
29 minute read
COVID-19
GETTING BEHIND CLEANING AND DISINFECTING TO FUTURE PROOF SURFACES
Whiteley Corporation managing director Darran Leyden
Advertisement
After almost a year of being obligated to becoming COVID-19 sensitive, it is important to consider if we have developed a good understanding about the most effective way to keep surfaces free from the potential transmission of the virus.
There is a clear difference between cleaning surfaces, as opposed to disinfecting them to reduce the risk of spreading infection.
Most realise now that social distancing, the wearing of masks and good hygiene through hand washing, play such an important role in keeping the spread of coronavirus down. But so too is how thoroughly we clean and disinfect hi-touch areas, exposed to the easy spread of the virus.
Industry Update delved deeper into the topic, catching up with Whiteley Corporation which has been leading the way in manufacturing infection control products for more than eight decades.
It is a subject that cannot be taken lightly. Australia and the world may have lesser numbers of COVID-19 cases, but new infections are still emerging and fatalities are a persistent result.
There are also places, like India, the US and Brazil, where new cases continue to be dangerously high, meaning it is vital countries share information and any new learnings about how we can keep the spread of the pandemic down.
As we approach the hotter months, and at the time of reporting, Australia’s national COVID-19 cas-es were 27,317 while the global total of those that had contracted the virus stood at 38 million.
The state of Victoria, which suffered the highest number of cases in the country, is recovering from a disastrous second wave through strict lockdowns, with cases down to about 10 each day.
The target of the Victorian government is to keep the number of new cases per day to five or under over a 14-day period before gradually lifting all restrictions.
However there continues to be marked spikes of new cases through community spread or un-known sources, so Victoria remains diligent in its calls for stringent practices in mask-wearing, now calling for the use of properly-fitted masks, especially in areas where there are known COVID-19 cases.
This tells us that we are not quite out of the woods; the pandemic continues to spread although it may be in smaller numbers.
Infection product experts, Whiteley Corporation says, the spikes and erratic number of cases may continue for a while yet.
Whiteley managing director Darran Leyden says there are many things we can do in our homes and work environments to keep the spread of coronavirus down.
He says good surface cleaning complemented by good disinfection process is an essential tool in keeping the infection spread of COVID-19 at its lowest.
In an industrial workplace or warehousing environment, Mr Leyden says hand-hygiene is funda-mental in stopping the spread.
“It is important of course that both employers and employees are conscious of the right preventive guidelines and as well as the legal guides to ensure they know what is good for their operations,” Mr Leyden said.
“It is good for employers to make sure there are sufficient hand-hygiene products available for staff to wash their hands appropriately. And if there’s no hand soap available that staff can use alcohol-based hand sanitisers,” he says.
More importantly, Mr Leyden says, employers should be increasing their cleaning and disinfecting frequency on their workspaces.
There is significant difference between cleaning and disinfection. “Cleaning is about the removal of biological soil and disinfecting is about killing the micro-organisms. If you’re going to disinfect the surface, you need to clean it first.”
Whiteley Corporation recommends special attention be paid to surfaces which are going to be touched more often than others – such as door handles, kitchen benches, or what they call the high-touch areas.
Whiteley recommends that the frequency of cleaning and disinfecting be based around risk and how often things are touched in those areas.
The general rule is that if its touched frequently then it should be cleaned and disinfected as fre-quently.
Mr Leyden refers to his company’s research which shows that contaminated surfaces touched by a hand can actually transfer germs x19 to different surfaces.
“Say for instance someone coughs on the surface and doesn’t clean, wipe it up and disinfect it and then someone puts their hand on that surface. That means that with the next 19 touches they can potentially spread infectious material.”
As soon as the COVID-19 breakout was announced, Mr Leyden says his company increased its cleaning frequency substantially. It used both detergent to clean and appropriate disinfectant on workspaces and other surfaces.
Whiteley Corporation believes many small- and medium-sized businesses which may have fewer resources are mostly doing a good job of future proofing their work environments against the spread of COVID-19.
Whiteley Corporation, a leader in research and innovative product development in the field of hy-giene, cleaning and infection control products, had its beginnings during World War II.
