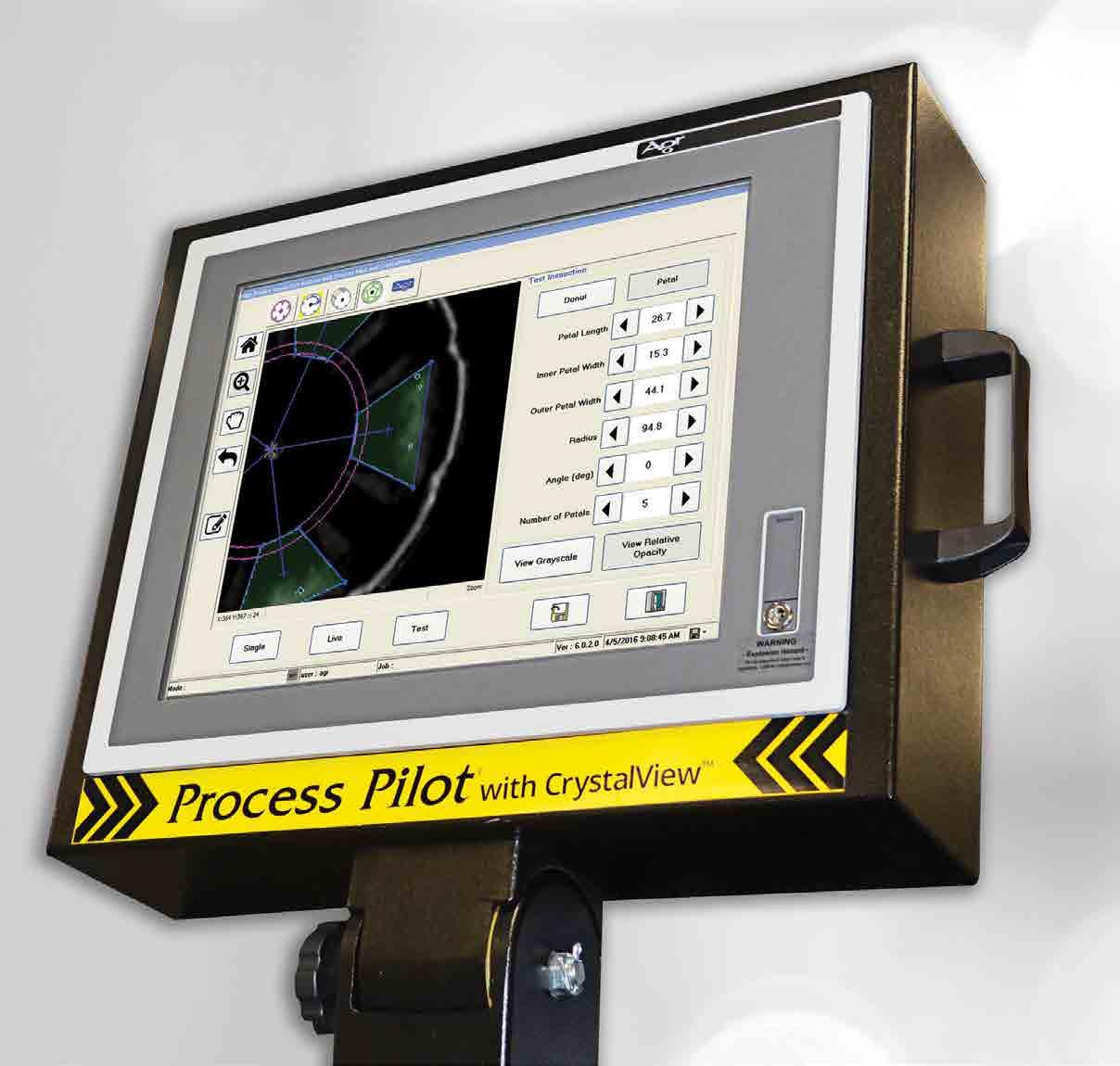
7 minute read
Maximising quality and performance Agr International
MAXIMISING QUALITY AND PERFORMANCE
With slim margins in the PET bottle industry, it is often difficult to produce a quality product while maintaining meaningful profit margins. The Process Pilot® system, from Agr International, offers PET bottle manufacturers a means to reduce PET bottle production costs while at the same time improving overall bottle quality and performance.
