
5 minute read
Creating more versatile deposition modelling Haidlmair
creAting more versAtile Deposition moDelling
Haidlmair is a global market leader in the field of injection moulding. It specialises in the production of packaging, thin-wall containers and stackable crates and pallets. The company is renowned for its high-tech, innovative processes. Philip Yorke reports on Haidlmair’s latest ground-breaking technologies.
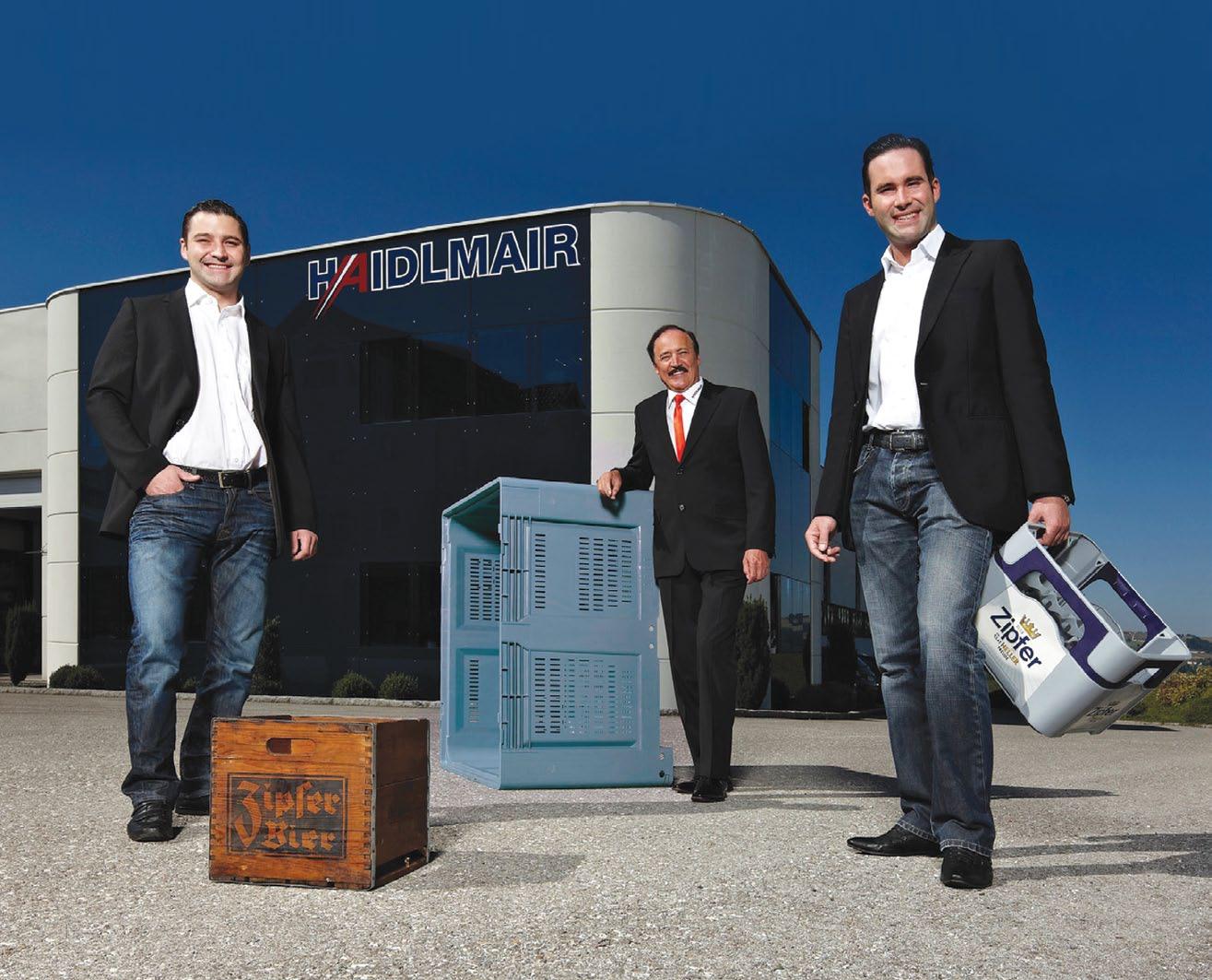


Founded in 1978 in Austria, the company has seen consistent growth over the years and has become a global market leader in its chosen disciplines. Today these include the production of advanced, high-tech injection moulds, thermoform moulds, automation tooling and component manufacturing. Haidlmair is a worldwide Plastics Technology company with 9 locations in North America and Europe. New Hot Runner System
Since 2017 Haidlmair has been committed to a long-term investment programme. However, it has not only invested in additional machining capacities, but has also built up injection moulding digitalisation know-how through the acquisition of the leading software developers Dataformers, based in Linz, Austria. Together they developed the Mould Monitoring 4.0 sensor system.