Managing director Darran Leyden says Whiteley was already making disinfectants for cinemas and theatres, which extended over to the war effort, helping with disinfection needs.
“We actually started in 1933 as the Australian General Disinfectant Company,” he said.
“For the last 87 years we’ve been making surface disinfectants and we’ve been involved in infection prevention products since then.”
The range of infection prevention products Whiteley manufactures includes hand hygiene products, surface disinfection, disinfectants and detergents, instrument detergents and disinfectants and steroids in the health care sector, as well as industrial cleaning products.
Mr Leyden is keen to see claims made about surface and instrument disinfectants to be evaluated by federal regulator, the Therapeutic Goods Administration (TGA).
“I think some have done a good job and maintaining a good work environment as best they can, and some people probably need to re-think where they are as far as risk is concerned for their staff.”
Mr Leyden concludes that cleaning, disinfecting and hand hygiene and infection prevention against COVID-19 are of the most important business practices in the current climate.
“It’s all about staff safety and trying to keep it that way as often as possible. If there is an outbreak in workplaces or factories, sometimes you just can’t prevent this. But by being diligent with your cleaning, sanitising and disinfection practices, you have minimised the risk for your staff and your
HOW WHITELEY SET THE STANDARD
business.”
“The TGA has a series of disinfectant tests and quite stringent tests that companies need to follow in order to make specific claims,” he said.
“Unfortunately with the pandemic we’ve seen some in the industry making unregistered claims and then being fined by the TGA.”
Mr Leyden says it is very important for companies providing products, and customers looking for them, that the products are registered the correct way.
“Business and consumers will know what they are getting because it is listed in the publicly regulat-ed market.”
Under the TGA guidelines, there are now about 45 products registered with claims on COVID-19 and the list is growing.
“We’re very proud that we we’re the first to actually negotiate directly with TGA the pathway for test-ing to get a COVID-19 claim.”
“Our product Viraclean was the very first one approved by the TGA under their new framework for COVID-19 testing,” says Mr Leyden.
EARLY WARNING TOOL IN SEWAGE KEY TO ASYMPTOMATIC COVID-19
Scientists of a joint CSIRO-University of Queensland team have uncovered a method for SARS-CoV-2, the virus that causes COVID-19, to be detected in sewage samples.
The analysis is accurate enough to detect the presence of the virus days before positive cases are observed in public screening programs.
According to CSIRO member Dr Paul Bertsch, this virus detection within our pollution is a critical element of public health response.
“We use filtration techniques to separate out the nano-scale viral and gene fragments from untreated wastewater, then ‘amplify’ the fragments, enabling us to isolate and confirm the virus’s fingerprint over any other genetic material present in the sample," Dr Bertsch said.
The team began sampling wastewater from treatment plants in Brisbane earlier this year, amid the first wave of COVID-19 in Australia.
Dr Borsch says that while the wastewater sampling cannot fully replace individual sampling, it can provide unique information into people who are carrying the virus but are also asymptomatic.
“Many experts say we’re a long way from having a vaccine.”
“So a national wastewater surveillance program or network could help Australian authorities detect and contain emerging COVID-19 clusters faster and more costeffectively.”
The testing of wastewater could also be highly beneficial for people travelling on cruise ships, preventing any sick passengers from disembarking.
“Scientists, disease ecologists, and epidemiologists have been predicting the emergence of other pandemics following the SARS and MERS outbreaks earlier this century.”
“We need to prepare for future pandemics. The economics of permanent sewage surveillance stacks up.”
He says it doesn’t take much to close down entire economies from a pandemic breakout.
Meanwhile, with the latest update from the state of Victoria, 13 new coronavirus cases were recorded overnight with another four people losing their lives.
Premier Daniel Andrews has announced that workers in high-risk industries will be asked to participate in a new Surveillance Testing Program in
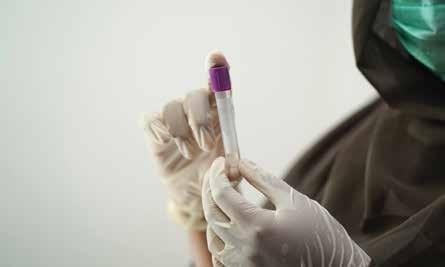
a bid to stamp out any new coronavirus outbreaks.
