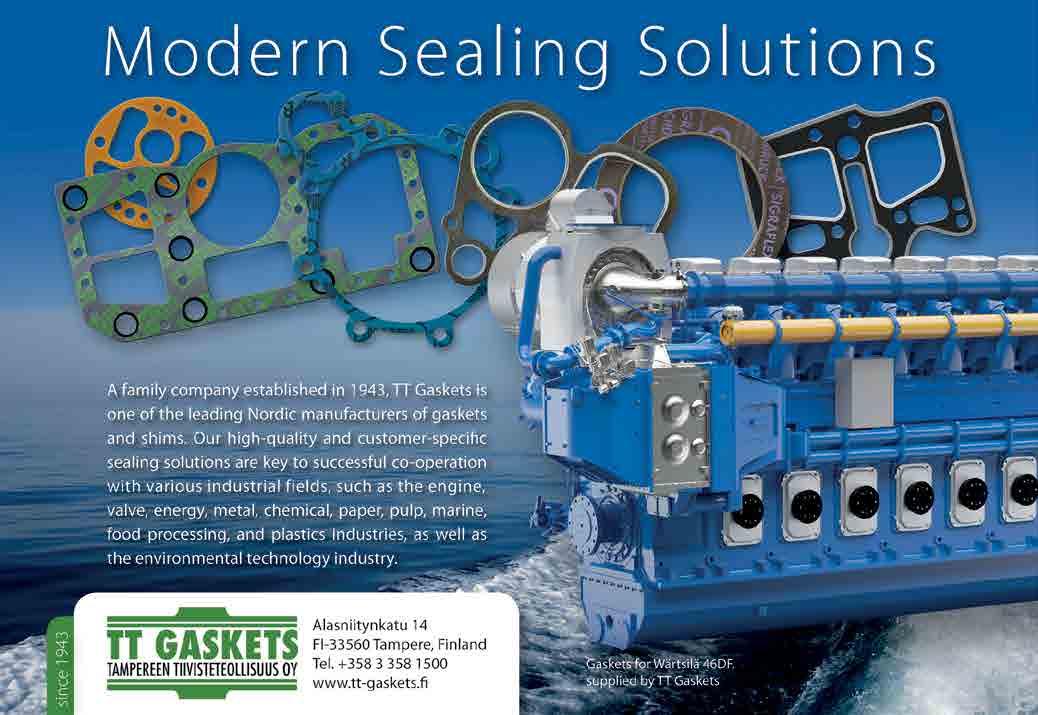
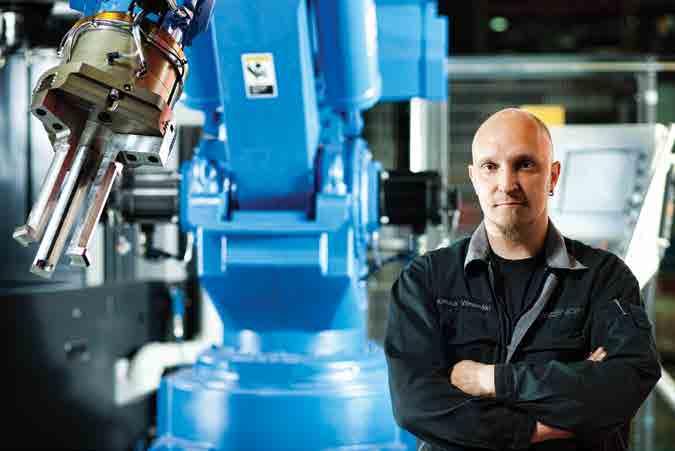
www.jmcengine.fi
JMC Engine Oy is a specialist provider of highly automated machining and system assembly services.
We take pride in delivering top-quality products to our customers on schedule. Our advanced production methods guarantee cost-effective manufacturing as well as business partner satisfaction.
We have developed into a strategic contract manufacturing partner of international operators, specialising in the manufacture of precisionmachined cast-iron parts and deliveries of readyto-assemble systems. For example, for engine manufacturers we are specialists for cylinder heads, guide blocks, injection tappets and valve tappets.
