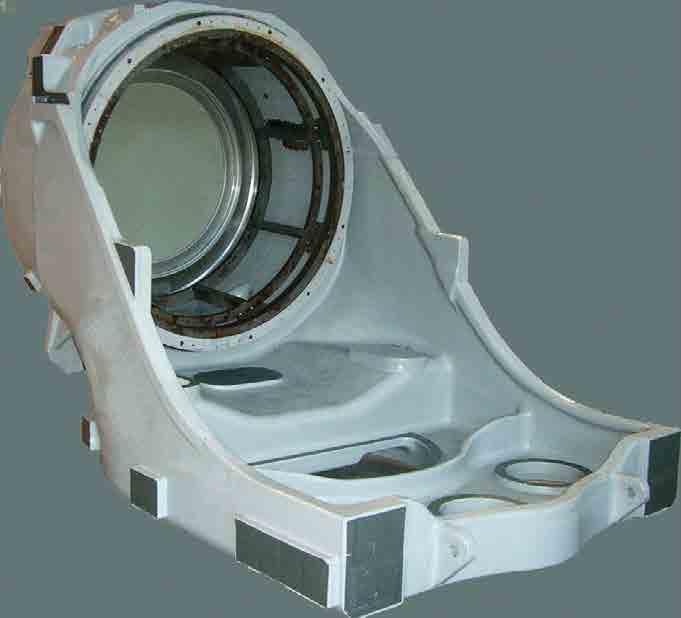
4 minute read
Moulding quality and reliability VDP
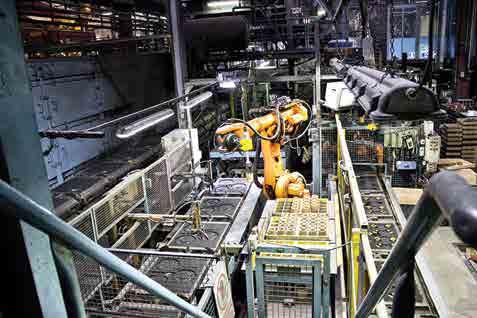
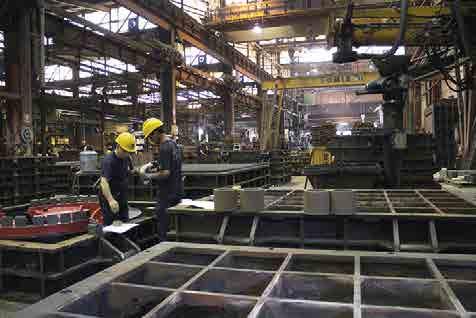
MOULDING QUALITY AND RELIABILITY
Energy, shipbuilding and mechanical engineering are the main areas of application for VDP, one of the most important Italian foundries. Its wide product range, high quality standards and customer service are its main assets, says Daniele Garavaglia.
With over €10 million invested during the last three years in new technologies for cast iron melting, and another €20 million investment to be apportioned, by 2020, for the construction of new facilities and the hiring of 40 new employees, VDP is on a path of dynamic growth. Active for more than three generations in the development of casting processes and cast iron jets, VDP Fonderia SpA is a force to be reckoned with.
“We have 200 employees and collaborators, and believe our company to be the second largest European fusion iron foundry, specialised in small-medium series up to a few hundred pieces, with numerous environmental work safety systems,” explains sales director Carlo Felici. VPD was founded in 1992 by the union of two families coming from the melting tradition: Vicentini (which today is responsible for the global management of the company) and De Pretto. Together, they oversee skills, capital and production facilities.
