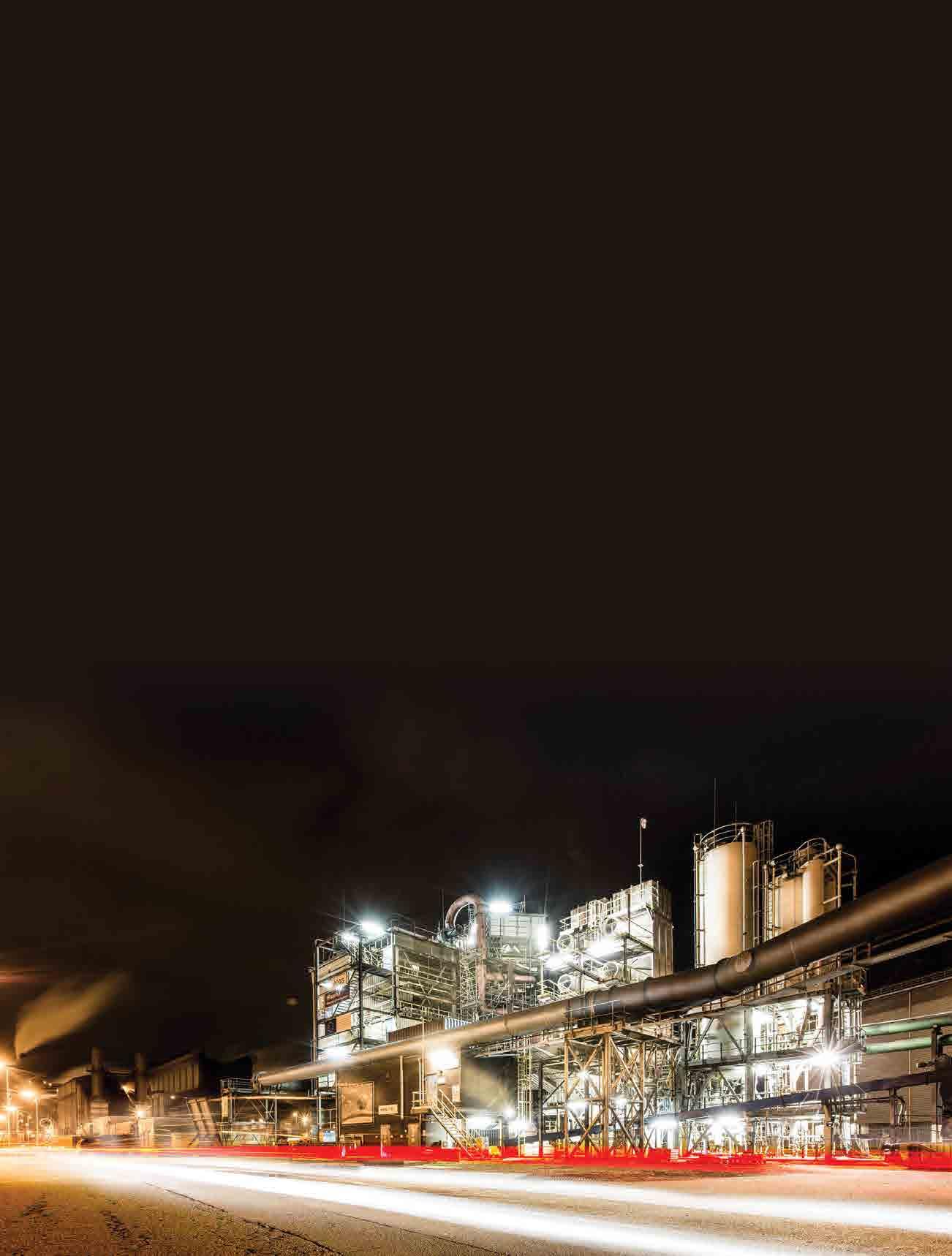
3 minute read
Revolutionary ironmaking process cuts both
REVOLUTIONARY IRONMAKING PROCESS CUTS BOTH CARBON AND COSTS
The HIsarna pilot plant at Tata Steel in IJmuiden uses groundbreaking technology to convert iron ore fines and coal almost directly into liquid iron.
