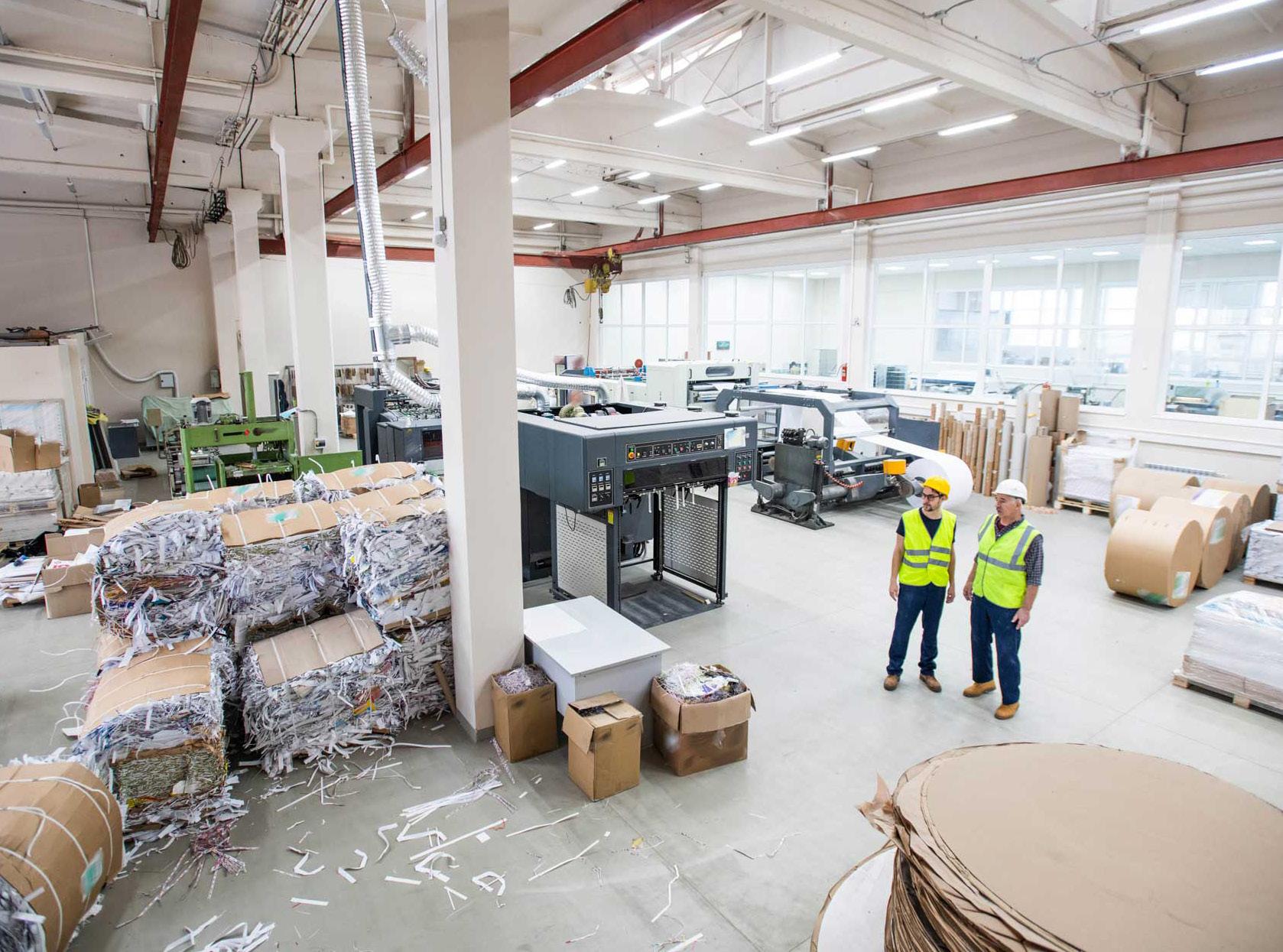
9 minute read
Recycling Manufacturing
Recycling transformation drives jobs in Victoria
The thirteen funded projects will enable Victoria to reuse over 137,000 tonnes of plastics, glass and tyres every year.
