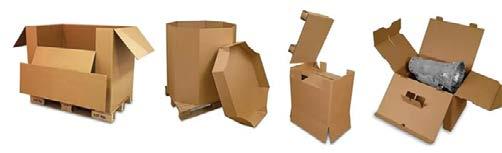
5 minute read
Redefining the concept of packaging DS Smith
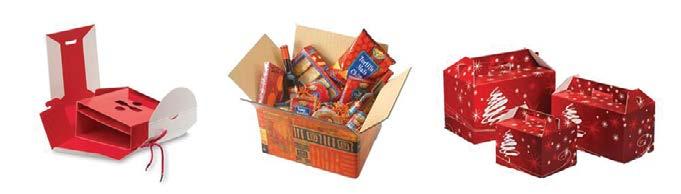
REDEFINING THE CONCEPT OF PACKAGING
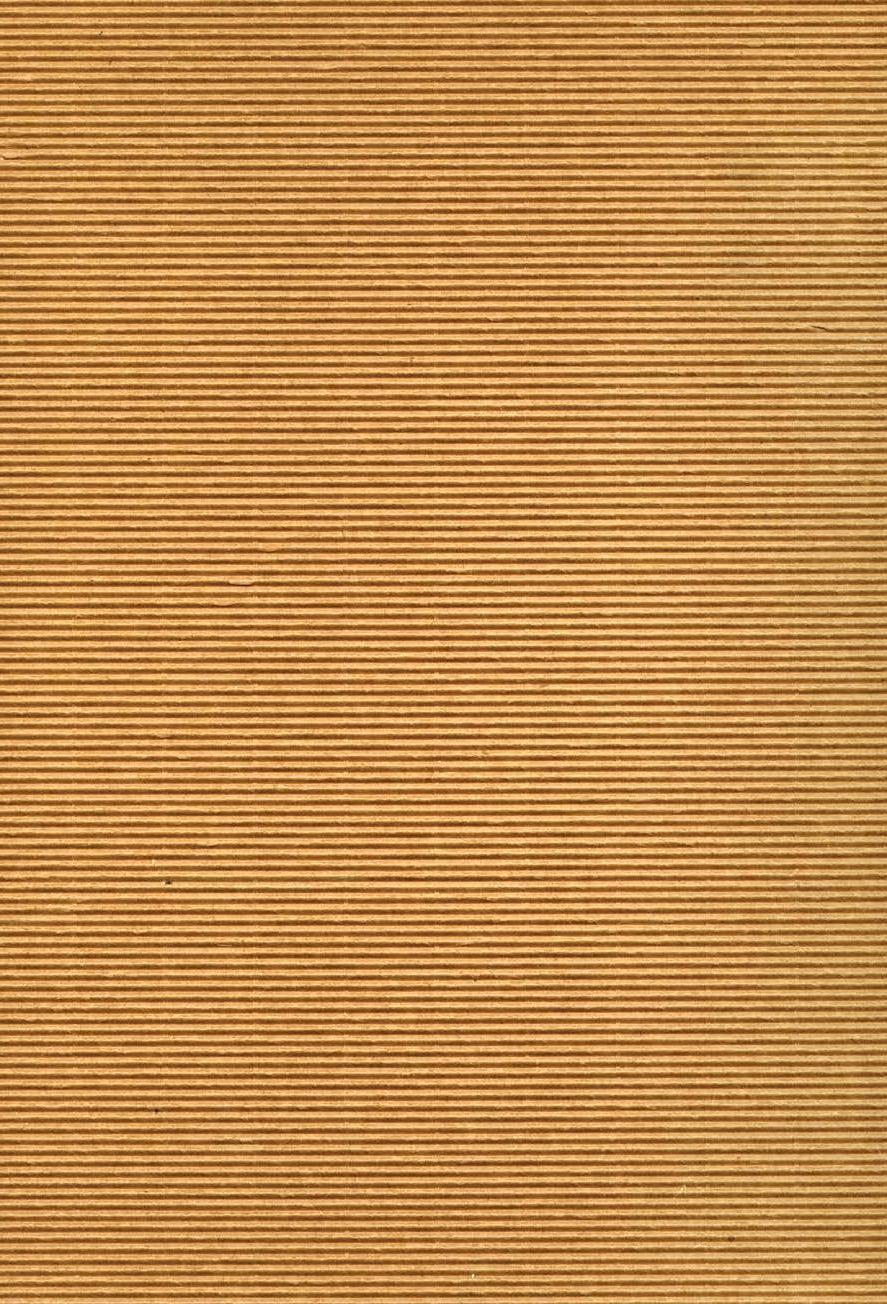
Sustainable packaging, paper products and recycling services provider DS Smith has used the lockdown as an opportunity to further intensify its focus on circularity and environmental performance. Romana Moares reports.