The European Union has agreed to contribute €7.4 million towards testing a groundbreaking new iron production process being developed at Tata Steel’s IJmuiden steelworks in the Netherlands.
The six-month test campaign of the HIsarna pilot plant in 2016 will establish whether the new technology can produce molten iron in a stable way over a sustained period of time. The EU’s support represents nearly a third of the €25 million test costs next year.
If the technology is viable and can be scaled up successfully, it would enable further resource efficiency improvements in steelmaking – using the world’s limited resources in a more sustainable way while minimising impacts on the environment. Steel companies would be able to use a wider range of raw materials, including recycling materials, and the technology would lead to 20 per cent lower CO2 emissions. If successful, the HIsarna technology could deliver greater environmental and economic sustainability 10 to 15 years from now.
Karl Koehler, chief executive of Tata Steel’s European operations, said: “We welcome the European Union’s support for this promising and potentially groundbreaking project. The development of this technology still has a long way to go, so support from the EU is vital.”
The main advantage of HIsarna technology is that it eliminates two energy-intensive preparatory stages in iron making. There is no need to cluster fine iron ore into sinter or pellet or to convert coal into coke, as there is in conventional blast furnace iron making.
“The steel industry is an integral part of the circular economy, striving for zero waste, 100

Karl Koehler, chief executive of Tata Steel’s European operations
per cent recycling and the reuse of materials,” Mr Koehler added. “HIsarna could play a future role in the creation of a more sustainable low-carbon European economy.
“Tata Steel and its partners have continued to invest in this potentially breakthrough technology despite some very challenging economic conditions in Europe. But future phases of HIsarna’s development will require very substantial investment that will exceed what the project partners can provide themselves and indeed what current public innovation frameworks are likely to be able to fund.
“We need the European Union’s continued, long-term support for the HIsarna project. If next year’s tests are successful, the following stage would be developing, constructing and testing an industrial-scale plant at a cost of €300 million.”
Sustained production goal
HIsarna represents a new phase in the global direct smelting development cycle. It is, in essence, a merger between Tata Steel-delivered smelt cyclone technology and Hismelt (Rio Tinto) developed bath smelting technology.
The HIsarna plant was designed, constructed and put into operation by Tata Steel’s R&D and Engineering teams. The project was part of the international ULCOS (Ultra Low CO2 Steelmaking) programme, a joint initiative of the European steel industry. A former hot metal desulphurisation plant in IJmuiden was chosen for the pilot plant because of good rail connections and an existing baghouse with suitable capacity. The two-year project was supervised by a technical committee of ULCOS partners and Rio Tinto. In April 2011, the plant was pre-heated for the first tests, where 50 tonnes of liquid hot metal were poured into the furnace for a quick start-up. Sixty per cent of the injection capacity was achieved for a short period, and parameters such as cooling losses and gas composition were in the right range. Two more trials have now been scheduled
Next year’s test campaign is the fifth series of tests since the pilot plant was built in 2010. Tata Steel and its project partners aim to prove the facility can produce liquid iron for sustained periods. The previous four campaigns each lasted about two months, during which iron was produced for a maximum of three days.
Another key objective is to establish HIsarna’s potential CO2 savings. There will also be tests using various types of raw materials, scrap and by-products from the steelmaking process.
The EU’s support is part of its Horizon 2020 SILC-II programme. If HIsarna becomes commercially available on an industrial scale, steel producers could lower manufacturing costs, reduce energy consumption and CO2 emissions and take resource efficiency to the next level. An additional advantage is that HIsarna reduces the emissions of fine particle dust and dioxins, as well as nitrogen and sulphur oxides.
HIsarna is a Tata Steel and Rio Tinto initiative, with close cooperation from European steel producers ArcelorMittal, ThyssenKrupp and Voestalpine and technology supplier Paul Würth. n
www.tatasteeleurope.com
