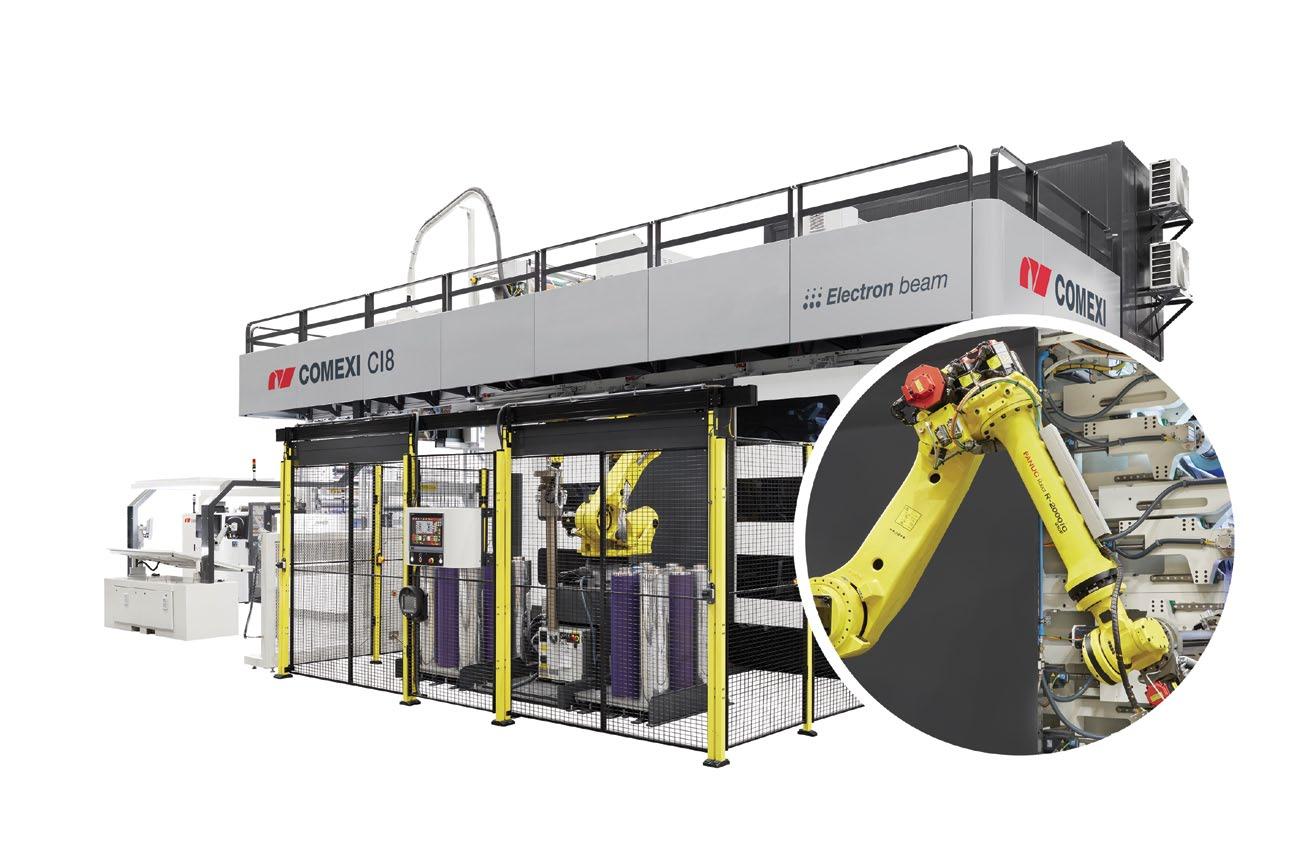
5 minute read
Flexible and innovative Chemosvit
FLExIBLE AND INNOVATIVE
Slovak Chemosvit Folie is a member of the Chemosvit Group, one of the largest businesses in the Slovak Republic. Over the past few years, Chemosvit Folie has successfully established itself as one of the leading flexible packaging printers in central Europe and has recently invested in new technology with a view to further strengthening its market position. Romana Moares reports.

