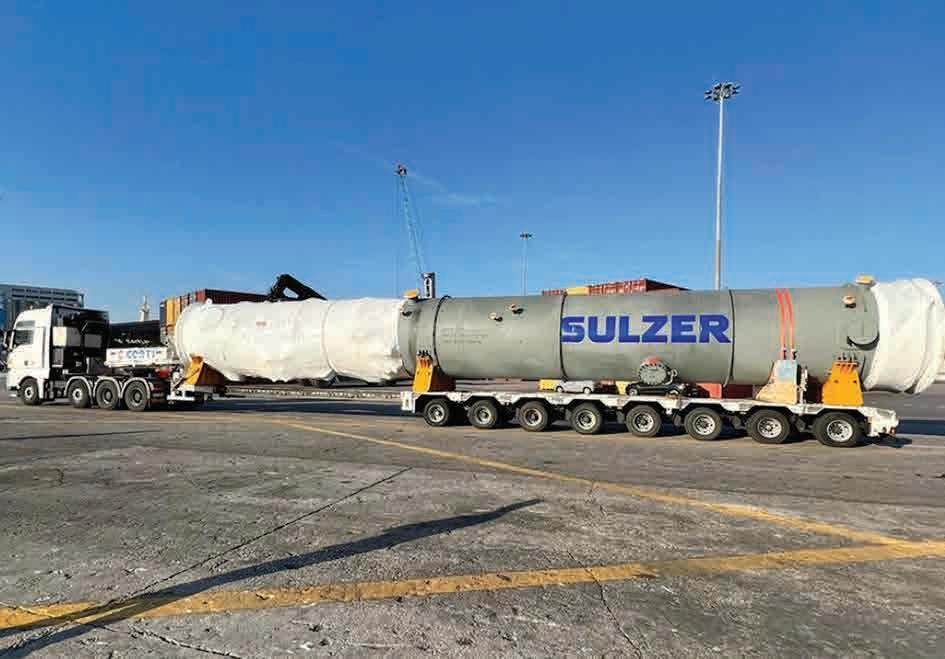
5 minute read
Sulzer Chemtech’s crystallization technology helps drive DSI’s growth
Song Ho Kim, President of DSI, says: “We are extremely happy with the collaboration established with Sulzer Chemtech. Their solution for crystallizing naphthalene is a leader in the market, so when looking at advancing our offering, we were confident we should invest in this technology. The flexibility of our operations will also be improved, helping us address different market needs while optimizing operational expenses and profitability. We look forward to installing the unit and beginning our first-grade naphthalene operations shortly.” can be used that can be used for applications with stringent quality requirements.
DSI’s facility in Serang processes naphthalene from coal tar to deliver the valuable chemicals. To this end, the plant has been producing naphthalene related products.
In order to increase the purity level of its raw materials and end products as well as serving the broader downstream sector, the company sors worldwide, enabling them to deliver high quality aromatics.
Prior to the delivery of the purification unit, Sulzer Chemtech completed extensive feasibility and pilot testing ahead of its basic engineering package. This helped ensure DSI to produce different concentrations, including levels of up to 99.9 wt% at an overall production capacity of 7’000 metric tons per annum.
Etienne Rigaut, Head of Crystallization at Sulzer Chemtech, adds: “For decades, we have been supporting the most challenging separation processes with state-of-the-art crystallization equipment. Thanks to our extensive expertise, combined with testing and engineering capabilities, we have been able to deliver a customized unit that will help DSI enhance its competitiveness in the marketplace. We strive to support our customers and the entire sector with cutting-edge technologies.”
Visit: www.sulzer.com
Precise gas mixtures even at high flow
For applications needing high flow rates of gas mixtures, such as steel production or the chemical industry, WITT offers the MG 2000ME ERC+ electronic gas mixer. Precisely and reliably, the device generates high-quality gas mixtures of two technical gases, even when the flow rate is fluctuating.
Inside the new top model from the market leader is an electronically operated proportional valve that achieves a maximum mixed gas output of up to 2,180 Nm3/h. The system is controlled either remotely via Ethernet or analog output, or directly on the unit via an intuitive touchscreen. The seamless mixture adjustment is thus particularly precise, and stored mixture specifications can be easily reproduced. When operated remotely, the user can control and see the system status at any time and from anywhere in the world.
The system keeps the mixture and outlet pressure stable, even when the flowrate is changing. In this way, the user obtains a precise mixture over the entire output range, even with cycling flowrates.
