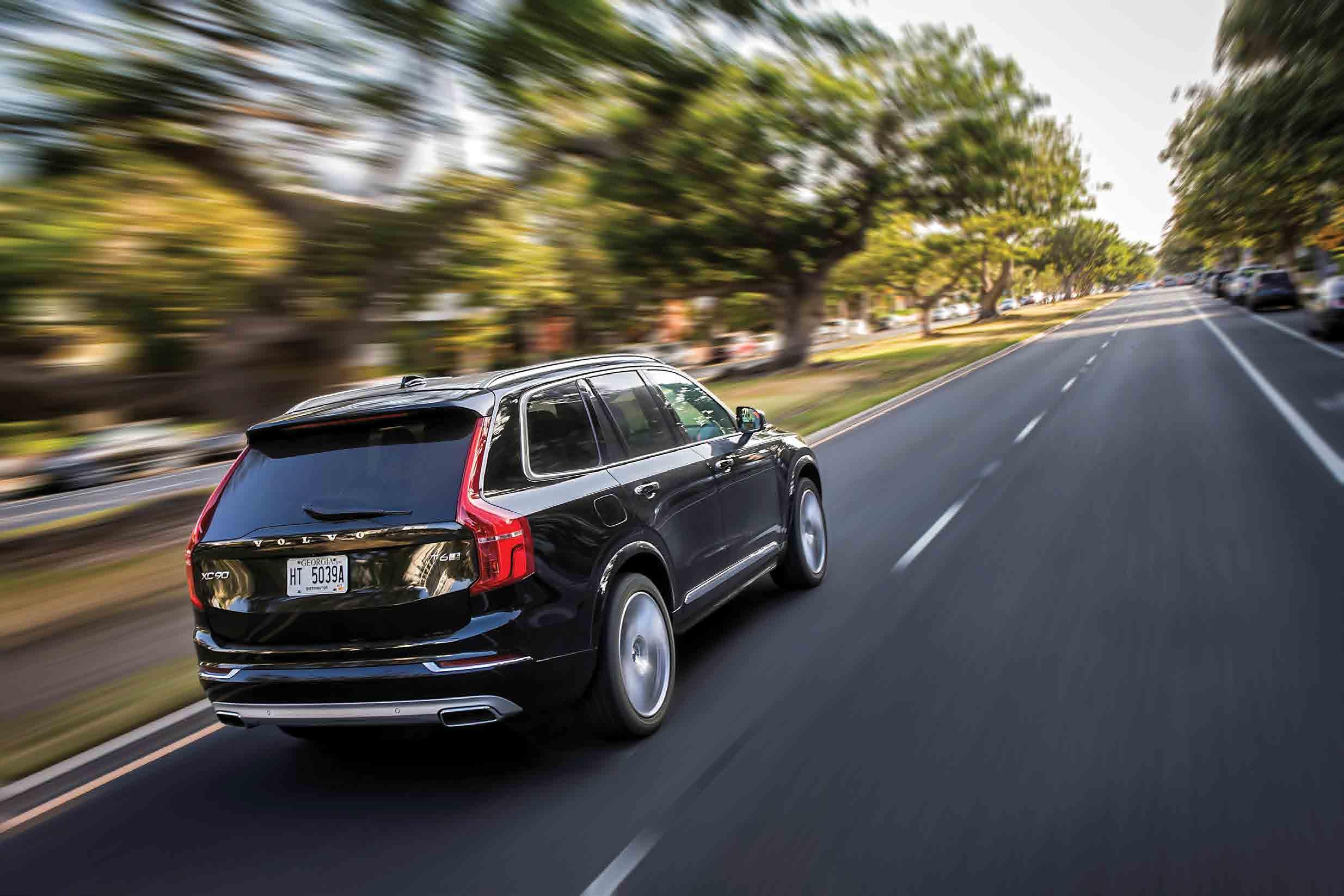
5 minute read
Passion for uniqueness Recticel
PASSION FOR UNIQUENESS

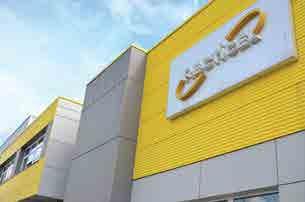

Recticel Interiors CZ, together with Recticel Most, are important production plants within the Belgian Recticel Group, a manufacturer of polyurethane products. The Czech plants are part of the group’s Automotive Division, and thanks to increased demand from leading carmakers both are expected to achieve significant growth in the coming years. Romana Moares reports.