All-inclusive services
We serve our customers by effective management of the entire production chain, which includes the subcontractor network, acquisition of materials and services, production and manufacturing methods, and assembly services.
Partnership
Our business operations are based on long-term partnerships. Openness, a quality which is highly valued by our partners, is the best guarantee for business reliability. Because our partners can trust us to fulfil our obligations, they can concentrate on organising their own business operations.
Quality
JMC Engine Oy’s quality operations are based on a certified quality system according to the quality management standard ISO 9001:2008. JMC Engine Oy’s environmental operations are based on a certified environmental system according to the environmental management standard ISO 14001:2004. We recognise our environmental responsibilities!
ment System) criteria. This approval was cited as being an important factor in Pioneer Marine’s decision making process when selecting a BWMS supplier.
According to Dr Joe Thomas, director of Wärtsilä Ballast Water Management Systems: “This is an important order and is indicative of the growing need for ballast water discharging to be properly managed. These vessels will operate in and around US waters, and it was imperative that the selected BWMS have the appropriate approvals. Wärtsilä has a strong track record in this field, and the components used have been thoroughly tested in the marine environment for many years.”
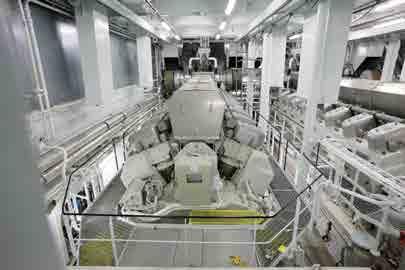
A first in bio-LNG
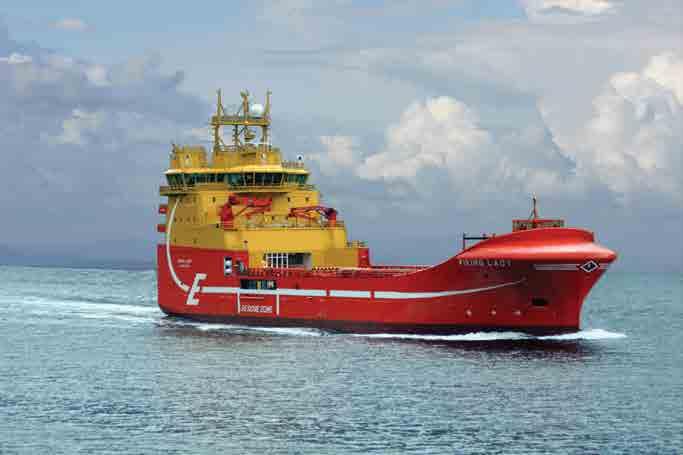
Another area in which Wärtsilä continues to prove itself a pioneer is LNG plants. The company has delivered plants with capacities ranging from 20,000 to 85,000 tons per year and has also developed solutions for capacities up to 1 million tons per year. At the other end of are Wärtsilä’s mini LNG plants that are particularly suitable for the liquefaction of biogas, and the production of LNG as a vehicle fuel.
An outstanding example of Wärtsilä’s expertise in this field is the Wärtsilä biogas liquefaction plant in Oslo, Norway. The plant converts household food waste into biomethane that is then used to fuel the local buses. The plant treats 50,000 tons of garbage per year, which produces enough fuel to run 135 buses. The environmental benefits are extremely significant with annual CO2 emissions being reduced by as much as 10,000 tons. Additionally, nitrogen oxides (NOx), noise levels, and particulate emissions are also considerably reduced.
In October this year, Wärtsilä signed a joint development agreement with two Indonesian partners with the aim of created the first ever bio-LNG plant in Indonesia. The co-signers of the agreement are PT Pertamina (Persero), a national energy company, and PT Godang Tua Jaya (GTJ), a waste utilisation sector specialist company.
“Renewable energy is an increasingly important global requirement, and we are proud to be involved in this landmark project. Wärtsilä has the experience and technological expertise in this area to turn solid waste into a valuable resource that can benefit the community,” said Mr Sanjay Verma, area sales dirctor, Wärtsilä Ship Power. n