
7 minute read
A future proof material Hydro
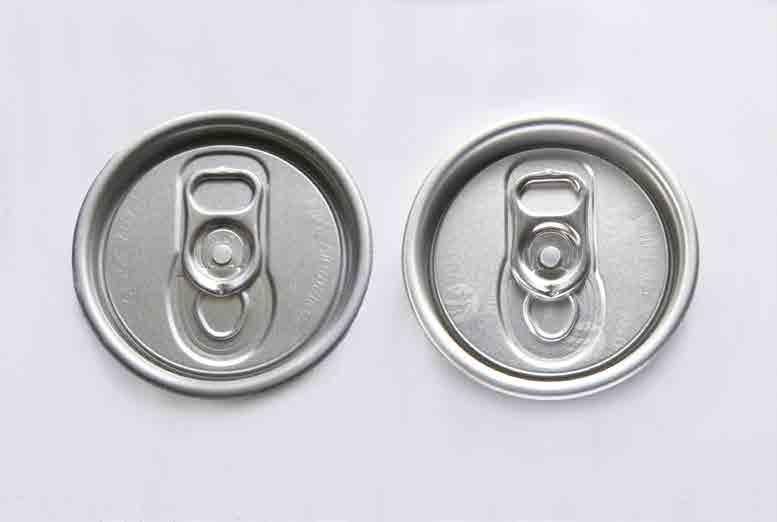
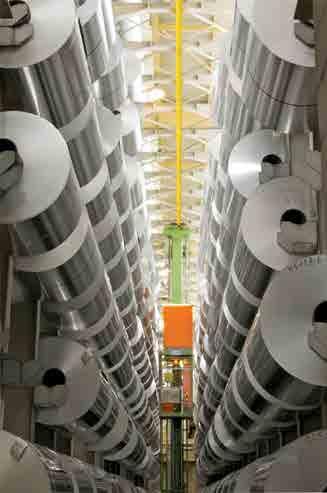

A FUTURE PROOF MATERIAL
As a global aluminium company, Hydro’s production, sales and trading activities stretch throughout the value chain, from bauxite, alumina and energy generation to the production of primary aluminium and rolled products as well as recycling. Elisabeth Skoda spoke to Hydro’s communication manager Michael Peter Steffen to find out more about the company’s vast product range and recent innovations in the packaging industry.
IN total, the Norway-based company has 13,000 employees involved in activities in more than 50 countries on all continents. In 2015, a turnover of NOK 87 billion was achieved.
Hydro has changed and developed a lot over the 110 years from its roots as a manufacturer of nitrogen-based fertilisers, evolving into an international industrial conglomerate. Since 2007, Hydro is a focused global, integrated aluminium and hydroelectric power company.
Packaging prowess
“Our constant strive to become better, bigger and greener is benefiting all our stakeholders, ultimately everyone´s lives, everyday. Think of your smart phone; of your mobility; of the packaging that protects your food … and Hydro is a leading provider of aluminium-based solutions, also for the packaging industry,” Mr Steffen explains.
“Since 2002 we have been able to maintain and even strengthen our leading position in the packaging industry, notably in the market segments of ultrathin high performance foil for aseptic packaging, mainly used in compound cartons such as tetra packs.”
Mr Steffen is keen to highlight a key innovation in this area. “We managed to reduce the thickness of our foil for sterilised beverage cartons by 16 per cent, allowing us to stretch the boundaries and reduce the industry standard of 6 micron to an impressive 5 micron. This innovative high-quality foil is manufactured with even less material than before, but still ensures barrier protection of foodstuff against spoilage.”
This foil is manufactured at the rolling mill in Grevenbroich in Germany, the largest and most technically advanced production site in the world for high strength foil.
Hydro’s aluminium packaging range consists not just of foil, but the company also is a leading supplier for can stock, tab and body stock, i.e. all the material needed for aluminium beverage cans. Packaging is of major importance both for companies and typical home users of today and tomorrow.