Advertisement
The transformation of Australia’s recycling sector has stepped up another gear with the Australian and Victorian Governments jointly announcing 13 new projects that will see 137,000 tonnes of plastics, paper, glass and tyres remade into new products while creating new jobs and new investment in the Victorian economy.
Federal Minister for the Environment Sussan Ley and Victorian Minister for Energy, Environment and Climate Change Lily D’Ambrosio announced $36.5 million in joint funding for projects under the Australian Government’s Recycling Modernisation Fund (RMF) and the Victorian Government’s Recycling Victoria Infrastructure Fund.
Minister Ley said the Morrison Government’s $190 million contribution to the RMF was facilitating unprecedented investment in recycling infrastructure, with the combined Commonwealth, state, territory and industry co-investment model on track to reach around $800 million.
“This latest round of projects includes a joint PET recycling venture that will process the raw plastic equivalent of one billion drink bottles each year to produce over 22,000 tonnes of recycled PET bottles and food packaging,” Ley said.
“It also includes remanufacturing projects, new products that will re-make waste into garden pots, railway sleepers and corrugated pipe.
“The co-investment model is exceeding all expectations and showing that materials can be recycled
and remanufactured to create new products and new jobs while helping our environment.”
The Victorian Minister for Energy, Environment and Climate Change, Lily D’Ambrosio said the new processing and remanufacturing technology would help create jobs, divert more recyclable material from landfill and tackle climate change.
“The thirteen funded projects will enable Victoria to reuse over 137,000 tonnes of plastics, glass and tyres every year and have generated over $86 million in industry investment, giving a total value of $122 million,” Minister D’Ambrosio said.
“These projects will reduce waste to landfill and boost the local economy through the creation of 204 local jobs, in addition to other jobs generated indirectly through the
construction and operation of these new facilities.”
The federal Assistant Minister for Waste Reduction and Environmental Management, Trevor Evans, said that the announced projects include two funded under the RMF’s regional and remote funding round.
“t” Assistant Minister Evans said.
“These communities often have to send their waste long distances for recycling, making it harder to create opportunities for local recycling and remanufacturing.
“This means our RMF investments in new recycling infrastructure can make transformational differences to these communities – delivering local circular economies and creating and keeping jobs in the region.”
The Government is driving a $1 billion transformation of our waste and recycling industry to turbocharge domestic recycling so we can process in Australia materials that were previously sent overseas.
The $190 million Recycling Modernisation Fund investment, and measures to support Australia’s National Waste Policy Action Plan, will create approximately 10,000 new jobs all around Australia over the next 10 years.
The Recycling Victoria Infrastructure Fund is part of the Victorian Government’s $515 million investment to deliver the biggest ever transformation of the state’s waste and recycling industry. This includes $380 million to deliver Recycling Victoria: a new economy, the state’s 10-year plan to reduce waste, create jobs in new industries and drive more value from our resources.
