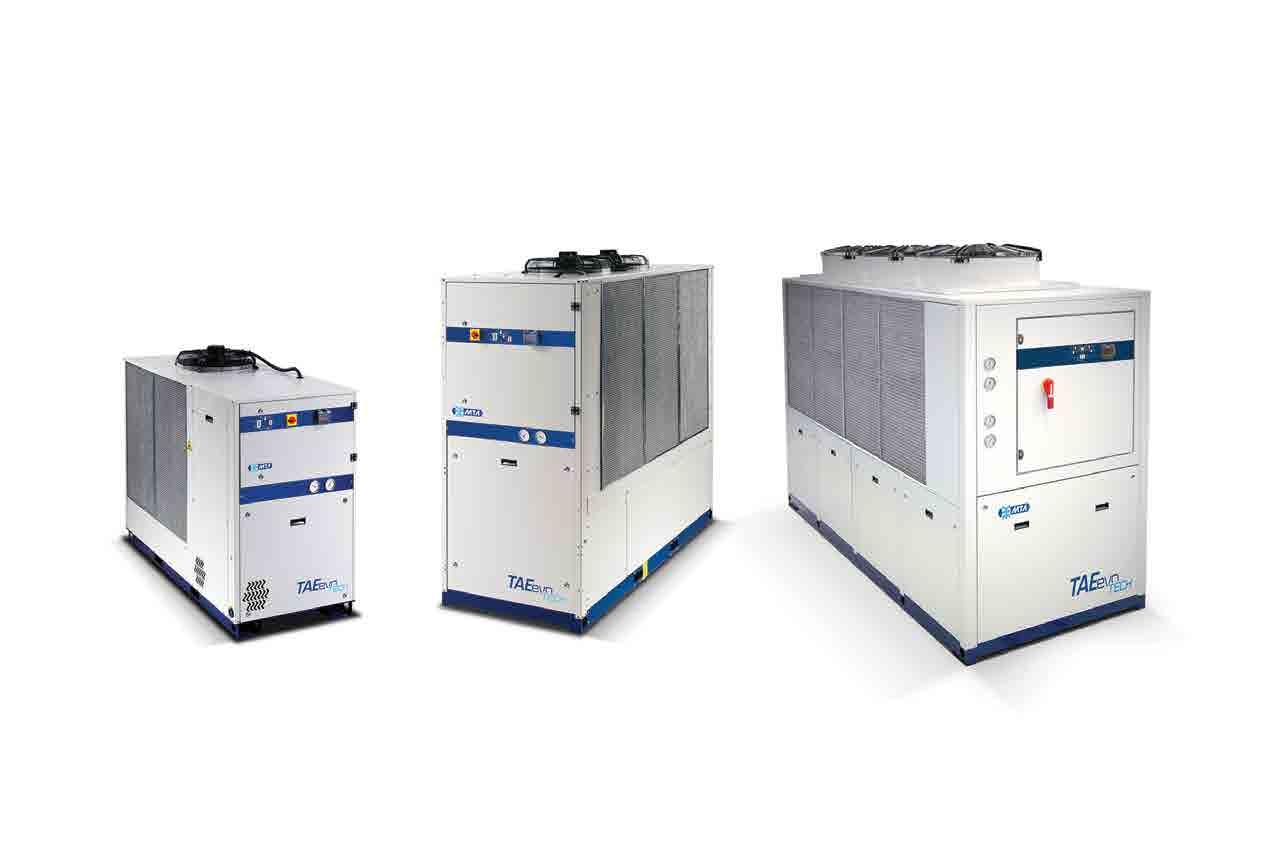
6 minute read
Fast, versatile and energy efficient MTA
FAST, VERSATILE AND ENERGY EFFICIENT
Established more than 30 years ago, Italian company manufactures industrial cooling and compressed air & gas treatment machines, as well as air conditioning equipment. While maintaining strong links to its roots, MTA operates on a global scale as Barbara Rossi finds out from Marco Motton, Operations director, and Enrico Callegarin, Compressed Air Products and Process Cooling marketing manager.