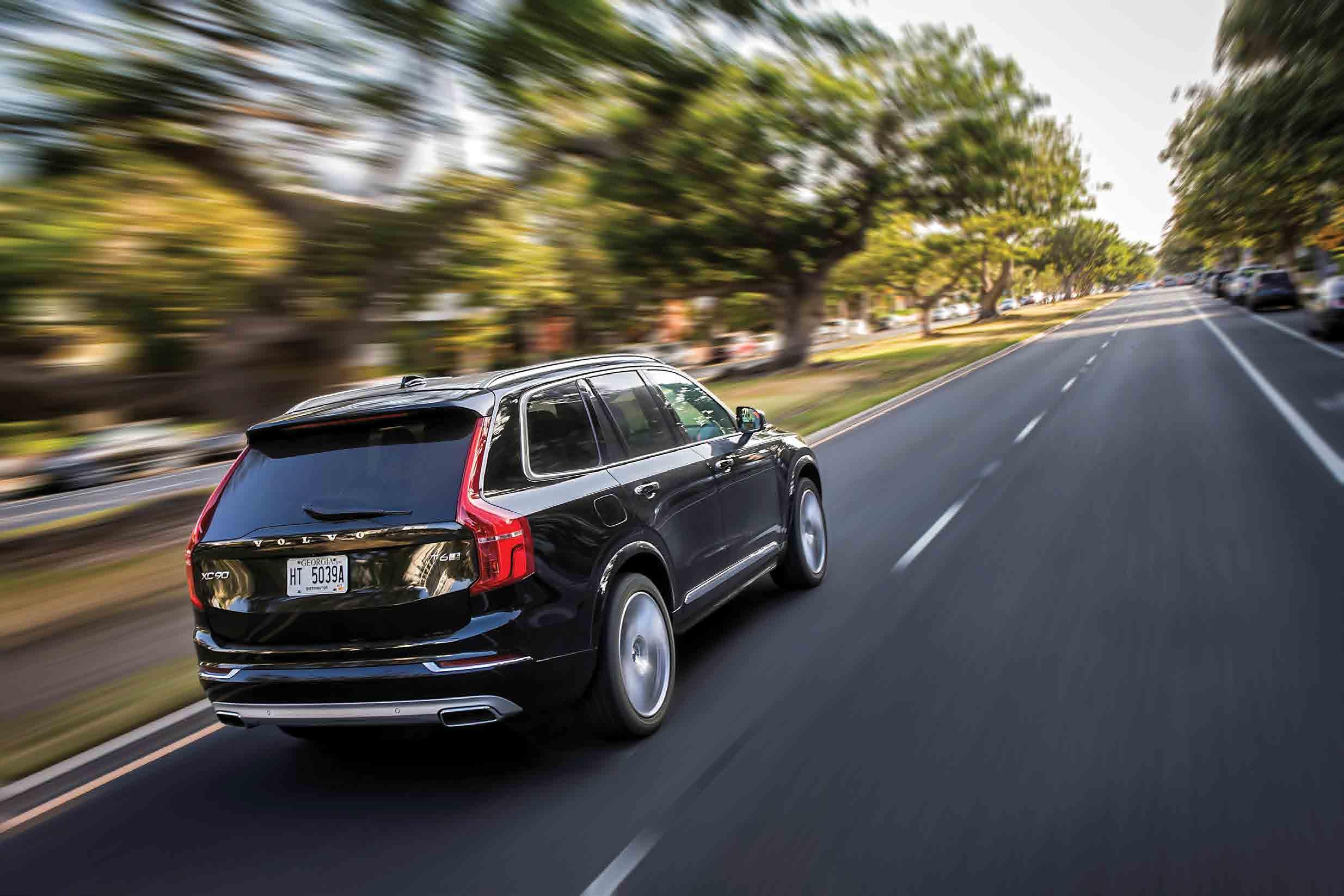
Recticel, a Belgian Group headquartered in Brussels, operates predominantly throughout Europe but it is active also in the United States and Asia. The group has 98 units in 27 countries employing 7600 people worldwide.