$45 million recycling plant opens in Albury

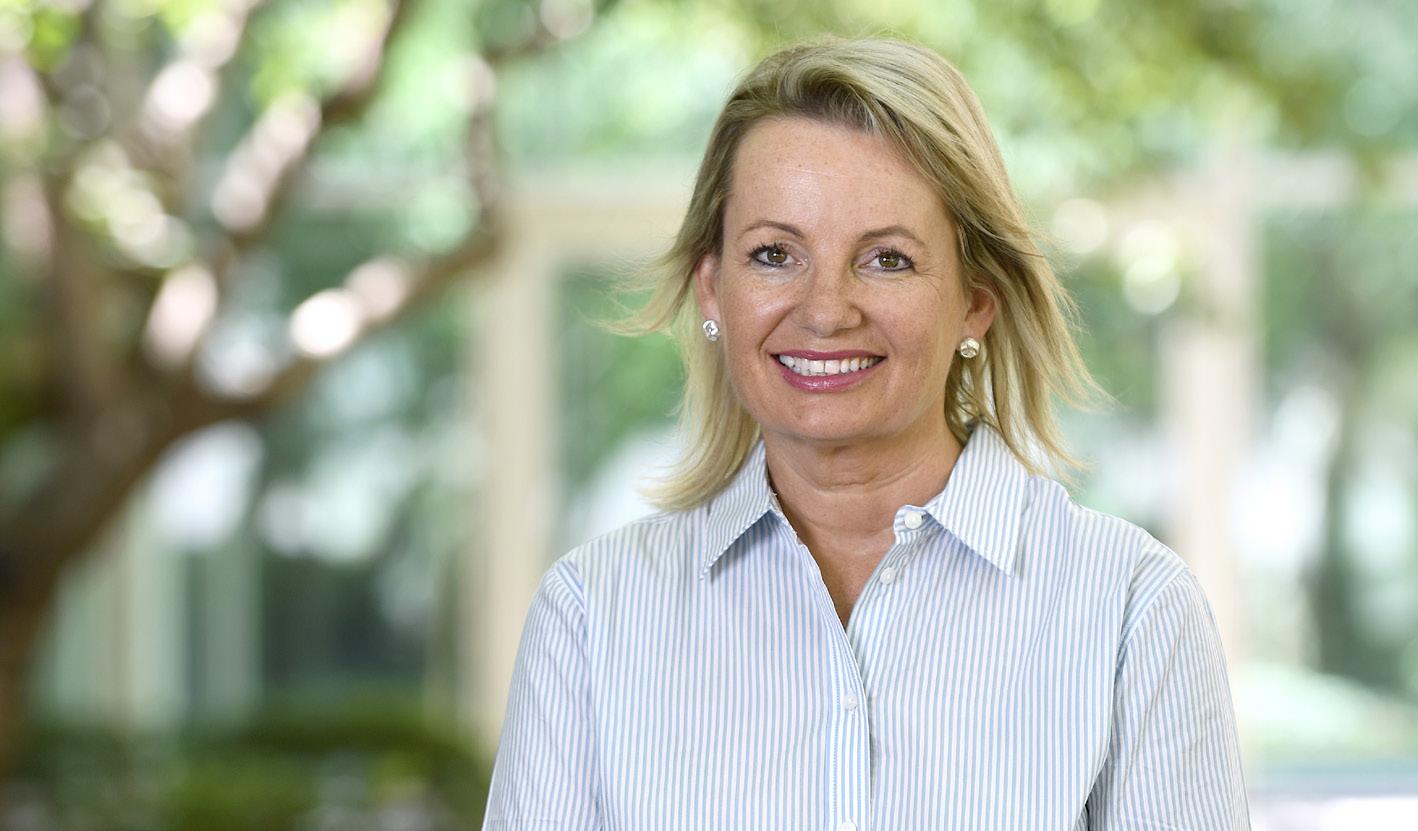
Minister for the Environment Sussan Ley said that this initiative demonstrates commitment to our national packaging targets when the supply chain and government work together.
Australia is taking a giant step into the circular economy in Albury with the opening of the nation’s largest PET (polyethylene terephthalate) recycling plant, capable of processing one billion plastic bottles each year.
Minister for the Environment Sussan Ley said the plant represented a massive step forward in ensuring end to end recycling by using materials sourced and remanufactured in Australia.
“The Circular Plastics Australia joint venture between Pact Group Holdings Ltd, Cleanaway Waste Management Ltd, Asahi Beverages and Coca-Cola Europacific Partners was born out of our first ever national plastics summit, and it is wonderful to see it come to fruition in Albury today,” Ley said.
