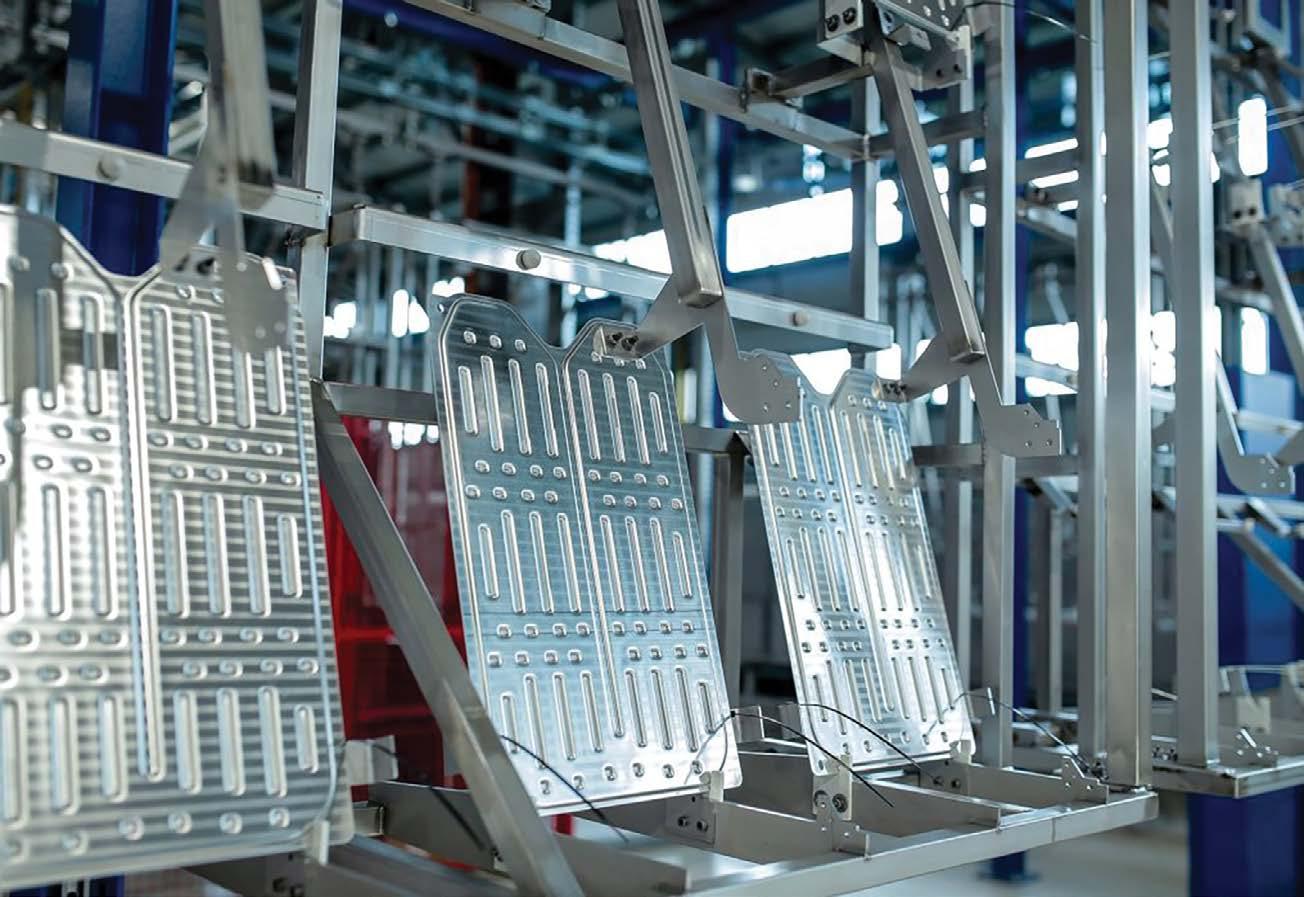
4 minute read
Complete cooling solutions RAAL
COMPLETE COOLING SOLUTIONS
RAAL, the manufacturer of cooling systems and heat exchangers, boasts a comprehensive in-house capability from design to dispatch, enabling rapid product development and a fast manufacturing cycle - benefits highly rated by leading global players from the automotive through to the energy sector.
Headquartered in Bistrita in Transylvania, northern Romania, RAAL is a manufacturer of cooling systems and heat exchangers made of aluminium alloys and stainless steel, in brazed construction: radiators, oil coolers, air coolers, condensers and evaporators, designed for agricultural, construction, industrial equipment and automotive applications.