Aluminium in packaging is on the up, and Mr Steffen sees good potential going forward. “Lifestyle changes have created an increased demand for ready meals, and aluminium trays are convenient. It is also an attractive packaging format at the point of sale. Aluminium is an ideal packaging materials, and products such as aluminium household foil are playing a crucial role in the storage of food remains. As long as consumers take note of advice to not store very sour or salty foods in it for any length of time, it is a useful and safe material. Aluminium foil routinely scores as good or better than other food storage methods such as plastic compounds or plastic boxes with regards to their carbon footprint.”
Another growing use for aluminium packaging is in the area of wine closures, not just for everyday wines, but also premium wines.
“Wine can be destroyed by cork effect. About 3 per cent of all the annual wine harvest is spoilt due to a corked bottle, and of course this doesn’t happen with aluminium closures. In addition, there is the convenience of being able to open and reclose the wine as often as is wished. With our rolling mills, we have a European wide network with a strong base in Germany and Norway. Our rolling mill in Holmestrand works as a major supplier of food can material,” Mr Steffen adds.
Water power
Hydro is proud of its long history. In 2015, the company celebrated its Høyanger aluminium plant’s 100th anniversary, the oldest still active smelter which has been available and in service all the time, and which is still a major plant, powered by water from Norwegian waterfalls. Today, Høyanger also works with recycled metals.
“One major USP for Hydro, distinguishing us from other aluminium producers, is that the majority of our aluminium production is based on hydro power,” Mr Steffen points out.
Hydro runs several hydroelectric power plants in Norway, harnessing the power of Norwegian waterfalls, making it the second largest private producer of hydroelectric power in the country.
The company is proud to hold a leading market position across the entire value chain of the aluminium industry, from mining to refining and processing it into a range of products, and values its sound process chain and secure raw material base.
“This reflects the depth of competence in this material. Thanks to our R&D, laboratories and detailed material analysis, we are on top of any industry developments.” As the boldest step going forward, Hydro will build a 70,000-tonnes-per-year test plant for the world´s most efficient primary aluminium production.
A varied range
Hydro´s aluminium solutions help make cars lighter and safer; turn buildings into more efficient homes and work places; open up for progress in electronics and renewable energy technologies – and help protect food, medicine or other valuables to preserve their usability and nutritional benefits, freshness and taste..
Mr Steffen sees the biggest future potential in the automotive industry. “The use of aluminium in cars has been booming. This development started in the USA with the Ford F150, and we have observed similar trends in Germany and all over Europe. To cater for this trend, we are investing € 130 million into a finishing plant for car body sheet in Grevenbroich, Germany, an application with demanding requirements on purity, surface looks and formability. With recent developments on alloys we have been able to serve the industry very well and are looking forward to be able to quadruple capacities with our investment into a new finishing line by the end of 2016. This line will be the most energy efficient processing line in this field.”
