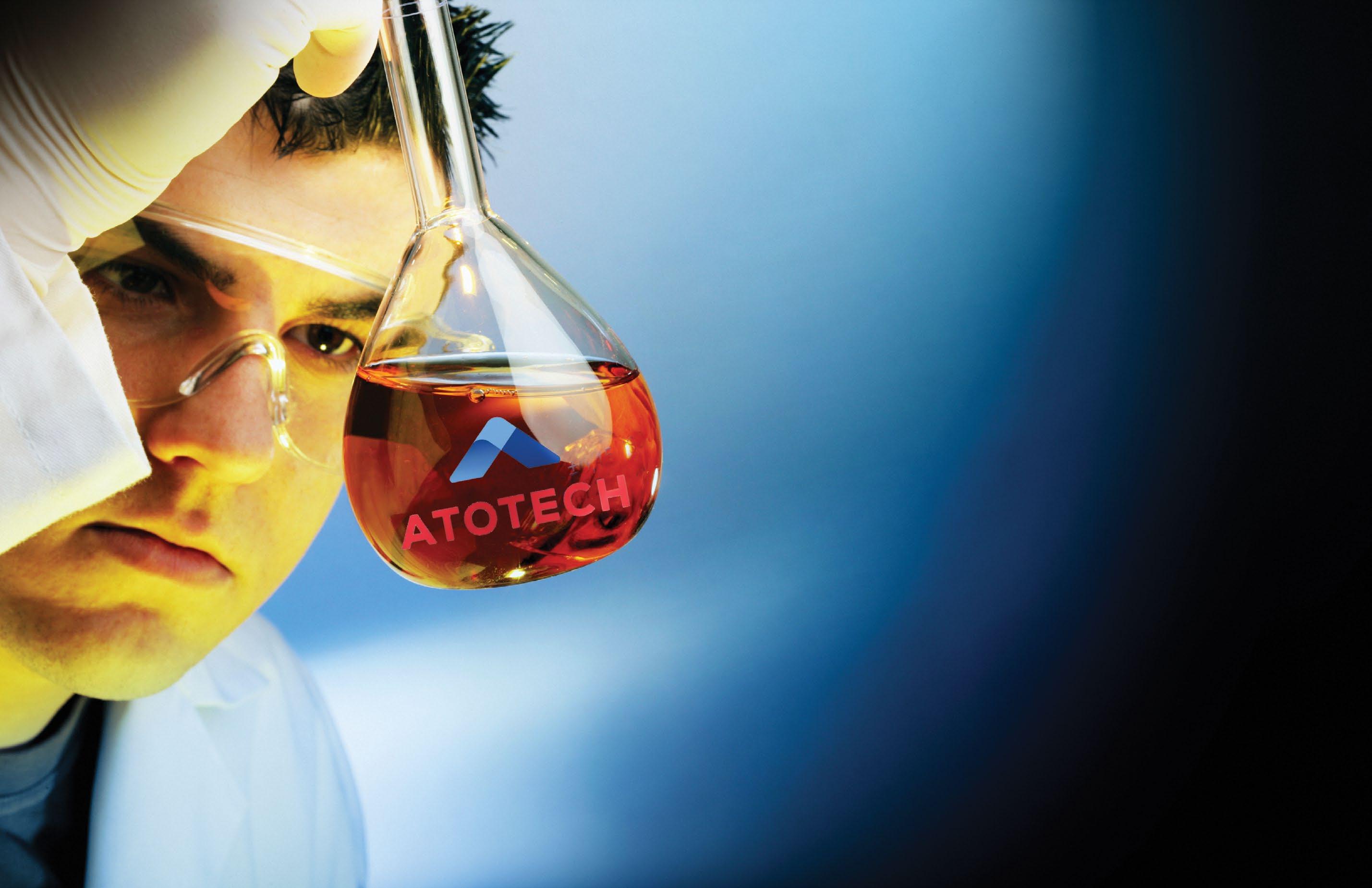
4 minute read
Yielding more Atotech

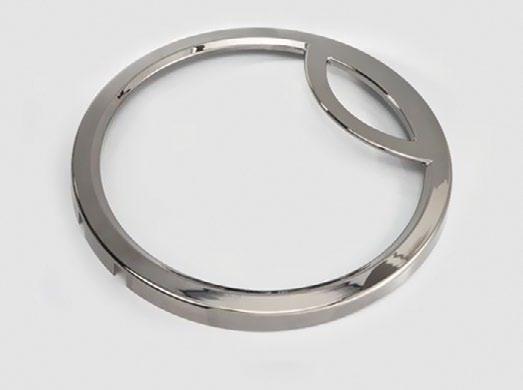
yiElDing morE
Atotech is the global market leader in the production of electroplating chemicals, equipment and services. Its relentless R&D efforts, combined with its worldwide TechCentres, enable it to offer pioneering products and unparalleled on-site customer support, thus making it a valuable industrial partner. Philip Yorke reports on the latest developments at this dynamic company.
