
4 minute read
PREMIUM LEATHER FROM AUSTRIA
Wollsdorf, headquartered in the Austrian state of Styria, has become a recognised producer of leather products, shipped to customers around the world. Founded in 1937, the Austrian manufacturer draws on decades of experience and extensive know-how. Today the company produces high-quality, highly durable leather furnishings using both high-tech manufacturing processes and traditional craftsmanship.
Its diverse product range provides a high degree of flexibility and allows the company to individually address individual customers’ needs. Wollsdorf’s all-in-one solutions range from whole leather hides, leather cut parts, lamination and perforation serviced to ready-stitched and certified dress covers.
The automotive sector is the strongest market – here Wollsdorf’s products can be found on the steering wheel, car seats, dashboard, gear stick and more. The company also has a strong position in other sectors, including furnishings and aviation: Wollsdorf offers perhaps the lightest bovine aviation leather in the world, used on more than 195,000 seats worldwide.
In addition to its corporate headquarters with its fully integrated leather tannery in Austria, Wollsdorf also operates production and sales sites in other countries, employing some 1,500 people across its locations. Wollsdorf premium leather goods are produced in China, Croatia and Mexico and the company offers a direct line of contact to customers in the United States and Uruguay.
Tradition meets innovation
The art of leather-making requires comprehensive expertise and up to 160 manufacturing steps in order to turn a perishable rawhide into a resilient leather product. Combining its long-standing experience with highly advanced manufacturing processes and traditional craftsmanship, Wollsdorf creates expertly processed products with a long lifespan that look and feel great and are available in a wide variety of colours.
These leather products can be fully customised. Numerous options are available: leather thicknesses from 0.6-3.0 mm, leather with natural grain or embossed leather as well as a broad colour spectrum, and more.

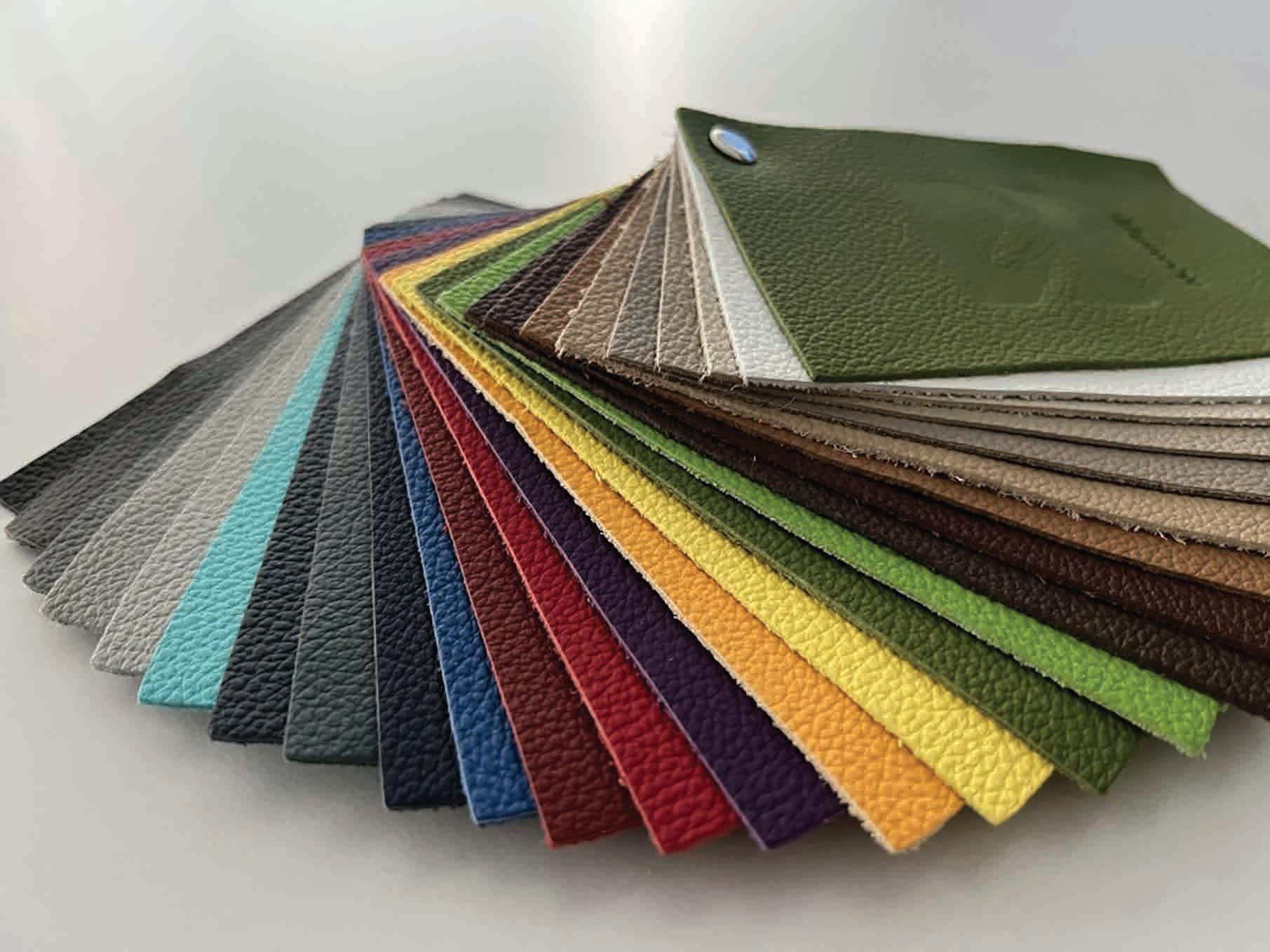
Research and development form the basis for creating premium and sustainable leather products. An innovative spirit, modern testing equipment and an optimally equipped laboratory also allow for the development of alternative manufacturing processes and creative surface materials.
Ahead of trends
Wollsdorf has pioneered a number of technical solutions including cool leather that does not heat up when exposed to direct sunlight, and shrink-optimized leather for instrument panels.
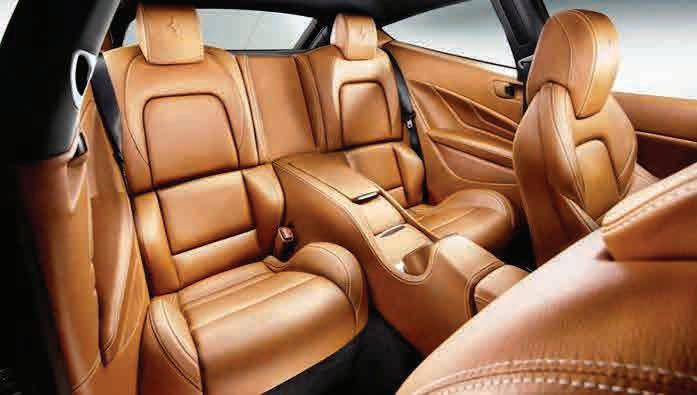
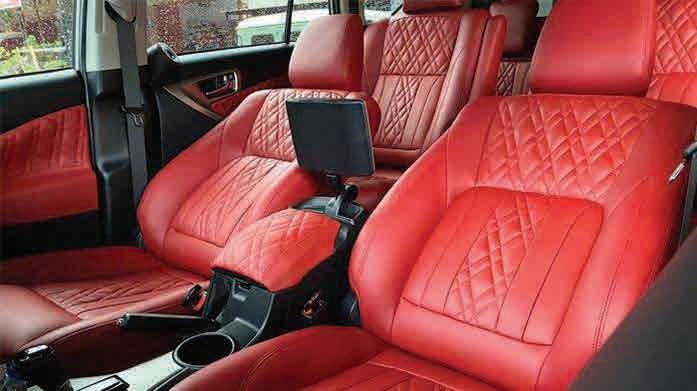
Another innovative product for the aviation industry, developed for Lufthansa a few year ago, was Wollsdorf’s Amba Eco FOC leather, which boasts a weight reduction of as much as 40% compared to standard aircraft leather without compromising on properties such as tensile strength.