A major player in foundry applications
With a consolidated turnover of approximately € 60 million, the company, based in Schio (Vicenza) is now a major player in foundry applications in the energy, shipbuilding, agro-mechanical, earth-moving and other
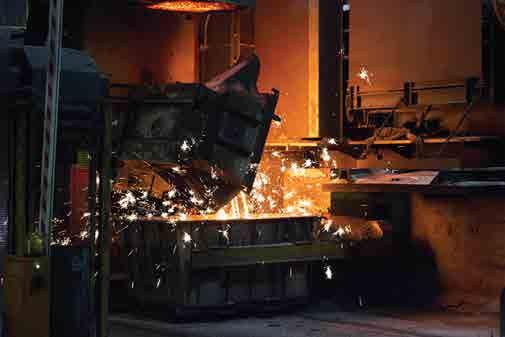
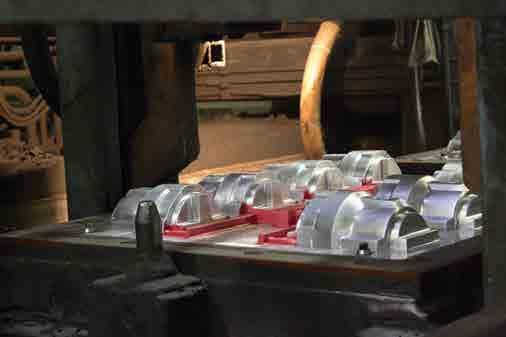
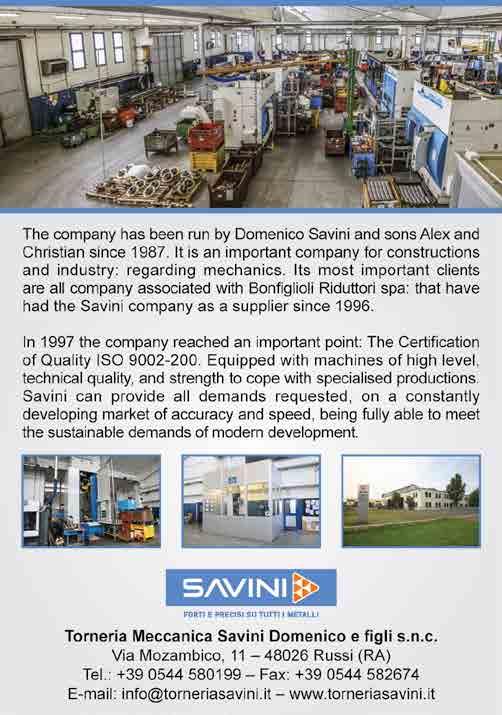
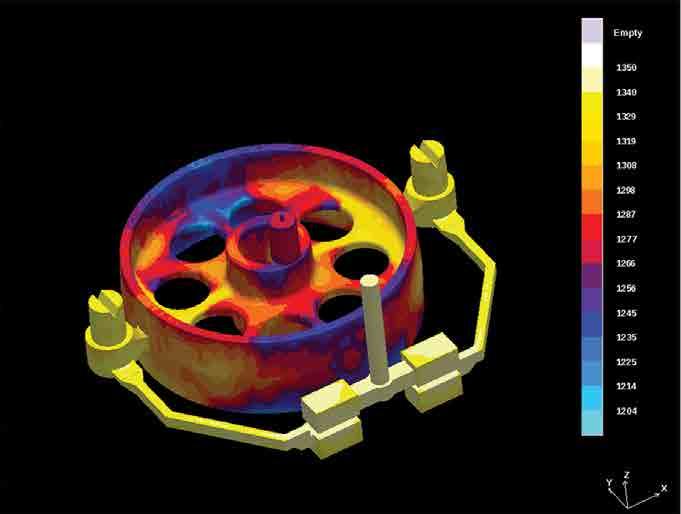
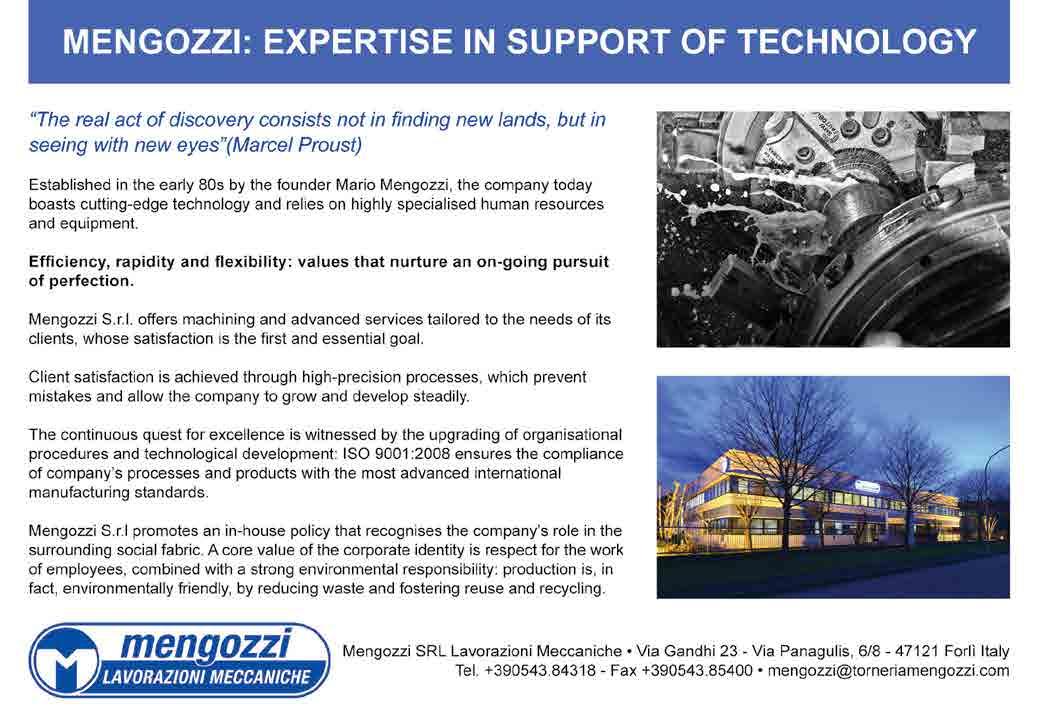

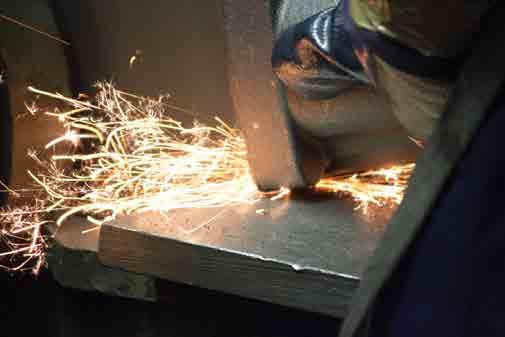
primary industries, with clients such as Siemens, General Electric and CNH Industrial. There has been a big surge in the production of castings for energy applications, particularly with regard to renewable sources, registering a 30 per cent sales increase. “Our three main melting plants, differentiated by volumes to be treated and by two casting systems, manual and automatic, allow us to create moulds of any size and shape, with weights ranging from 2kg to 100 tons and a very broad range of products for mechanical applications,” says Mr Felici. This production versatility makes VDP almost unique among Italian foundries.
Hand and automatic casting systems
The hand moulding plants are used for the production of: permanent magnets and multipliers for wind power plants; gas and steam turbines; compressors and pumps for medium and large systems; bases for diesel and gas engines, gearbox housings for the marine sector, propulsion components; racks for diesel and gas engines; presses for the moulding of iron products; tools, and a series of enormous jets. The jets produced by the automatic casting system, working on components up to 150 kg, include air compressors and refrigeration equipment, engine shafts, water pumps, components for earth-moving machines and oil-pressure systems.
Ensuring maximum safety
The melting department is the ‘core’ of the company: five electric furnaces, with variable capacity of between 17 and 60 tonnes per hour, produce melting power of 140 tonnes per hour. Always keen on technological innovation and structures that ensure maximum safety in the workplace, VDP uses a fully automatic system for handling