Atotech’s origins date back to the mid-19th century. Over the decades several mergers and acquisitions have led the company to become the global leader in the highly complex world of electroplating chemicals. It offers equipment and plating services for printed circuit boards, package substrates and semiconductor manufacturing as well as for decorative and functional surface finishing.
Following a programme of continuous expansion, Atotech has established additional TechCentres worldwide. Furthermore, its focus on green product development has resulted in its leading the field in sustainable plating technology. In 2017, a major milestone was reached when Atotech became a fully independent, stand-alone company. Today it is the global market leader in plating technologies, generating sales of more than $1.4 billion, with more than 4000 professionals worldwide.
As the world’s leading supplier of speciality chemicals, equipment, services and solutions for printed circuit board manufacturing and advanced electronics packaging, it offers unrivalled expertise in both decorative and functional surface finishing. The company’s core business units include electronics and general metal finishing, as well as others that cover semiconductor technology and electronics materials. These new technologies are playing an increasingly important role in the future growth of the company.
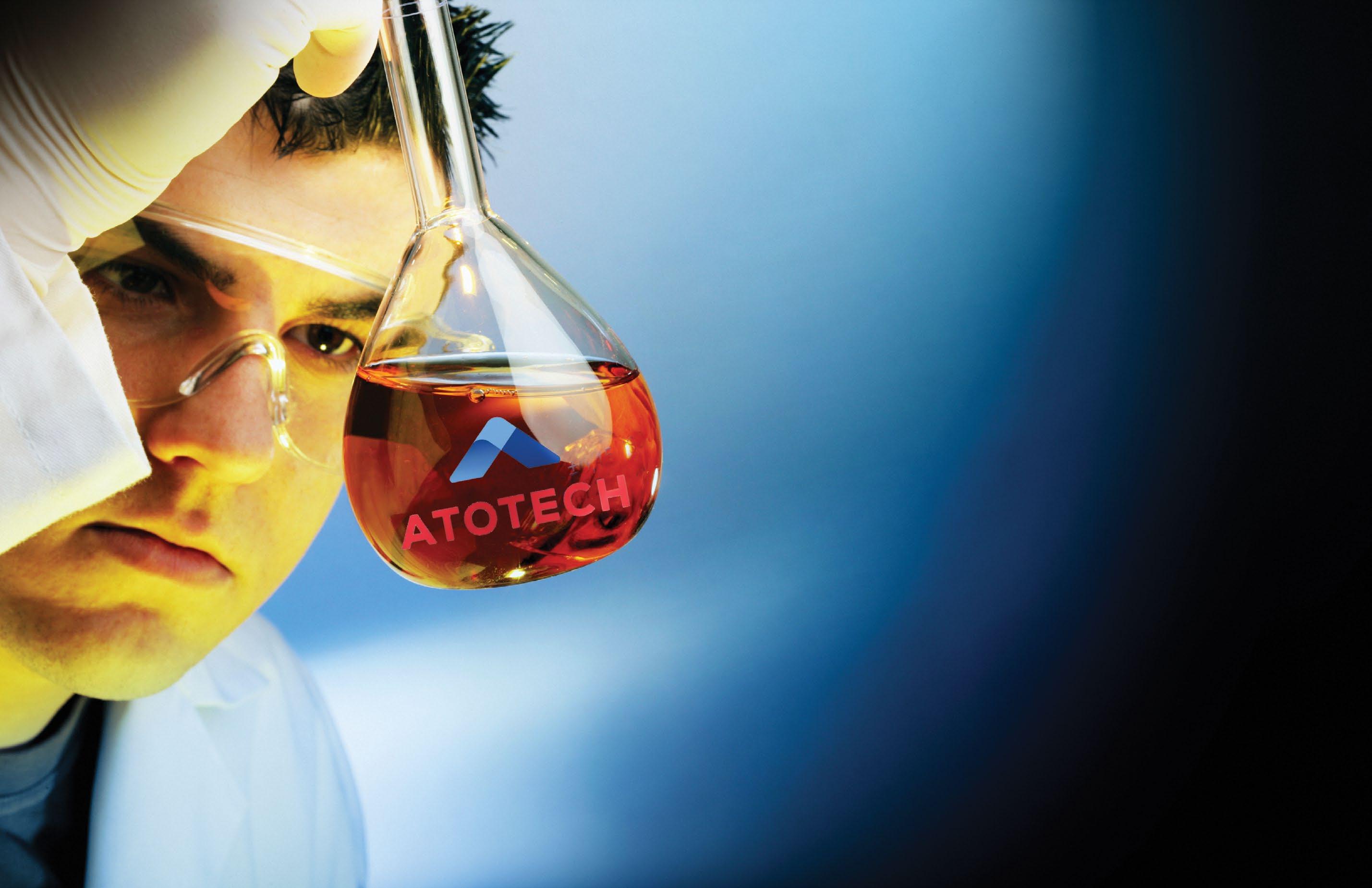
Higher yields, longer life
