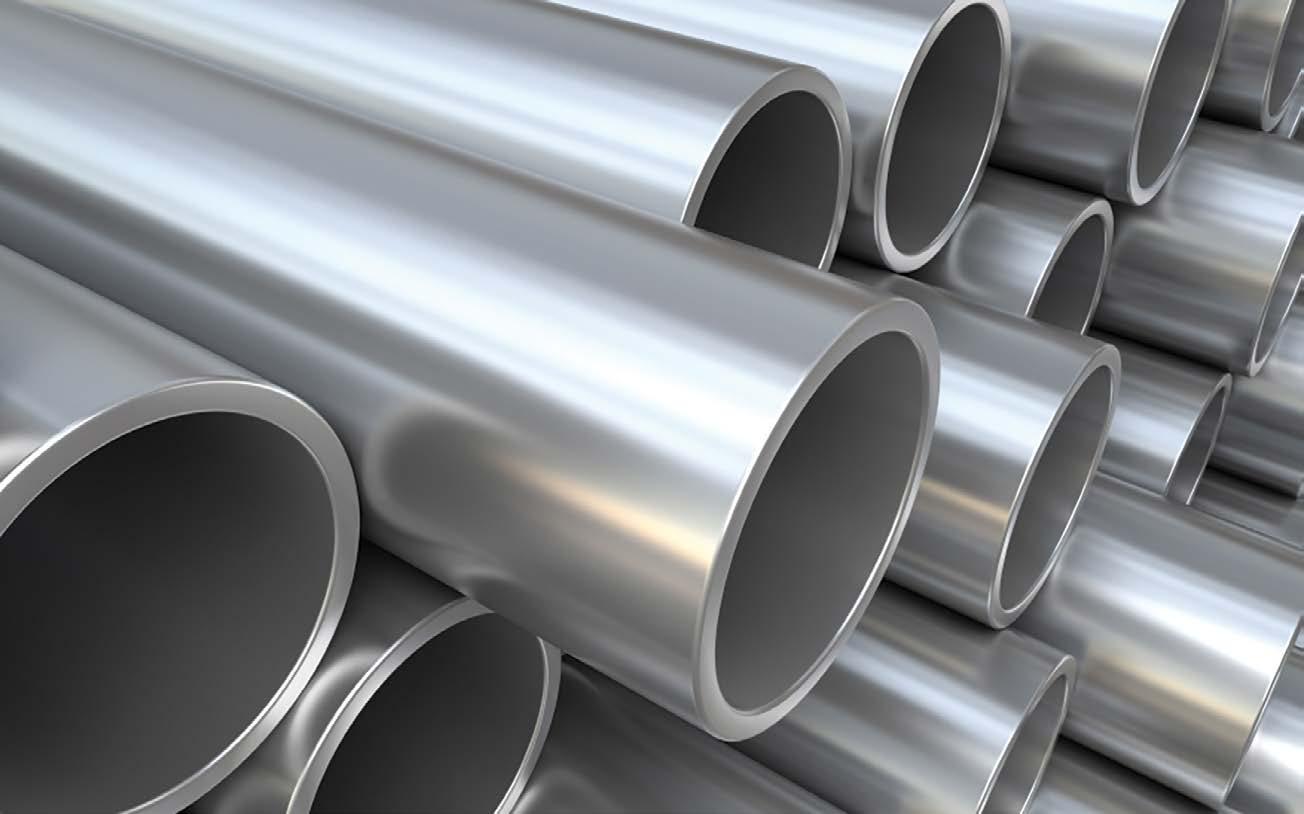
4 minute read
Aluminium in all forms Profilglass
ALUMINIUM IN ALL FORMS
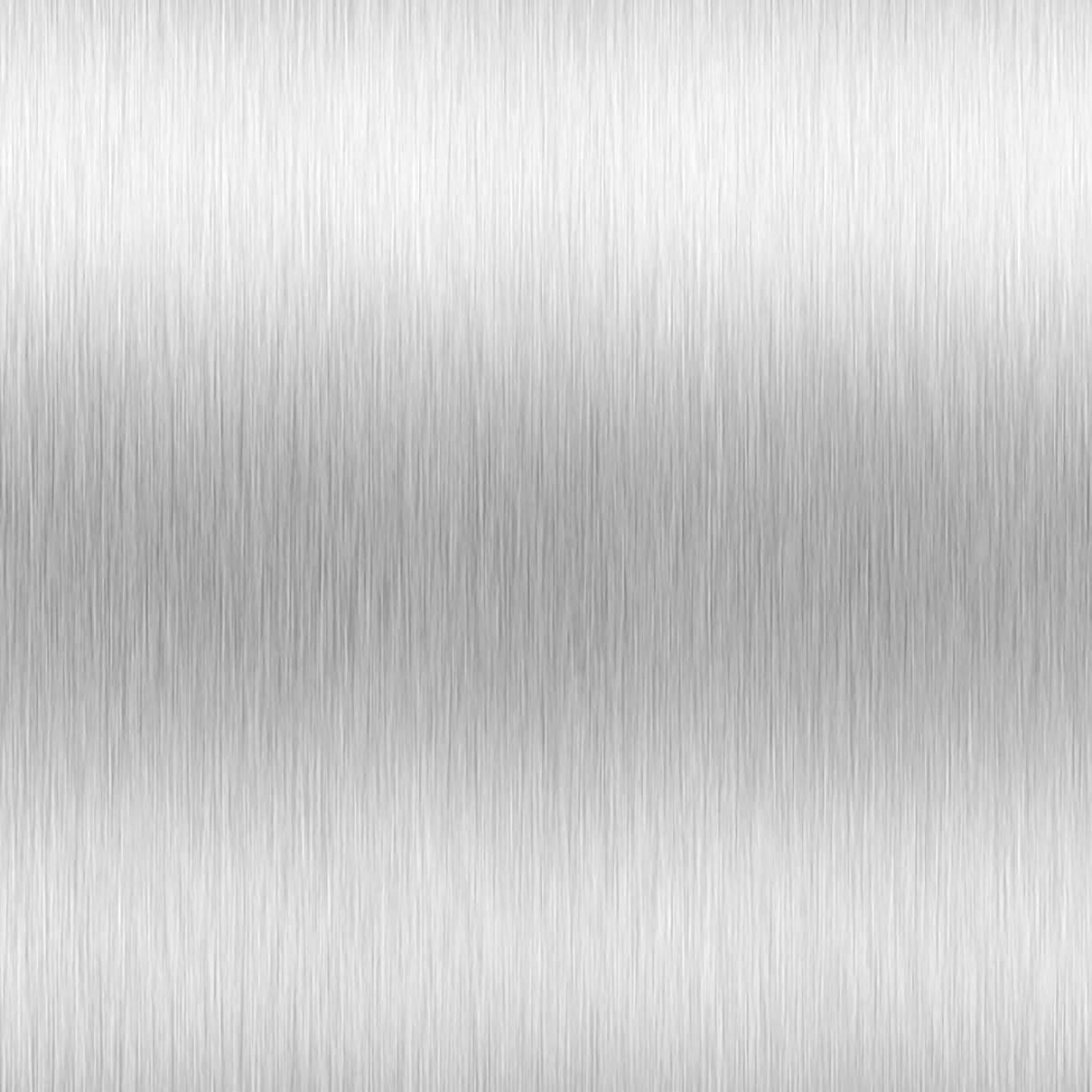
Italy-based Profilglass offers a wide range of aluminium profiles, tubes and flat-rolls designed for