“Up to 28,000 tonnes of PET plastic bottles will now be recycled and remade into new bottles and beverage packaging. “This demonstrates commitment to our national packaging targets when the supply chain and government work together. “Often the domestic manufacture of drink bottles has involved importing recycled plastic that has been recycled and processed overseas. “This is a ‘bottle to bottle’ process that sees industry and government working together to help our environment and economy by fully remanufacturing on shore.”
Leading the way
NSW Deputy Premier Paul Toole said regional NSW was leading the way with this world-class facility. “Establishing the country’s largest end-to-end PET recycling plant in Albury proves we’re serious about delivering jobs and investment in the regions,” Toole explained. “On top of the huge environmental benefits from recycling an estimated 1 billion plastic bottles each year, it is supporting the local economy by providing more than 200 local jobs during construction and more than 40 local jobs during operation.” NSW Environment Minister James Griffin added that the state is building momentum with government, industry and the community working together to find better ways to deal with waste and conserve our resources while reducing landfill and litter. “The joint venture between Pact Group Holdings Ltd, Cleanaway Waste Management Ltd, Asahi Beverages and Coca Cola Euro Pacific Partners will provide ongoing benefits to the local economy,” Griffin said. “It is great to see NSW’s highly successful Return and Earn scheme providing the raw ingredients for this game-changing circular economy project, backed by a successful partnership between federal and state governments and private industry.” Federal Assistant Minister for Waste Reduction and Environmental Management Trevor Evans said that the Australian and NSW governments are proud to have invested about $5.3 million in this facility. “Through the NSW Government’s Remanufacture NSW grant program we were able to support the installation of specialised equipment to the production of high-quality recycled plastics suitable for use in food and beverage packaging by major Australian brand owners,” Evans said. Member for Albury Justin Clancy added, “This has been an exciting journey for the partners who together make up Circular Plastics Australia. Already well-established in Albury, by working together and utilising the statewide resources of the Return and Earn program, we are seeing an evolution towards a true, nation leading circular economy in action.
