
4 minute read
Reinforcing perfection Feralpi
reinforcing perfection
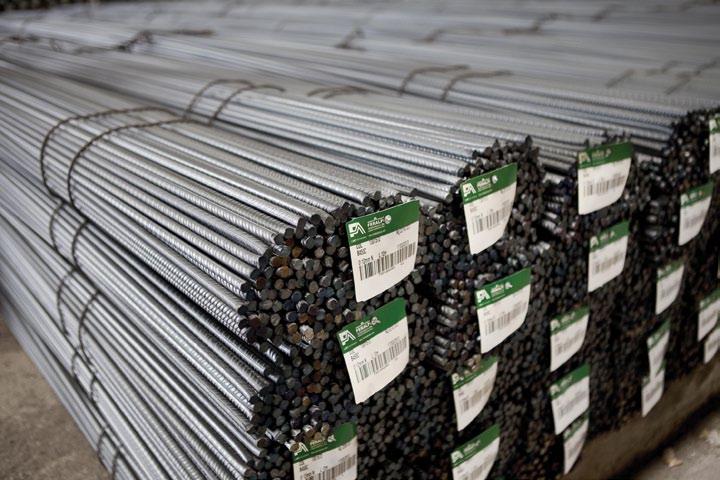
The Feralpi Group is one of Europe’s foremost steel producers and specialises in the manufacture of steel for the construction industry. The group is best known for its reinforcing steel bars, and wire rod and mesh products. However, Feralpi stands for so much more than speciality steels, as Philip Yorke reports.
Feralpi Siderurgica was founded in 1968 in Bresica, Italy and its continuous development has resulted in a steel metals group that currently produces around two and a half million tonnes of steel and rolled products a year. In over 50 years of business the company has expanded into foreign markets and currently employs more than 1,500 people worldwide.
With its strong presence in the iron and steel industry, Feralpi has diversified into the development of innovative new products and new markets through organic growth and strategic acquisitions. Today the Feralpi Group also deals in special steels for cold working, structural steelwork, the environment and fish farming, in addition to offering financial consultancy services and shareholder management support.
From the outset, Feralpi has not only focused on manufacturing the highest possible quality construction steels, but it has been committed to doing so by using the best technologies available and patenting new solutions resulting from its extensive investments in research and new product development.
Greener innovation
