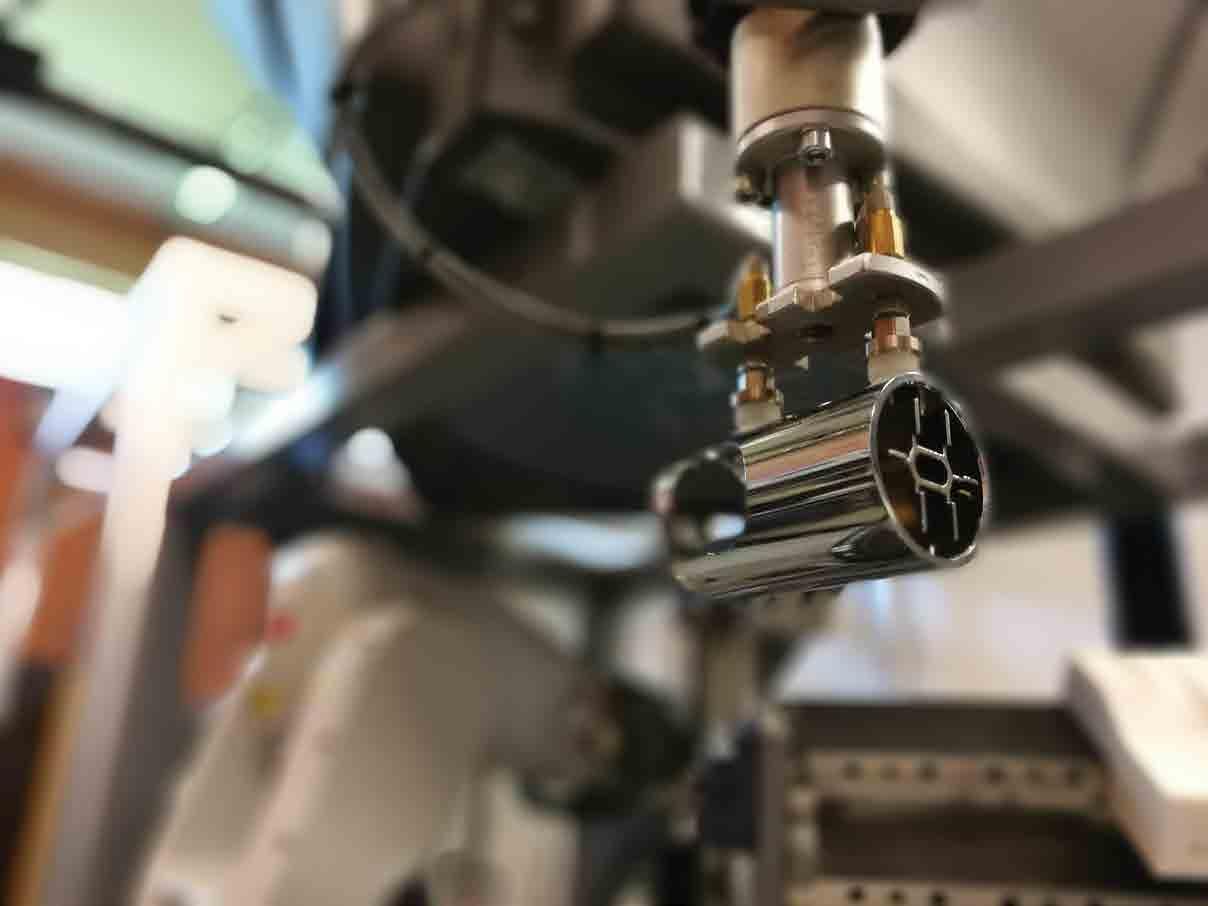
4 minute read
Mirror-image vision Helmee Imaging
MIRROR-IMAGE VISION
Helmee Imaging is a high-tech machine-vision company that leads the field in the 3D quality control of glossy and chromium plated products. Philip Yorke talked to Matti Saarinen, the company’s CEO, about its revolutionary 3D robotic inspection systems and the extensive global market opportunities for the company’s unrivalled technology.
Helmee Imaging Ltd is a high tech machine vision company based in Finland that provides automated quality control systems for manufacturers of highly-polished surface products. The independent company is a spin-off from the VTT Technical Research Centre of Finland. Helmee’s revolutionary machine vision systems are based on its unique CSD™ patented technology, which enables the accurate 3D imaging of glossy, mirror-like objects for the first time. Conventional systems fail in the quality control of glossy products due to uncontrolled reflections interfering with the results.
