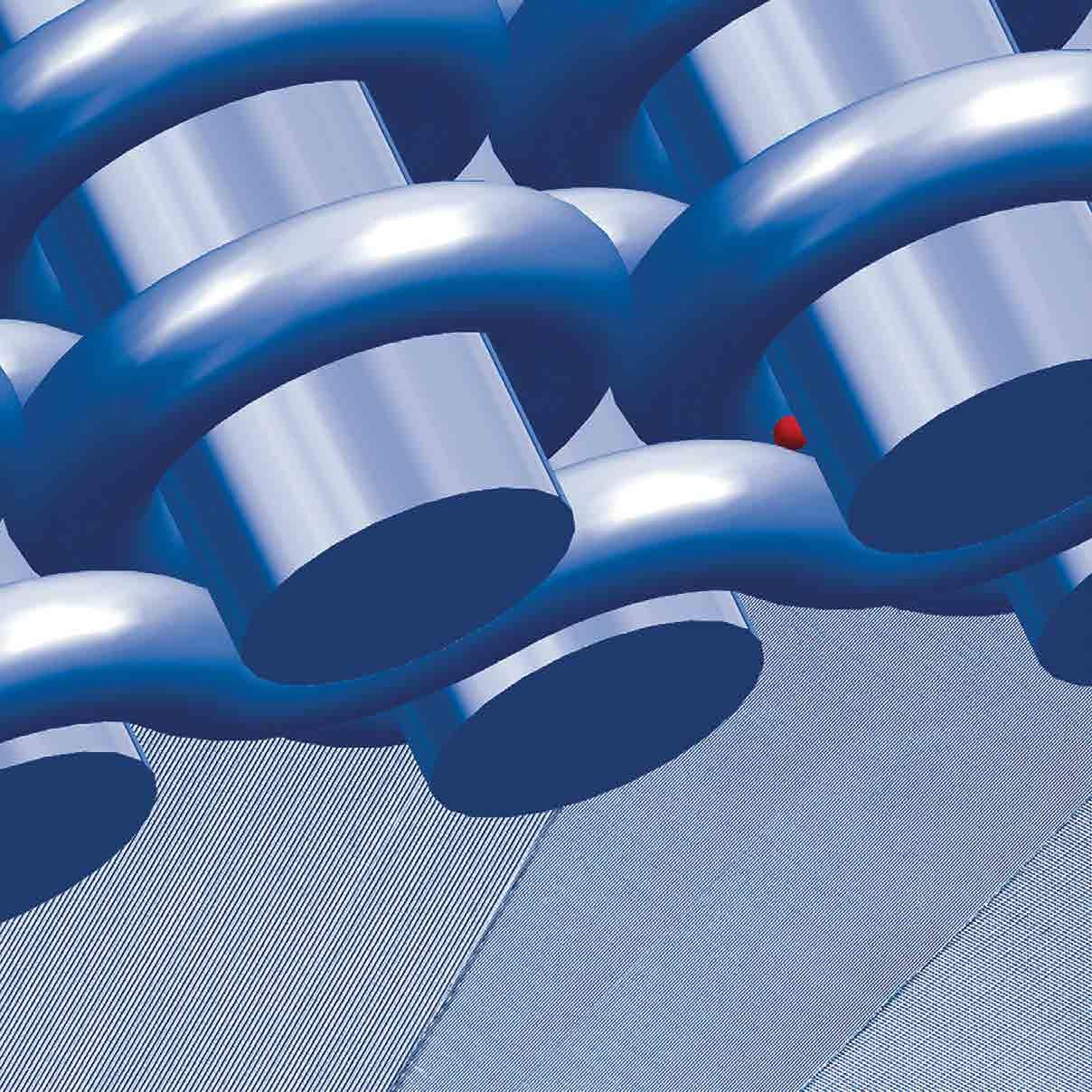
4 minute read
Masterclass in woven wire Haver and Boecker
MASTERCLASS IN WOVEN WIRE

Haver and Boecker is a privately-owned family company that is a global leader in the design and manufacture of metal woven wire cloth for a wide range of filtration applications. Philip Yorke takes a closer look at a company that continues to broaden its product portfolio and create new, innovative, and eco-friendly products.
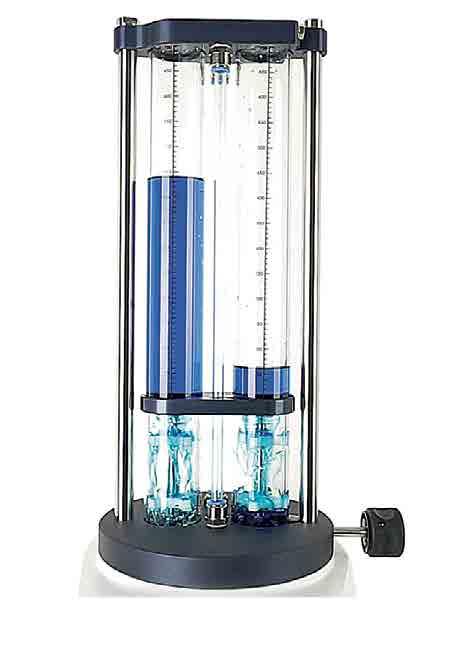
Haver and Boecker began by producing wire cloth in Hohenlimburg, Germany in 1887. Today it is one of the world’s leading wire weaving companies with a global network of branches and manufacturing facilities. The headquarters of the family-owned and managed company is in Oelde, Westphalia, Germany. With more than 50 subsidiaries located across all five continents, the Haver and Boecker Group operates worldwide with over 3,000 employees and 150 representatives. In 2015 the company recorded sales of more than €450 million.