For the Feralpi Group innovation is seen as the engine of growth and as such is an important element of its business strategy. The company is dedicated to the search for competitiveness that requires projects that pursue tangible sustainability. This entails achieving optimal technical performance by reducing energy consumption and CO2 emissions, whilst increasing standards in a continuous programme of improvement.
One perfect example of this strategy can be found in the company’s “Green Stone 2” project, which transforms EAF slag from harmful waste into a useable green by-product. The process of dross was developed in collaboration with a specialist independent company, and it now makes it possible to transform the slag waste into by-products known commercially as “Green Stones”. These are used widely in the construction industry in place of materials from non-renewable sources.
Following controls by an international certification body, all “Green Stone” by products were given the CE2 marking according to specific UNI EN standard ptotocols.
making Whaves
The Feralpi Group is also a co-partner in a pioneering heat recovery programme called “Whaves” (Waste Heat Valorisation for more Sustainable Energy-Intensive Industries. Awarded by the Sustainable Industry Low Carbon scheme (CIP-SILC) initiative, the programme is aimed at supporting industrial processes in pursuing a reduction in greenhouse gas emissions, while maintaining a clear competitive edge. The important SILC initiative contributes to the achievement of the strategic objectives and energy efficiency established by the
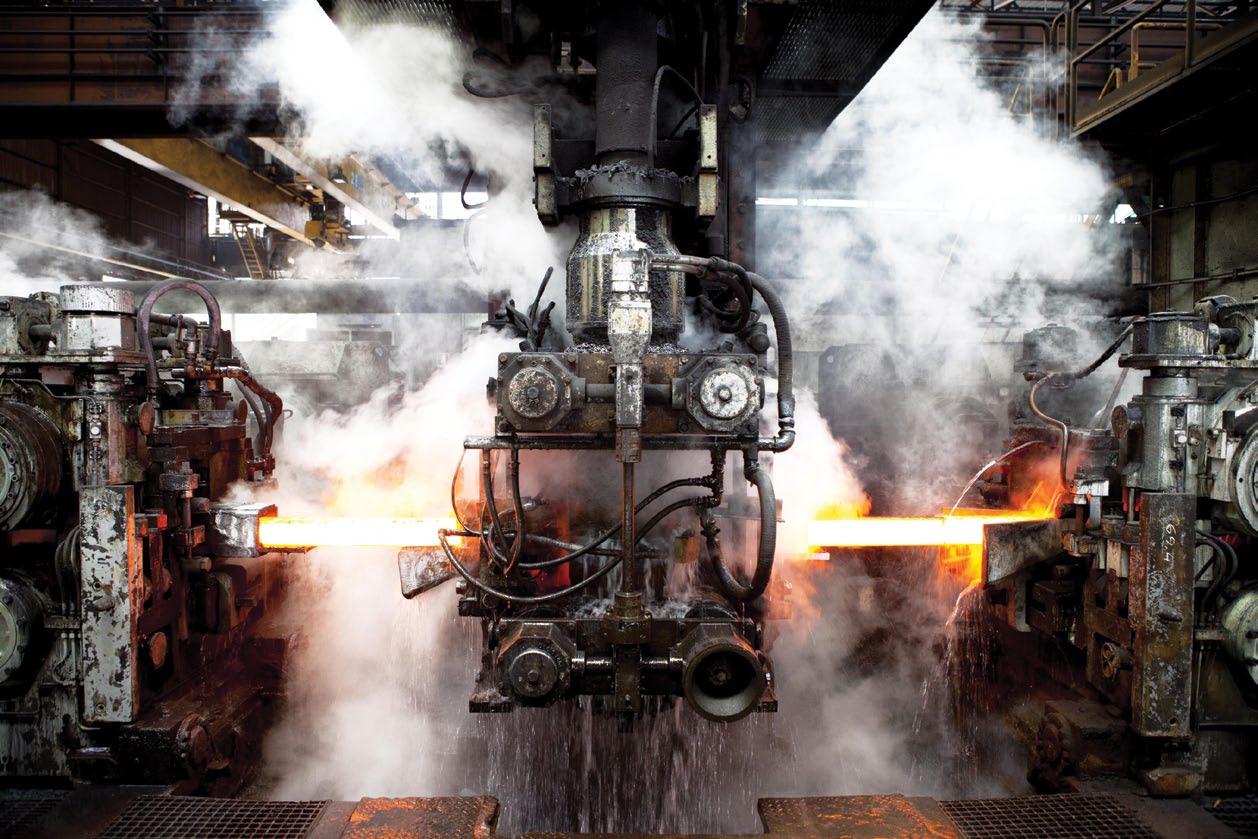
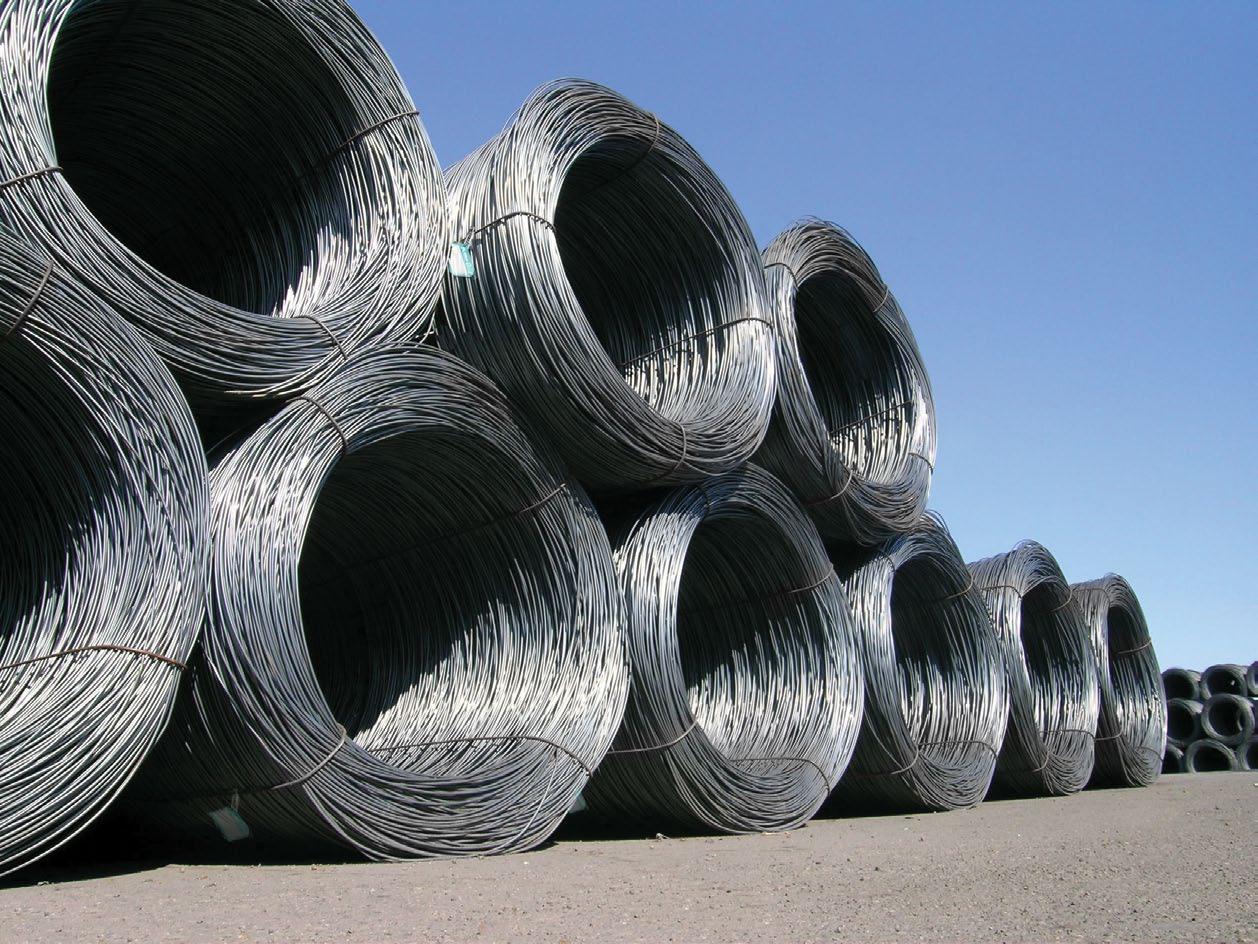