Wollsdorf can manufacture leather without the use of heavy metals, chrome and glutaraldehyde, and has developed its EVO+ surface protection that sustainably reduces bacteria on leather surfaces by 99.9%. EVO+ is integrated directly in the dyeing system and guarantees the protection of leather over the course of the product’s entire life cycle.
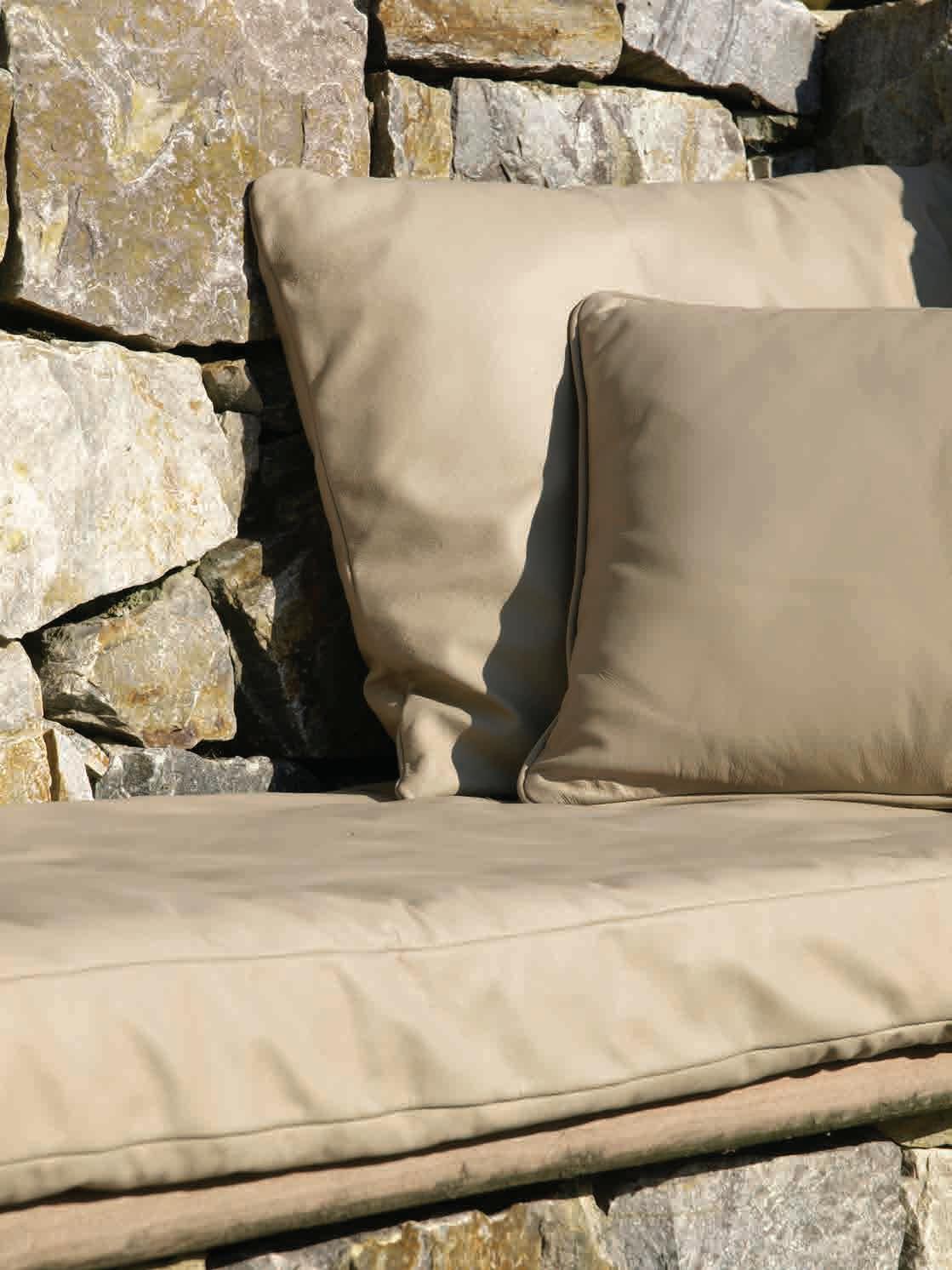
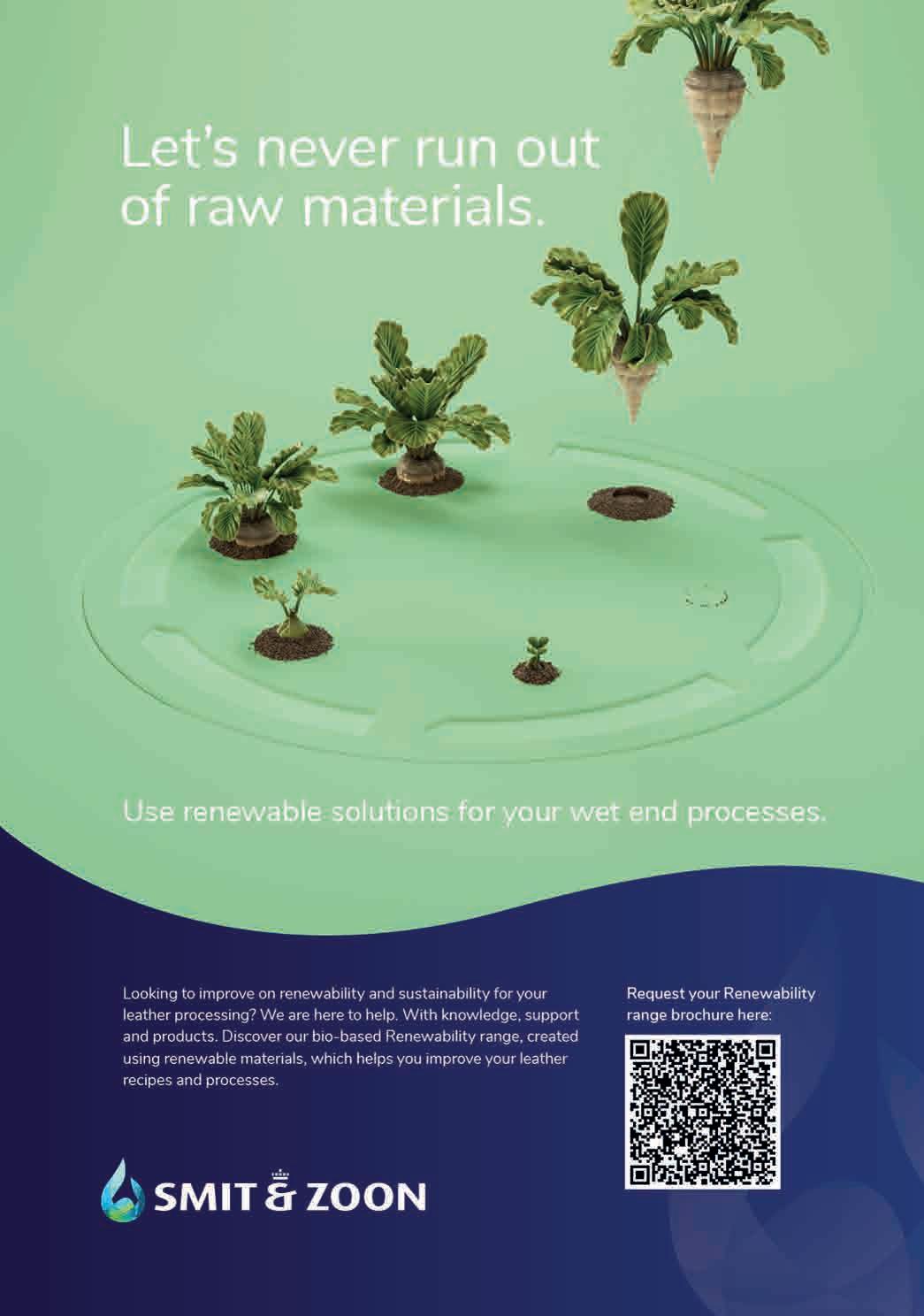
For applications where an alternative material is required, the new synthetic surface WolSynt®, a high-quality synthetic surface based on PU, is ideally suited. It is vegan and free of PVC as well as solvents and critical plasticizers.