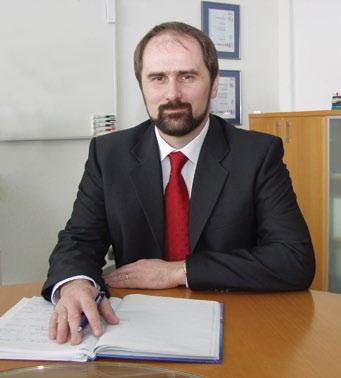
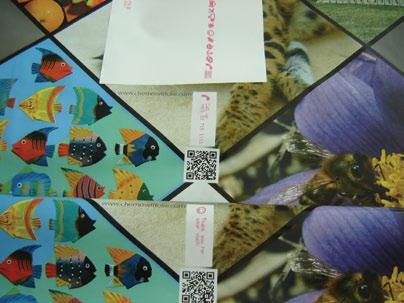
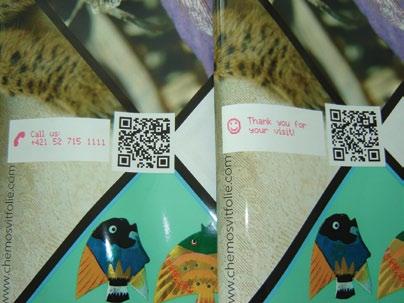
Chemosvit Group consists of a group of companies involved in the production, converting and sale of flexible films intended for packaging and the electro-technical industry. It also focuses on the production and sale of plastics, recycled plastics, polypropylene yarn, machinery and packaging machines. Furthermore, its business line includes: technical services, power production and distribution, forwarding, transport and hotel services. The group has manufacturing sites located in Slovakia, the Ukraine and Finland.
Chemosvit was established in 1934 by Tomáš Baťa, one of the most prominent business figures and industrialists of that time, on a green field site under the peaks of the High Tatras in northern Slovakia. The plant housed the first production of viscose films in Europe and the second in the world (after the USA). In the 1930s, the company was regarded as one of the most progressive in the world, with a great emphasis on satisfying both the customer’s and employer’s needs – reflecting the business philosophy of its founder and owner. This philosophy has been inherited by later generations of workers and has remained a pillar of Chemosvit’s development throughout the 20th and early 21st centuries.
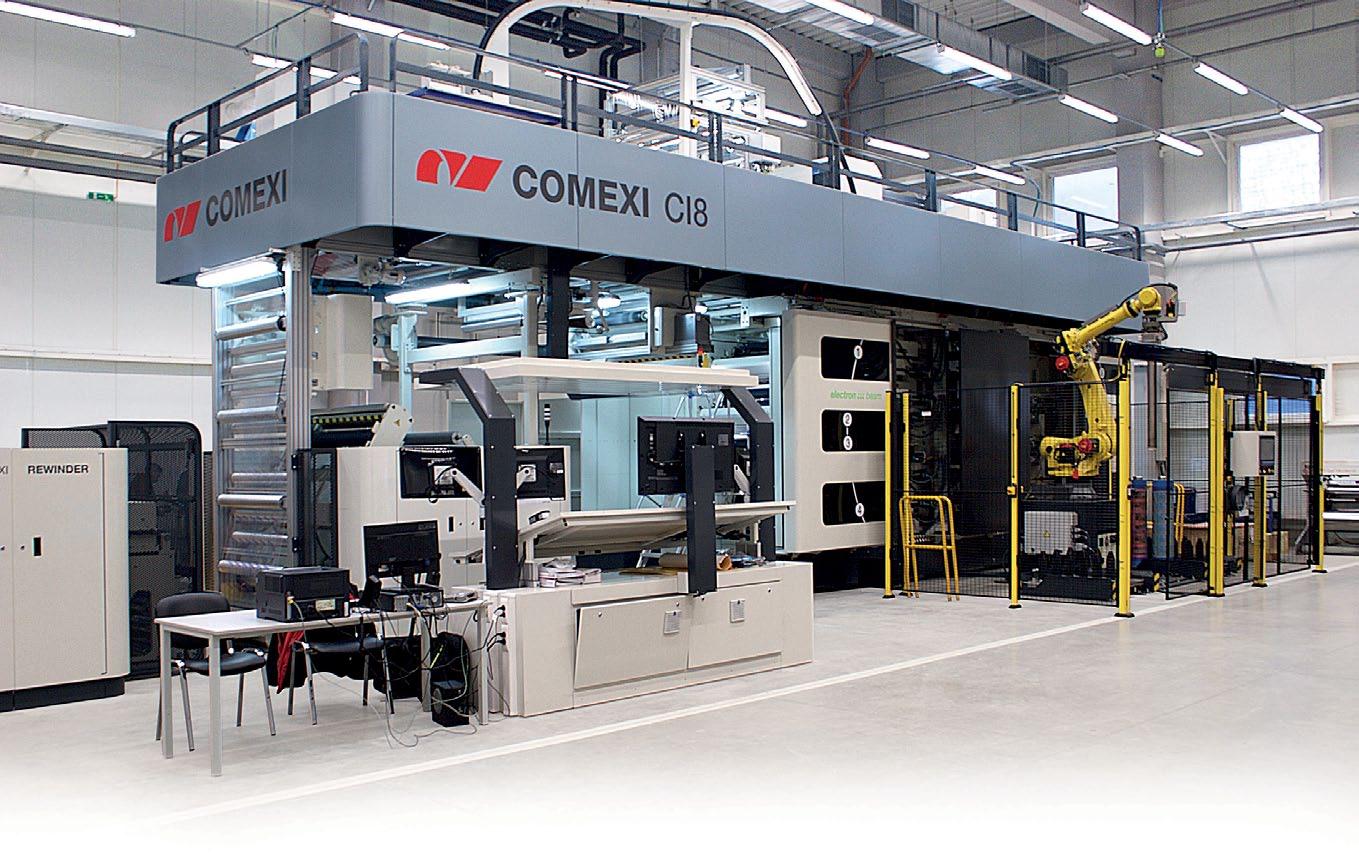
member of a strong group
Chemosvit Folie houses the group’s conversion lines for its in-house manufactured coextruded polyethylene, polypropylene and barrier films, as well as of purchased BOPP, BOPET, OPA, aluminium films and cellophane. The company, fully owned by Chemosvit, was established in 2005 by separating the business from the parent company, and its activities include rotogravure printing using up to 11 colours, flexoprinting using up to 10 colours, lamination, winding and slitting, sealing and adhesive binding (production of