the smallest ladles. A powerful robot on rails works on the furnace line, perfectly performing and completing the casting preparation cycles, and managing the preparation of different alloys through a computerised system. The furnaces department also supplies the hand and moulds handling line: some ladles with exceptional collection capacity are used for large casting production.
A perfect knowledge of the processes that transform a liquid metal into a permanent solid metal mould enables the company’s R&D department to plan and simulate, using appropriate software, the solidification of a new product before the construction of the equipment. The castings are subject to stringent tests to ensure their structural integrity. Qualified technicians perform several tests ranging from examination with durometers up to the examinations carried out through ultrasonic inspection tools, magnetic particle and thickness measurement. The metallurgical laboratory performs tests on temperature, quantometer analysis, microscopic examination with dedicated software for graphite and matrix measurements, tensile testing with machines up to 60 tonnes and resilience tests through pendulum up to a temperature of - 50 °.
Famous for quality and reliability
VDP is famous throughout Europe for its quality and reliability: “Our main market is Europe, where the required quality standard for cast iron industrial products is quite high and where we can sell directly. We believe it is more difficult for a company like ours to take on distant markets by using melting as the only product: the logistical costs are significant, and the competition relies on a less sophisticated demand. In any event, we are not competing on price with manufacturers in low-cost countries simply because the choice of a supplier is based on other benchmarks in the most developed markets,” concludes Mr Felici. It is the company’s high level of service, focus on customer needs, and attention to detail right from the design stage that have ensured its success in this competitive market. n
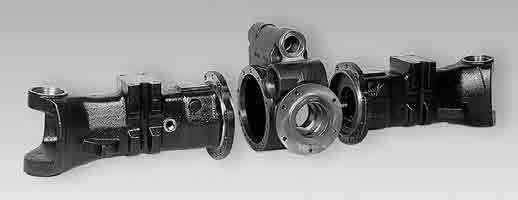
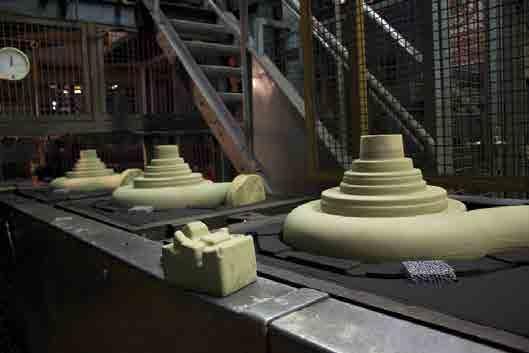