
4 minute read
Naturally perfect porcelain LUBIANA
NATURALLY PERFECT PORCELAIN
LUBIANA SA is Poland’s leading porcelain factory. It is also the main part of the PORCELAIN GROUP, which is the largest group of that kind in Europe. Dariusz Balcerzyk reports.
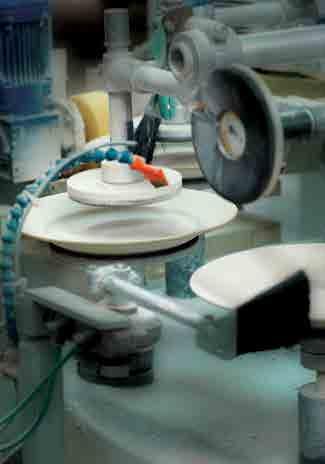

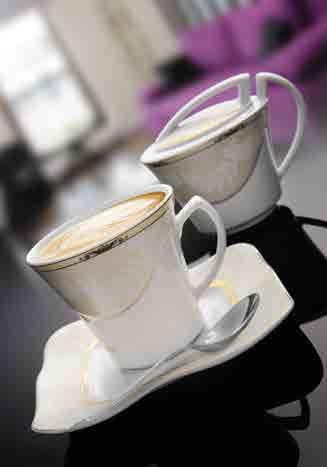

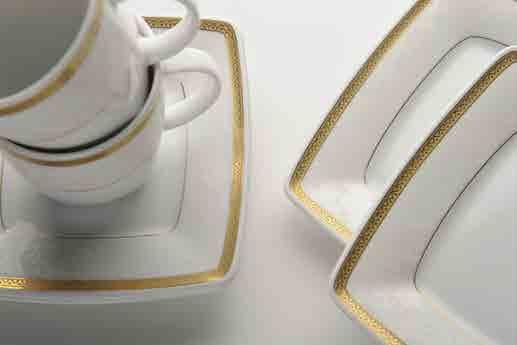
LUBIANA was founded in 1969 in the small town of Lubiana. In 1992 it was transformed into a joint-stock company with the State Treasury as a single shareholder. Three years later, under the General Privatisation Programme, the company’s shares were located by the State Treasury in the National Investment Funds. In 2002 the majority shareholding (90.7 per cent) was sold to WISTIL SA, a silk company from Kalisz.
The next year, LUBIANA started to build its own group. It took over the 99.41 per cent share previously owned by Porcelana Chodziez SA, then in 2012 it completed the acquisition of the Z.P. Cmielow Limited Liability Company. Both Cmielow and Chodziez have a long tradition in the manufacturing of high quality porcelain (Cmielow was founded in 1790 and Chodziez in 1852). The group also consists of the following companies: Limko, a manufacturer of decal; Lubiana-Hurt, which is the china, glass and cutlery wholesaler; and Lubeko, a sewage specialist. LUBIANA also owns a carton producer. Porcelain for every taste
“LUBIANA is a well-organised, modern organisation with more than 1460 employees. We have achieved a very high quality and wide range of products, with more than 2000 assortments for catering and domestic use. We offer around 80 styles, both in regular (round) and irregular shapes. Annually, we introduce 150 new products. Our range of decorations includes about 3000 proposals for different designs prepared by domestic and foreign designers. We have been closely cooperating with designers from Italy and Germany. We are capable of carrying out short-term orders, both for small batches of goods and for large projects placed with us by such big networks. We also accept orders for products with individual decorative designs and logos (for instance, for the HORECA sector),” says Zbigniew Andrzejewski, LUBIANA president.