RAAL has two production two sites - Bistrita (12,500 m2) and Prundu Birgaului (32,000 m2), and a strong R&D capability to design programmes for its customers’ new products, providing a differentiation factor based on innovation and performance.
Over the last three decades, the company has completed thousands of projects of various designs and dimensions, always providing the greatest flexibility, and striving for technological and research advancement. Around 99% of the output is sold in export markets either directly or via its branches in various countries in Europe and dealers further afield.
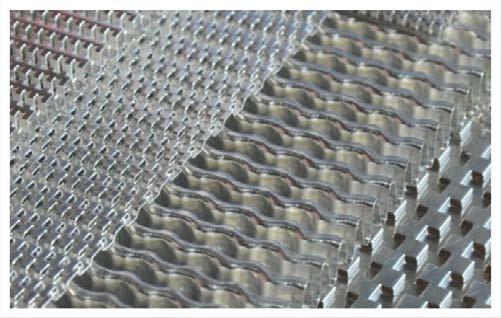

Delivering Performance
The Romanian company was established in its current form in 1991 but draws on the wide-ranging experience of its predecessor, which had operated in the cooling system business for many years.
In 2007 the company commissioned its second, brand-new cooling system factory in Prundu Birgaului, northern Romania, in the Transylvanian region, and in 2015 began a major investment in the manufacture of steel and aluminium structures to deliver both cooling systems and metal structures.
In 2017 RAAL reached another significant milestone by opening a new production hall for automotive applications, housing production of heat exchangers for electronic circuits and batteries for hybrid and electric cars.
“We have also invested heavily in the research and development department, a testing centre with advanced equipment and patents for fins and new solutions,” says General Manager Paul Ilies. “With our highly skilled designers and R&D specialists, we can offer fast development of a product that delivers outstanding performance in terms of corrosion resistance and a high degree of complexity.”
RAAL performs the sizing of heat exchangers and cooling systems using its own software, based on theoretical studies and on the results of thousands of performed tests. RAAL uses FEA (Finite Element Analysis) to simulate structural, flow and vibration-stress conditions. The performances and structural features of new products are validated in the RAAL testing centre, based on the technical specifications and the parameters obtained by data acquisition on the customer’s equipment.
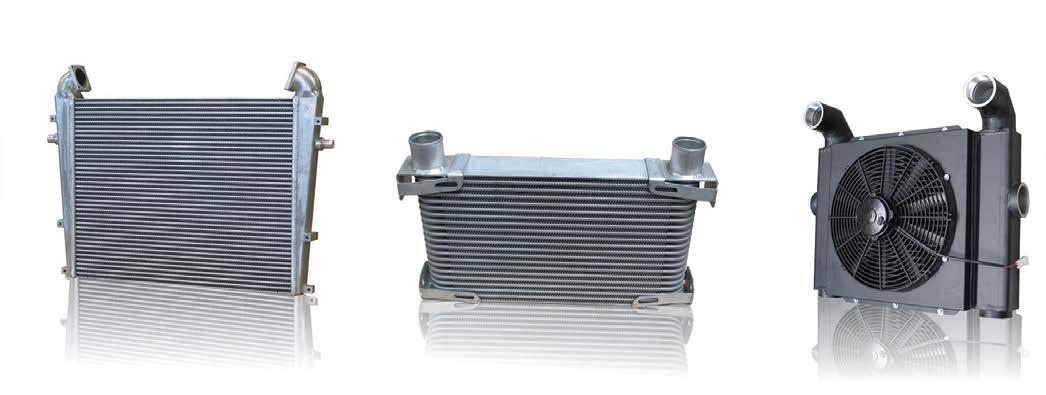
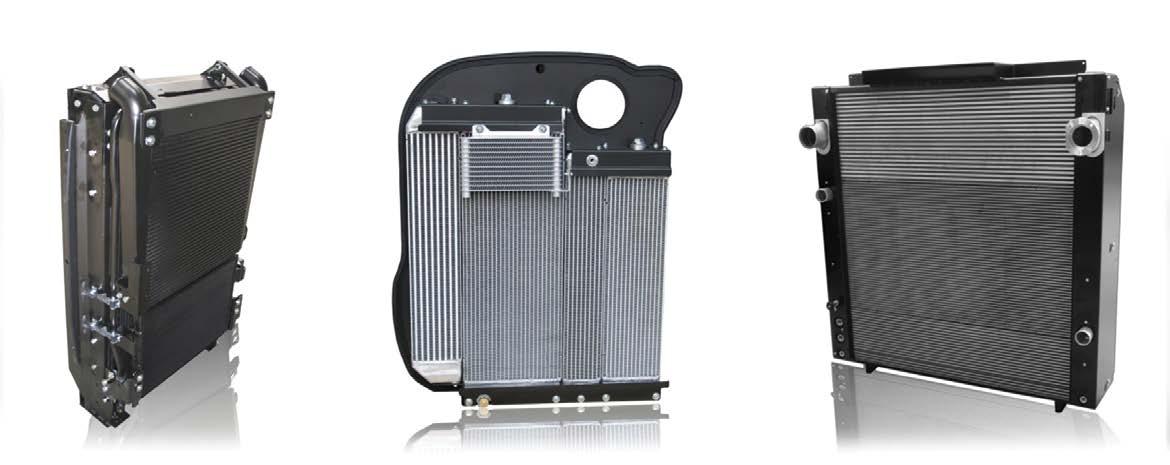