Beyond this, the most important innovation has been the investment in the industry’s largest computer tomography scanner for measuring sample parts. This has helped to close the last gap in the company’s full service portfolio, from the customer’s product idea through to the moulded part. Another recent Haidlmair innovation, which has now achieved production maturity, is the FDU (Flat Die Unit) hot runner system. A representative overview of the benefits resulting from this breakthrough is reviewed here and more details can be found on the company’s website: www.haidlmair.at.
The future today
Haidlmair’s adoption of Industry 4.0 management also necessitates Mould Making 4.0, which in turn is an important prerequisite for
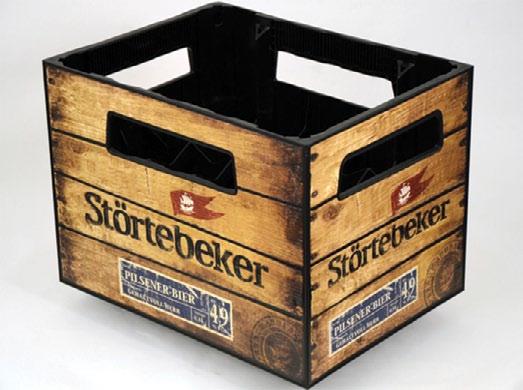
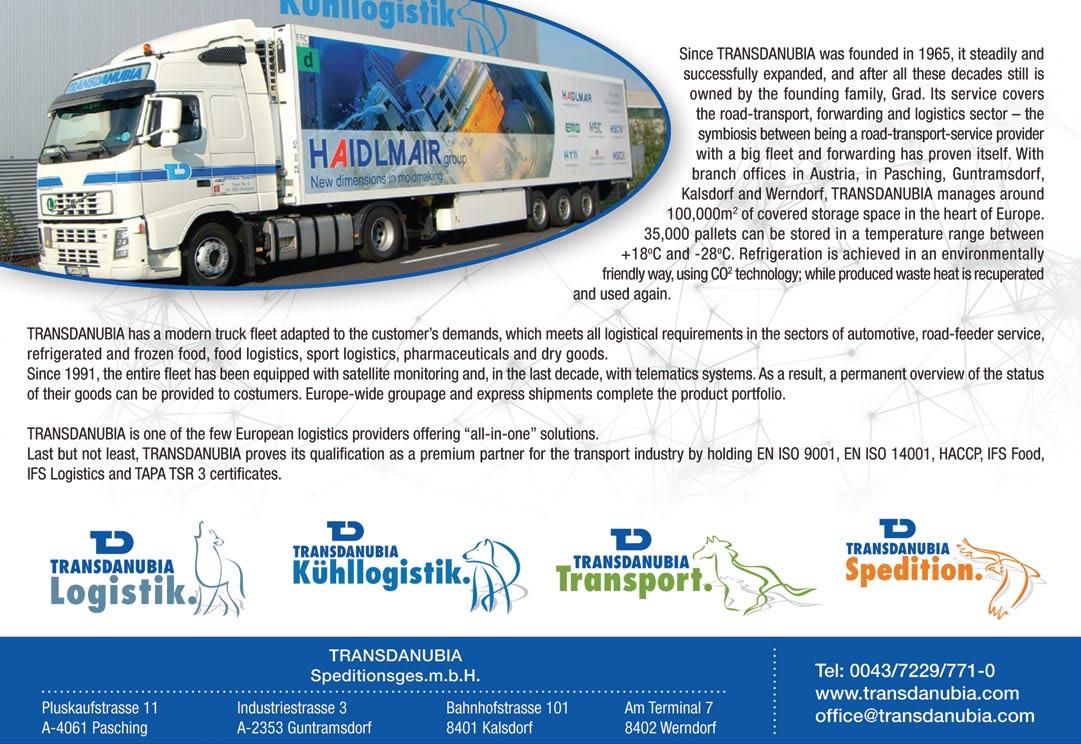
Injection Moulding 4.0. This is the central message the company is promoting at its forthcoming Fakuma trade fair presentation. Mould Making 4.0 stands for the productivity potential opened up by digitalisation in mould making, and for digital services centred on the injection mould process, where it brings the future of mould-making into the digital technology of today.
At the Fakuma trade show, Haidlmair is presenting itself as a highperformance system partner for manufacturers of plastic containers, from simple stackable boxes, through beverage crates, or boxes for warehouse and logistics applications, to dustbins or pallets and pallet boxes. The company, which has production facilities in Upper Austria, Hungary and Canada, has been able to consolidate its leading role in this market segment in recent years.
The company has also received multiple awards for the best central European mould maker. In 2006 and 2017 it won in the category for companies with more than 50 employees, and now has a place in the finals this year, confirming that its strategy of leveraging new opportunities and making these opportunities usable for customers and partners is a winning strategy.
