
5 minute read
The 3D printing revolution
How long is it before we are seeing huge 3D printers on building sites rather than traditional construction teams? According to Maurizio Andreoli of the Italian WASP Project, which is focused on the development of 3D printing technologies for sustainable development, that day may not be so very far off. Victoria Hattersley reports.
Across the global construction industry we are seeing an ever-increasing interest in green construction – not least because of the significant savings it offers compared to traditional construction methods. So what if, in the future, houses could be 3D-printed using locally sourced raw materials at a fraction of the current production and environmental costs? This is the aim of the WASP initiative: led by the Italy-based 3D printing firm Centro Sviluppo Progetti (CSP), it was created in 2012 to manufacture professional 3D printers inhouse in order to encourage sustainable development and in-house production.
To this end, WASP is studying new materials to utilise in the printing process, leading to the innovative use of straw, clay and porcelain, amongst others. The project’s first 3D printer was the PowerWasp – a versatile machine that also allows the shaping of aluminium and wood. This was followed by the current 12m DeltaWasp line, which is adaptable to every 3D printer requirement and can be used for both small and large projects.
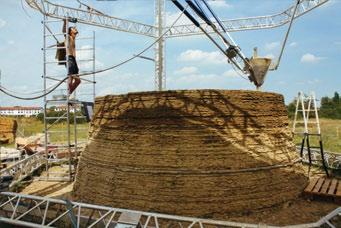
The benefits
But why exactly can the kinds of 3D printing technologies developed by projects such as WASP can potentially revolutionalise the construction industry? Mr Andreoli explains: “For one thing, it is extremely efficient: the client’s project can be perfectly realised owing to the precision of the mechanical process and customisable designs can be easily achieved using geometric modeling softwares. We can create cavity walls that are impossible to obtain with traditional techniques, and the aeration canals could be utilised for air circulation, air conditioning and air heating systems.”
There is also, of course, the matter of cost and environmental savings. Using a mixture of straw and natural terrain and its in-house developed extruder, WASP can
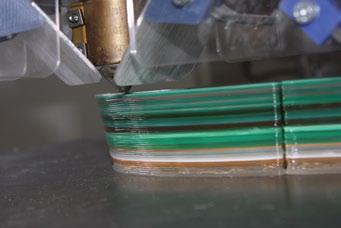
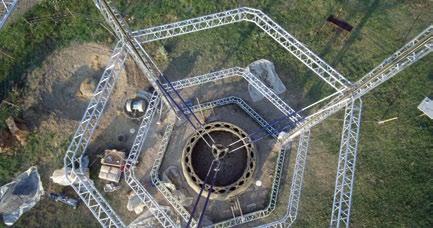

obtain a fibre-reinforced composite-like material with around half the material consumption of traditional building methods.
Mr Andreoli continues: “Our aim is to create micro-independent communities, born and developed on community knowledge thanks to advanced self-production systems that anyone is able to achieve. The 3D printing process will allow us to realise the goal of the no-debt house – a house which offers more freedom to people and in fact produces energy instead of using it. A living solution at zero costs able to satisfy all basic human needs: house, food, energy, health, jobs, culture. This type of building technology can also be helpful in cases of humanitarian emergencies caused by economic or political crises or natural disasters.”
Significant achievements
There have already been several examples of WASP’s 3D printing technology in action. Last year, a collaboration with the Siam Cement Group (SCG), the largest cement manufacturer in Thailand, saw the development of the first 3D printed house in Asia. The project, called ‘Helix: The Family Cocoon’, involved the creation of a small shelter imitating a natural shell structure.
The Hermitage shelter project, meanwhile, is a versatile and reproducible model of shelter with almost zero environmental impact using locally sourced materials and rapid prototyping machines of CNC. In its search for a combination of advanced technology and the use of natural resources, WASP has developed what it calls an ‘architectural archetype’ – the result of a multidisciplinary project converging the skills it has developed from a number of sectors including: renewable energy, furniture design, research on hydroponics and vertical gardens.
Hermitage houses are what WASP describes as a ‘passive’ architectural model “because they are able to meet most of their energy needs with passive devices, capable of producing energy instead of consuming it.” Built using only natural materials (earth, straw, lime and stand) found in the local territory, which are completely reusable and compostable at the end of their life, this sustainable architectural model leaves no waste.
ongoing project
One of the most significant projects in which WASP is currently involved is an experimental eco-village at Massa Lombarda (Ravenna), around 50km from Bologna, using soil and straw. This village represents the pinnacle of everything the project has been working to achieve up to now: sustainable housing construction with locally available materials at the lowest possible costs. 3D printing the world’s first ever soil and straw building has been a challenge, but Mr Andreoli says WASP is very encouraged by the results so far: “We have already proved that two men and one machine can 3D-print a comfortable and healthy shelter with extremely little money. We are very satisfied with the results, even if we know there is still a lot to do in the future.
“The main goal was to develop an extruder to lay down scores of mixtures, to verify if the machine mechanism was able to stand continuous material deposits, to supervise the extruder during the printing phase, to face printing interruption and recovery, also connected to material pickup, to protect the wall from the rain in case of storms, and more. These are just some of the difficulties we have faced and solved.”
Looking ahead, WASP will continue to test new materials and carry on its research into 3D printing with soil and straw. Mr Andreoli concludes: “New challenges in the improvement of systems for cheap and fast material preparation are coming. The printer is doing its job and after the last changes in kinematics we will modify something in the extruder too. The aim is to automate the system to enable the machine to print a shelter in a few days.”
WASP is still in the prototype phase of its work and clearly there are still regulatory and quality control issues to be addressed. That being said, given the way technologies are developing it is not unrealistic to believe we may be seeing the first commercially viable 3D house-printing technologies on the market before 2020. And from then on, there is no end to the possibilities. n
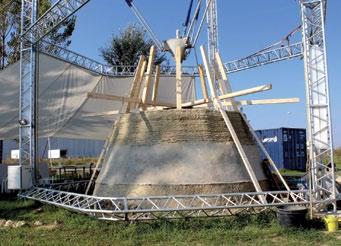