various types of pouches and carrier bags). The company has its own graphic studio and facilities for the production of printing forms for rotogravure and flexoprinting technologies. Its core product is packaging film for the food industry, used mainly for wrapping sweets and biscuits, as well as for the packaging of fresh and frozen food products. Its products are also supplied to other segments, such as the toiletries and pet food sectors. Other products made by the Chemosvit Folie include flexible films, the design and production of printing plates and various flexible film products. However, the biggest percentage of sales comes from its rotogravure cylinder production and lamination. As Slovakia is a relatively small market, about 85 per cent of the company’s output is exported, mainly to EU countries such as Germany, the Czech Republic and the Netherlands. Only small quantities are shipped to non-EU countries such as the neighbouring Ukraine, where Chemosvit operates another small production plant in the western Ukrainian town of Luzk.
First class technology
The plant is housed in five factory buildings within Chemosvit’s huge industrial complex, and is steadily being modernised to improve workflow and to further increase production efficiency. Massive investments have been made into state-of-the-art technology with a view to increasing its base of prestigious customers, which today includes a number of global players.
In 2012, the company installed a new 11-colour Heliostar rotogravure press, followed by a new 5-layer blown line in 2015. “Invest-
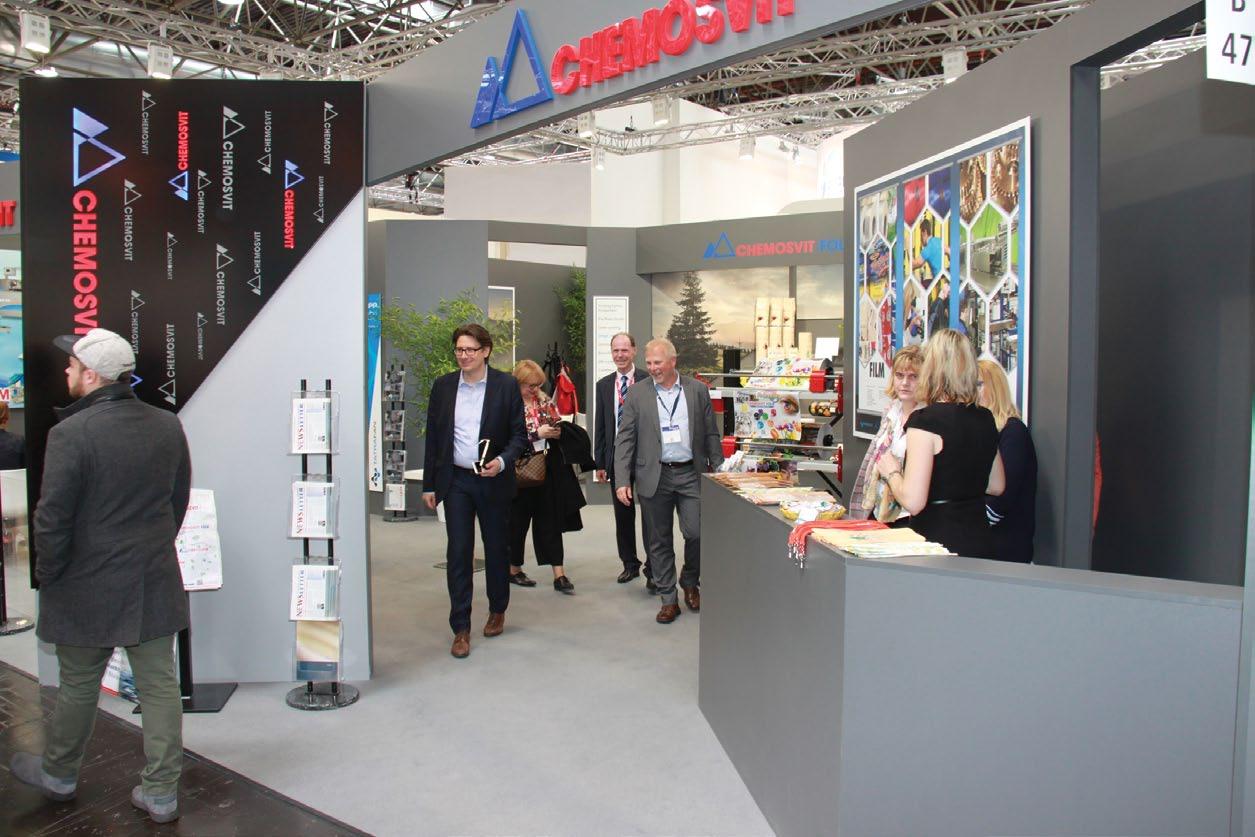
ment in new technology is an on-going process,” says managing director Jaroslav Mervart. “Each year machines are either bought or modernised. Last year we installed a new Kampf slitting line, an additional Comexi laminating line and an offset printing machine – all significant additions to our existing technology.”