Its history goes back to the mid-18 century, although the activities of today’s company are focused on polyurethane processing and are divided into four core divisions: Automotive, Bedding, Flexible Foam and Insulation. The Automotive sector is very important for the group – it develops, produces and commercialises interior solutions (dashboard skins, door panels and other interior parts) on the basis of its unique, certified Colo-Sense® Lite spray technology. Under the motto ‘Passion for comfort’ Recticel strives to make an essential difference in driver comfort. The Automotive lines operate 10 production plants: one in the States, two in Germany, two in the Czech Republic and five in China (some of which are currently under construction). Czech operations
The group has two factories in the Czech Republic: one in Mlada Boleslav, the other in Most. “The two Czech plants are the largest and their importance is growing,” says Pavel Vokurka, plant manager of Recticel Interiors CZ in Mlada Boleslav, the larger of the two facilities. “Our plant generates almost 30 per cent of the division’s turnover, with the total output of both plants making up about 45 per cent.”
Recticel Interiors CZ was established as a green field development to support the group’s growing activities. In 2001, it started as a small factory employing 50 people, and series production for its first project – dashboard polyurethane skin for Mercedes Vito and Viano – was launched in 2003. Other contracts followed for BMW, Opel, Škoda-Auto, Volvo, VW, Scania and others. Over the years it has grown into a large operation covering 15,000 square metres and employing almost 500 people.
In 2007, Recticel won a production contract for the Mercedes E-class and it was assigned to the Czech operation. To this end, the second subsidiary, RAI MOST, was established in 2007. Series production for the E-class was launched in 2010, which was followed in 2011 by production for the Peugeot 408. The facility’s core production today consists of dashboard skins, door panels, passenger boxes and other components for car manufacturers.
Skin as required
“Basically, our core ‘spraying’ technology involves the spraying of polyurethane mixtures into heated moulds or polyurethane mass into special closeable forms. This technology quickly gained the attention of the leading players in the automotive industry. The second most important technology for us involves foaming the actual sprayed parts together with solid bearers,” says Mr Vokurka. “The desired outcome is a perfect harmony of surfaces throughout the entire interior, which is becoming more and more important for our demanding customers. This is one of Recticel’s key competitive advantages.”
The company’s production portfolio is regularly expanded, to reflect current trends for reduced weight and emissions and also to introduce new products to win additional contracts from both current and new customers. While Recticel started as a typical Tier 2 supplier, its products are now sold to Tier 1 manufacturers or even OEMs. The focus is, as Mr Vokurka explains, on increasing the added value and thus boosting sales.