The Haver and Boecker Wire Weaving Division conceptualises, designs and produces metal-woven wire cloth made of steel, stainless steel alloys and special materials such as titanium, Hastelloy, silver and many non-ferrous metals.
The company processes and fabricates the woven structure into precision engineered products. These are used for screening and filtration applications by the chemical, plastics, automotive aviation and electronics industries. This is in addition many to other industries including the aviation, aerospace, electronics, foodstuffs and animal feed industries.
New, unique filtration media
Haver and Boecker are planning to showcase an entirely new and unique filtration media at FILTECH this year that offers unsurpassed performance characteristics. The company will display its latest woven wire cloth products for filtration, cleaning, homogenising, protecting, securing and optimising, as well as its design and simulation capabilities. The company’s focus is centred on its newly developed three dimensional high performance metal filter cloth: Minimesh® RPD HIFLO-S.
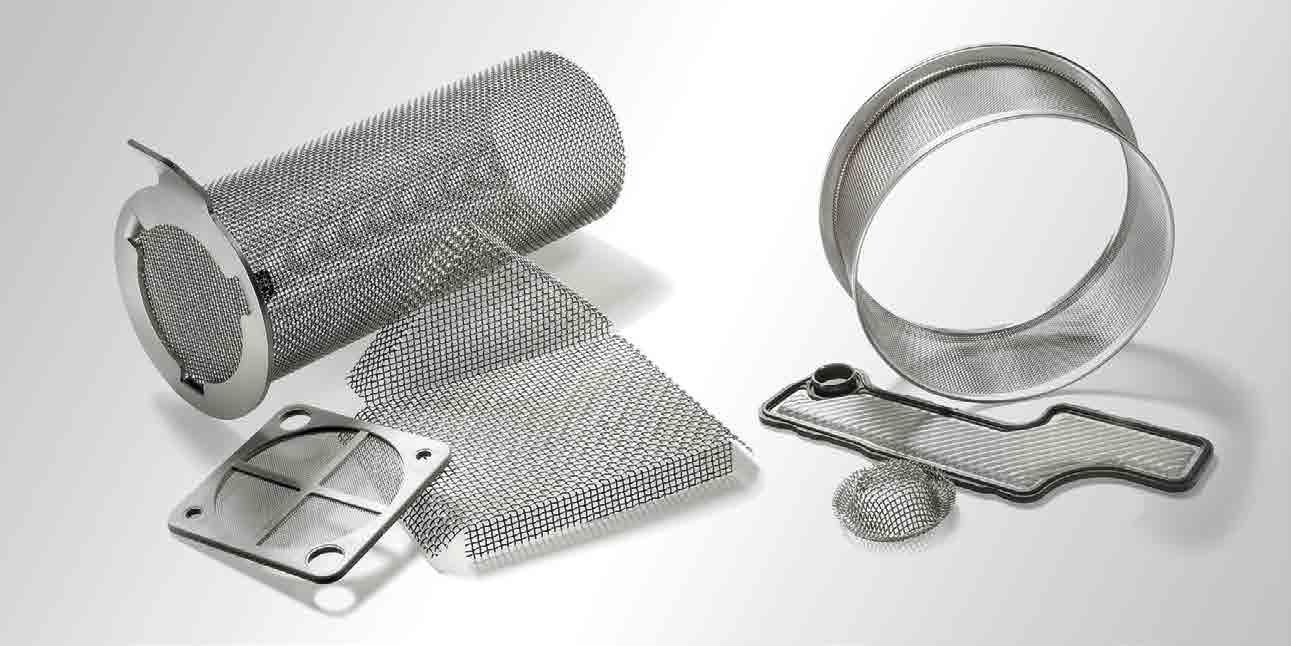
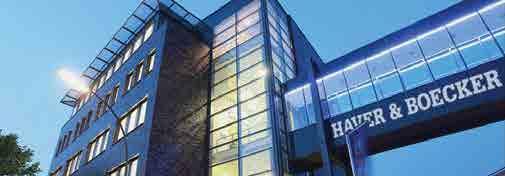
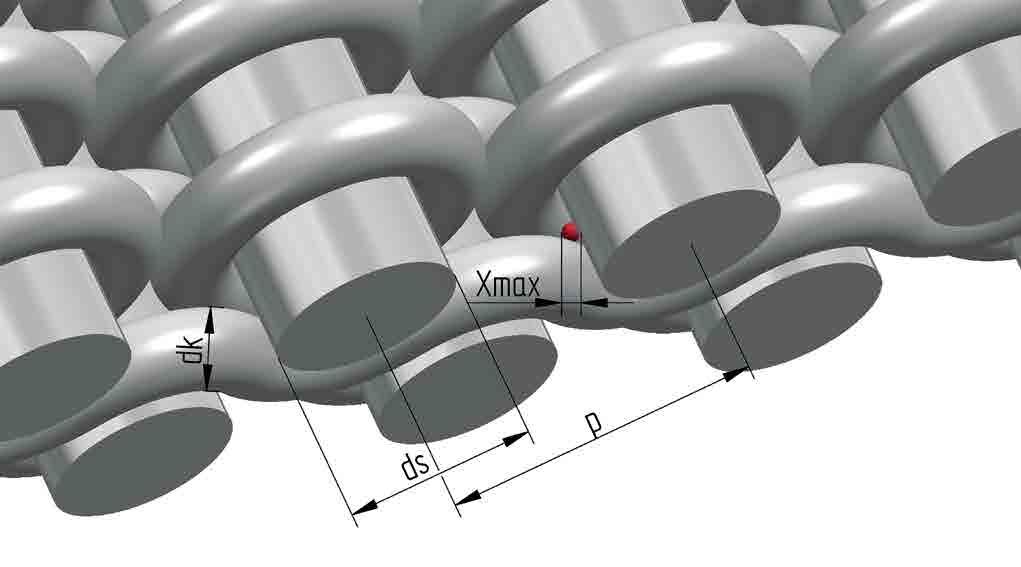
Haver and Boecker’s competitive advantage lies in its unique experience and continuous programme of research, which keeps it one step ahead of its competitors. This combination of tradition and innovation allows it to meet and usually exceed the high expectations of its customers. Furthermore, the exacting control of its production processes begins with its own design and manufacture of the machines that it uses and extends right through to its tightly controlled production processes.
This in-depth knowledge not only guarantees its high quality products, but allows it to develop special types of weave to meet diverse and challenging customer specifications. The company’s high production capacities work in tandem with its large range of products held in stock, which offers a clear guarantee of supply for its worldwide customers.
Focus on optimisation
Energy-efficiency optimisation is the foremost trend in the filtration industry today. Using less energy to produce more product in the same amount of time is a never-ending requirement in view of the growing demand for sustainable utilisation of resources.
