
5 minute read
Working to be the best Fedegari Autoclavi
WORKING TO BE THE BEST
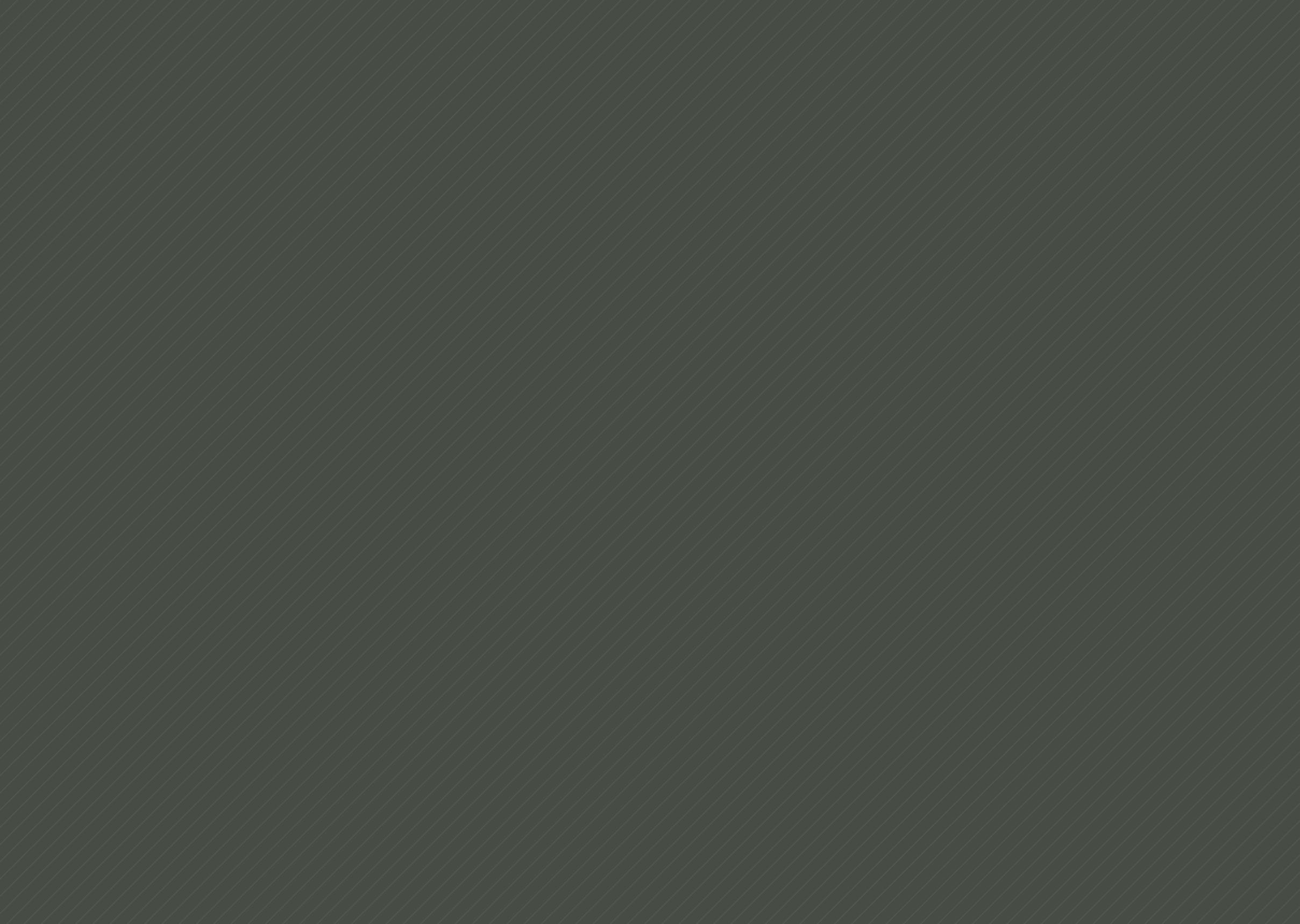
Fedegari Autoclavi SpA is an extremely successful company, with outstanding know-how in steriliser production technologies for the pharmaceutical industry. R&D plays a fundamental role in its success and the company has recently developed a number of highly innovative technologies and solutions. Barbara Rossi reports.
