
4 minute read
The specialist for machine tool peripherals LNS
THE SPECIALIST FOR MACHINE TOOL PERIPHERALS
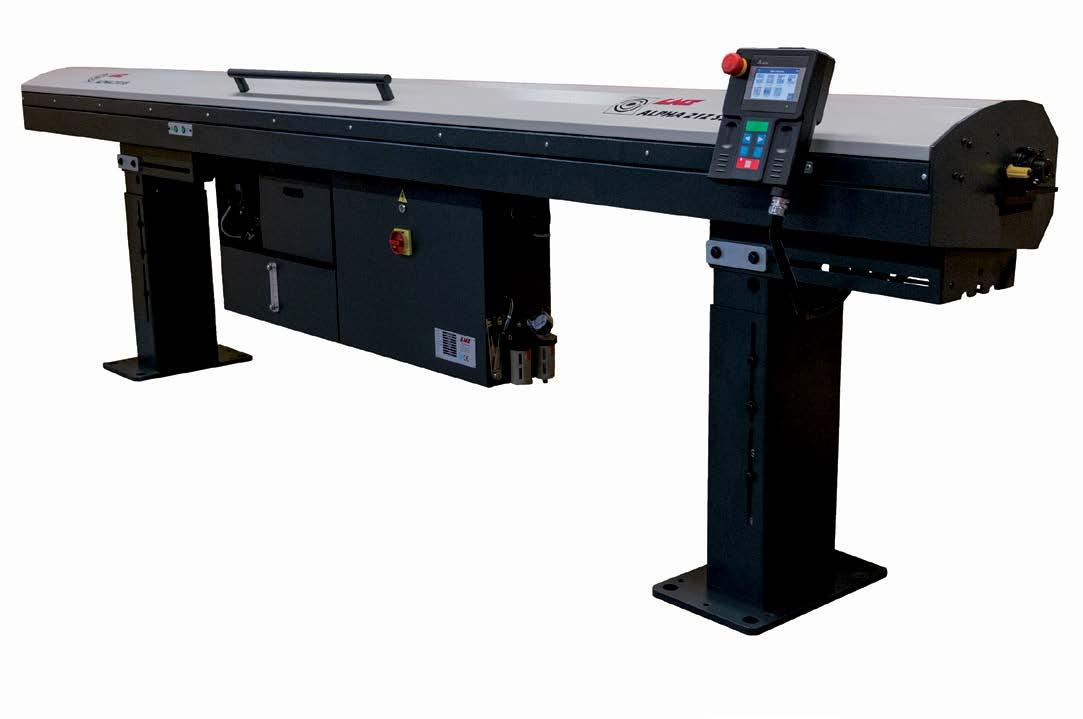
LNS is the one-stop resource for industry-leading bar feeding equipment and accessories, chip conveyors and coolant management systems, offering an unmatched product range, applications experience, service, and support.
With more than 45 years of proven experience in machine tool peripherals that optimise manufacturing performance, productivity and profitability, LNS leads the way in the sector. Based on the principle of sustainability and its knowledge of customer requirements, the company offers a complementary range including chip management systems, coolant management systems, air filtration systems and bar feeding systems.
Since its establishment in 1973, the Group has become a worldwide leader with a global operation, to be closer to regional markets and to respond faster to future developments. Today, LNS employs nearly 1,000 people in its facilities across Europe, North America, and Asia.
The business is managed on a global level through an everexpanding network consisting of sister companies and exclusive agents. This solid distribution network, which has been built up over the years, allows LNS to create customer loyalty and to acquire new customers.
Fast and effective
In the 1970’s, LNS addressed bar loading machine shortcomings by developing the first hydraulic bar feeders that reduce friction, noise, and vibration, better known as the Hydrobar®. This invention was such a resounding success that not only did LNS’s business
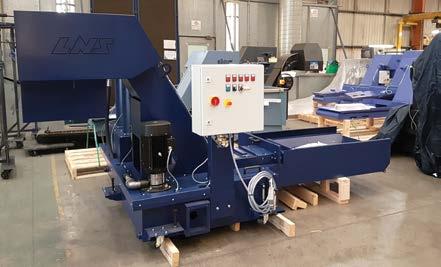
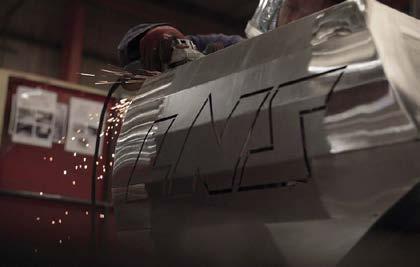


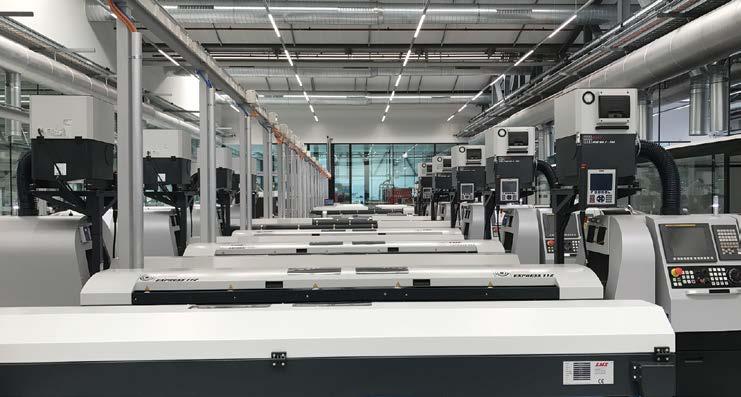
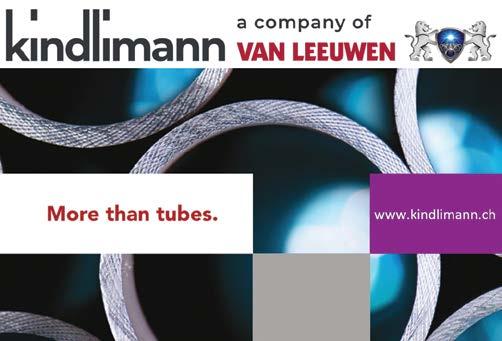
increase significantly, but the name Hydrobar® became a generic term still used throughout the machine tool industry today.