The company’s new Minimesh® RPD HIFLO-S family of products clearly meet these growing industry requirements. The main unique properties of this ground-breaking system include achieving twice the throughput volumes compared with conventional Dutch weave systems in the low micron pore size range. The product can also be supplied with corrosion and heat-resisting alloys unlike any other woven media in the low pore size range. This is in addition to as offering an extremely sharp cut-point, thanks to the Haver and Boecker precision pore technology (verified and certified by Whitehouse Scientific glass-bead challenge testing).
Other major product benefits include excellent dirt-holding capacities and cleaning performance along with a high degree of mechanical stability thanks to its robust three-dimensional design. Finally the
RPD HIFLO-S offers significantly longer service life for increased production runs and reliability. New dimensions in filtration
Where conventional filter cloths have reached their limits, the newly developed RPD HIFLO-S opens up new dimensions for filtration. Using an entirely new weaving technology developed by Haver and Boecker, a three dimensional pore geometry is created that makes industrial filtration processes more efficient, faster and more economical than ever before.
The open surface over an area is significantly increased due to the unique new weaving structure. The medium’s flow-through rate can be doubled when compared to conventional filter cloths having the same pore size. In addition, the flow conditions are optimised and turbulence around the filter cloth is effectively avoided.
This new filter cloth can be manufactured from standard diameter wires. This has a positive effect on cost. Moreover, it is now possible to weave special materials such as Avesta, Hastelloy, Inconel or titanium in the small pore range, which previously had not been possible. Thus for the very first time the Minmesh RPD HIFLO-S offers a corrosion and temperature resistant filter cloth with pore sizes below 40um and a host of new product benefits. n
For further details of Haver and Boecker’s latest innovative products and services visit: www.haverboecker.com
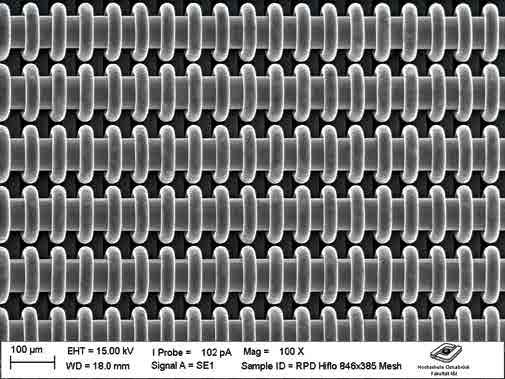