The group’s annual production capacity reaches 20,000 tonnes and it makes 4 million pieces of porcelain a month. With exports accounting for almost 70 per cent of Lubiana’s total sales, its products have been
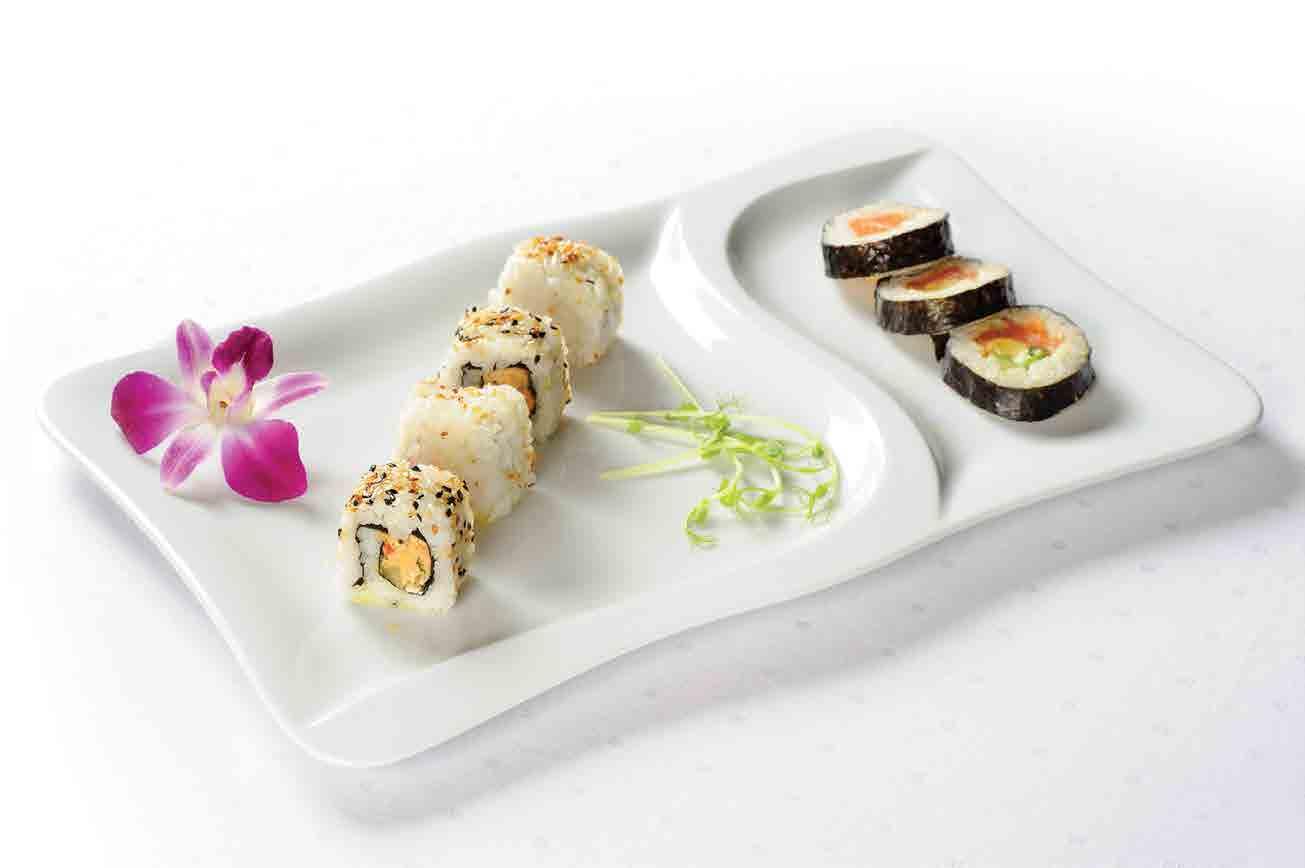
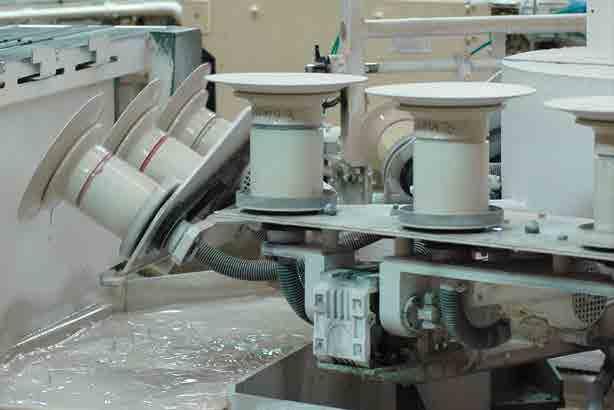
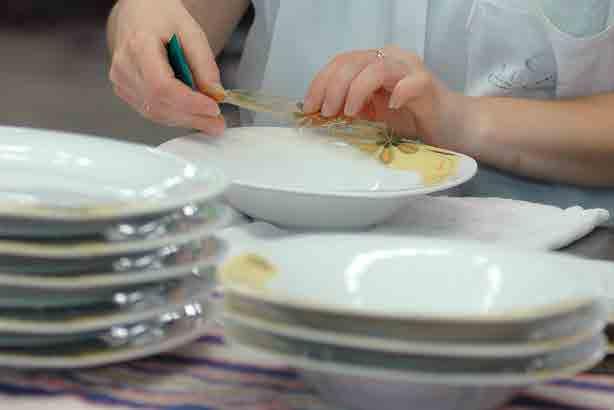
delivered to 42 countries around the world. The largest foreign markets are Germany, Italy, France, Switzerland, the Netherlands, Russia, Switzerland, the USA, Canada, Brazil, Dominican Republic and Mexico.
LUBIANA Porcelain is also appreciated by global VIPs: “Recently, we delivered 200 sets of porcelain to the aircraft fleet of the King of Spain. The Air Force Two, the aircraft carrying the US vice-president, has also been equipped with porcelain sets from LUBIANA,” points out Mr Andrzejewski.