TAEevo Tech, air-cooled industrial chillers
MTA stands for ‘Macchine Trattamento Aria’ (literally ‘Air Treatment Machines’). The company was set up in the Padua area of northeastern Italy in 1982 by four partners, all of whom came from an air treatment background. MTA quickly launched its first product, an innovative thermal mass dryer, thanks to which it became renowned at global level. Another milestone was reached in 1989 when the company impressed the compressed air & gas treatment market with a new environmentally-friendly silica sand thermal mass dryer.
Following this, thanks to the success of its own refrigeration air dryers (of which it still produces between 6000 and 7000 a year), in 1991 MTA entered the process cooling market with TAE, an industrial liquid chiller. TAE was equipped with a tank containing an innovative water heat exchanger, suitable for a wide range of applications. Since then, the company has developed different models of TAE, of which it currently supplies about 6000 units a year. Innovation is key
Today MTA, with its 440 employees and 50 product lines, offers a comprehensive product range spread across three main areas: process cooling; compressed air & gas treatment; and air conditioning. The process cooling range, including water cooled chillers and water cooled heat pumps from 1 kW to 1900 kW, offers an extremely high level of product reliability. When it comes to compressed air & gas treatment products, what differentiates the company from competitors is the wide range of solutions on offer, product performance and energy saving. “We do not simply offer energy-saving dryers, like some of our competitors. We go a step further. Energy saving is part of our DNA, as proven by our refrigeration air dryers able to process from 0.3 to 760m3/min. Their energy saving features have gained widespread market recognition,” said Mr Motton.

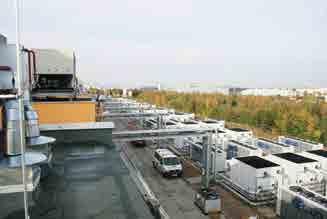
A series of chillers and dry coolers MTA installed in a large industrial manufacturing plant in Germany Headquarters and production facility in Conselve, Padua

Two new Lean assembly lines for Cygnus Tech and TAEevo Tech ranges Rooftop installation of Aries Tech units in Germany
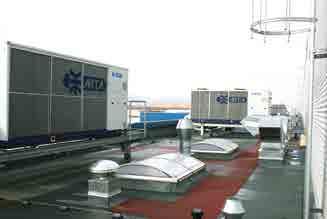
“The drive towards the development of new products to meet customers’ specific needs is our main priority. We carry out continuous R&D and a team of specialists follows each phase of development, from the initial needs analysis to product design and manufacturing. We have a highly qualified technical department and in our sector a high level of technical expertise is what makes the difference. Our latest products are the new energy saving DE ETM thermal mass dryer and the high efficiency industrial application heat pump HAEevo TECH,” added Mr Callegarin. “DE ETM could be defined as the joining link between a dryer and process cooling, while HAEevo TECH is an industrial heat pump offering the energy efficiency required by the air conditioning market.”
Mr Motton added, “As well as carrying out R&D internally, for special projects we collaborate with the university of Padua. In addition to this, we have co-engineering projects with some of our highly selected suppliers, especially when it comes to heat exchangers and machine control management. We work with highly reputable international suppliers, 40 of which supply us with 80 per cent of what we purchase.”
Market outreach
MTA operates from three sites (Conselve, Bagnoli and Tribano) all based in the Padua area, occupying a total area of 58,000m² (26,000m2 of which are taken up by covered facilities). It has a production capacity of 20,000 products a year and a yearly turnover of more than €75 million, 80 per cent of which derives from exports.