Starting with the food production sector, the new program will test 25 percent of staff in high-risk workplaces each week.
Those among the supermarket, refrigerated, meat, poultry and seafood processing and distribution sectors will be asked to have a quarter of their staff tested on a week by week basis.


FACE MASKS UNMASKED: WHAT YOU NEED TO KNOW TO KEEP YOUR STAFF SAFE
As Australia and the world reaches the seventh month of the COVID-19 pandemic, there is growing business and consumer interest about mask- wearing and its importance in preventing infection.
Science has established that properlymade masks do work in reducing the risk of further transmission.
The important role of masks is that it creates a barrier against the virus by minimising its spread through air droplets arising from when one sneezes, coughs, speaks or even breathes.
If any of these droplets land on a surface there is a possibility that if the surface with the virus droplet is touched by another, it can spread up to nineteen times more each time it is touched.
The other common way the virus is spread is when hands carrying the virus touch the face. The virus is then spread by entering the respiratory system.
The most effective method of minimising transmission is wearing of masks combined with diligent hand hygiene and maintaining 1.5metre social distance from others.
Research into how the virus behaves indicates that it can travel up to 1.5 metres to further infect quickly within
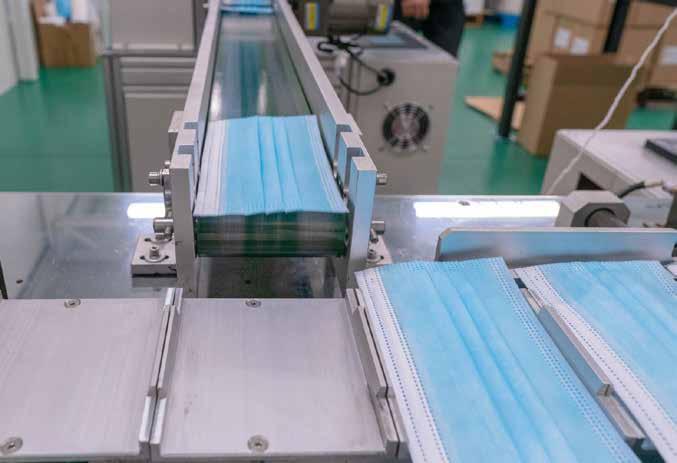
a short span of time, making it a virus difficult to contain.
In enclosed environments or within areas where there is already a known spread of COVID-19, the wearing of masks provides an even more important physical barrier for users and those around them.
Key Signatures’ Australian-made Level 3 masks meet the toughest Therapeutic Goods Australia specifications, consisting of four layers of Australian made material and finished to the most rigid standards.
The company believes that having safety and protective equipment such as Level 3 masks available to staff and communities readily, helps keeps business open during COVID-19.
Owners Rebecca Michelini and Jodie King believe that as business gradually re-opens in Victoria, it is important for employers to reassure employees and customers that they are being protected with quality Australian made masks, while also supporting the local economy.
Ongoing global studies also indicate that the virus can be carried without showing any symptoms and this can last for a few days,up to months in some cases.
There is no way of knowing if you or people around you are carrying the virus
GETTING THE RIGHT MASK
at any one time unless a COVID test is
Ms Michelini suggests two simple tests when selecting masks – the breath test and the water droplet test.
If you breathe into the mask and you can feel your breath through it, it is inefficient and unsafe. If droplets of water pass through it, it is in the same category.
Key Signatures also has created specific education resources to assist in understanding, caring for and using masks and general protective equipment, such as anti-bacterial wipes, thermometers, and disposable gloves aprons.
The business also is able to provide these products in bulk through its headquarters in Melbourne. conducted through a swab sample that identifies the pres-ence of the virus within one’s body.