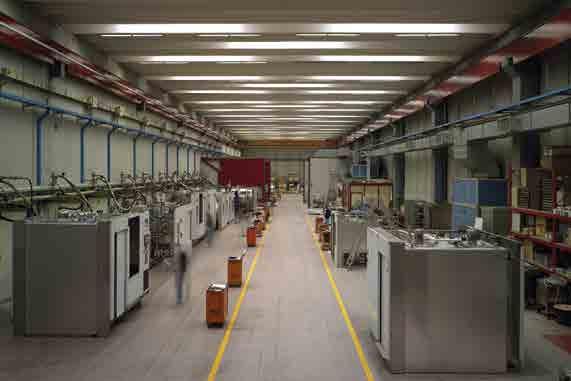
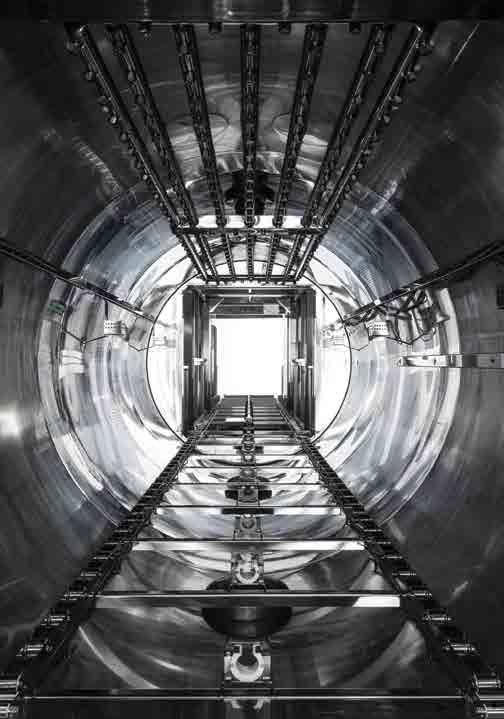
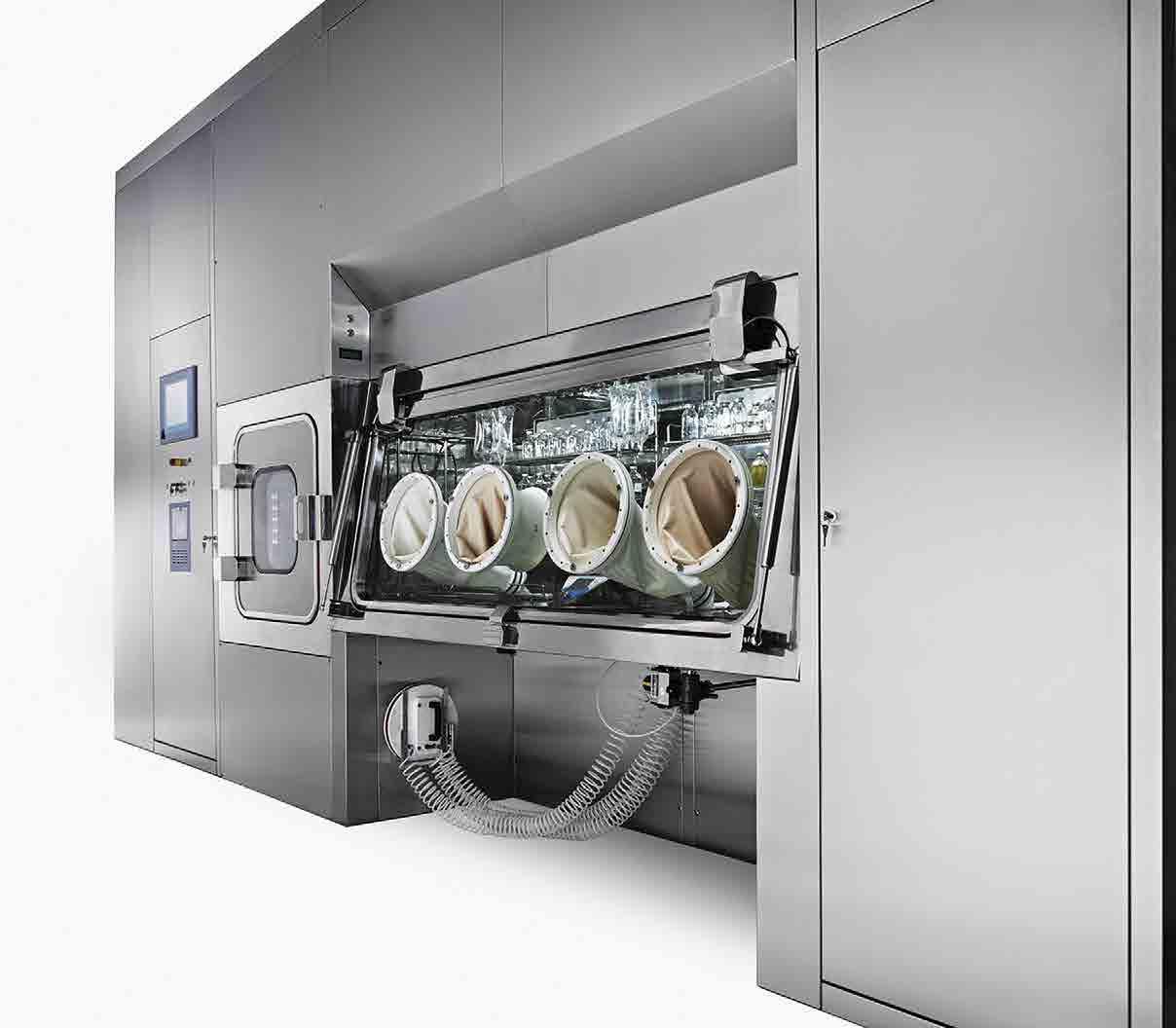
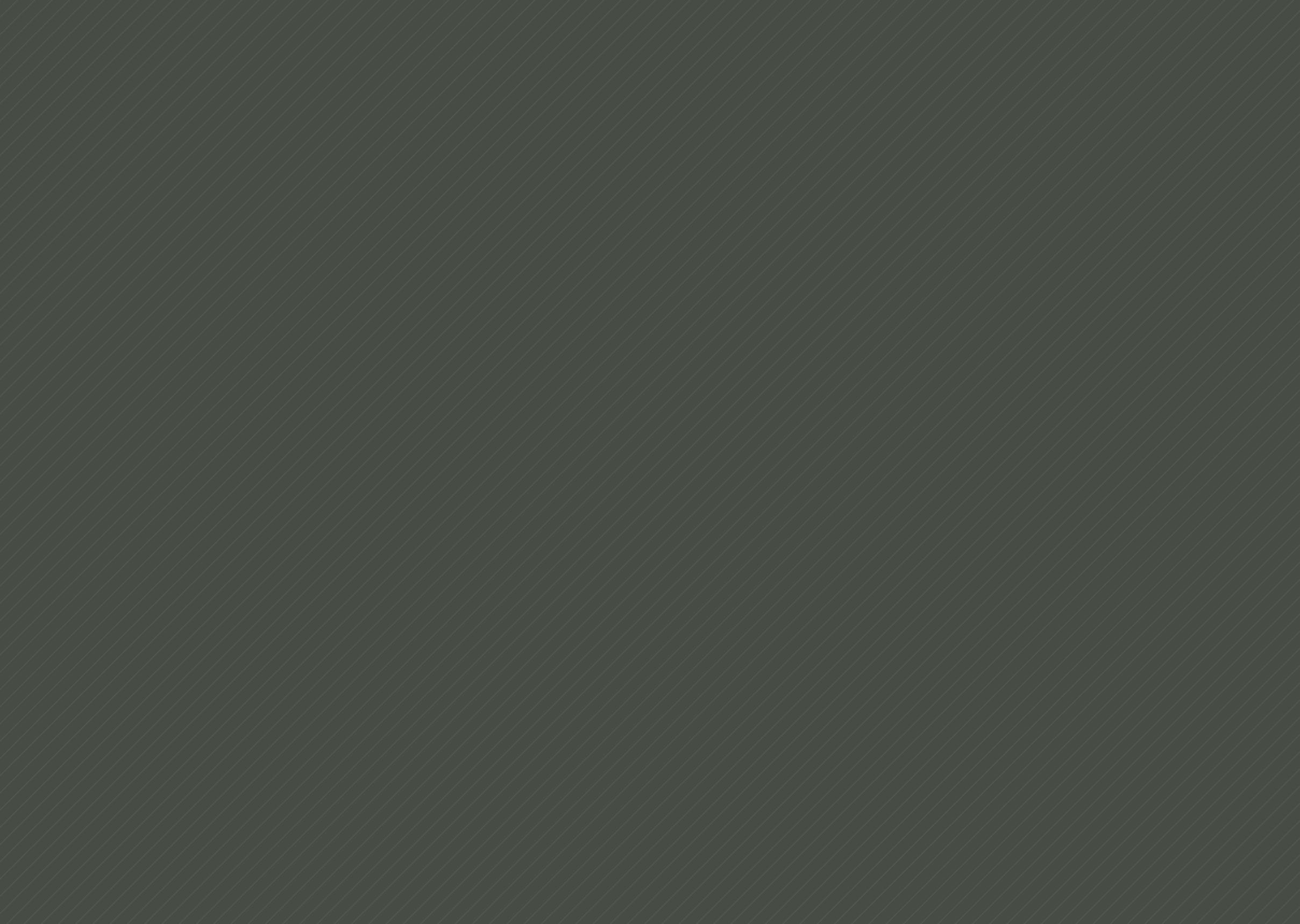
Fedegari is headquartered in Pavia, northern Italy, where it was established in 1953 by two brothers: Fortunato and Giampiero Fedegari. Over the years the company has grown into an international group with subsidiaries in Italy, Switzerland, Germany, the USA, Singapore and Russia. A real leader in the field of sterile and clean processes for the pharmaceutical sector, in recent years it has also begun to offer products and solutions to the food industry. Fedegari’s mission is to build the best sterilisers and decontamination solutions for its clients throughout the world. It is still managed by the founding Fedegari family, who maintain operational control of the whole group.
The range of products on offer includes machinery for moist and dry heat sterilisation, aseptic processing (decontamination and isolators) and washing (fows); as well as laboratory solutions (vertical and horizontal chamber sterilisers), components, accessories and pre-owned or refurbished