Atototech continues to set new standards for the production of higher yields and more sustainable processes with longer life. Recently the company unveiled its latest regeneration system, Satilume® LongLife, which combines its well-known Stilume® Plus, with advanced filtration and dosing equipment. Its continuous electrolyte filtration and optimised, fully automated additives dosing systems help stabilise the process and allows for uninterrupted manufacturing, thus enabling production increases from several hours up to five days with no further maintenance required.
In addition to ensuring constant and stable satin nickel finishes with improved quality and appearance, Satilume® LongLife also
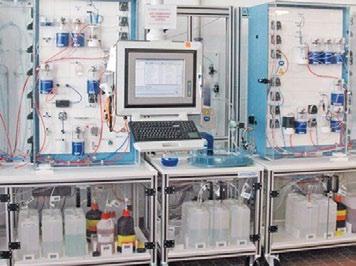

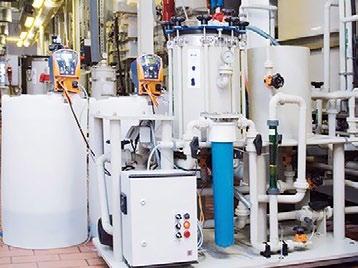
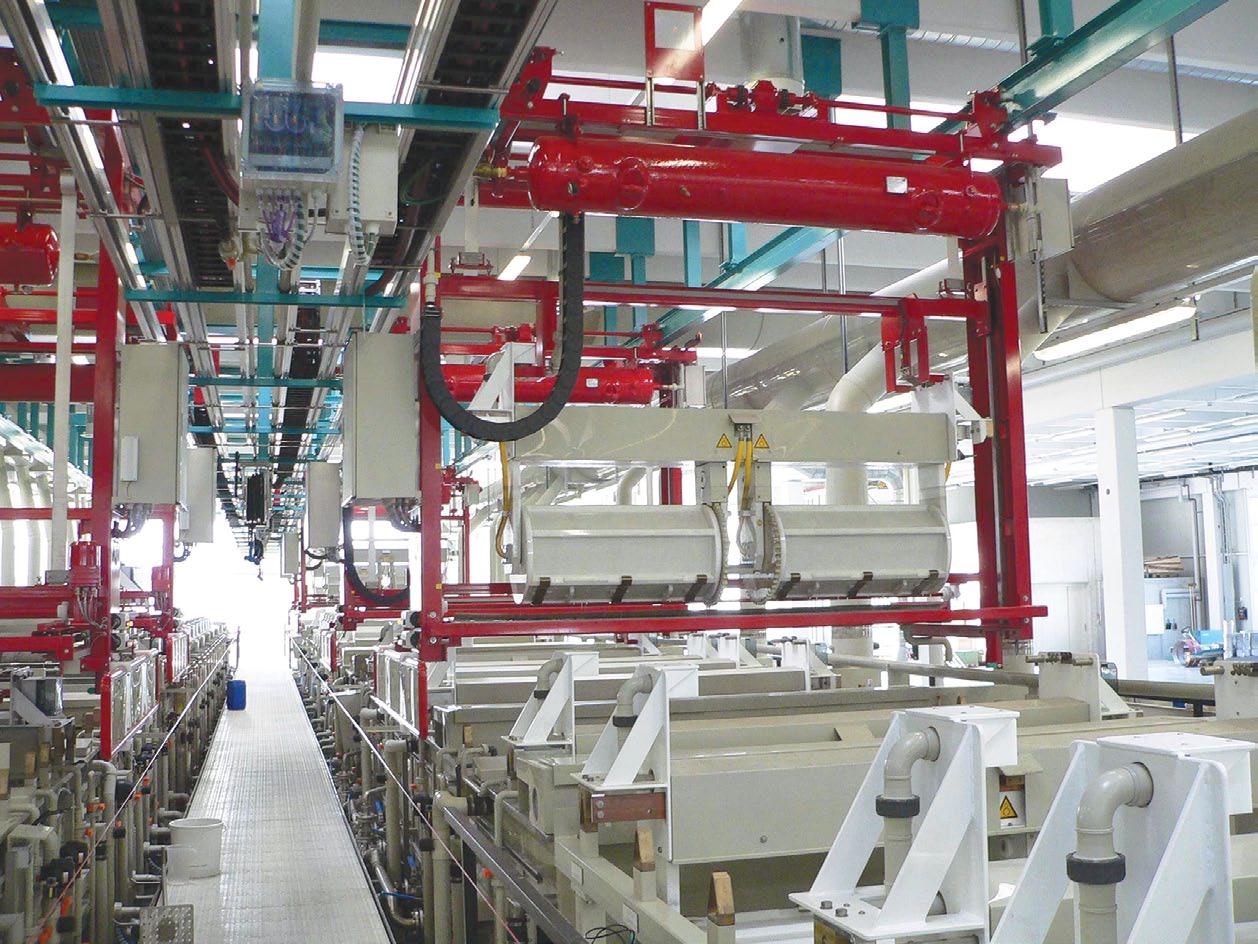
increases the plating capacity of existing plating lines, thus reducing the amount of maintenance required and significantly lowering rejection rates.
The company’s automated online analytics system also provides fast, simple and direct control of important parameters that influence the quality of plating processes. This fully automated online system is easily implemented in pre-existing production lines and provides consistent monitoring of the baths.
It also ensures maximum control over the line by performing a comprehensive range of automated analyses, from titration and spectroscopy to conductivity measurements. If combined with dosing units, the system can also automatically adjust the composition of the baths, extending their lifetime and preserving the high quality of the plated layers. With prompt analyses results, the entire plating process can be effectively maintained at consistent, optimum conditions, resulting in higher material and production yields.