a number of sectors. As the drive for sustainability increases globally, the company is set to make use of the emerging opportunities.
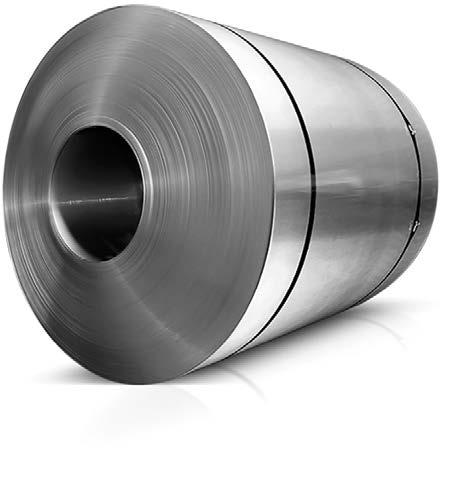
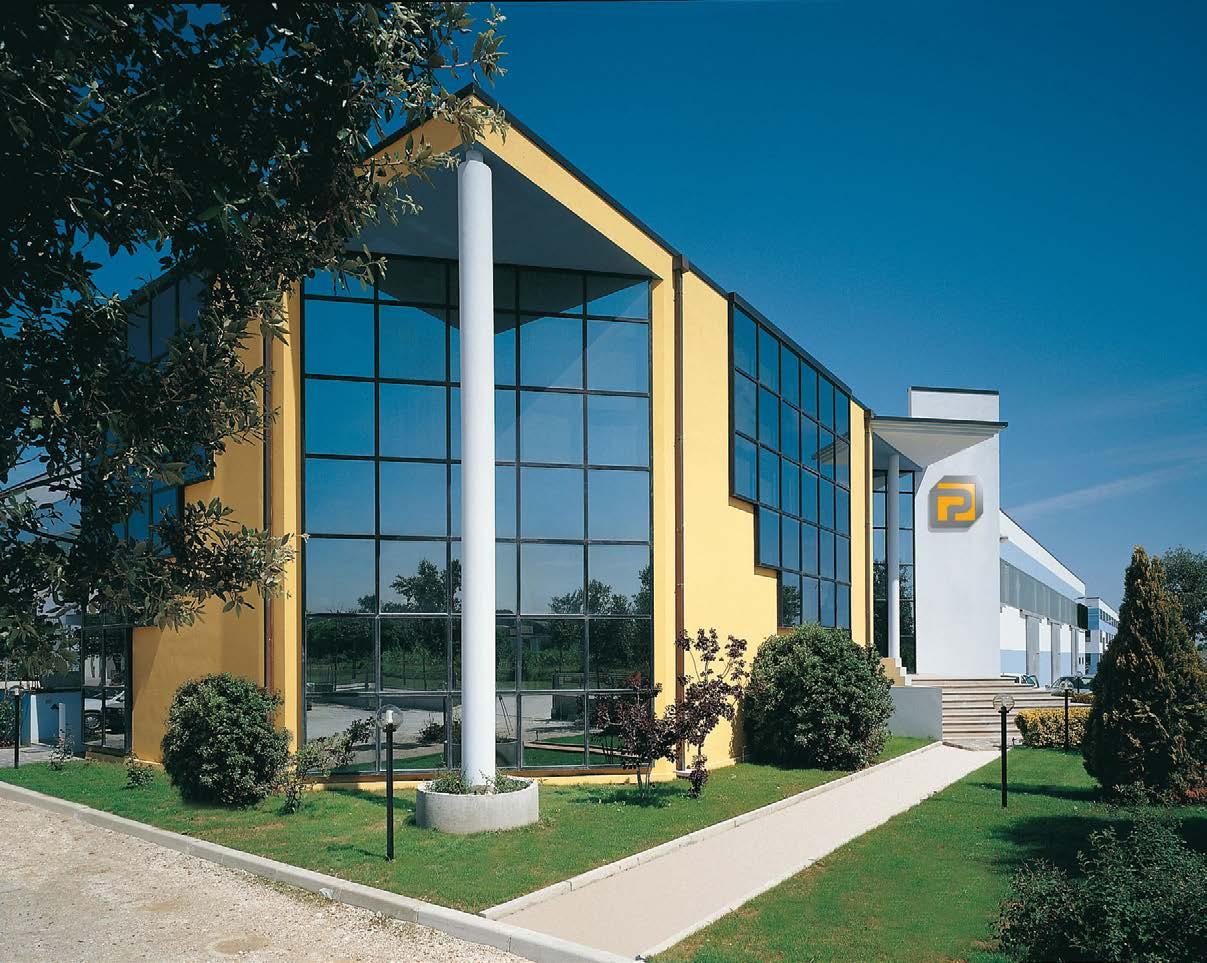
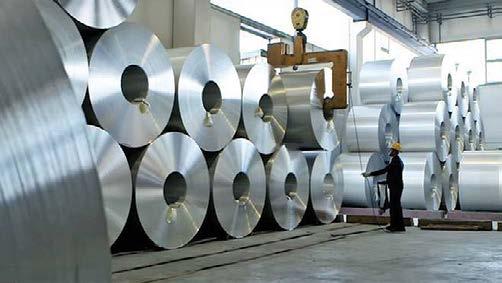
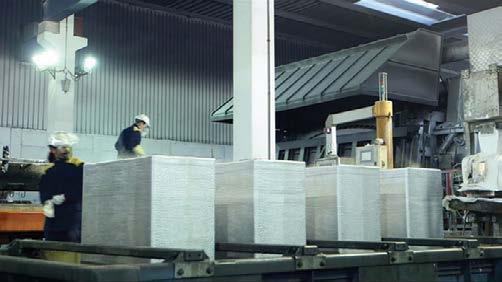
Eco-sustainable, lightweight, resistant, non-toxic, easy to mould and process, aluminium has some unique properties which, when enhanced by suitable processing, make it ideal for a wide range of applications.