equipment. Moreover, Fedgari’s Thema 4 process controller manages all the industrial machines manufactured by the company, guaranteeing total integration. It also supplies after-sales support, training, feasibility analysis and documentation services.
Production takes place in both Italy and Switzerland and all solutions can be customised to meet specific client needs. For the same reason, the work of the R&D department is fundamental to establishing and maintaining relationships with clients, particularly in the initial stage, when there is the need to establish how the machine or product itself needs to be processed. The R&D department also works closely with clients when they decide to launch new products or make changes in terms of packaging.
Focused on R&D
One of the projects recently developed by Fedegari has been a fully integrated solution for the food industry, specifically for the optimisation of the sterilisation process at one of the biggest European tuna can manufacturers. The challenge was to overcome temperature fluctuations and overheating, guaranteeing homogeneous heat distribution throughout. Furthermore, it included developing a fully integrated solution for treating different tuna can formats, increasing productivity and reducing operating costs. Fedegari has been supporting its customer with in-depth knowledge in sterilisation processes, developing a solution which allows it to increase its productivity at the end of every cycle and reduce the number of rejected cans to zero.
Another interesting innovation developed inhouse by Fedegari is its FTCS series of sterility test isolators. These products are equipped with a revolutionary built-in hydrogen peroxide (H2O2) vaporiser with control loop. The isolator offers different modularity options and can be integrated with a chemical bio-decontamination chamber (transfer hatch). The new
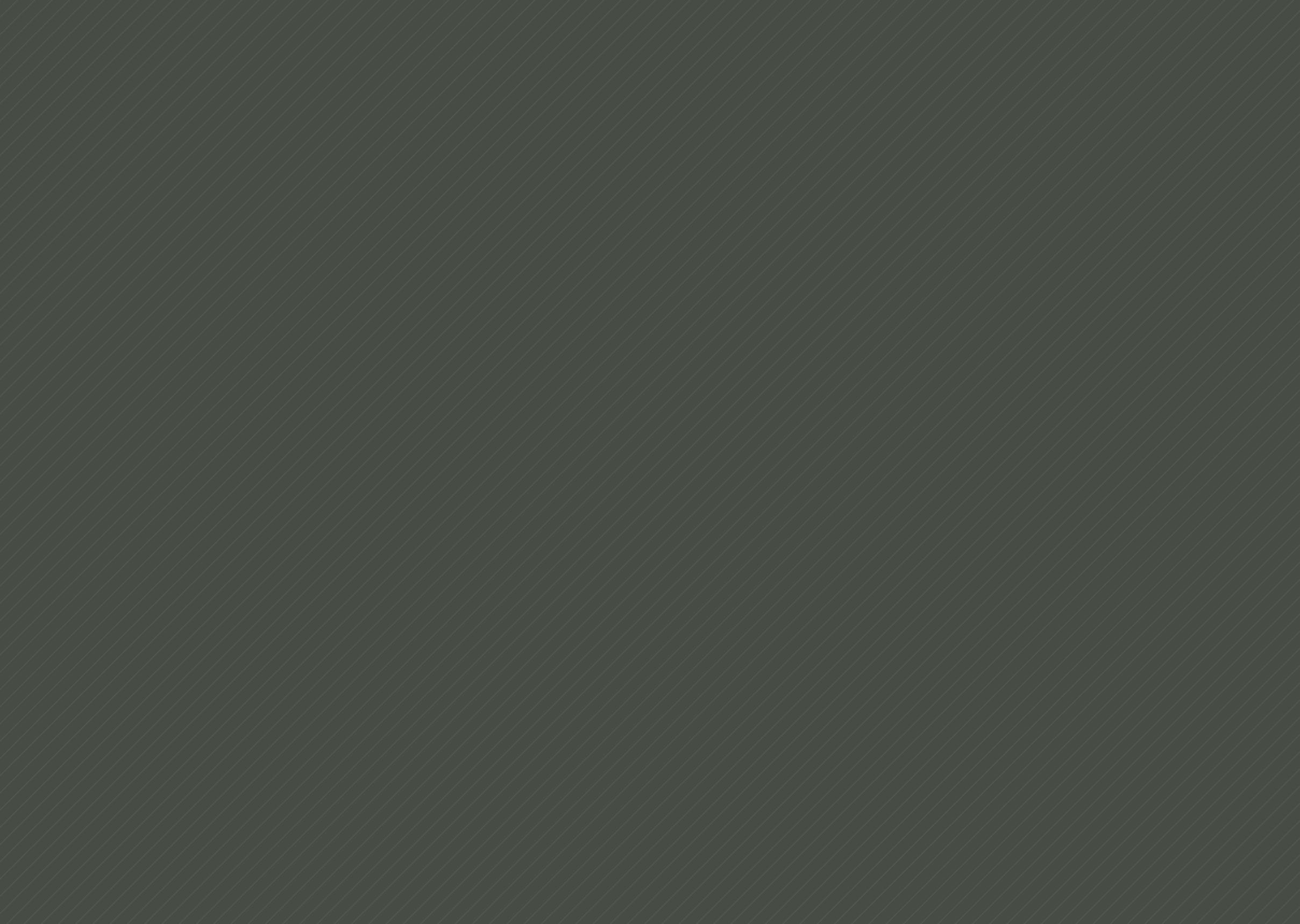

FCTS series is equipped with an innovative PID-based hydrogen peroxide vaporiser and gloves. Leak testing is managed entirely by a Thema4 process controller.
Fedegari is also active in innovation in biological indicator evaluator resistometer vessel technology. Information about the process resistance of the biological indicator and bioburden in sterilisation is essential to