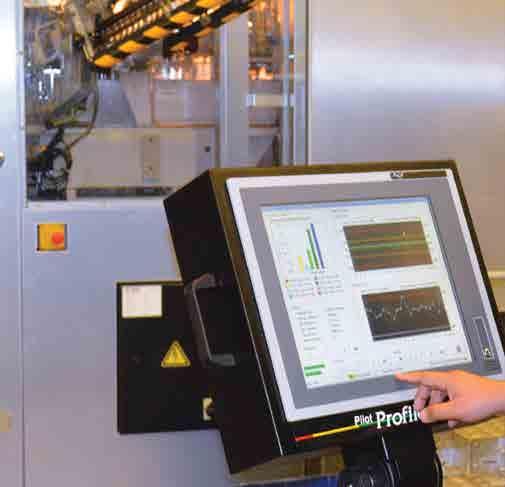
Installed in a reheat stretch blow-moulder, the Agr Process Pilot system makes it possible to operate with a tighter process control than possible with traditional ‘hands-on’ blow-moulder management. With that comes a myriad of benefits, some of which have significant cost saving implications.
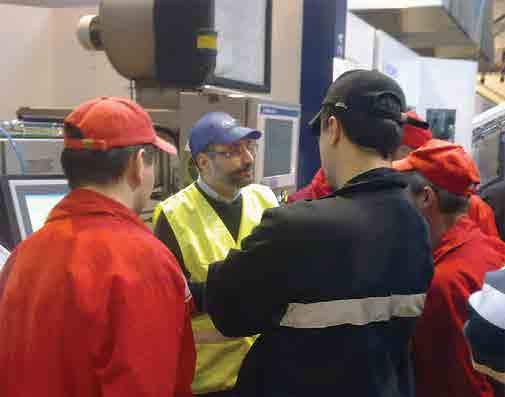
Measure, control, optimize
Consistent and properly distributed material is the key to the production of high performance PET bottles. The precision of material distribution becomes increasingly critical with bottles when lightweighting programmes are in play. With a multitude of variables affecting the blowing process, producing bottles that have accurate material distribution on a consistent basis is a daily challenge. Agr’s Process Pilot® blow-moulder management system addresses this challenge with a simple solution. Installed within the blow-moulder, the Process Pilot system incorporates a three-pronged approach: 1) measure material distribution on every bottle with high precision; 2) control the blow-moulder based on bottle measurement to maintain desired material distribution; and 3) optimise the material orientation to maximise bottle performance. Unlike operator adjustments, the Process Pilot system can adjust one or all of the blow-moulder controls simultaneously to achieve the best possible material distribution and bottle performance.
How Process Pilot works
Agr’s Process Pilot system works in conjunction with the reheat stretch blow-moulder to proactively manage and maintain container material distribution at a specified thickness to within ~0.01mm. This is accomplished by continuously monitoring every bottle for material distribution, analysing minute changes and adjusting the blowmoulder controls to maintain pre-defined distribution levels. Unlike operator adjustments, the Process Pilot system can adjust one or all of the blow-moulder controls simultaneously to achieve the best possible material distribution.
By monitoring the material distribution of the blown container, the Process Pilot is able to account for subtle changes in the process that would normally go undetected by the operator. This prevents the process from drifting out of control before the operator’s next quality sample and averts the loss of precious little processing margin.
In the course of bottle production, an untold amount of variables in the production cycle can affect the processing and quality of lightweight bottles. The Process Pilot system can accommodate many types of environmental changes in and around the blow-moulder as well as preform preparation and storage conditions that can occur. Compensation can be made for temperature, moisture content, and minor Intrinsic Viscosity (IV) changes to the preform to maintain a consistent process, within the smallest process window.
CrystalView™ Optimisation
Managing crystallinity for optimal performance
A recent expansion of the Process Pilot system includes the management and optimisation of crystallinity with the CrystalView™ option. Maintaining appropriate material distribution, and at the same time optimising material orientation, requires great skills, and is difficult to achieve with conventional blow-moulder management techniques. With the CrystalView option, the Process Pilot system has the capability to manage material distribution and material orientation simultaneously, making it possible to produce the highest quality bottles, with consistent material distribution and optimal material properties. CrystalView manages the process to the point where material orientation is ‘just right’, while avoiding the creation of pearlescence. With CrystalView, it is possible to reduce the preform processing temperature to the ideal processing point (as much as 10 deg. C) for a given bottle design. By
Process Pilot® Control
Pearlescence
Traditional Measurment and control
-5 -4 -3 -2 -1 0 1 2 3 4 5
Perform Stretching Temperature
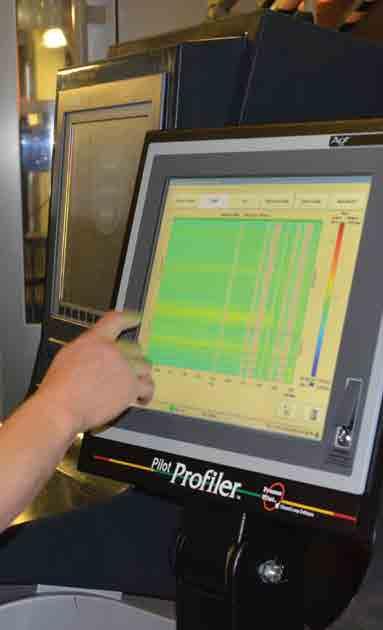

doing so, material orientation is optimised over the entire bottle. Plus, by running colder, excess material can be pulled is moved from the base of the bottle to other areas, reducing the amorphous material and the residual stress that can lead to base failures associated with the transition region.