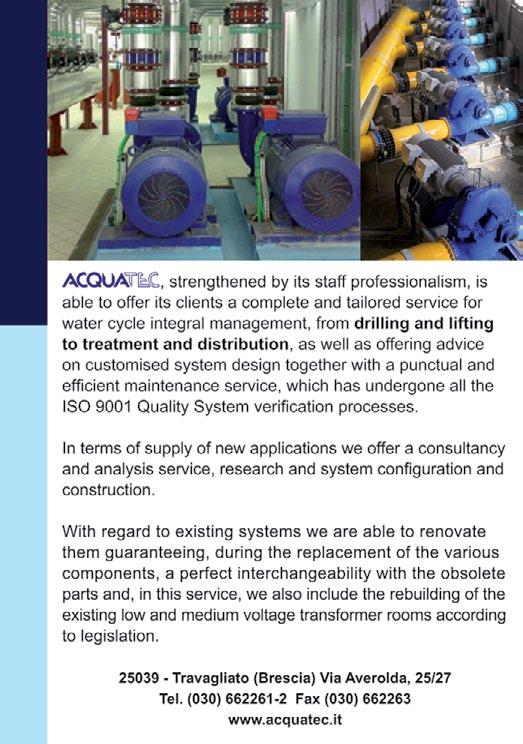
European Union. The first prototype of an EAF heat recovery system using ORC technology was developed at the Feralpi Group member company ESF, at its modern steel mill in Riesa, Germany.
The new advanced heat recovery system can be used in many industrial processes, thus contributing to their sustainability and competitive edge. The impact of this system at a European level has a potential to reduce emissions by more than 6 million tonnes of carbon dioxide a year, which requires investments in European technology estimated at around €8 billion.
Stronger French connection
The Feralpi Group company, ‘Presider’, is a Turin based steel manufacturer with a global product portfolio. The company has recently invested in a major new manufacturing plant in France in order to strengthen its
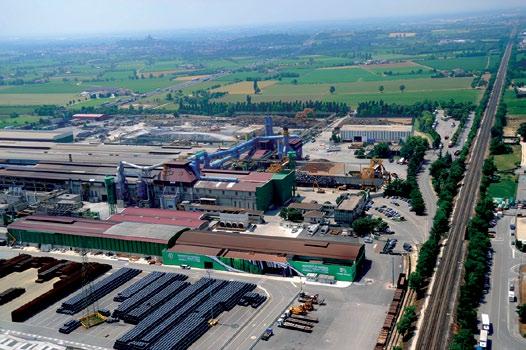
sales in both Mainland Europe and Eastern Europe. Presider is now able to serve its customers from its new Parisian headquarters, which places it even closer to its French customer base. The investment is considerable, with a purpose-built state-of-the-art facility that covers over 37,000 square metres, much of which is dedicated to its new production lines.
Thanks to its new Parisian headquarters, the Feralpi Group’s subsidiary, Presider will be able to tap into and better serve some of the country’s most prestigious infrastructure projects. These include the Grand Paris Express, a Parisian network project consisting of four regional automatic subway lines that loop around Paris with a total track length of more than 200km.
