
3 minute read
Technology spotlight Advances in technology
NEWS
TECHNOLOGYSPOTLIGHT
Advances in technology across industry
Morgan and D3O create world’s most advanced helmet for defence sector
Morgan Advanced Materials, a world leader in the application of advanced composite material technology, has incorporated the D3O TRUST high-performance padding system into its ultra-lightweight combat helmet portfolio, the LASA AC914 and LASA AC915. The combination of Morgan’s hybrid composite ballistic helmet shell technology, with D3O’s impact pads, is believed to be the most advanced combat helmet in the global market.
The D3O TRUST helmet liner system, created by the experts in real-world impact protection solutions, is engineered using patented composite materials. The seven-piece system, which exceeds required Advanced Combat Helmet (ACH) protection levels by 33% at 10ft/sec, has now been used by Morgan to complement its world leading ballistic helmet shell technology.
Morgan’s LASA AC914 and LASA AC915 ballistic helmets are manufactured using proprietary ultra-lightweight, composite hybrid technology, which provides structure, durability and a level of protection at weights significantly lower than previously available. The helmets are the outcome of over three years of materials and product development at Morgan’s Ballistics Centre of Excellence.
Duncan Eldridge, president of Morgan Advanced Materials – Composites and Defence Systems, explains: “Morgan has been at the forefront of ballistic protective combat helmet design for more than 30 years and we are proud to partner with D3O in the creation of our most advanced combat helmet yet.” Visit: www.morgandefencesystems.com British Steel, the UK-based manufacturer of premium steel products, has launched a revolutionary new rail product which can withstand the rigours of being laid in some of the most corrosive of environments.
The new product, Zinoco®, is a premium coated rail that can be installed in harsh environments where corrosion is expected to be the main cause of future rail replacement such as coastal lines, wet tunnels, level crossings, mineral lines and salt pans.
Contracts have already been secured across the UK, Ireland and France. British Steel’s Rail Sector Head, Richard Bell, said the product was developed at the business’s headquarters in Scunthorpe and that extensive testing shows Zinoco® will typically outlast traditional uncoated rail by around five times in a broad range of aggressive environments.
Richard said: “This is an exciting time for British Steel and Zinoco® is a great example of our innovation and development of premium products for the global market place. Our highly-skilled employees create and manufacture world class steel every day and we are proud of the response Zinoco® has already received.” Visit: www.britishsteel.co.uk
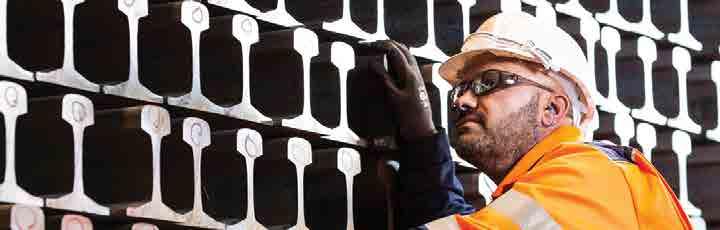
Developing 48V through-theroad hybrid vehicle technology
Controlled Power Technologies, a developer of vehicle driveline electrification based on state-ofthe-art switched-reluctance machines (SRMs), has partnered with Ricardo, Tata Motors European Technical Centre (TMETC) and Provector to apply its low voltage electric motor technology to the rear driveline of a B-segment city car.
The consortium has secured a funding award from Innovate UK, the UK’s innovation agency, who will contribute £1.8 million of the total £3.4 million investment. The investment will help to further introduce advanced mild hybrid functionality to mainstream vehicles at significantly reduced cost to that of high voltage plug-in hybrid or pure electric vehicles (EVs). The innovative electrified rear axle technology will be an important step in enabling OEMs to further improve both regulated and real world fuel economy in modern urban city driving conditions.
CPT will lead the project and will be responsible for developing the electric motor and control system, and will support their integration into the rear axle module. Provector has extensive experience in the control and management of advanced lead-carbon battery chemistry through projects such as ADEPT and its involvement with the Advanced Lead Acid Battery Consortium. Ricardo’s key responsibilities within the project will be the design and analysis of the integrated 48V rear axle module, development of the supervisory vehicle control system, sub-system testing and project management support, building on its previous work on the ADEPT and ULTRAN projects. TMETC will supply the base vehicles, develop the suspension solution, and provide support for the application of the technology and overall vehicle integration and testing. Visit: www.cpowert.com