In addition, by drastically reducing laboratory time, and automating the analytical control of process baths, it also allows for lower overall plating costs. For example, in order to achieve the same result manually, a decorative plating on a plastics line for automotive parts with 14 process steps and 40 parameters requires 17 hours of manual work.
Another important plating process is one that improves nickel plating profitability, which today can be achieved in a more sustainable way. Atotech’s HELIX® or ‘Highly Efficient Long-ion Exchanger’ is the next generation of ion-exchange systems designed to recover nickel from the rinse water of the company’s semi-bright, bright, satin and microporous nickel processes. It provides advanced nickel recovery that results in higher efficiency and higher generated nickel concentrations from the rinses.
Worldwide R&D network
Alongside the world’s leading manufacturers and OEMs, the company operates a unique global R&D network, which co-develops new production concepts to further drive innovation. Atotech’s global
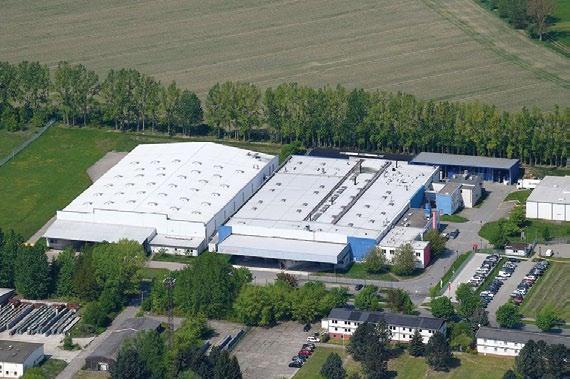
R&D teams seek out new paths and set the benchmarks for the development of sustainable plating processes. The success of these commitments can be measured not only by the increase in sales, but also by the increasing number of Atotech patents. The company maintains close partnerships with its OEM customers as well as its tier one and two manufacturers, in addition to institutes, universities and other notable research bodies.