Helmee’s machine vision systems are the first in the market to enable 3D shape measurement and the detection of surface defects on high-curvature and mirror-like glossy surfaces. These advanced systems are able to accurately calculate an object’s shape and surface properties made of a variety of materials including plastics, glass, paint and ceramics. Quality control of complex products
Helmee’s breakthrough quality control system enables the quality control of complex products such as bathroom mixer taps, automotive fittings, bearings and even artificial joints. Although machine vision technology is widely used for the quality control of industrial processes, up until now it has only been possible to inspect complex glossy surfaces manually. Manual inspection work is expensive and the quality level can vary for a variety of reasons.
Helmee Imaging offers revolutionary systems for accurate quality control with benefits that include increased control capacity, lower inspection costs and more accurate, more consistent quality. With the aid of the company’s unique machine vision systems, it is possible to image every kind of glossy, high curvature, angular object and components. This remarkable system is capable of the simultaneous measurement of an object’s surface and 3D shape.

Unique image-processing software
Most conventional stereo imaging systems use two identical cameras that are horizontally displaced in order that the image captured by the two cameras overlaps. If a correspondence between the two images can be found then a triangulation can be used to determine the depth of the object. The biggest disadvantage to this traditional stereo system is occlusion, which occurs when some parts of the object cannot be seen by one, or both, of the cameras. However, no matter what imaging method is adopted, it is virtually impossible to acquire images from objects with highly polished, mirror-like surfaces. This task is made even more difficult if the glossy object involves high curvature or an angular surface.
For this reason, many highly reflective items such as ceramic plates, faucets and chromium-plated, painted of polished objects are still inspected manually after they are manufactured.
Helmee has resolved this age-old problem with its unique imaging technique known as, Covered Stereo Deflectometry (CSD™). The company’s CSD™ inspection station consists of a machine vision system that includes cameras, a special illumination system, a PCbased image processing unit, a mechanical frame with dust-proof covers and an operator interface with monitor and HMI.
Revolutionary system
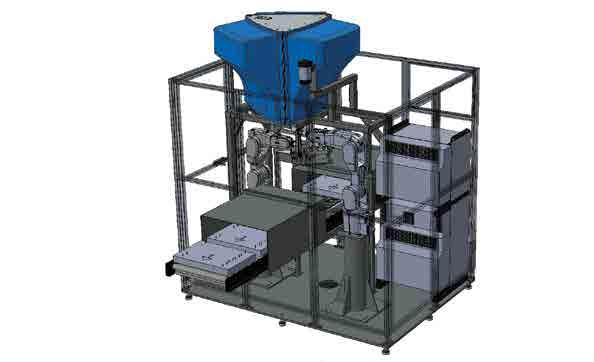
Saarinen said, “Helmee was founded as a result of research carried out at Finland’s VTT research centre in Espoo Finland into the quality control of mirror-like finished objects, which until now has been impossible due to the highly reflective nature of the objects involved. We have a long history in the development of sophisticated machine vision systems and now the technology has been tested and proven, we have been contracted to commercialise the exciting new technology.
“Although there has been no official launch of the new system yet, we will be showcasing our new, revolutionary technology at the forthcoming K Trade Fair in Dusseldorf, Germany later this year. We can be located in Hall 11 on booth C46 where visitors will be able to see a live demo of the new imaging system in operation. Our advanced vision system will demonstrate how chrome-plated items can be imaged and even the tiniest defects can be reliably detected.”
Saarinen added, “Today manufacturers demand flawless chromium plated and plastic parts that can be guaranteed to be perfect, without scratches, pits or pimples on the mirror-like surfaces of their products. The automotive industry and domestic appliance industry are both markets that could benefit significantly from the new Helmee imaging systems. For example there is huge potential for us from the manufacturers of chromium-plated car door handles, with more than 300 million being produced every year.
“As a relatively new company we are working closely with JMI in Hong Kong, which is one of the world’s biggest chromium plating companies, and Sarrel in France, a manufacturer of components for the automotive industry. Here at Helmee we design, develop and manufacture the vision system light-sources and software. We subcontract the manufacture of our special robotic systems before we assemble them and deliver them to our customers.
“Our unique, patented machine vision systems can scan and sort over 14,000 product parts or components a day, so for a run of 300,000 parts, 20 vision systems would need to be employed. Just one of our robotic cells is capable of replacing up to nine manual inspectors and offer far greater accuracy than the human eye. It has been proved that our imaging system is 100 times more accurate than relying on human examination.” n
For further details of Helmee’s revolutionary machine vision imaging systems and services visit, www.helmee.com