Since then, LNS bar feeders have evolved into user-friendly, ergonomic, and highly efficient devices that provide a number of significant advantages including faster changeovers, optimum turning machine RPM, unattended operation as well as remote monitoring.
With over 170,000 units installed worldwide, LNS bar feeders are universally recognised for their exceptional bar guiding technique. In the most varied applications, LNS bar feeders ensure maximum productivity on all types of fixed or sliding headstock lathes.
In addition to bar feeders, LNS offers air filtration systems to eliminate pollution related to the metal manufacturing environment, and is also a specialist in chip management systems, designing and producing conveyors and full integrated chip disposal systems for all machine types. The range of conveyors covers all material types and chip shapes, and can cater for all filtration requirements, up to 50 microns.
Last but not least, in order to improve machine tool productivity, LNS Group offers a complete range of coolant systems, oil mist collectors and tramp oil removal systems that guarantee optimal lubrication, allowing a considerable increase in machining speeds.
ULTRA 80
A constant search for new technologies and solutions that will allow customers to maximise their productivity has been one of the factors supporting LNS’ global growth. New products and innovations are developed to match evolving customer needs.
In 2020, the company launched the ULTRA 80, a new bar feeder. Provided with an extremely rigid 700 kg mineral cast iron support beam, helping to “seat” the machine in position, it guarantees machining quality by damping to a maximum the vibrations generated by the rotating bar. To make this support beam, LNS Group uses a specific patented manufacturing process. The complete machine weighs up to 2 tonnes and remains perfectly stable even while long bars with a diameter of 80 mm and weighing over 160 kg are rotating.
In response to requests from its customers, LNS Group designed a highly flexible front rest system for the ULTRA 80 to reduce the need to change the guiding elements. The front rest is an essential support element for the bar before it enters the lathe spindle, keeping the bar perfectly centred, while accepting a wide range of bar diameters. It adjusts automatically to bars of different diameters, so the operator does not have to change the guiding elements.
The ULTRA 80 is available in two versions, with internal ramp or external lift to offer customers the configuration best suited to their requirements. The oversized insertion and extraction system is also equipped with a booster for all chucks available on the market.

E-Connect
The company has been active on the digitisation front since 2006, enhancing productivity through a unique electronic connection system to help reduce downtime, material waste and labour costs, all of which help manufacturers maximise productivity and profitability.
The LNS proprietary e-Connect Ethernet communications system enables bi-directional data sharing between CNC machine tools and LNS bar feeders. These intra-machine communications monitor material usage and CNC production schedules to provide automatic changeover capability that reduces material waste and improves throughput.
Developed in cooperation with major turning machine original equipment manufacturers (OEMs) and with extensive input from end users, the system enables manufacturers to create a library of over one thousand parts programs that are stored in the bar feeder’s programmable logic controller (PLC).
Currently in use with select turning machines, the system will soon be more widely available. LNS continues to listen to OEMs and end users, and the needs of these will drive the development of other useful enhancements. n
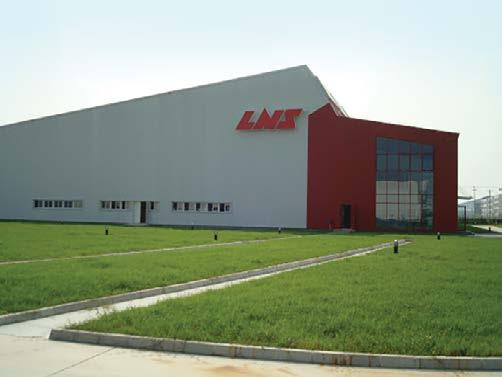