Profilglass promotes the potential and qualities of aluminium not only for the growth of its clients but also in order to build a better future: the raw material the company processes is 100 % recyclable and versatile, suitable for many applications across a range of sectors from construction to automotive.
Four decades of growth
Founded in Fano in 1982 by the brothers Giancarlo and Stefano Paci, Profilglass has grown quickly within a vertical structure, to the point of completing the aluminium cycle and diversifying its business. The company initially produced spacing and decoration profiles for double glazing, as is still reflected in its name.
In 2000, the company expanded both capacity and staff numbers and entered the flat-rolled products sector in response to the increasing demand for high-quality aluminium products.
Today, with over 250,000 tons of aluminium processed every year, Profilglass has attained a leading position at international level, exporting to more than 85 countries, continuing to focus on innovations and responding to evolving market requirements.
The company runs state-of-the-art production facilities. The foundry, the first raw material transformation point, is equipped with modern plate pouring furnaces and advanced degassing and filtering systems which guarantee high quality standards. The six lines for continuous casting are fitted with furnaces using
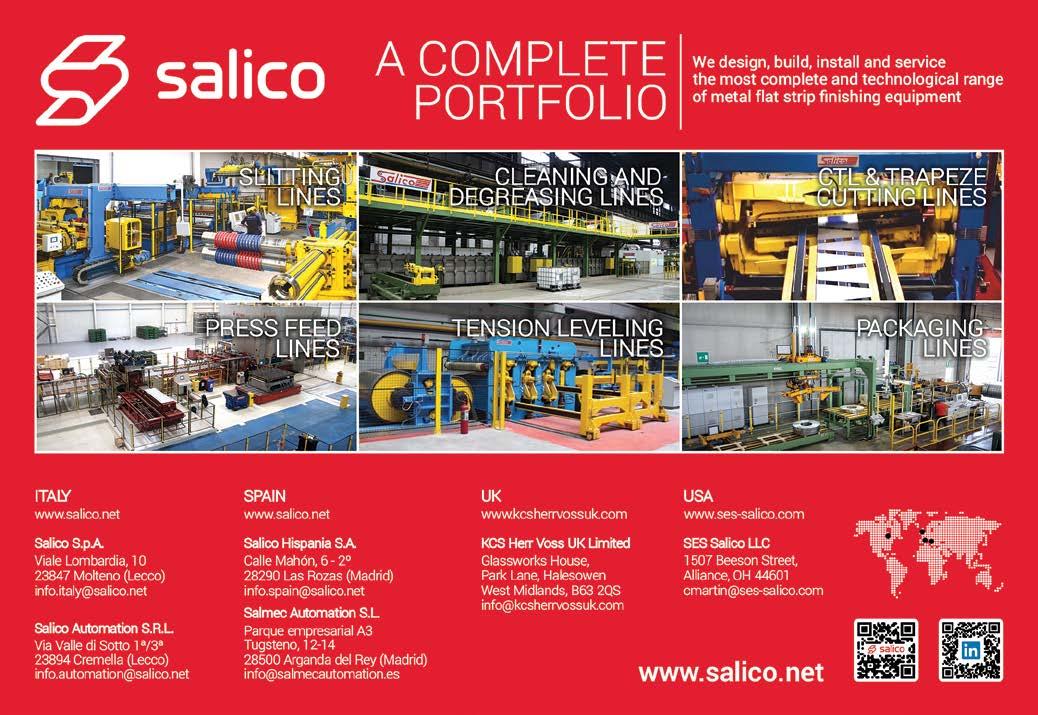
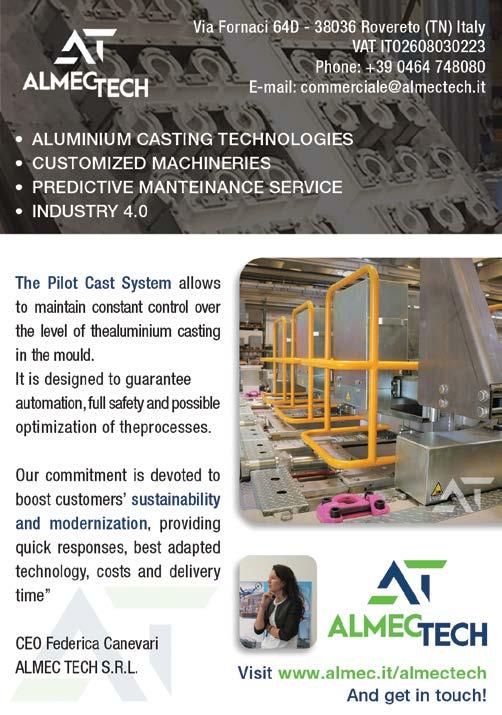
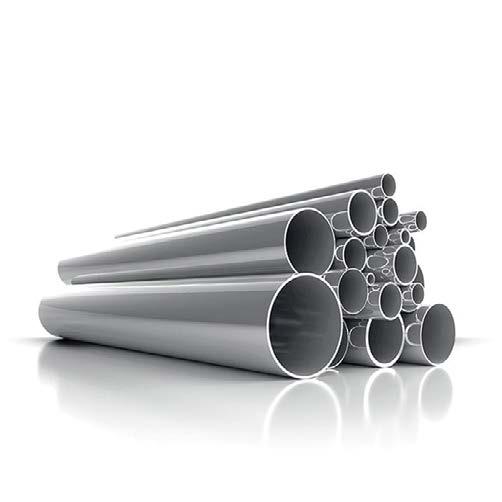
innovative liquid metal treatment systems which allow for perfect homogenising, as well as degassing and filtering devices which ensure the correct quality standards in aluminium.