be able to understand aseptic process effectiveness. In fact, over- or under-estimating the resistance of either the indicator or the indigenous bioburden can lead to failed validation studies, potentially contaminated batches, sterility failure investigations, and other serious situations.
In addition to this, the Fedegari R&D department is actively working on emerging gloveless robotic technologies in aseptic manufacturing. Fedegari believes that there will be a growing trend towards this technology in the pharmaceutical and biotech manufacturing industries in the years to come. The
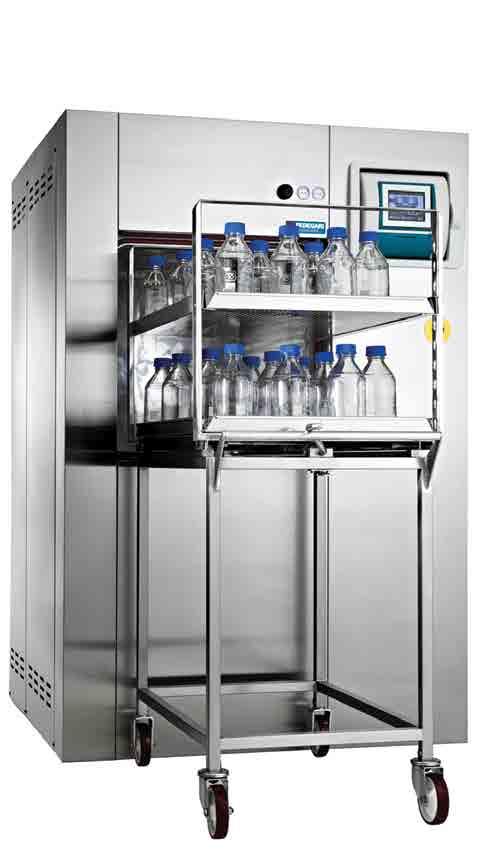
group is developing an advanced compact solution for the aseptic fill/finishing of cytotoxic drugs. The new equipment is a gloveless isolator in which all the operations are handled by a GMP-compliant stainless steel robot arm. This solution is chosen because an environment free of human presence is expected to be cleaner. Furthermore, considering how dangerous the handling of cytotoxic drugs is, a robotic solution increases process safety, as the operator is not directly involved in the manufacturing equation.