But the Czech plants are by no means only focused on manufacturing processes. Some 3–4 years ago, applied research and development was transferred to RAI MOST where a specific department
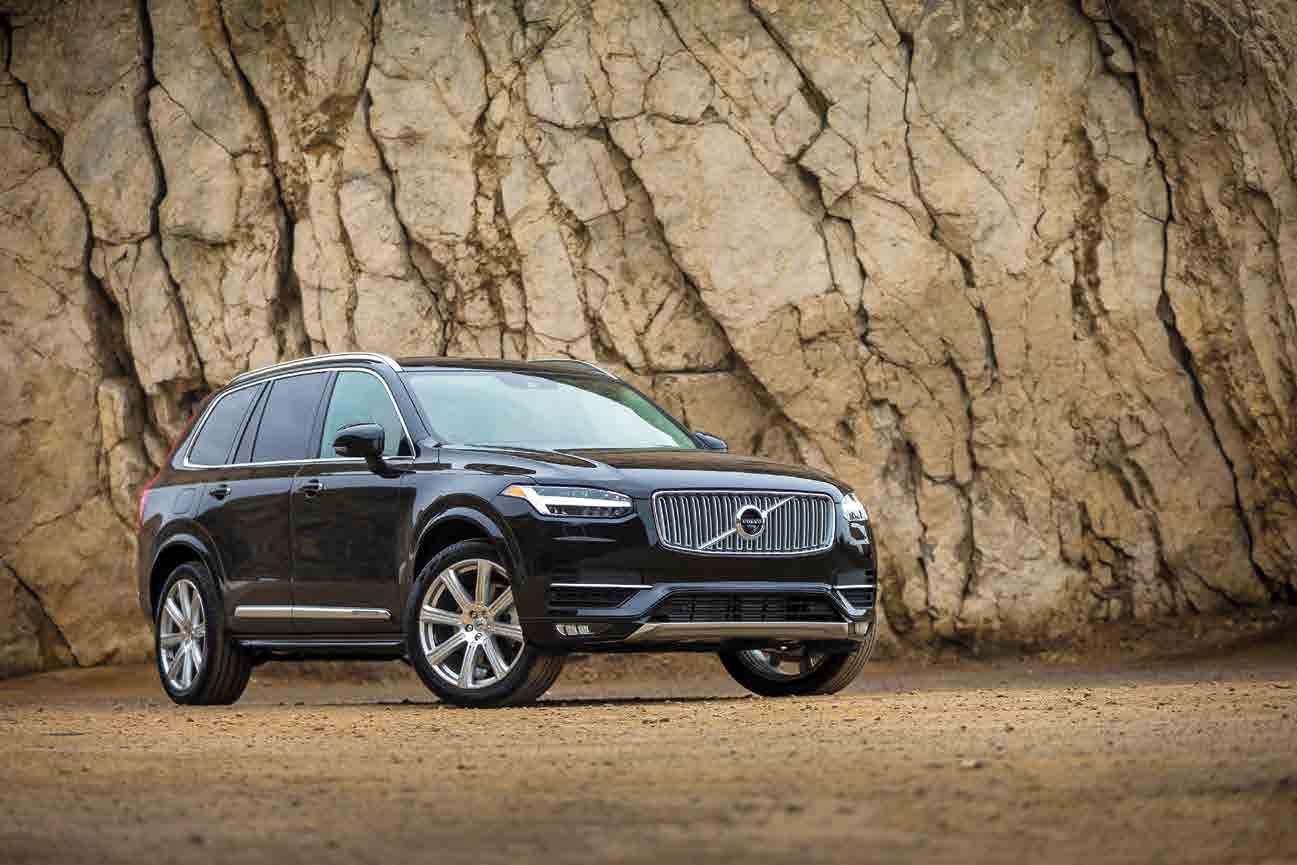
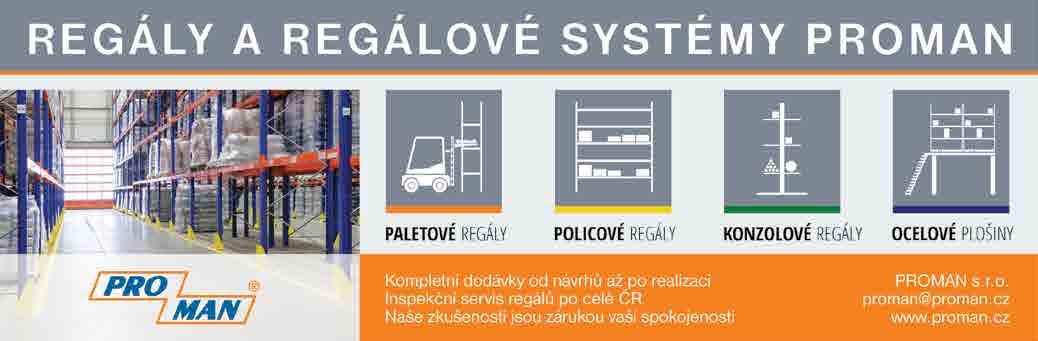
was established to focus on the development and production of technological assemblies as well as new materials and applications.
