
3 minute read
Quality and diversity in steel Tazzari Group
QUALITY AND DIVERSITY IN STEEL
Automotive and much more: product diversification is the strategic driver of the Tazzari Group. With a halfcentury of expertise in the world of aluminium casting, the company utilises cutting-edge technological systems. Daniele Garavaglia reports.
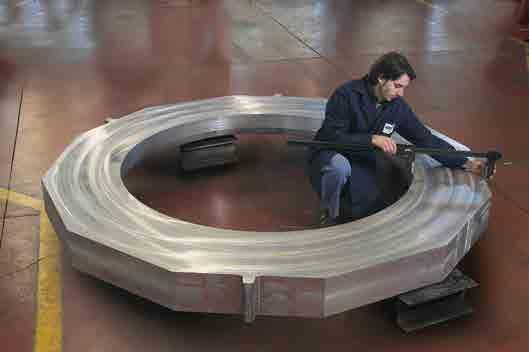
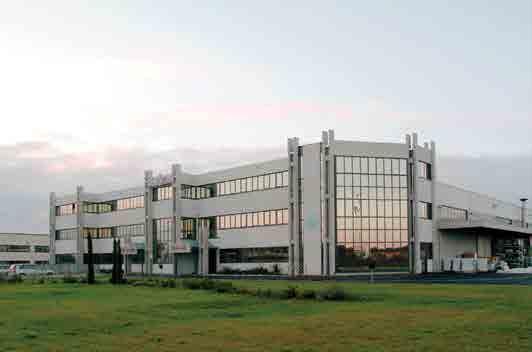

From Imola, the centre of the Italian motor sports and automotive district and home to top brands such as Ferrari, Lamborghini, Maserati and Ducati, the Tazzari Group is expanding its global business. The company employs 250 people across six production plants (amounting to a covered area of over 35,000m2), with a consolidated turnover amounting to €44 million.
The group comprises two major divisions. The first is Fonderie Alluminio Tazzari SpA, which consists of three companies specialising in: green sand and resin sand aluminium alloys (Fomet); the production of aluminium alloy gravity castings (Shell Casting); and the development of models and prototypes intended for the foundry itself (Modelleria Imolese).
The second division, integrated into the company Tecno Meccanica Imola SpA, consists of three enterprises dealing with: mechanical engineering, assembly machines, systems and components for third parties (Tazzari GL); lightweight structural metal and sheet metal working (TecnoLam); and systems for concrete pumping and distribution (Concrete Systems). It also offers innovative production of vehicles and city cars for electrical mobility, marketed under the Zero EM1 brand.
Staying strong
“In 2009, when the entire manufacturing world was in the throes of financial crisis, our turnover dropped by more than 50 per cent, plunging below €10 million,” says sales manager Fabio Cardelli. “In 2015, following a deep reorganisation and substantial investments in new technological processes and market strategies, revenues reached and exceeded €27 million.” Not bad for a family business now into its third generation, with 50 years of experience in the aluminium casting industry.
“Even in the most difficult times, we have never given up our vision: the manufacture of high-quality products. Our design approach is characterised by a constant focus on the critical aspects of development,
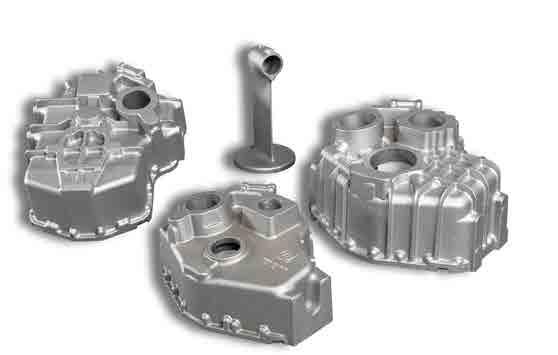
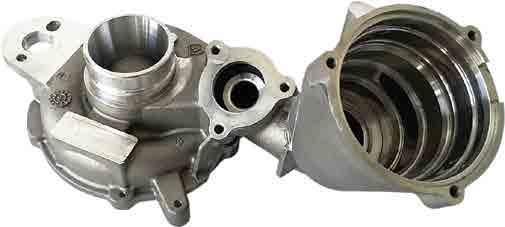

with the aim of optimising productivity, reliability and quality. We manage the entire project in-house, from prototyping up to mass production. The automation of the melting process, covering both sand and gravity castings in any size, is one of our strongest assets. We can proudly state that we guarantee cutting-edge technical standards in this industry.”
Diverse applications
The company’s product range primarily focuses on the needs of its most important target market: automotive. As for its products made from gravity-cast aluminium alloys – such as compressor housings, water pump covers, motorcycle swingarms – nearly 80 per cent are for vehicle applications, including agricultural machinery. The production of sand castings, on the other hand, is far more diversified with application in sectors such as energy distribution, shipbuilding, machine-tool production, automotive and so on.

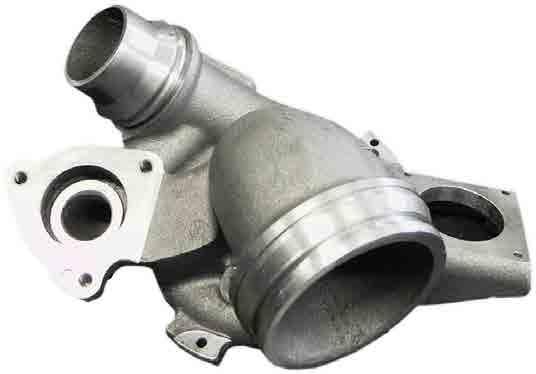
Diversification is key to understanding the continued successful expansion of the Imola-based Group, as Cardelli says: “We have always tried to propose customised solutions adapted to the different industrial fields we work with. Even within the automotive world we have so many different end users and, while yesterday our target market was Germany, today we are expanding in Italy too. As far as our products are concerned, we are always focused and specialised in compressors, but we have also developed solutions and useful components for other vehicle parts. Then, a couple of years ago, we started working successfully in the field of agricultural machines – a thriving market especially in emerging countries which require a completely different approach.”
The end users of Tazzari’s products include international groups such as Daimler, Mitsubishi, Hyundai and ABB, leading Italian companies such as Ansaldo Energia and Riello, as well as numerous small and mediumsized suppliers of automobile manufacturers and multinationals. The development strategy is well-defined: maintain a high quality production standard, with forward-looking technology and equipment, and maintain ISO 9001 and ISO/TS 16949 certifications in order to ensure the standards and performance demanded by the medium/high-end market. n