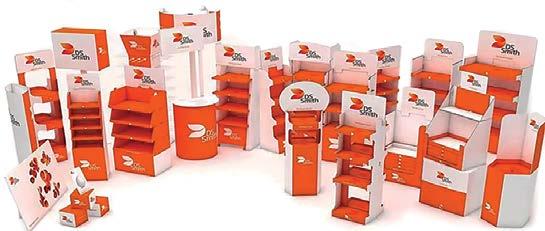
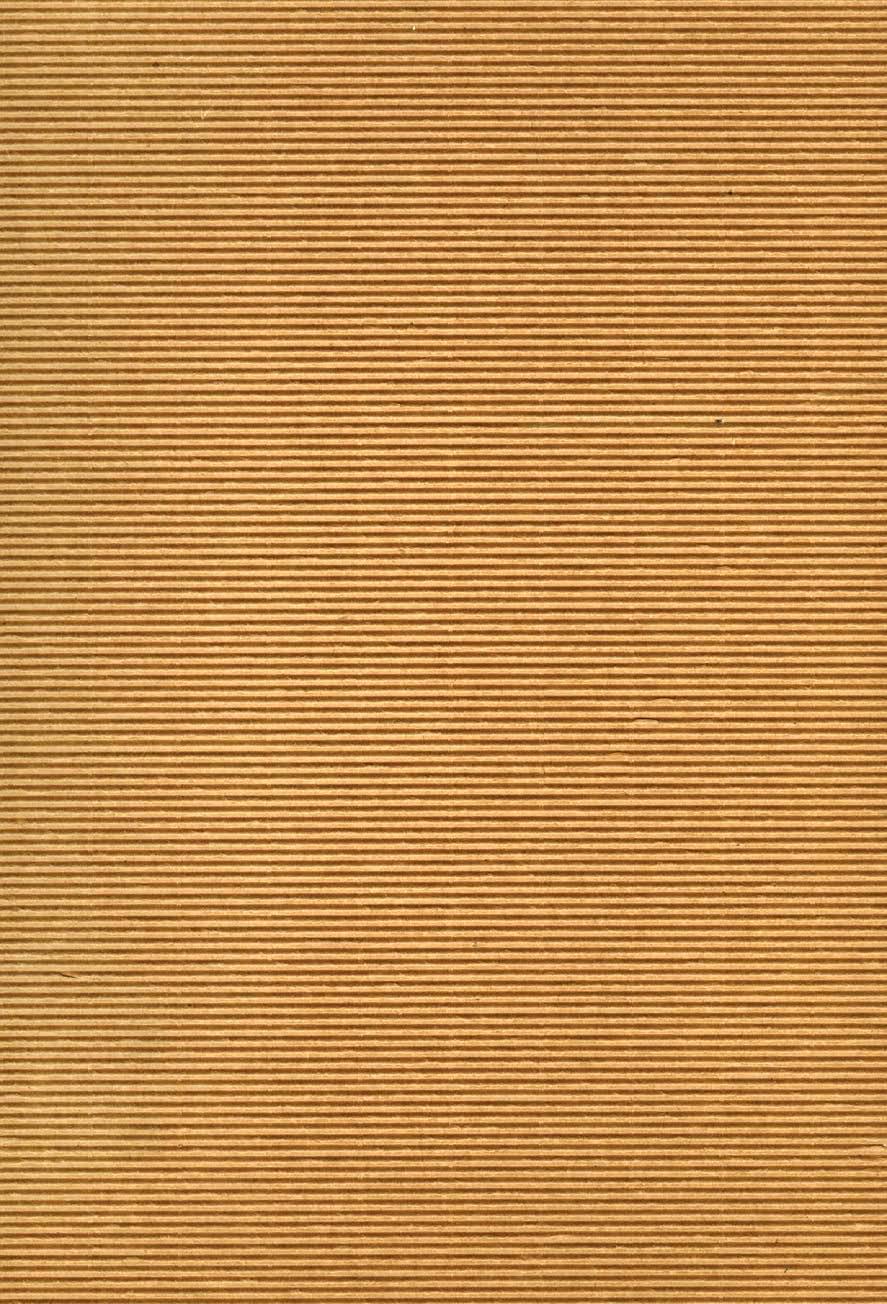
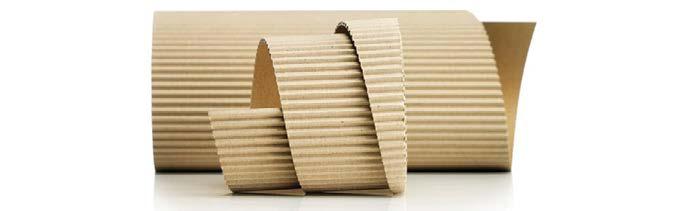
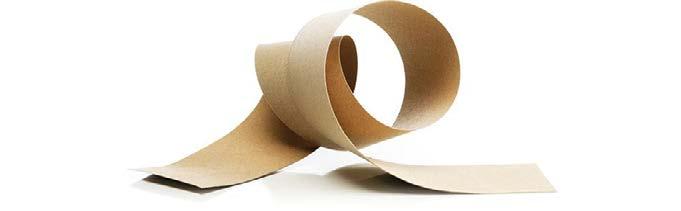
DS Smith, which started as a box-making business in East London in the 1940s, is today a major organisation employing over 30,000 people in 30 countries.
The company’s core business is the design and manufacture of innovative, sustainable packaging that takes the entire supply chain into account. DS Smith’s products can improve transport and storage efficiency, boost retail presentation and increase product sales for its customers – this is done with sustainable corrugated cardboard.
At DS Smith sustainability is the foundation of the business. The company has recently defined its ‘Now and Next Sustainability Strategy’ focusing on closing the loop through better design, protecting natural resources, reducing waste and pollution with recycling, and training people to achieve the transition to a circular economy.
By 2023, the company is set to manufacture 100% recyclable or reusable packaging by training its designers in ‘Circular Design Principles’ and making recyclability mandatory in new product development. By 2030, the company is aiming for all its packaging to be recycled or reused. Circular Design Principles