Modern technology, experienced people
LUBIANA manufactures white hard porcelain. It applies two kinds of high-temperature burning: the first, so-called biscuit burning, at 1000º C; the second, so-called sharp burning, at 1400º C. Such production process ensures high thermal strength, resistance to mechanical damage and high glaze hardness. There are also two methods used for the decoration process: the first involves embedding the decoration in enamel at 1250–1270ºC, so burnt decorations have a very long life; the second is known as ‘on-enamel decoration’, in which the burning process is performed at 780–820º C. This method is applied mainly to decorations with gold and platinum.
Production is carried out using the world’s most advanced machines, such as isostatic presses, pressure die casting and mechanical glazing devices, the energy saving Riedhammer and Grün kilns and the in-glaze decoration burning kilns. The in-glaze kilns (1260°C) allow for the manufacture of products suitable for microwave ovens and dishwashers.
LUBIANA uses standardised imported raw materials: kaolin from the UK, Germany, and the Czech Republic; feldspars from Nor-
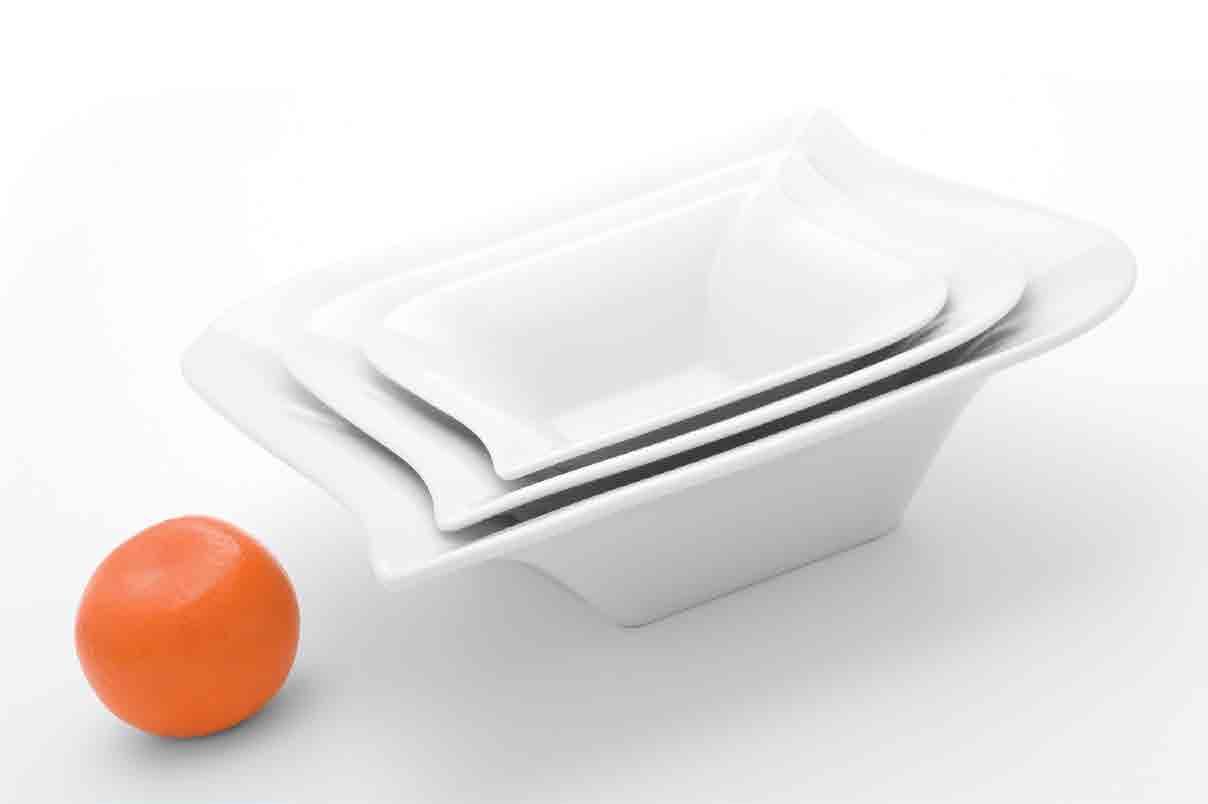
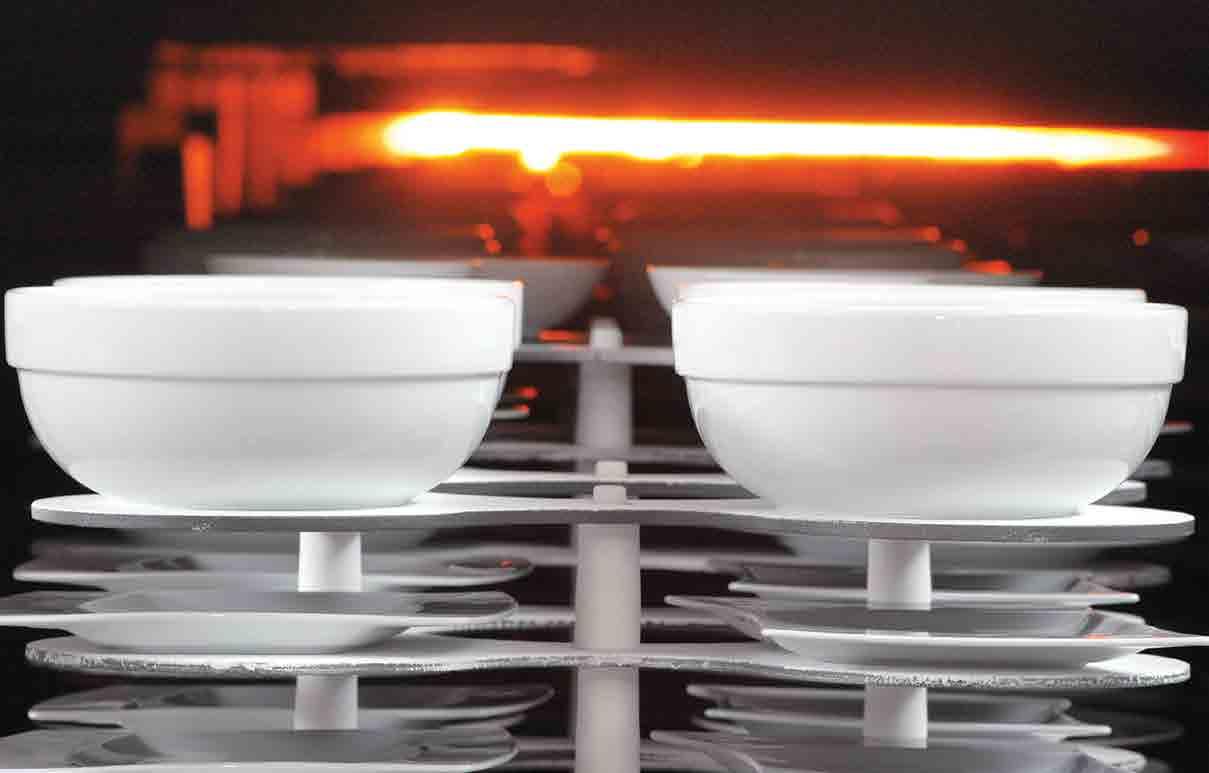