vertical shredders. Built tough for the most demanding of shredding applications.
HEAVY DUTY VALUE FOR MONEY CIRCULAR ECONOMY

• Aggressive size reduction and densification of preshredded materials • Clean, high bulk density output for easy sorting and transportation • C&D waste, scrap metal and other heavy duty applications • Available with up to 440kW of power • Industry-proven and built tough for Australian conditions
To find out more, call: 03 9706 8066, Email: sales@appliedmachinery.com.au, or visit: www.appliedmachinery.com.au
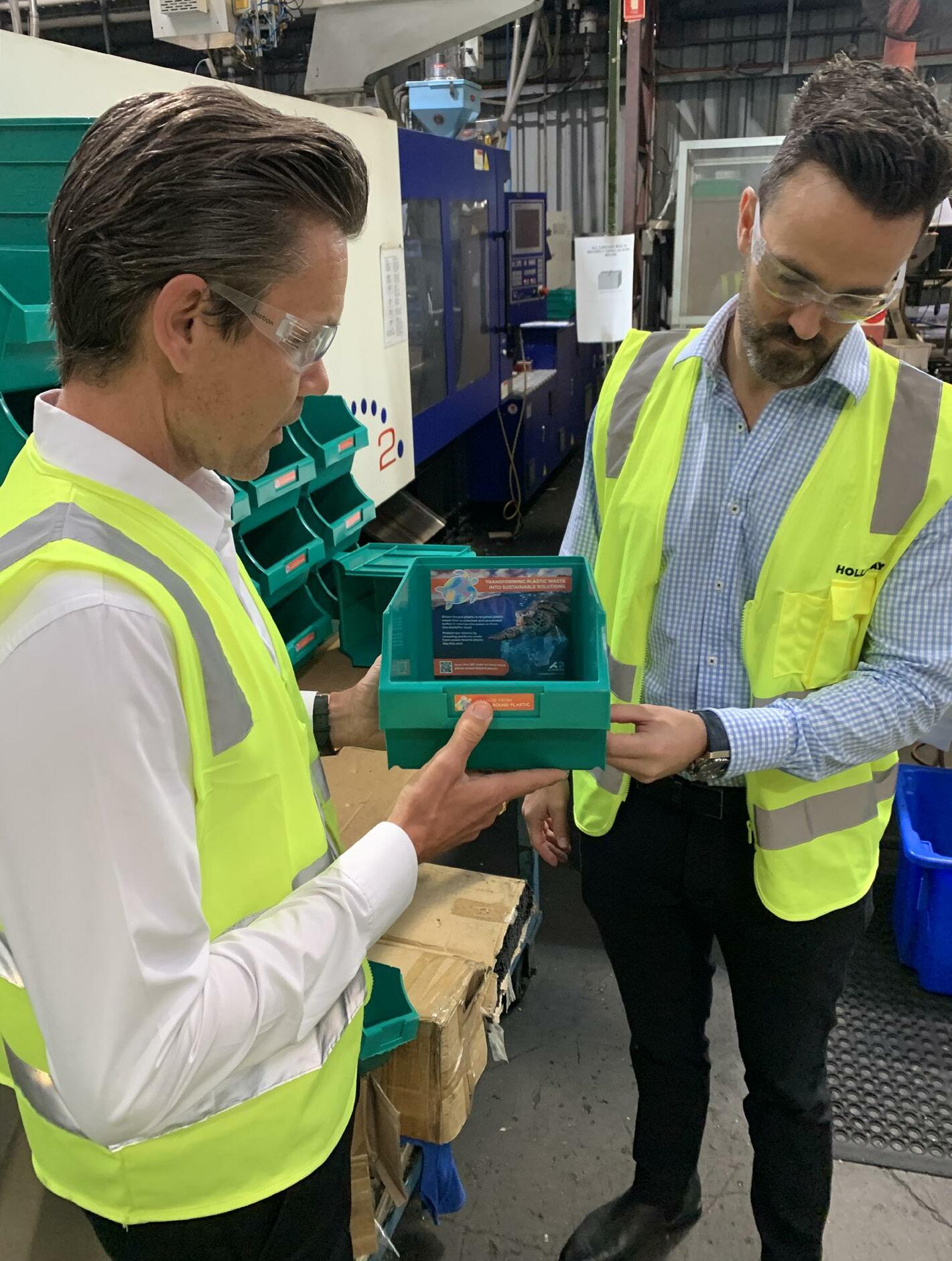
Holloway Group CEO Matt Holloway with general manager A Plus Plastics, Arto Taalikka.
Reshaping plastic – the product and its reputation
APlus Plastics is an Australian owned business that has been in operation for nearly 50 years, and one of its key goals is to help the plastics industry drive towards sustainable solutions and true closed-loop recycling. General manager Arto Taalikka said the plastics manufacturing sector has the power to reshape the way people think about this essential product.
“There is a vast amount of innovation in this space. We need to enable that, and we need to talk about it, because so much of the good work is happening from within the industry,” he said.
Demand for A Plus Plastics product is so strong that the operation’s manufacturing schedule is currently maxed out, but Arto says that will not stop the business from innovating.
“As a business, we are growing, with over 100 lines already and more to come, but we are not just focused on profits. We want to lead the way on keeping waste out of landfill and helping our customers continue to innovate. We see ourselves as an innovator and driver in this sector and we want to make plastics a good story.
End-to-end service
“We’re about more than injection moulding. We work with customers to help them refine their ideas and create products that solve problems – and all the while, we are focused on promoting local manufacturing and improving sustainability. We’re also the first business able to offer an end-to-end service from design to manufacture, to recycling over several key categories,” Taalikka explained.
Right now, everything A Plus Plastics makes is recyclable, and about 50 percent of the products manufactured are made from recycled materials.
According to Taalikka, within five years, that figure is likely to be 80 percent and by 10 years it will be virtually 100 percent,”.