Around the globe there is a race to find a vaccine, Australia included, but reportedly the earliest time antiCOVID-19 vaccines may become available, is in a year’s time. Hence, the donning of face masks has become almost non-negotiable during the pandemic, as even though there are lesser cases in some states, the virus continues to spread.
Studies conducted by Larisa Labzin of the Institute for Molecular Bioscience, The Uni-versity of Queensland, indicates that the wearing of masks has strong impact on recovery capacity if you contract COVID-19. Not wearing masks can expose individuals to higher density of infection and hence potency of the virus.
“ How we wear the mask matters, as touching it often and not completely covering the nose and mouth renders it ineffective,” Ms Labzin says.
“Finally, even with asymptomatic infections, we don’t know yet what the long term effects of COVID-19 are. That’s why wearing a mask is a responsible thing to do, even if we feel fine.”
How do we know if we are using the right masks?
There are three types of mask commonly used in the market. These include the N95 or P2 “respirator” masks worn by many health-care workers.
Then there are the Level 2 and Level 3 masks most people in the community use, along with fabric or cloth masks.
More states are building partnerships with scientific bodies like the CSIRO and business, to jointly seek NATA accreditation where applicants undergo stringent efficacy tests, to become registered in producing the right quality of masks for Australian use, rather than relying on imports.
The federal government has made available joint funding to the manufacturing sector so businesses are able to pivot into mask making and massproduction quickly and efficient-ly.
There are a handful of business in NSW, Melbourne and Queensland that have attempt-ed to join the pivot to manufacture masks locally.

An industry-led company based in Melbourne, Key Signatures, is one of them. It has been producing personal protection (PPE) equipment and masks for a year now, specifi-cally targeting the Australian workforce.
Managing director Rebecca Michelini says the company had no choice but start to pro-duce masks and PPEs, because this allowed it the most security over the manufacturing process, as well return profits and jobs to the Australian economy.
Regular testing for safety
Being a key supply provider for the health sector in Victoria, Key Signatures send its masks to local laboratories for regular testing to ensure their ongoing safety.
“There are key points to consider when looking for the right type of Level 3 masks, which is what we test our masks on – the level of filtration and the fit, and fluid resistance to pre-vent droplets penetrating or escaping,” Ms Michelini says.
The wearer should always check to ensure the fit is right so it forms a seal around the face and businesses check with manufacturers over how long a worker can wear the same mask on a shift before replacing it.
Ms Michelini is an advocate for keeping business open in Victoria and the implementa-tion of different safety strategies to make that happen within a pandemic environment.
“COVID-19 will continue into the foreseeable future, and most Australians have never had to wear a mask or worry about buying them before – until now,” she says.
Key Signatures also found there were very few educational resources on what consti-tutes an effective and appropriate

mask. This led Key Signatures to create videos and re-source content to fill the void.
By manufacturing face masks, with independent testing on products on daily production runs, Key Signatures can ensure the quality of its masks.
Along this journey, Ms Michelini, found that the quality of some masks were typically of low grade, including some not even passing the most basic tests. Many simply broke.
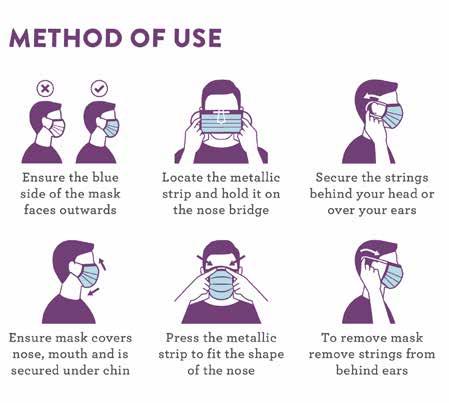
To resolve this, Ms Michelini created Key Signatures, which now manufactures quality masks in Victoria and also educates businesses and local communities about the varia-tions of mask levels, how to correctly wear, care and dispose of masks and the importance of quality products.
“I’m sure that like us, you want to keep your staff safe at work. It makes good moral and economic sense as well."