Recticel’s customers include renowned and traditional carmakers such as Grupo Antolin, IAC, Faurecia, PVT, Visteon, Decoma and many others. “We supply directly to VW, cover the almost entire range of current Volvo lines and very recently, for the first time in the company’s history, we signed contract with Audi with production and delivery planned to take place two years from now,” says Mr Vokurka.
Future growth
Recticel’s development in the Czech Republic has been a history of ongoing investment. Mr Vokurka explains that the group generally invests around €10 million in technology upgrades each year, of which a substantial proportion is spent on the Czech factories. As a result of continuous capacity extension, Recticel Interiors CZ has recently built a new storage facility, while the former store was turned into a production hall to support growing demand. In 2016 further investment in production technologies is planned in order to meet new project demands. Similarly, RAI MOST is also in the process of increasing production capacity. According to Mr Vokurka, the Czech plants expect to increase their turnover by around 25 per cent in the next 2–3 years.
The group’s largest investments will, however, be made in China. Mr Vokurka stresses that in the next few years the focus will be on the successful startup of projects in this market. “The Czech plants provide full support to our Chinese colleagues so that the startup is as smooth as possible. This is currently the most important goal,” he says.
In the future, the company wants to continue to develop and employ new, more environmentally friendly materials. There will also be a focus on the development of new materials of the Compo-Lite® type (bearers of various elements in car interiors), where Recticel has achieved very low weights. The general strategy is to continue to provide first class products to existing clients, as well as winning new ones.
“In this context, I would like to thank our employees without whom no success would be possible. We have been though some turbulent years and they have carried the company through. I hope that they will keep their enthusiasm and commitment in the next challenging years so we can grow further,” concludes Mr Vokurka. n

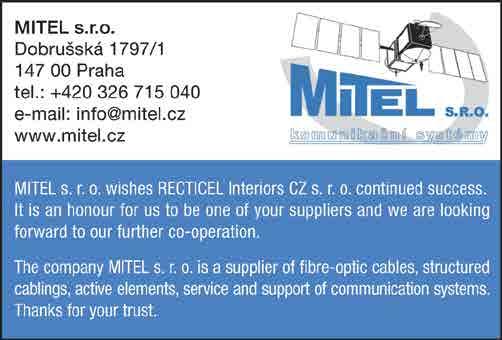
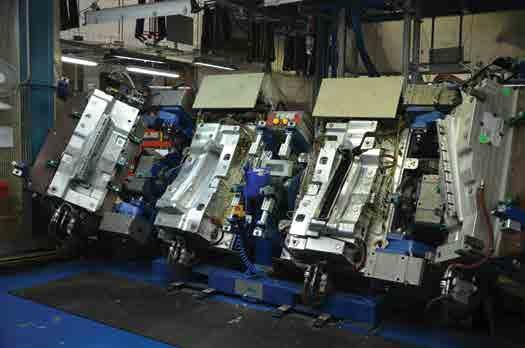
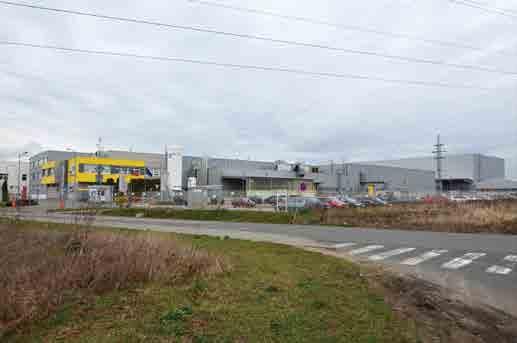