Another use for aluminium Mr Steffen is keen to highlight is the printing industry. “Aluminium is the base for a chemical layer in many
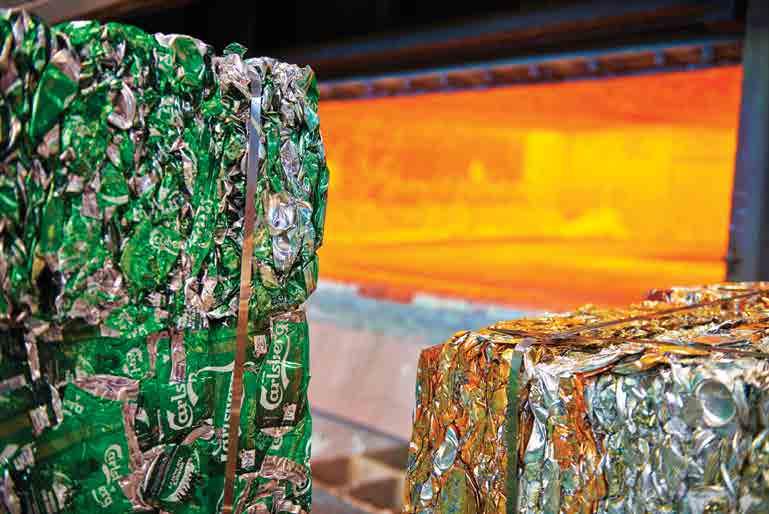
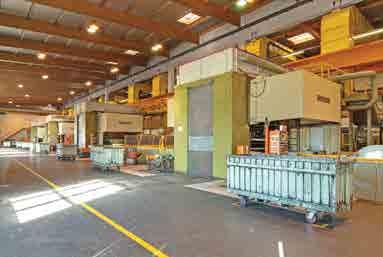
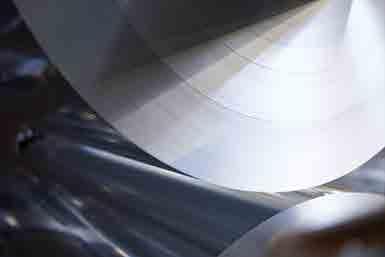
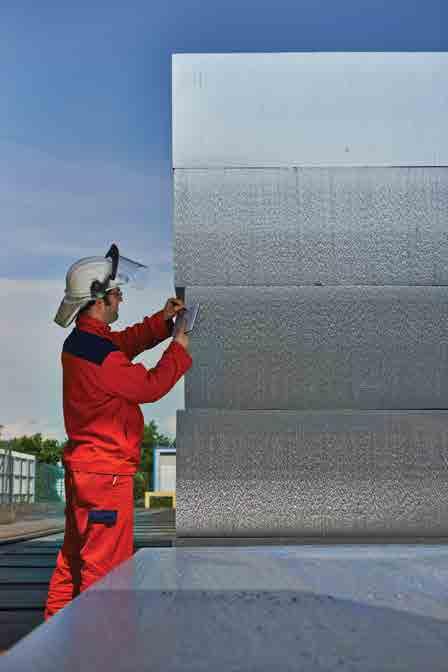
printing plates for offset printing – every third newspaper is printed on plates that have aluminium sheet manufactured by Hydro.”
A further common application of aluminium is in the heat exchange industry, where the storage of heat or cold is required.
“Aluminium is a good conductor of temperatures and currents, making it the ideal material for electronic devices, long distance power cables and smartphones. It also comes into its own in the area of renewable energy, for battery foils with distinguished purity and surfaces. This enables renewable energy to be stored, which is important as of course the wind does not always blow and the sun does not always shine, necessitating storage systems,” Mr Steffen points out.
Reusable material
Germany is already a leader in aluminium recycling within Europe, and Hydro supports a closed material loop, by further expanding its network of recycling capacity .- to keep .aluminium, the strongest growing metal on earth, in use, again and again. This May, Hydro commissioned a €45 million facility to recycle up to 50,000 tonnes of used beverage cans per year at its Neuss plant in Germany. While countries collect cans in various systems, where bulk often contains impurities and other materials, Hydro is the first to adopt a patented, advanced sorting technology for used beverage cans, able to process collected aluminium material with up to 20 percent impurities. “It makes the new recycling line the best place to be for any used beverage can,” said Hydro President and CEO Svein Richard Brandtzæg.
The new used beverage can line helps optimize Hydro´s sourcing of metal for subsequent fabrication. Thus it will save 350,000 tonnes of CO2 emissions each year, compared to use of primary aluminium.
“Recycling only requires 5 per cent of primary energy, this is like a payback into an energy bank, each time we conclude and start a new life cycle. This is of particular importance for fast moving products such as beverage cans: when collected, it can be recycled, processed and back as a filled can in just 60 days. In contrast cars or buildings with aluminium last for many years, so around 75 per cent of all aluminium ever produced is still in use today,” Mr Steffen says.
R&D facilities
Hydro values research and development and has several competence centres, where even better aluminium alloys are developed. Activities are strongly focused on core products and production processes, but also cover broader topics, such as understanding the societal, technological and environmental requirements for sustainable development.
“We have our own technical customer service teams in each market segment and business unit, in order to be in close contact with customers and manufacturers, and also with developers, to help them make the best use of aluminium,” Mr Steffen concludes. n