Key Signatures https://keysignatures.com. au/manufacturing-industry/
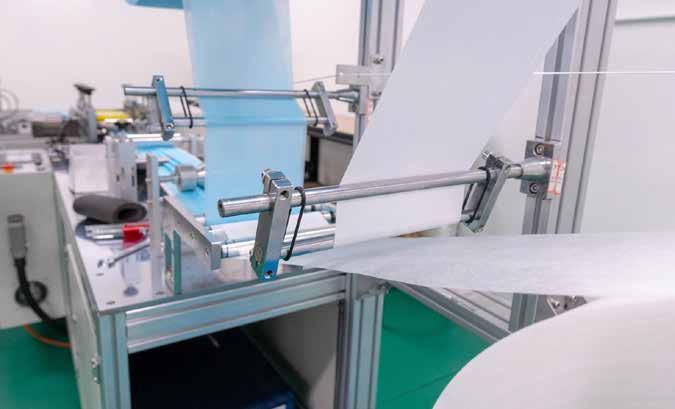
ELON MUSK ANNOUNCES INTENTION TO MINE BATTERY METALS
TESLA founder and Chief Executive Elon Musk has revealed that the company is planning to break into the battery metals mining industry.
Standing alongside manufacturing industry executive Drew Baglino, TESLA had acquired the rights to a lithium clay deposit in Nevada.
According to Baglino, TESLA will leverage its US resources for nickel and lithium mining.
“Just doing that and localising our cathode supply chain and production we can reduce the miles travelled by all of the materials that end up in the cathode by 80 per cent."
“Nobody has done this before to our knowledge and it’s a very sustainable way of obtaining lithium, all of the elements are reusable."
Elon Musk said there was a massive amount of lithium in Nevada, enough to convert every car in the US to electric vehicles.

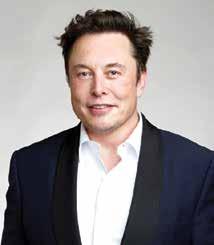
“There is enough lithium in the US to convert the entire United States fleet, the 300 million vehicles to lithium, using only lithium that is available in the United States that we already know exists.”
The announcement is part of Tesla’s plan to be self-sufficient, significantly reducing costs and the hundreds of kilometres that need to be travelled before materials used in electric vehicles (EVs)
MANAGING MENTAL HEALTH IN A CHANGING WORKPLACE
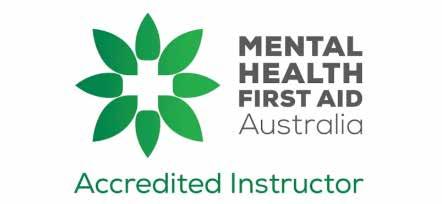
In theory, maintaining and growing a successful business is simple. Great products and good staff support the business.
It turns out creating and marketing the product is the easy bit; keeping good staff is the challenge. Industry knows that valuable employees are reliable, loyal and keen to see the business succeed.
However, good staff are also human. The ebb and flow of daily life can impact and adversely affect productivity.
When a valuable employee explains they have a health issue, this is resolved relatively easily: questions are asked about medical treatment and a back to work timeframe. Job done.
So what happens when an employee comes to you with a mental health issue? When asked, many managers struggle to answer, hoping to avoid such a situation.
The simple answer is to have staff trained in Mental Health First Aid.
Mental Health First Aid officers are an emerging trend in companies. Trained to provide initial support to other employees in the workplace, as well as complimenting more formal support services, Mental Health First Aid officers give your employees an outlet that’s increasingly necessary in modern life.
Accredited Mental Health First Aid training is available. Due to current restrictions the MHFA course is available online and offers instructorbased and e-learning sessions that include relevant workplace scenarios.
To take advantage of this opportunity contact accredited MHFA instructors Jan Fisher on 0403 912 890 or Melitta Pinney on 0408 266 267.
https://melittapinney. com.au/mental-health-firstaid-training-course/
FOR SALE UNIQUE OPPORTUNITY
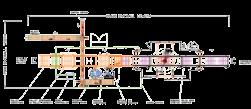
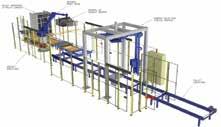
Motopal-1120 Palletiser & Stretch Wrapper
“Half replacement cost “ up to 30 Shelf ready cartons min. A major Sydney food producer have built a new plant & will no longer require the only “two year old” exible Robotic Palletiser system including stretch wrapper as a complete line. Available Beg Nov 2020

As a publicist for the last 50 years, I read with a pinch of scepticism the multiple warnings the Australian economy risks “falling off a cliff” much higher than the 1991 recession if State and Federal Governments halt spending on Covid relief packages.