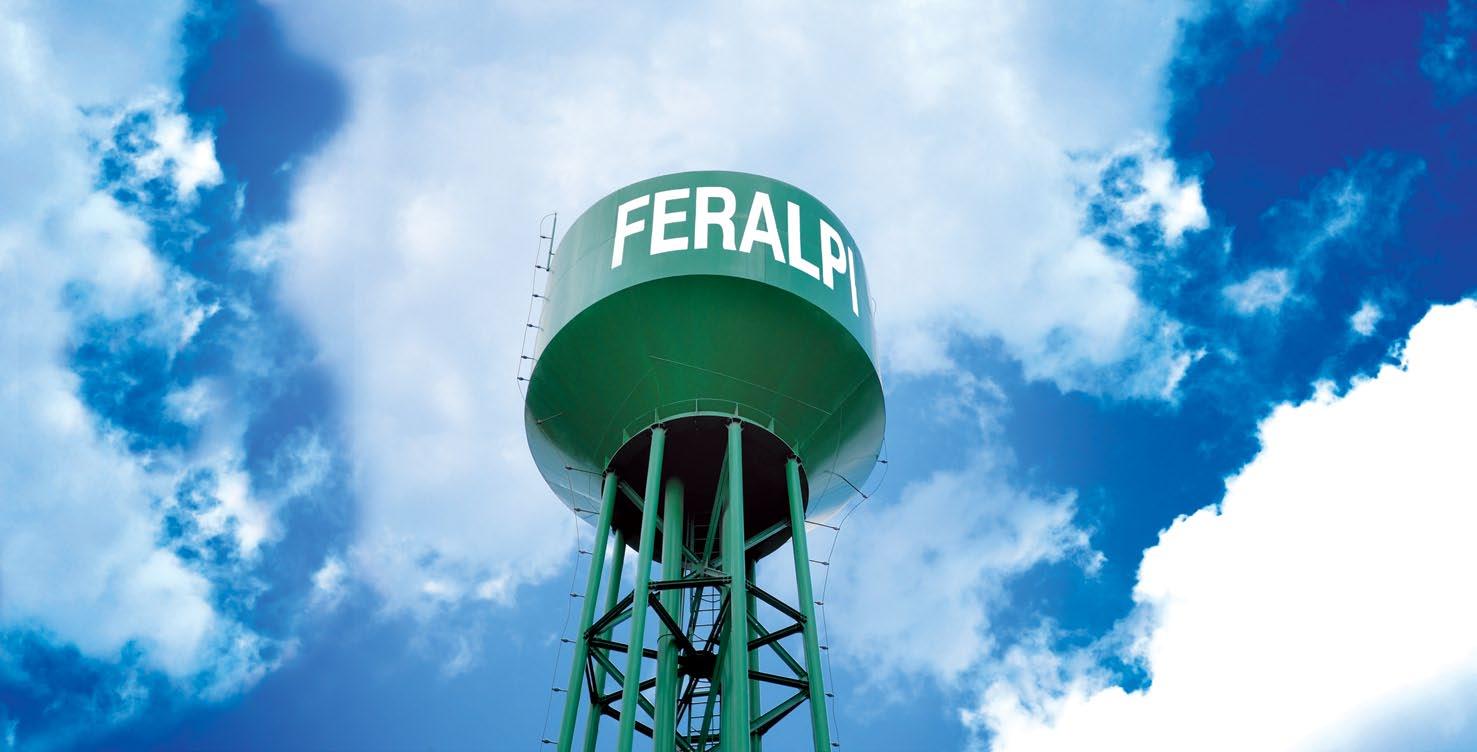
Hot topic
In order to optimise the production processes at its two rolling mills at Feralpi Siderurgica, an innovative, “Hot Charge” project was conceived to optimise productivity and energy efficiency.
Major investments were made at Rolling Mill One in Lonato del Garda to install roller systems for conveying billets from continuous casting straight to the heating furnace, in addition to the complete remaking of the core heating furnace.
This has made it possible to considerably reduce the holding times of the billets thus leaving the continuous casting machine free to be fed to the rolling-mill heating furnace, and to feed them at a temperature of around 650C, instead of the usual ambient temperatures.
The final results certainly justified the big investment in Paris. Benefits included a significant reduction in natural gas consumption, a major reduction in electricity consumption, increased productivity and a considerable reduction in the release of direct CO2 emissions. n For further details of Feralpi Group’s latest innovative products and services visit: www.feralpigroup.com