One of the latest ventures for A Plus Plastics has been the introduction of Ocean Bound Plastics, an alternative to virgin plastic and regular recycled plastic. Ocean Bound Plastics (OBP) differ from other plastics recycling programs because they remove plastic waste from the environment before it ends up in waterways. The composition of the product is different from other recycled products, making it suitable for a wide range of uses.
“A major plus is that OBP can be certified food safe, unlike many recycled plastics, which means there is enormous scope to develop products for the food processing and service sectors,” Taalikka said.
“Also, while it’s possible to create coloured products from general recycled plastics, it’s tricky because of the nature of the plastics that end up in most recycling programs,” he says. “Ocean Bound Plastic, on the other hand, includes a lot of clear plastics so that makes it much easier to colour.”
Bunnings signs up for Ocean Bound Plastics
A Plus Plastics has just struck a deal that will bring a range of Ocean Bound Plastics products to nearly 300 Bunnings stores. Initially, Bunnings committed to offering four tech bin products at its warehouse stores, with more SKUs to follow.
Taalikka added thaT the ongoing demand for plastic products and the growing range of sustainable options create a strong story for industry.
“We’re excited to continue to work with customers, especially major supply chain players who can influence the whole market, to create not just products but programs that address business needs and develop the circular economy.”
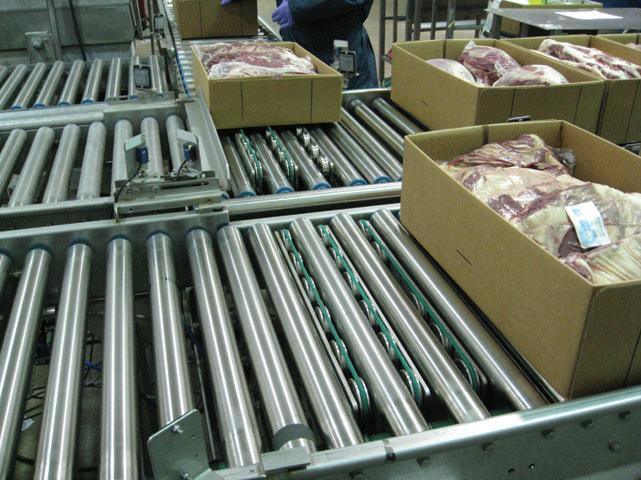

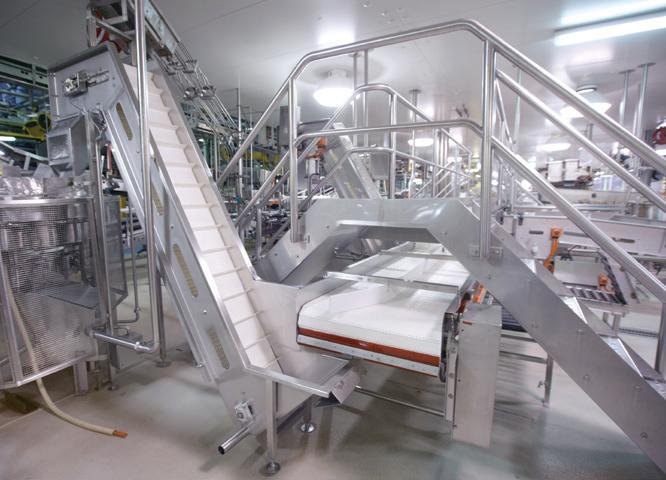

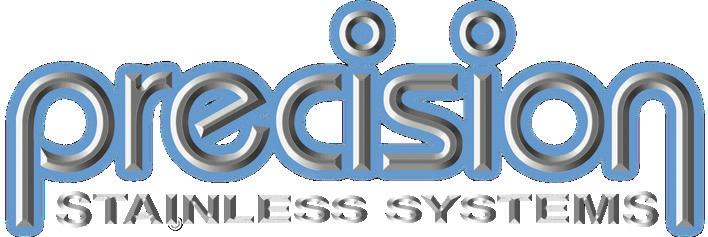