Given that to a large extent, the environmental impact of a product is determined during the design stage - from the materials used to the way the products are manufactured - DS Smith decided to give this stage increased attention. Therefore in 2019, the company started to collaborate with the Ellen MacArthur Foundation to design the Circular Design Principles in 2020.
The aim is to deliver packaging that is circular economy-ready by helping designers adopt a re-use, return, repurpose and recycle mindset during the design stage and encourages them to follow the company’s ‘Materials Hierarchy’, where 100% of DS Smith’s solutions are reusable or recyclable and are fully optimised for customer supply chains.
In May, the company announced that it has achieved its target of training all of its designers - across 26 countries - in its Circular Design Principles.
“By achieving this milestone, we have set an industry standard for design and innovation. We can proudly claim that from the start of

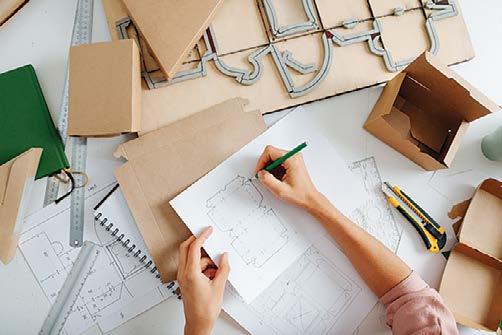
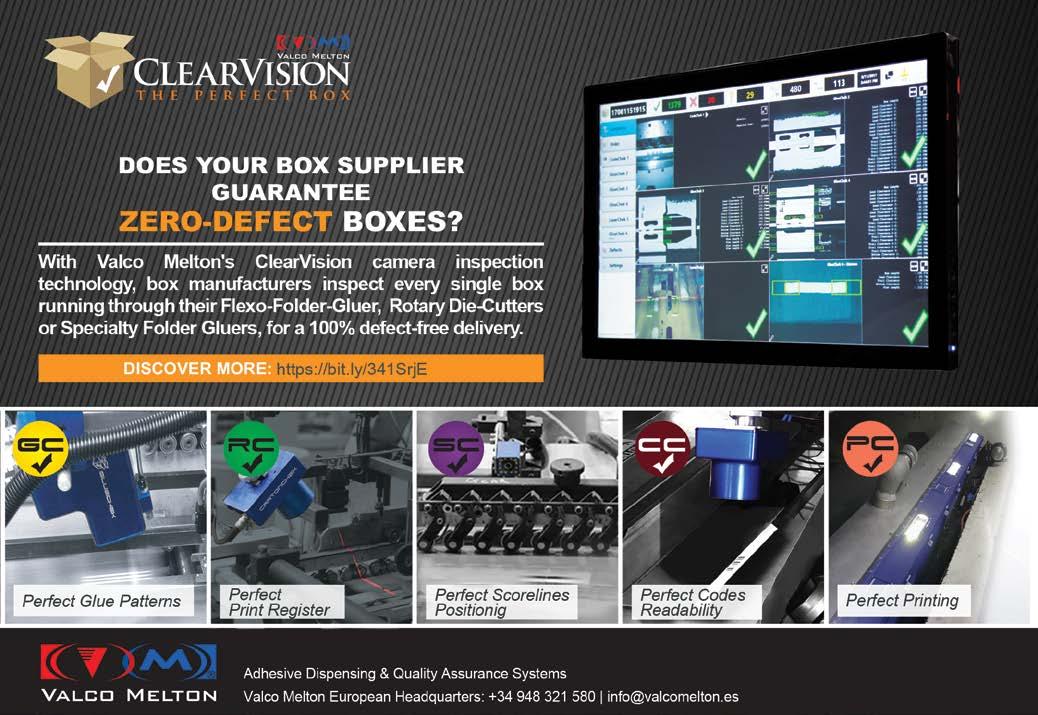
Packagers can demand faultless boxes and expect no machine downtime associated with defective cases when their suppliers rely on ClearVision Inspection Technology for their Flexo-Folder-Gluers, Rotary Die-Cutters or Specialty Folder Gluers.
Controlled from one single screen, ClearVision software can inspect up to 6 features of every single box such as glue patterns, codes readability, printing, print-to-print and print-to-board registrations and the correct position of scorelines. ClearVision provides custom solutinos that can be adapted to each product specifications.
GlueChek camera verifies glue presence, and its correct placement and volume to validate that every pattern has been properly applied. By measuring distances between printing and borders, RegChek detects variations in the print-to-print and print-to-board registrations. CodeChek camera verifies the readability of any barcode or 2D code printed on any place of the package and avoid mixed copies problems. ScoreChek verifies the correct scorelines position to determine that the blanks have been fed correctly. Finally, color, unwanted spots, marks, missing printing, board damages, smearing… can be inspected with PrintChek.
Box suppliers working with ClearVision’s system guarantee that packagers will only receive defect-free boxes, avoiding subsequent machine downtime, product waste or end user complaints.
ClearVision is Valco Melton’s quality inspection technology division, a leading supplier of gluing systems for the corrugated, folding carton, packaging, paper converting and other industries. Specifically designed for the packaging industry, ClearVision has also developed the PackChek camera, that inspects the already closed boxes for the correct hot melt pattern application for a perfect end-of-line box sealing.