Single source service
At Haidlmair everything can now be obtained at a single source, from the initial concept to the final product. In addition, the company has also extended its customer service portfolio, on the one hand through its investments in FDM (=Fused Deposition Modelling) systems for coating plastic parts with fused materials, and selective laser coating of metals, and on the other through additional digitalisation offerings centred on the injection mould process itself.
In particular, this includes Haidlmair Mould Monitoring for identifying potential faults before they impact on production or on the
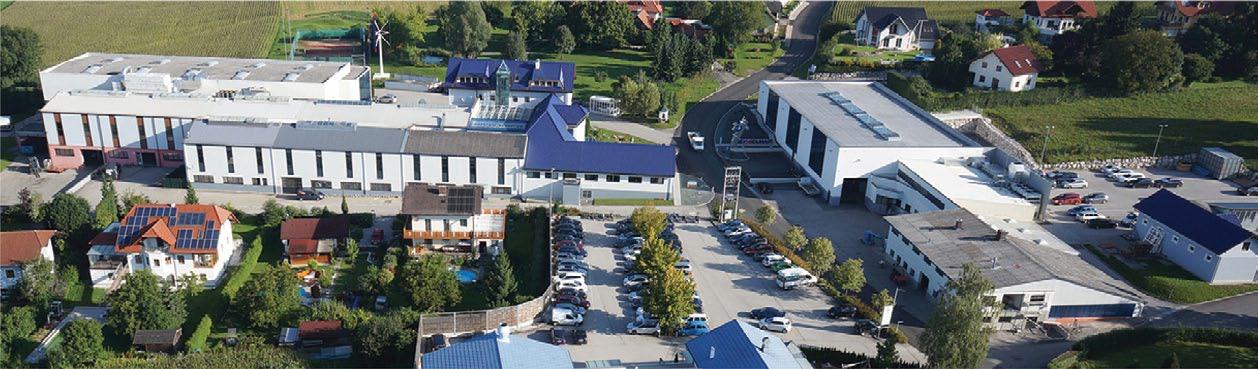
mould. It consists of a system of in-mould sensors and evaluation electronics directly on the mould. This ensures that status data can be retrieved with mobile devices or PCs, from an online platform and using a personalised login, independently of the type and location of the injection moulding machine deployed.
The long-term objective is to be able to use mould-monitoring as an alternative for autonomously controlling the production process by exchanging data with the machine control system. Putting the large industrial computer tomography scanner into operation in June of this year was a further investment to improve the service portfolio in the framework of mould making projects. The scanner supports versatile applications, from measuring and analysing sample parts and feeding the 3-D data back into prototyping and design, and comparing the original data with the measurement data of the mould parts, through to density or inclusion analysis in the scope of part development.
Advancing computer tomography
The recent introduction of computer tomography has helped Haidlmair forge the missing link in the service chain for its mould making customers. It covers all sub-processes of a mould order, starting with the customer’s product idea and including any prototype part production and subsequent part optimisation, the actual mould design, mechanical production, assembly, sampling and quality control by tomography measurement, which can now be offered completely from the company acting as a one-stop-shop.
New sheet die system
After 5 years of development and extensive practical tests, the sheet die (FDU) system developed as a combination of elements from sheet extrusion technology and conventional hot runner nozzle technology is now ready for series production. The main advantage over hot runner systems with round-section nozzles is the die’s comparatively higher throughput via the slit gate. This means that fewer dies are required per part. The slit sprues and runners can be cut off safely and largely without residue.
Shut-off nozzle designs are currently in trial operation and will also be available at short notice. Despite the slit gate design, all dies have round outer dimensions and can therefore be integrated into injection moulds without additional overhead. The market launch began with Midi medium size dies, which are designed for a shot weight of 250 to 1500 g/die.
During the second quarter of 2019 a new company will be launched by Haidlmair called the ‘FDU-Hotrunner Limited’ This will offer higher productivity across the board, and will become the latest independent subsidiary of the Haidlmair Group. It will be headquartered in the Palatinate region of Germany and it is Andreas Kibler, the well-respected current FDU manager at Haidlmair, who will be the new company’s CEO. n
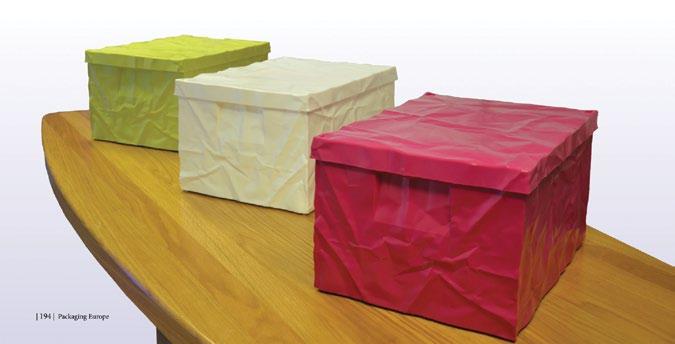