Simple operation
The Process Pilot system operates very similarly to the auto-pilot in an aircraft. The process engineer sets up the optimised process for a given bottle, then a one-time control characterisation is performed (learn mode) to finalise the recipe and establish a baseline. Once set to the defined recipe, Process Pilot manages the blow-moulder as if on auto-pilot, continually adjusting control parameters to maintain precise thickness distribution as the process changes. Since the Process Pilot system can oversee blow-moulder operation on a 24/7 basis, it provides a continuity in bottle production that is not possible with other methods.
Facilitating light-weighting
Light-weighting has been an important tactic in the cost reduction efforts of PET bottle manufacturers. However, as manufacturers continue to remove material, bottle processing becomes increasingly difficult. The process window becomes smaller as weights are reduced. Consequently, on a light-weight bottle, minor changes in the process can have major effects on material distribution. Tight control over the process is therefore imperative and the need to control the location and the thickness of the remaining material is critical for proper bottle performance.
Often bottle producers limit light-weighting to a point where bottles can be processed with minimal problems, leaving extra material in place to provide ‘comfortable’ processing safety margins. With the Process Pilot system’s ability to tightly control the process, lighter bottles with ‘just enough material’ to meet performance requirements can be processed with a very high level of confidence. Material distribution is managed precisely throughout the production process, paving the way for maximum material reduction.
Additionally, material optimisation through the CrystalView product brings further lightweight opportunities. The ability to produce lightweight CSD and water bottles where the material is fully optimised makes it possible to realise the maximum bottle performance with minimal weight from a given design. Bottles are stronger with better performance and as a result provide greater stability and an increased ability to confidently process without incidence in filling, labelling and capping operations. Raw material flexibility
Another area where Process Pilot can offer cost saving opportunities is in the type and quality of raw material. Lower grade material and/or preforms can have a variability and inconsistency that can translate into processing, quality and performance issues. With the Process Pilot system, blow-molder adjustment to accommodate minor variations in material quality (high AA or variations in IV) is performed on a continuous basis. When material-related process variations are detected, the Process Pilot system pro-actively adjusts the blow-moulder to account for these variations and maintain optimal material distribution. Because the Process Pilot system tightly controls the processing window of the blow-molder, it is possible to increase the percentage of off-spec (wide-spec) material and/or PCR content safely. This capability provides bottle manufacturers with additional opportunities for savings without compromising quality.
Other benefits
The Process Pilot system offers a number of benefits in addition to improved light weighting and materials savings. These include the elimination of the need for section weights, reduced scrap, energy savings, improved overall bottle performance and quality, and lower incidences of downtime in the filling, capping and labeling operations.
Summary
Agr’s Process Pilot® blow-moulder management system offers manufacturers a means to take the variability out of the bottle blowing process, especially when light-weighting programmes are in place. It also provides the additional process feedback that makes it possible to go the extra step and take light-weighting to the limits with full confidence. Where material is limited and safety margins are very tight, the Process Pilot system can provide the detailed, in-process feedback to manage and maintain bottle material distribution to a very high level of precision, resulting in the production of consistent, quality bottles, even at the fastest production speeds. In the end, with productivity improvements, energy savings, reduced downtime, improved quality and downstream performance, Process Pilot has been shown to have an ROI of less than two years. With an active light-weighting program, ROI can be reduced to a matter of months.
Agr’s Process Pilot automated blow-moulder control system has been on the market for several years and has amassed a significant global install base of major bottle converters and self-manufacturing brand owners. The Process Pilot product has proven to be a vital tool in the production of light-weight bottles, while improving overall bottle performance and quality. n Visit: www.agrintl.com