Moreover, the Fedegari Group is implementing advances in the field of robotised systems in general, offering integrated projects where various process machines interact with robotised handling systems for fully automatic high-throughput manufacturing lines.
Technical parameters
When it comes to research, Fedegari has also published a paper summarising the concept of FO and its related parameters, and explaining essential notions regarding sterilisation kinetics. The idea of physical and biological ‘equivalent time’ is also presented in this paper, which then discusses its application in the moist-heat sterilisation processes.
Linked to the same topic, Fedegari has produced an e-book on the F0 value, discussing its meaning, calculation and use in sterilisation processes. This e-book can be downloaded for free from the Fedegari website. The F0 algorithm was firstly introduced in 1968 in line with international food industry practices, and proposed by the FDA in 1976 for the pharmaceutical sterilisation of large volume parenterals. It is now officially included in most pharmacopoeias. Yet F0 is still regarded with some suspicion from a conceptual point of view and frequently misinterpreted. It is always necessary to remember that F0 was invented for the purposes of the heat sterilisation of products containing water. The purpose of these Fedegari technical notes, first distributed in 1988 and now revised, is to clarify the nature of FO and its related parameters (D, z, PNSU/SAL), and to explain their use and limits for the setting, adjustment, control and validation of moistheat sterilisation processes. n
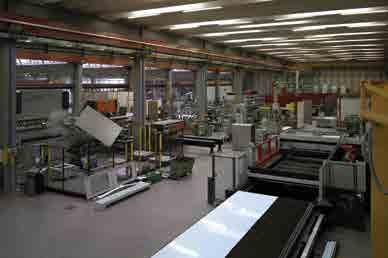
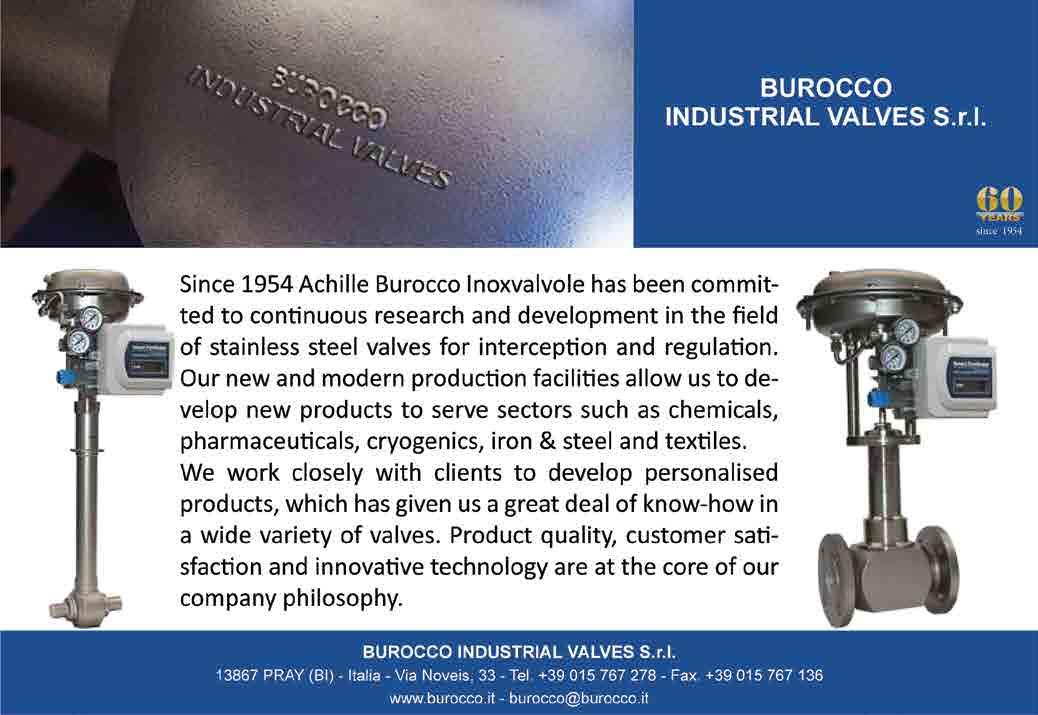
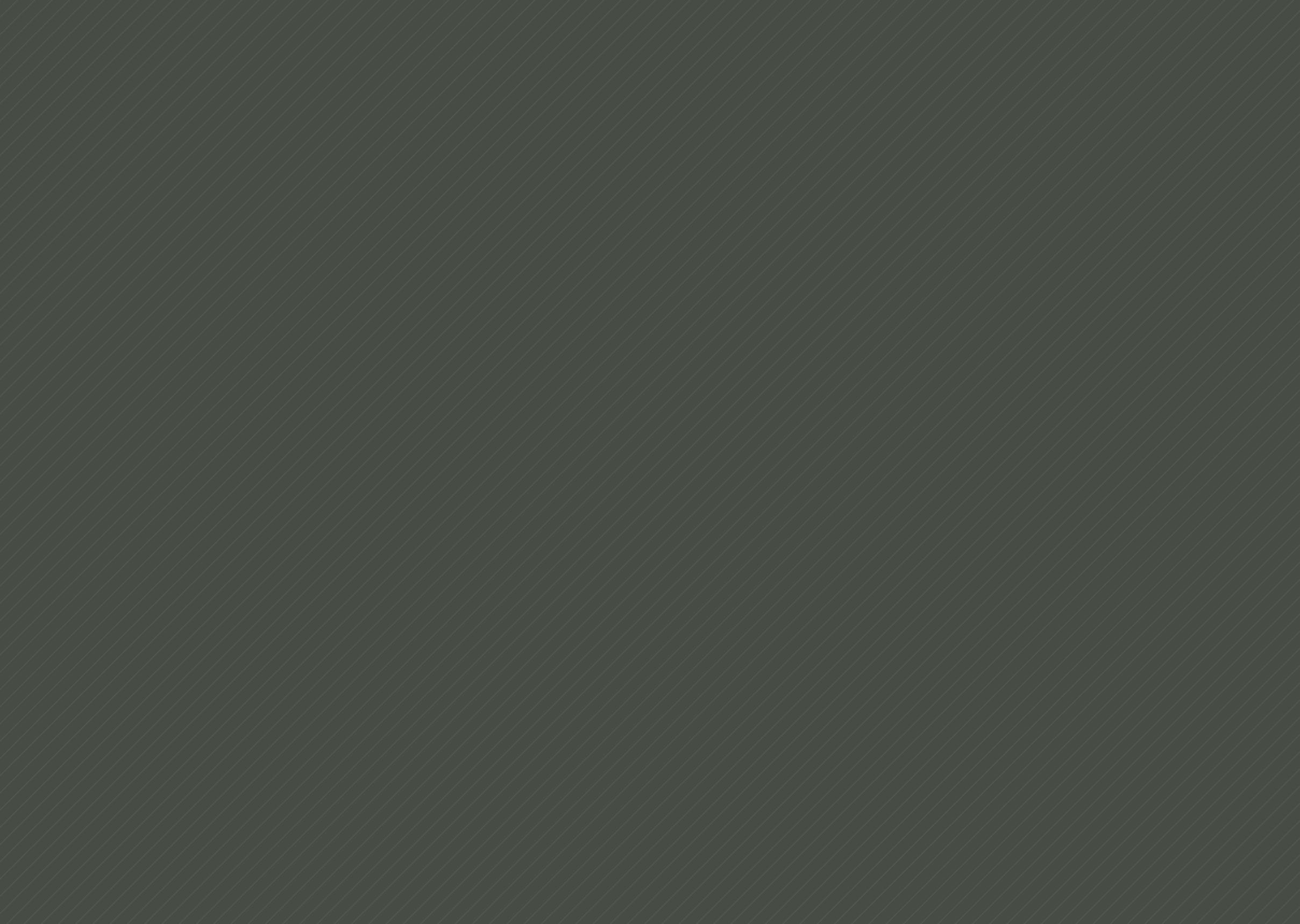