One of the company’s strengths is its high degree of flexibility. Its modular heat exchangers and cooling systems are adapted to its customers’ needs and are developed in partnerships with customers’ designers. This trust and an open-minded approach towards the latest technical solutions and customer focus are the core values of RAAL, the very basis of long-term business relationships, says Ilies.
Recognised expert
Heat exchangers and cooling systems are RAAL’s core product groups. The heat exchangers are designed and made in the following structural solutions: plate&bar, tube&fin, shell, extruded tubes, brazed plates and “in-tank”. The company offers custom cooling solutions for hundreds of applications; and has delivered tens of thousands of different products in small, medium, and large series. RAAL offers stainless steel heat exchangers, suitable for high pressures, high temperatures and corrosive environments, using vacuum furnace brazing technology.
RAAL designs and manufactures complete cooling systems, composed of brazed aluminium heat exchangers and metallic structures, frames, expansion tanks, fan cowls, fan guards and ensures systems equipment with fans, motors, other components. These systems boast high cooling performance, compact construction, modular solution using various design types and configurations, a “drop-in-place” concept for integration into equipment, and the company has full responsibility for the entire cooling system.
The company has a dedicated manufacturing hall for the production of heat exchangers in brazed plates constructive solution. RAAL brazed-plate heat exchangers have been designed to increase the thermal performance in fluid-to-fluid cooling applications. This type of heat exchanger is fully made of aluminium alloys using controlled atmosphere brazing technology. Different working fluids can be used: water, oil, air, refrigerant, etc.
The company’s production hall, opened in 2017 specifically for hybrid and electric vehicle applications, houses the manufacture of products designed for shipping to car manufacturers in Europe, Asia, and the United States.
Once the products are completed, RAAL can provide customised logistics services, i.e. transport, storage and distribution as required, completing the last stage of the whole process, delivering the products direct to the customer’s premises. n
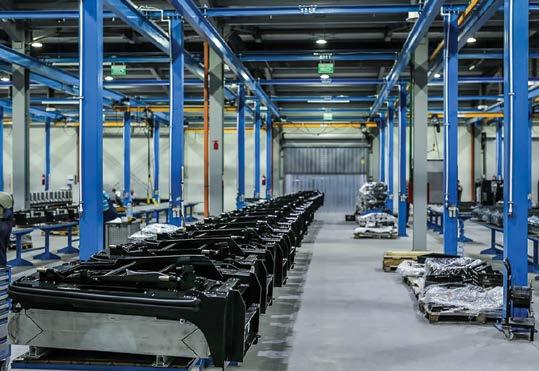
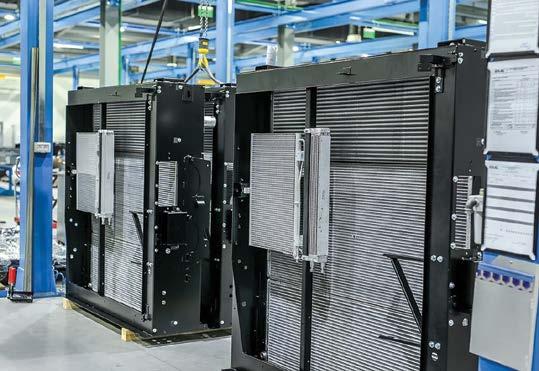