Certainly the correct gas mixture
With its numerous features, the WITT gas mixer ensures a particularly high level of process reliability. Pressure fluctuations in the gas supply are compensated by a constant pressure control and have no influence on the mixture quality. Optional pressure and temperature transmitters monitor the gas supply. Excessively low inlet pressures or temperatures generate an alarm and shut down the system. The setting of the mixing valve is maintained even when the mixer is switched off. This means that after a restart, the required mixture is generated again immediately.
For even greater certainty, the mixer can be optionally equipped with an integrated gas analyser for monitoring and documenting the gas mixture.
High quality, flexibility and economy
Like all WITT gas mixers, the MG 2000-ME ERC+ offers the user major benefits : It reliably generates precise and absolutely homogeneous gas mixtures of the highest quality. In addition, it offers the highest possible flexibility with regard to mixing ratio, gas quantity and place of use. By using comparatively inexpensive standard technical gases, the on-site generation of mixtures with the low-maintenance WITT unit is particularly economical.
Depending on the requirements, WITT gas mixers are available in various designs for almost all technical gases and different performance ranges.
Visit: www.wittgas.com
Beyond Ionomers: Regulation Drives Demand for New Fuel Cell Membranes, Finds IDTechEx Research
Membrane materials are of fundamental importance for fuel cells. So significant, in fact, that they typically give their name to the fuel cell, as is the case for Proton Exchange Membrane (PEM) fuel cells, with IDTechEx forecasting the market for ion-exchange membranes in PEM fuel cells to be worth over US$1.1 billion by 2033. Typically, the material of choice for PEMs is an ionically conducting polymer known as an ionomer. These ionomers are one of a family of perfluoroalkyl substances (PFAS), and concerns are mounting regarding PFAS, with alternative materials beginning to emerge.
The new IDTechEx report, "Materials for PEM Fuel Cells 2023-2033", gives a detailed technical overview of membranes and other key components for PEM fuel cells, an analysis of the major players, and also includes granular 10-year market forecasts for key fuel cell components and materials in terms of both units and volume. IDTechEx has also extensively covered the electric vehicle industry and forecasts demand for fuel cell electric vehicles (FCEVs) in "Fuel Cell Electric Vehicles 2022-2042".
The PEM enables the functionality of the fuel cell by transporting protons from one side of the cell to the other while keeping the different fuels separated. In the report, IDTechEx provides extensive benchmarking of the market leader against competing ionomer materials for three of the most critical parameters for PEMs; electrical resistance, ion exchange capacity (IEC), and membrane thickness. Despite transporting protons, it is imperative that the membrane has high electrical resistance to avoid short-circuiting the cell, while the combination of high IEC and thin membrane increases the fuel cell performance by enabling rapid proton transport. Promising alternatives exist, with performance exceeding the market leader in the three previously mentioned categories; however, the latter remains dominant due mainly to its position as the first mover in the market. Although dominant, ionomers are a PFAS-containing material and are subject to many of the concerns relating to PFASs. PFASs are considered "forever chemicals" due to the strength of the fluorine-carbon bond, with several health risks associated with accumulation in the human body, such as liver damage, kidney cancer, and reduced response to vaccines. PFASs are transferred to the water cycle during their manufacturing stages, use in industrial processes and end-of-life treatment, leading to inevitable exposure for organisms. Bioaccumulation occurs in the tissue of organisms, such as fish in polluted waters, and this is then transferred up the food chain, including to humans.
On the back of these current and proposed restrictions, many companies are moving to reduce their reliance on PFASs. An interesting case study is the American company 3M. Having produced PFASs since 1947, 3M announced in December 2022 that it will cease the manufacturing of, and work to discontinue the use of, PFASs by 2025. 3M cited regulatory restrictions, consumers becoming "increasingly interested in alternatives" and operational difficulties as primary reasons for exiting the PFAS market.
So, what does this mean for fuel cells? Ultimately IDTechEx expects to see the beginning of a transition away from PFAS membranes to alternatives (including hydrocarbons) within the next three to five years. Prototype developmental projects are underway with various OEMs and novel materials gaining traction, predominantly at an academic level, such as metal-organic frameworks (MOFs), although these materials are still at an early stage with little commercial uptake. Historically, hydrocarbons have not seen success as membrane materials due to their tendency to disintegrate in the harsh chemical environments within the fuel cell. However, recent advances at companies such as Ionomr Innovations have seen the development of hydrocarbon ion-exchange membranes capable of fulfilling the requirements for PEM fuel cells without the health and environmental concerns associated with PFAS chemistry.
For more details on the materials demand, trends, and emerging novel alternatives to the incumbents for PEM fuel cells, please see the IDTechEx market report "Materials for PEM Fuel Cells 2023-2033". For more information on IDTechEx's other reports and market intelligence offerings, please visit www.IDTechEx.com.