The company presented its new technology at interpack 2017. “There was great interest in our new e-beam offset,” confirms Mr Mervart. “Our philosophy is to inform the general public and potential new customers of the advantages and possibilities of printing directly on films,” he explains, adding that ever since the natural disaster in 2004 in the Tatra mountains, when a large part of the forest was destroyed by a massive storm, each tree is valued and the company strives to eliminate any unnecessary paper wastage.
Focus on innovation
The managing director further highlights the advantages of the patented Comexi technology: “It features a central drum printing, allowing for the printing of tensile materials. The last station is flexo-
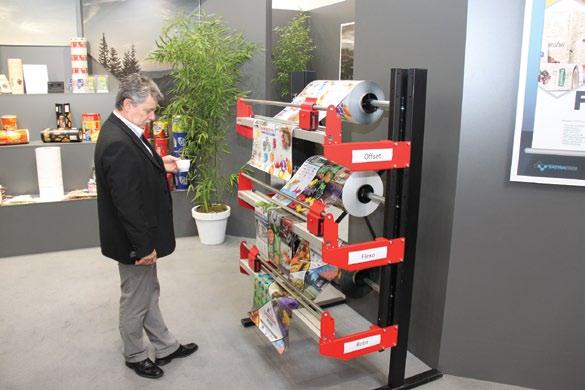

printing, so white colour and special varnishes can be deposited here with sufficient covering power or special effects.” The development of offset printing of plastic films suitable for small jobs has progressed rapidly in the past few years. Customers often want their new packaging quickly introduced to the market. They want a small volume, but in rotogravure quality. Offset can meet this demand. A focus on innovation has been one of the aspects behind the company’s success. “We were among the first to introduce rotogravure printed winning codes to the market for direct contact with food. We have solved the issue of UNI code printing on laminate with cold-seal. This year, we can offer simultaneous printing of not only 2-line winning text but also of various pictures. We believe this news will attract our customers’ attention,” says the managing director in conclusion. n
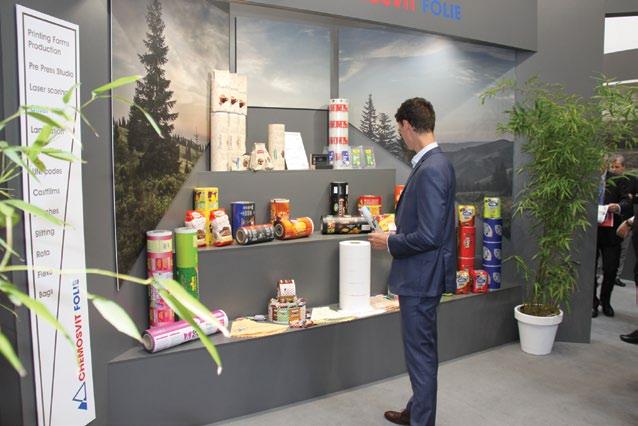

Comexi
Comexi’s offset technology it’s being in the market since 2014 with more than 15 presses sold around the world. Comexi’s offset Sales Director, Felip Ferrer, highlights that Chemosvit is a reference converter with a wide sales network all abroad europe. “They stand out for their exigency and professionalism; it is really relevant that they have invested in our Comexi CI8 offset press, as a complementary technology for their flexo and gravure presses”, emphasizes Ferrer. “We will help them with everything they may need to make this technology as successful as possible for them and for all their clients”. In this sense, Ferrer assures that Chemosvit will improve its competitiveness and attract new customers thanks to all the improvements this technology offers like its high quality printing, production flexibility and better time to market.