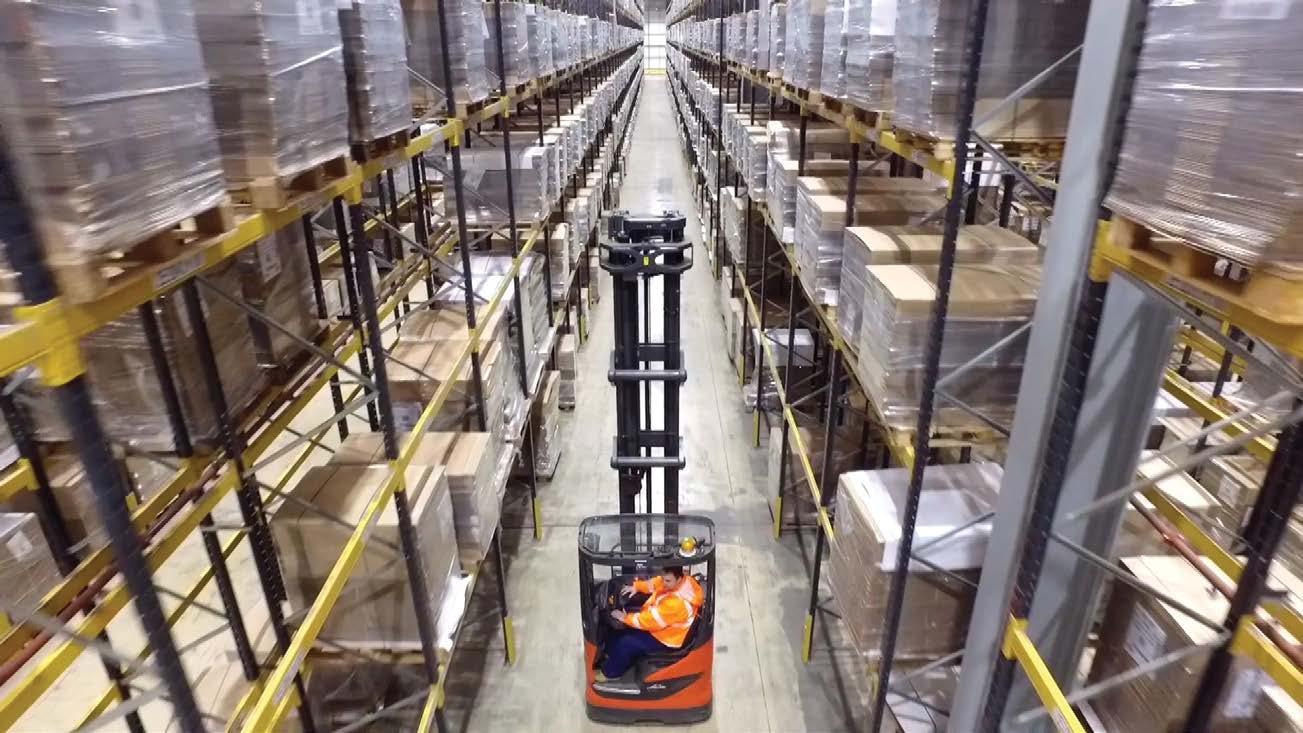
the design process we are working towards our purpose, ‘Redefining Packaging for a Changing World’,” says Alan Potts, Design and Innovation Director.
Circular Design Metrics
In May, DS Smith achieved another milestone by unveiling its ‘Circular Design Metrics’, an industry first that allows customers to rate the circularity of their packaging.
This pioneering initiative provides a unique insight into how companies’ packaging choices can reduce their impact on the environment. Through the collaborative design process, customers will be able compare the environmental performance of different solutions, in order to create more circular packaging.
The Circular Design Metrics is a breakthrough new tool that makes it possible to see and compare the performance of a packaging design across a range of indicators, such as recyclability, renewable content, supply chain optimisation. The metrics include eight different indicators that provide a clear indication of circularity performance and help identify areas with potential for improvement. The tool is a first of its kind for brands that want to drive sustainability performance through their packaging.
Stefano Rossi, Packaging CEO at DS Smith, commented: “Our new Circular Design Metrics is a game changer in driving environmental performance in packaging. We’re excited to use our expertise to help companies, large and small, on their journey to become circular economy-ready.”
Doubling Investment
There is increasing evidence that since Covid-19, consumer attitudes towards sustainability have strengthened and circular procurement will have a vital role to play in winning and retaining business.
In line with market developments, DS Smith has recently announced that it will double investment in R&D to accelerate its work in the circular economy. The £100mn (€116mn) investment over a period of five years will cover the creation of a new breakthrough technologies hub in the UK, new materials development to replace plastics, and a pilot to gauge G-force shock in home delivery packaging.
The company is also investing nearly €17 million in its German plant, which specialises primarily in innovative packaging solutions for the e-commerce and FMCG sectors. These investments underpin the company’s circular economy-led sustainability strategy to replace a billion pieces of supermarket and e-commerce plastic by 2025.
DS Smith Chief Executive Miles Roberts said: “We are now investing more than in previous years to ensure that we can offer customers packaging that has less impact on the environment. DS Smith makes sustainable packaging that is fibre-based and fully recyclable. We continue to focus on reducing the impact of our operations on the environment but more importantly, we are able to contribute to wider society by providing circular packaging solutions and supporting our customers in transitioning to a circular economy.” n
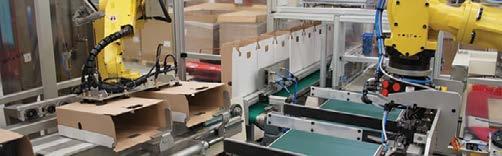