way and the Czech Republic; quartz from Norway and Germany; and plasticisers and fluxing agents from Germany. “Our partners and collaborators are reliable companies that can provide us with adequate raw materials and spare parts, as well as good logistics and services. It is worth saying, however, that the highly specialised tools we use in the production process are made by us. We have set up the ‘Implementation Centre’ specialising in the design and production of tools for isostatic pressing, pressure die casting and other forming technologies. The Centre is equipped with computer-aided design systems linked with numerically controlled machine tools. On average, we introduce a new product to the production line every three days,” says Mr Andrzejewski.
Porcelain in irregular shapes is in high demand and forces the company to invest in specialised presses and brush machines. “Generally, customers all over the world expect products with novel shapes and high quality at the same time. Such an effect can only be achieved by using the advanced technology. First and foremost, we offer our customers products of the highest quality, which are also friendly and safe to use. For us it is both: a mission and a continuous challenge. We put a lot of knowledge, technology, and a lot of heart into our products. The LUBIANA porcelain has been produced in a very modern way, but it is also the work of many people,” concludes Mr Andrzejewski. n
http://www.lubiana.com.pl/
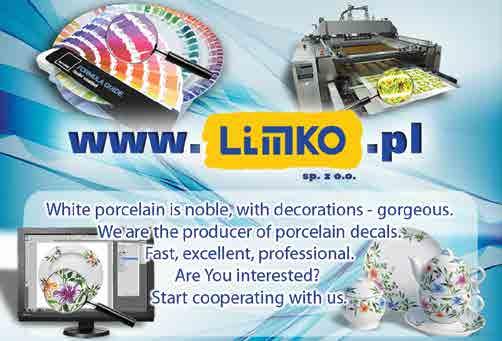
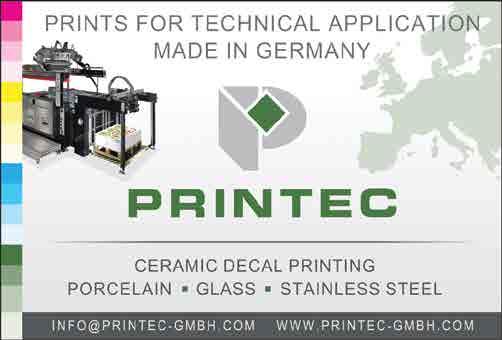