Bagnoli is dedicated to the production of tanks, while Conselve, the main site, hosts assembly facilities, alongside the technical office, R&D and procurement. It is where all the machines ranging from 15kW to 1900kW are produced and assembled. Meanwhile Tribano, which was previously focused solely on logistics, was trans-

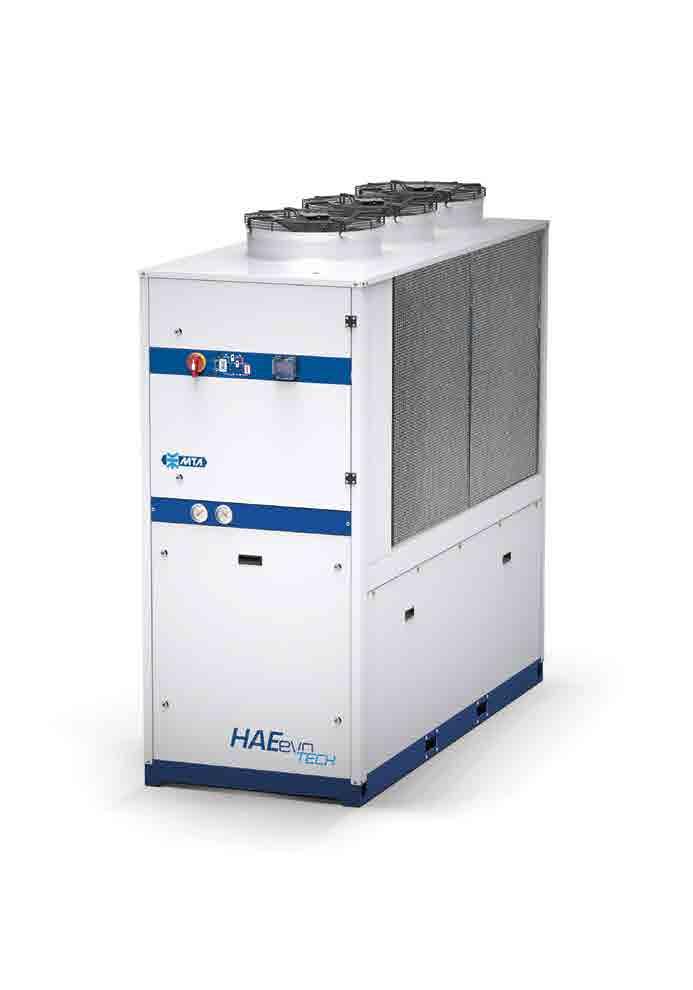

HAEevo Tech, high efficiency air-cooled reversible heat pumps formed into a production site a year ago and is now responsible for the manufacturing of the smaller TAE and dryer models.
Through its network of representatives, MTA is commercially active in more than 80 countries worldwide, as well as having direct branches in various countries (Germany, France, Spain, Romania, the USA and Australia). In this way it ensures an excellent geographical coverage for all of its customers.
Ready for further growth
“The founding partners are very involved in the company; in fact we could say it is a family company. Three years ago they decided to appoint a technical director in order to be ready for further growth. Our internal organisation and assembly lines were revolutionised, thanks to a €3 million investment in production and organisation. Lead times have been reduced and are clearly stated. We have implemented a KANBAN production system, in which some of our suppliers have been integrated, which has allowed us to increase our flexibility in responding to customer demand.”
The company’s very detailed business plan for the next three years includes a 15 per cent annual growth rate. This will be entirely of an organic nature and the current facilities will be perfectly able to accommodate it. The commercial reorganisation undertaken recently was implemented in preparation for this and further changes are taking place.