Innovation-driven success
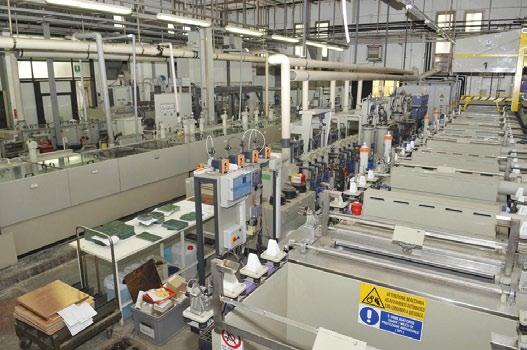
Atotech has an enviable reputation for its innovation-driven culture, which is designed to keep the company well ahead of its competitors. Currently Atotech has over 2000 worldwide patents in force. These have been developed at its many R&D centres worldwide, as the company continues to commit over 10 per cent of its annual sales to research and development. This is to ensure that it will always have the most advanced, sustainable products and processes at the disposal of its customers.
The regional headquarters of Atotech are located in Rock Hill (USA) and Yokohama (Japan) and are supported by over 40 regional service centres of which 18 are specialised technical centres that provide advanced analytical and technical support. With 14 production plants for chemistry and two for equipment, Atotech can be relied on to provide fast, on-time delivery worldwide. n
For further details of Atotech’s innovative products and services visit: www.atotech.com
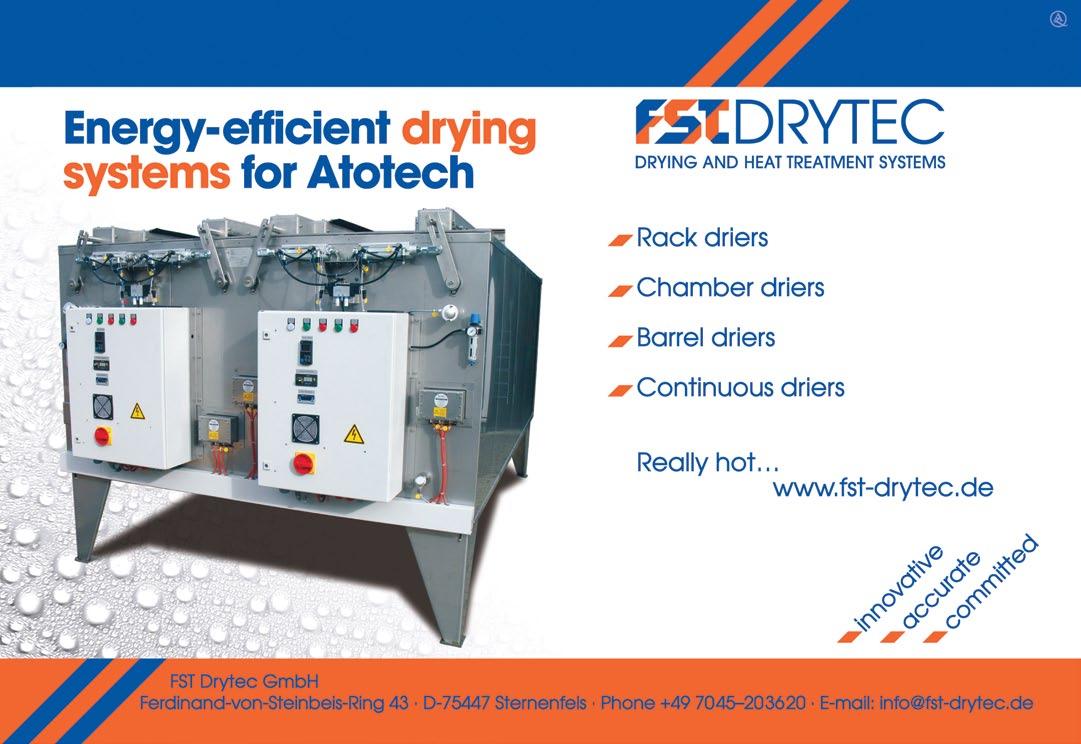