In line with nature
Wollsdorf Austria has been relying exclusively on green power since 2012. Around 80% of the electricity used group-wide is CO2neutral. This gives annual savings of approximately 4,600 tonnes of CO2. Wollsdorf can thereby provide an essential contribution to climate protection and the fight against global warming.
In 1998, Wollsdorf was the world’s first tannery to receive the ISO 14001 environmental certificate, and the company remains focused on the sustainability of new products and solutions, continually optimising its processes at all its locations.

Low-emission leather guarantees that environmental and healthrelated burdens from the tanning process are minimised over the entire life cycle until recycling or disposal.
On the resources side, the company reduces water consumption through process optimisations and recycling. Waste water at Wollsdorf is treated and purified in an elaborate process and reintroduced into the natural water cycle. Waste materials are recycled, thermally utilised, harnessed for energy recovery or upcycled.
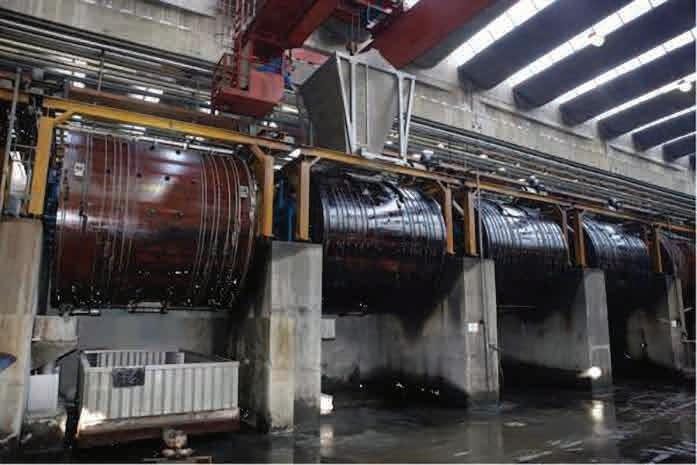

Exceeding clients’ expectations
The company claims that it conscientiously insists on species-appropriate animal husbandry and the consistent fulfilment of ecological procurement criteria when selecting its suppliers – only hides from healthy and uninjured animals can be processed into premium leather and other products.
None of the animals used by Wollsdorf for leather production are butchered for their hides, since the rawhides are a by-product of the meat and milk industry – a perfect example of upcycling whereby otherwise superfluous materials, i.e. the hides of animals, are processed into sustainable and valuable products.
In 2000, Wollsdorf became the first leather producer in the world to be awarded the ISO/TS 16949 quality certificate and was also EN 9100 certified in 2007. The result of these efforts is a range of exclusive leathers that meet and exceed the high expectations of customers all over the world.
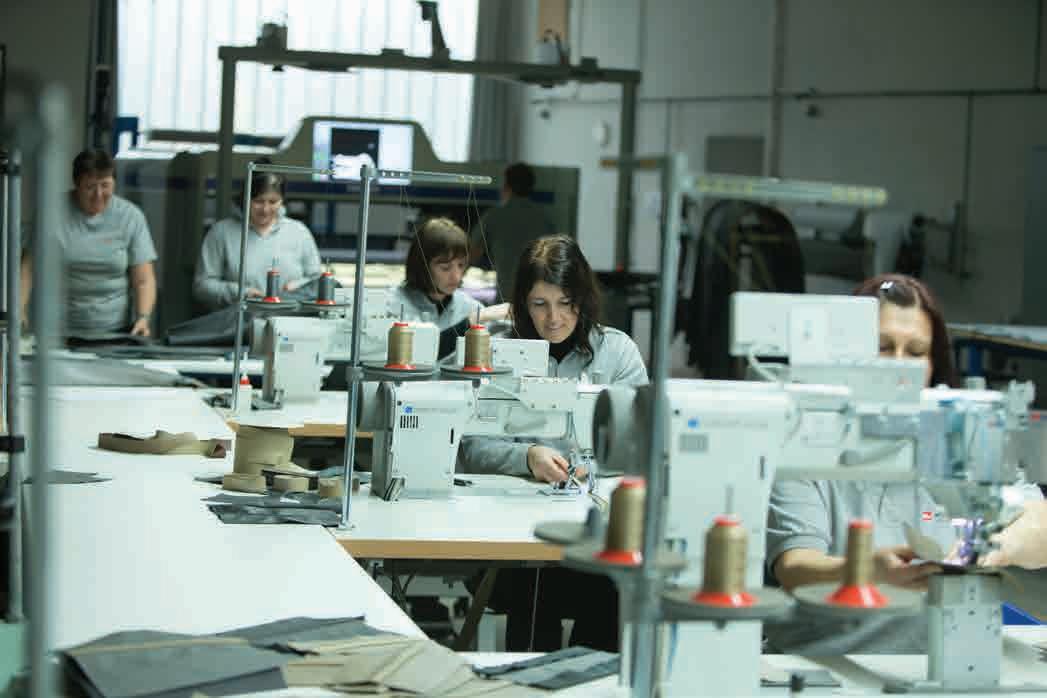
New developments in the Consumer Goods
Avantium and Henkel sign offtake agreement on FDCA for adhesives to be used in electronics applications