At its 30th anniversary, Profilglass invested in a hot rolling mill that optimised the production processes and increased the company’s product range. Fitted with the most advanced control systems, and in compliance with high quality standards, it is designed for hot lamination of about 150,000 tons/year of aluminium plates up to 4 mm thick. The production technologies are rounded out by cold rolling, heat treatment and surface treatment.
Recent investment includes two impressive cutting lines, delivered by Salico, for automotive and aerospace applications. De-coiling, levelling, slitting with final recoiling of edge-trimmed coils or in multislit formats are some of the functions featured in the combo-line designed to process aluminium coils. The Covid-19 pandemic did not delay the project, which was completed quickly and efficiently.
Wide range

From the company’s very beginnings, spacers and decorative profiles for double glazing have been its core product group, and the one that has made Profilglass a world leader in this segment. The profiles, 250 different types, are available in standard version, bendable, anodised and in different painted colours.
The flat-rolled product range includes a wide range of shapes including discs, sheets, strips, triangles and bands; tailor-made solutions are also available.
Tubes are made in Eurotubi, one of the group’s companies, a leader in the production of electrically welded aluminium pipes in different alloys, sizes and surface appearances, offered in 6-70 mm diameter sizes.
In 2017, Profilglass established LamiAl, a new company within the group, with a view to expanding the parent company’s experience and competence into automotive, transport and industrial applications. Using LamiAl’s advanced production technologies from cold-rolling to surface treatment, materials are processed to the very highest quality standards to meet the ever-increasing demands of the specific sectors.
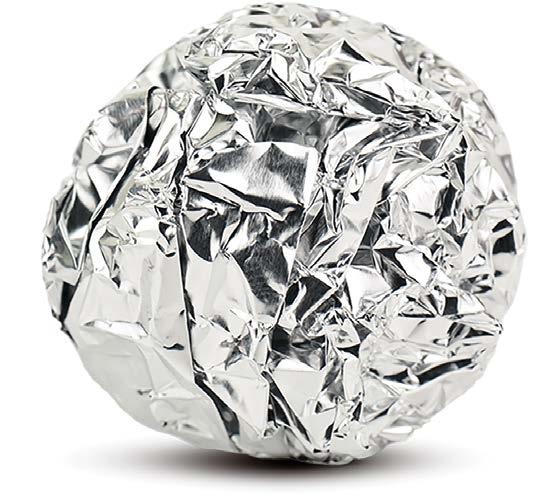
Green and clean
Profilglass bases its values on environmental and social sustainability, promoting “development that meets the needs of the present without compromising the ability of future generations to meet their own needs” (Brundtland Report, 1987).
Starting with the features of the raw material used, ideal for improving the quality of life and of the environment, Profilglass applies policies aimed at recovery and recycling to minimize environmental impact, with a focus on continuous improvement.
The company strives to reduce energy consumption and resources employed, as well as waste, and to mitigate its overall environmental footprint. Every effort has been made to ensure its facilities are as environmentally friendly as possible: recent investments include a large-scale photovoltaic system – one of the largest solar parks in Italy.
“Working with aluminium means looking to the future, developing products with a high added value for the future and for the growth of new sectors. This is why we strive for ongoing progress, constantly assessing the usefulness of actions and investment aimed at optimizing quality, safety, costs and times for products and processes. We will continue to meet dynamic market requirements and to keep offering cutting-edge solutions,” affirms the management, as stated on the company website. n