MTA plans to further strengthen its position in its main markets – namely Europe, Russia and the USA. In addition to this,
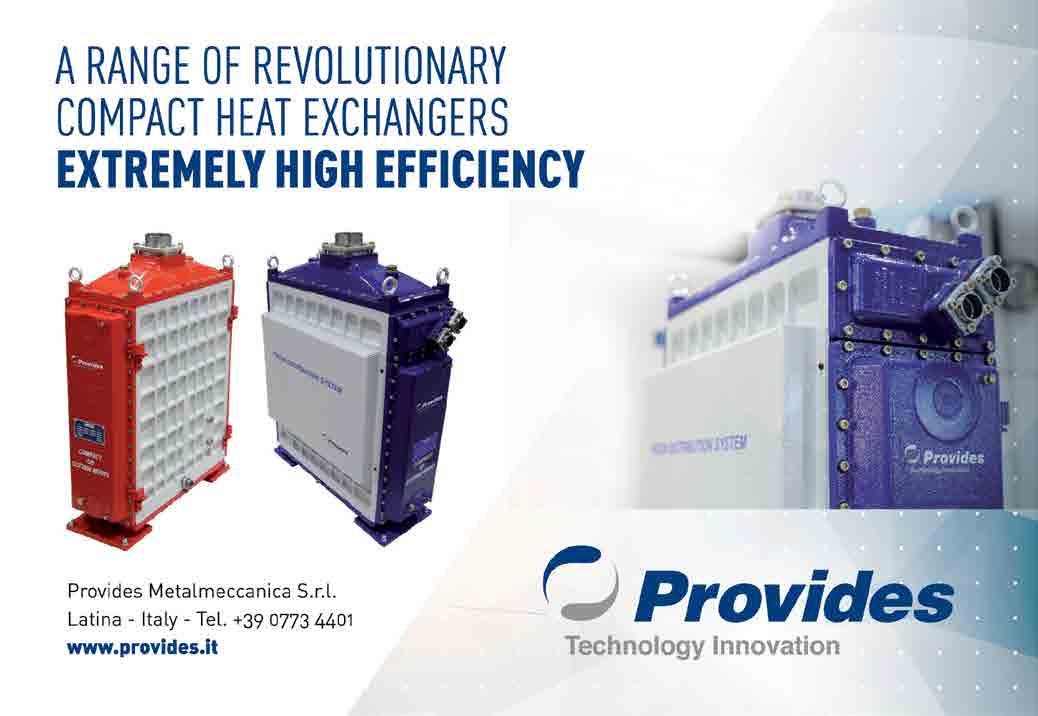
it intends to establish its commercial presence in regions where sales are currently limited, including Africa, Asia, the Middle East and Latin America.
Mr Callegarin commented, “We have a very wide range of applications, such as plastics, packaging, automotive, wine-making, chemical,s pharmaceuticals and many more. This is a true strength, differentiating us from our competitors. We have a vast know-how at our disposal and a global vision. We are working on many important projects at the moment, developing both existing and new products. We want to be able to offer a comprehensive range, covering a wider spectrum of market levels.”
He concluded: “Our lead times have decreased by over 90 per cent and some of our suppliers have been further integrated into our processes thanks to the IUNGO software systems, which allows them to receive orders in real time. We do this because we want to offer quick and reliable deliveries. We have a chart stating delivery times for all our products according to the chosen configuration. We offer prompt deliveries for all our standard products and very quick and reliable deliveries for customised solutions. Our suppliers are carefully selected in terms of both technical and organisational quality in order to help us achieve reliability, quality, flexibility and customer satisfaction. They are an integral part of our growth and success.” n
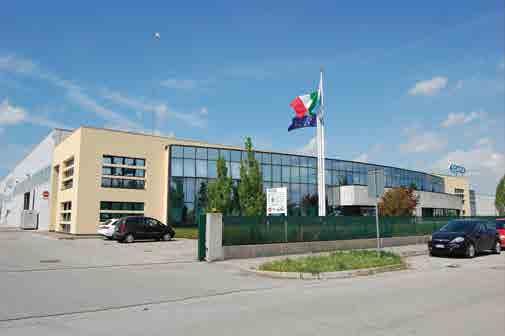
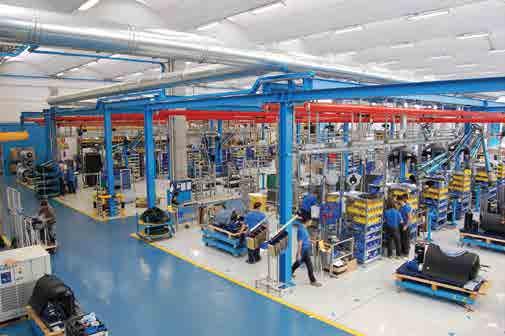