For a start, they won’t halt spending.
The manufacturing, mining and other welcome measures announced recently and also contained in the Federal Budget demonstrate that the wise counsel from multiple parties across party lines is being heard in the Federal and State capitals.
This includes the representations of big business, big unions and everyone else with a legitimately vested interest in restoring our national economic recovery after the huge hit it has taken.
But it is worth standing back and sorting the likely reality from the strident calls from these legitimately vested interests benefitting from current wage supports and other incentives.
Because it is a fact of public life that if you introduce measures that give support to particular sectors, you create an instant pressure group that will howl with discontent when there is a threat of them reducing.
So my point – as a former journalist and political press secretary – is that you have to listen carefully and form your own balanced judgement about what the likely future reality will be.
There is no doubt this Covid situation is serious and will be enduring. It is more serious than the five or six major economic disruptions I have worked through over the last five decades, starting with the oil price shock in 1974. Remember that? By March 1974, the price of oil had risen nearly 300%, from US$3 per barrel to nearly $12 globally.
Those were the days when some of the fossil-fuel dependants in Australia and New Zealand – myself included – could only use their cars on alternate days according to odd and even number plates.
NZ suffered losses of 100,000 skilled workers, mostly to Australia, from a labour pool of about a million. I was working with the NZ Prime Minister’s Economic Advisory Group at the time (remember Piggy Muldoon?) and putting out messages to interest groups (employers, unions et al) about how the economic pie had shrunk and we would all be getting less.
I moved to Australia to be greeted a decade later by the 1987 stock market crash when the Dow Jones fell overnight by 22.6 per cent (508 points). The Australian share market lost around 25% in one day and 41.8% of its value by the end of October.
But both markets came back strongly.
Falls of similar magnitude seem minor when the Dow rides at 26,000-28,000.
Such falls are now just a bad night, not a tectonic shift as it was headlined then.
That doesn’t mean they won’t happen again, with flow-on effects for business, but history suggests it would recover again even if this did happen (and probably sooner than expected, given that human beings by and large are optimistic creatures, who prefer to build for success than plan for failure).
Move forward another decade to the 1990s with Australia in the “Recession we had to have” (Paul Keating, 1990), then tech stock bubble, then the Global Financial Crisis from 2002. We picked ourselves up, dusted ourselves off, and put in a world-class performance economically. Then along comes Covid. What’s different this time is the magnitude of the problem. It is a huge problem. But it is also engendering a huge response. And one that does engender some optimism among the more general gloom of the daily commentators. Take the comments of John Edwards, of the independent Lowy Institute, for example. He recently gave us some perspective and pointed out that, after infections of more than 23,000 Australians, and the deaths of more than 420 (at the time he wrote), the coronavirus is fading sooner and with less economic damage than expected. “Despite Victoria’s second wave of infection, Australia’s economic recovery from coronavirus is under way,” he says. “The bitter aftermath includes high and rising unemployment, vastly increased government debt, and a markedly less congenial global economy.” “Though formidable, the fiscal challenge is well within Australia’s means, especially if the Reserve Bank remains willing to acquire and hold Australian Government debt. It may need to anyway to suppress an unwelcome appreciation of the Australian dollar in a world where major central banks are committed to low long-term interest rates. “Australia’s increasing integration into the East Asia economic community offsets the draft BRENT WHYTE - MANAGING DIRECTOR OF WHYTE PUBLIC RELATIONS
from the major advanced economies, but the US- China quarrel and the dislocation of global trading and investment relationships it threatens heightens the tensions between Australia
WE’RE HEADED FOR A CLIFF, AREN’T WE?
economic and security choices.” So, not all bad, not all good.