Henkel and Avantium have been partners since 2019, when Henkel joined the PEFerence consortium1 . This consortium of partners, coordinated by Avantium, aims to establish an innovative supply chain for FDCA and PEF (polyethylene furanoate). As part of the PEFerence project, Henkel has tested and positively evaluated the feasibility of FDCA for the use of polyurethane adhesives. Now Henkel has decided to proceed and bring those adhesives to the market for the use in electronics applications, such as consumer devices.
For many years, Henkel has been committed to sustainable business practices. As a market leader for adhesives, sealants and functional coatings, Henkel is making an important contribution to climate protection by embracing innovative solutions that facilitate recycling and enable CO2 savings across the value chain. “Henkel is constantly innovating high-quality and sustainable adhesives to support our customers and ecosystem partners in their implementation of a circular economy. Avantium’s 100% plant-based FDCA enhances our strategy to incorporate renewable carbon into our technology roadmap while offering improved performance in our products. We look forward to continue working with Avantium in the years to come. For us, this is just the start as we see high potential for FDCA in application areas beyond electronics, such as packaging, wood construction or textile lamination”, says Adrian Brandt, Head of Bio-Renewable materials team at Henkel Adhesive Technologies.
Bineke Posthumus, Director Business Development of Avantium Renewable Polymers , comments: “We are very pleased that yet another partner of the PEFerence consortium has decided to sign an offtake agreement with Avantium. One of the benefits working with such diverse group of reputable companies within the PEFerence consortium is that it enables us to create new applications for FDCA and PEF. The decision of Henkel to use FDCA for polyurethane adhesives for use in electronics applications is a great example of the possibility to use our high-quality, plantbased chemical building block FDCA in various markets and applications.”
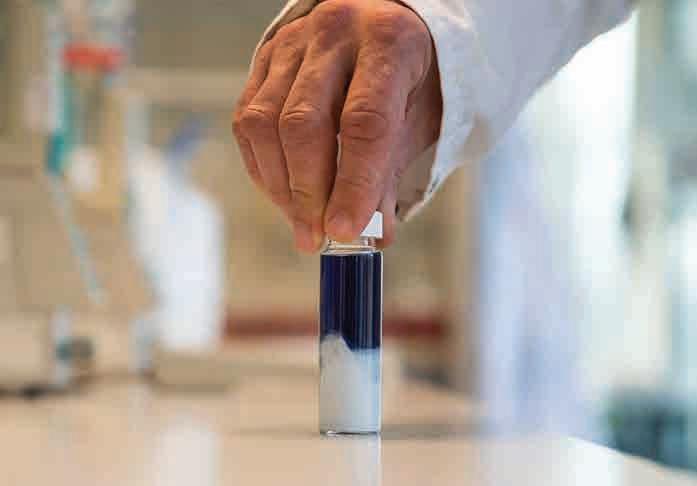