And, as most of us right now are focussed on survival, it might also be time to look ahead and position ourselves for change. Change, along with taxes and death, is one of the few absolute certainties of life.
Amidst change, we can either adapt and plan to succeed, or not adapt and let failure take its course. It is a clear choice, a strategic vision. Even if the path to success is complicated, businesses have to start with a vision of where they want to be, to see challenges and change as a time of opportunity, of positive thinking.
Because business opportunities haven’t died from the coronavirus. They are still out there.
Some have diminished, some have been put on hold – and huge new sectors are quietly opening up in the background (hydrogen and solar power, for example, as well as communications, sustainable resource development, energy-efficient building, improved logistics to manage and protect supply chains, industry 4.0 automation to respond nimbly to changing demand.
Already as a specialist company operating in the B2B space, we are seeing expanding optimism and planning among existing and new clients who want not only to respond to change, but to be seen to respond by the markets they want to reach.
The imperative for forward-thinking B2B companies is to communicate that they are taking the lead, and responding to changing needs – as well as having the ability to adapt swiftly if further changes arise – to better serve their client base.
So yes, we might be headed for a cliff. But it may not be as tall as we thought. And adaptable businesses will land on their feet and thrive through flexibility and innovation.
scanCONTROL Laser Profile Scanner
Automated measurement and inspection system for welded seam

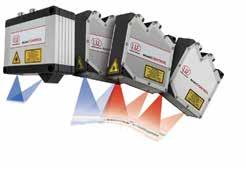
Compact design and integrated evaluation without PC High profile resolution for fine details High profile frequency up 10kHz Dynamic adaptation to changing surfaces Intelligent tracking to guide robots Programmable SDK via C, C++ and LabVIEW integration
Email: enquiry@bestech.com.au GLOBAL TECHNOLOGY LOCAL SUPPORT
Visit: www.bestech.com.au for more information
Phone: (03) 9540 5100
COLIN WELLS - MANAGING DIRECTOR, ROBOTIC AUTOMATION PTY LTD

TECH SUPPORT, NICE TO HAVE OR NOW ESSENTIAL?
Have you had a look under your car’s bonnet lately? Innovation and technology have evolved at such a rapid pace that even contemplating to repair or service your own vehicle is beyond the understanding and capabilities of most people. Today’s complex operating systems, mechanical components, and electrical controls require certain skills, tools, and specialised knowledge that can only come from factory trained technicians who possess the tools and software required to carry out critical servicing. The good old days of self-servicing and maintaining one’s own equipment is long gone, and hiring a professional service has long been accepted as the new norm where cars are concerned.
The same applies nowadays to modern technology solutions employed in manufacturing. However, unlike a car, of which “many thousands are made”, a modern palletising system (for example) uses multiple elements all coupled together such as robots, AGVs, packaging equipment, vision systems, laser scanners, barcode readers, labelers, PLC control systems, and the list goes on. All are important elements that make up a modern system for a client that, when integrated together, create a complex, be-spoke solution requiring a commensurate level of tech support.
A great example is Apple, who are hugely successful not only because they have a great product, but importantly they have in place an equally amazing tech support package second to none, which without they would not have had such great success. The two now go hand in hand.
This year, Covid-19 has unfortunately presented all sorts of issues for the manufacturing sector to combat. However, one unexpected positive outcome for RA is that, due to the restrictions regarding entry into Australia, our tech support team have been heavily involved with the installation of specialised robotic systems delivered by overseas integrators. The outcome has been beneficial for the client as now they also have a local tech support resource which they were probably unaware of.
It is interesting today to observe company procurement practices that still appear to not properly take into consideration the level of ongoing tech support that is going to be required for the full lifecycle of the system. Some ageing systems have had their operational life extended significantly way past their use-by-date by utilising a combination of having the right spares in stock and moreover, the appropriate tech support available. These systems generally had much simpler technology with less components and software controls involved. This approach may have been adopted previously by industry, however in today’s fast paced and constantly changing global manufacturing environment, it is exposed for what it is: a high-risk strategy. technologies across the board, gone are the days when companies were able to provide their own in-house tech support for the reasons mentioned above. This trend is deepening but appears in some client’s horizon to ‘be a matter worth not much consideration’. Thus, this subject has in many cases been given a less than appropriate level of priority when choosing a supplier and the total package being offered, especially the topic of local tech support capability.
Regarding spare parts this is also generally an increasing issue in this market and a subject worthy of further investigation. Below are a few such examples.
1) In any given modern and complex automation system there are many components used in multiple quantities which in some cases are easy to replace with a new version or an equivalent; this has always been the case in the past.
However, with market pressure on component makers to constantly upgrade and promote their components as ‘new’, the rate of change has vastly increased in recent years. Hence the individual compatible product availability has reduced drastically in some instances to a couple of years compared to several years in the past. If this is translated into the lifecycle of a whole system being 15 or more years long it is possible that the parts you are looking to replace are four to five generations out of date!
2) Many suppliers have also embarked on securing future demand for their products by ensuring their parts are hard to replace with a different brand. With the software, wiring, and plugs all being unique, it makes it hard to simply swap out a part for another brand.
There is a simple solution to combat this issue:
END OF LIFE AND DEVELOPMENT AND IMPLEMENTATION OF REPLACEMENT SYSTEM INSTALLATION, COMMISSION AND TRAINING
CONTINUOUS IMPROVEMENTSOPTIMISATION • Increase throughput and continuous improvementMAINTENANCE PROGRAMS • Regular PMS • System & Safety Audits • Software and Hardware Upgrades • Inspect • Analyse • Control
Automation system lifespan

Local experienced tech support is essential
companies need to allocate some funds for spares. The client, with the help of the supplier, has the option to acquire what is deemed to be the minimum spares package rated on a risk basis when the system is initially purchased.
These critical decisions give a business the peace of mind and confidence that by conducting early due diligence it has taken significant steps to remediate any future issues which arise. This small investment up front could save a huge amount of down time, expense, and stress.
Do I hear a call for the integrator to carry these spares? This is difficult for all the reasons above.
The component employed or required could well be one of only a few in the country and possibly the only units ever sold by that system integrator.
“How about leaning on the integrator’s supplier located in Europe?”, I hear you say. That is possible, but given the issues listed in the two examples above, they are almost in the same situation. You also must consider the supply chain and time frame for door-to-door delivery, especially during Covid-19.
Industry, along with society, points to the direction of future and change in most walks of life. One thing is for sure: we are not returning to the old ways. And frankly, I don’t want to, as I much prefer the car I drive today over the one 20 years ago.
Robotic Automation 1300 552 333 www.ragroup.com.au
SUPPORT YOU CAN TRUST
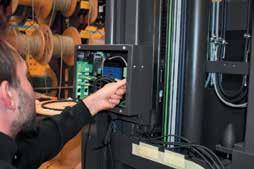
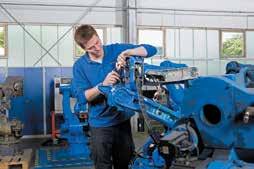
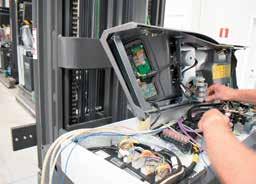
RA are committed to providing a fully comprehensive, value added support program to keep your operations running smoothly. Our annual service agreements are designed to maximise the performance of your automation systems and provide the highest return on investment over every stage of its lifecycle.

WHAT WE OFFER
24hrService
Technical Support – 24/7 access to a nationwide team of highly skilled technicians. Spare Parts - Robotic Automation only source and stock genuine factory spare parts. Keep your systems running with our customised Spare Parts package. Training - Empower your employees with the knowledge they need with training available on-site or at one of our training facilities. Optimisation & Upgrading - Extend the life cycle of your robots for increased productivity through our Robot Rebuild and Planned Upgrade programs. Life Cycle Management - Optimise ROI and system performance through our Preventative Maintenance Program. Consultancy Services – Utilise our specialised engineering and technical consulting team to receive expert advice across a broad spectrum of industrial automation applications.