
31 minute read
Modern Manufacturing
R&D centres light the way to modernise manufacturing
To build Australian manufacturing sovereignty and ensure the country is a powerful force in global manufacturing, widespread innovation and modernisation are needed. This requires greater access to research and development.
Advertisement
The way for Australian manufacturing to reach this point is becoming clear as universities, manufacturing hubs and research centres are opening themselves to working with manufacturers to research, invest, test and commercialise new products and technologies.
A variety of R&D avenues is already available and these will be on show at the Modern Manufacturing Expo on 20 and 21 September 2022 at the
Sydney Showground. An ‘Innovation & Collaboration Zone’ in the exhibition will give visitors access to these resources in one convenient location. Attendees will have access to a dedicated space for manufacturers to meet, match and discuss their R&D needs with the likes of CSIRO, The University of Sydney, and New South Wales Smart Sensing Networking (NSSN). Also on offer is an ‘Expert Arena’, where visitors can hear from industry leaders including Advanced Manufacturing Growth Centre, DMTC, Open IIoT and AusIndustry among others.
A hub for manufacturers
The Sydney Manufacturing Hub is an initiative from The University of Sydney, and is a Foundation Partner of the Modern Manufacturing Expo. It is a core research facility dedicated to advanced materials processing and additive manufacturing, and focuses on the production of lighter, stronger and more flexible components in a manner that minimises waste.
“The hub gives manufacturers a place where they can try before they buy—to see what technology is available, get help from researchers on how to implement it and get the base work done before making a large investment,” says Gwénaëlle Proust, Academic Deputy Director of Sydney University’s Sydney Manufacturing Hub.
The hub provides capabilities for design, topological optimisation, the 3D printing of metals, ceramics and polymers, as well as post-processing heat treatment, advanced characterisation and more; paving the way for new technology in industries like aerospace, autonomous vehicles, biomedical, defence, maritime and robotics.
Local industries can benefit from enhanced additive manufacturing as it reduces material waste, simplifies supply chains, and builds independent capacity to create materials, components and even whole machines.
Opportunities for industry
Innovation can’t happen without collaboration, and different resources can help the modern manufacturer to develop different skill sets.
Christian Ruberg, Future Digital Manufacturing Lead at Australia’s national science agency CSIRO, says Australian manufacturers’ strength lies in collaboration and learning from one another. He suggests that manufacturers can promote industry collaboration in the following ways: • Participate in the ecosystem around supply chains by attending events where current programs and opportunities are explained such as the upcoming Modern
Manufacturing Expo • Participate in pre-competitive technical collaboration • Engage with industry growth centres and technology alliances • Participate as a trusted knowledge sharer and advisor
While this advice is useful, some manufacturers may still be asking themselves, ‘These new opportunities for manufacturing sound great but where can I find the best solution for my needs?’. According to Marie Kinsella, CEO for the IEC International Exhibition and Conference Group, this question will be answered at the Modern Manufacturing Expo.
“This new event was created after realising the need for innovation through collaboration and to assist with the government’s goal to modernise and digitise Australia’s manufacturing sector,” said Kinsella. “It is much more than an exhibition—rather a coming together of collaborators and a place where manufacturers can find not only new technologies but also help to implement modern manufacturing practices”.
The event will also host the first Smart Manufacturing Conference on 20 September at the Sydney Showgrounds. Tickets for this event are available on the website.
The expo will also see the launch of a dedicated Innovation & Collaboration Manufacturers Guide and the MICD Directory, which aims to help guide manufacturers along the digital transformation and innovation journey. Smart manufacturers will find this guide useful for inspiration through leading-edge stories. It also includes a practical directory of where to find the help they need to be competitive in tomorrow’s manufacturing world.
The full program for the Modern Manufacturing Expo can be found at modernmanufacturingexpo.com
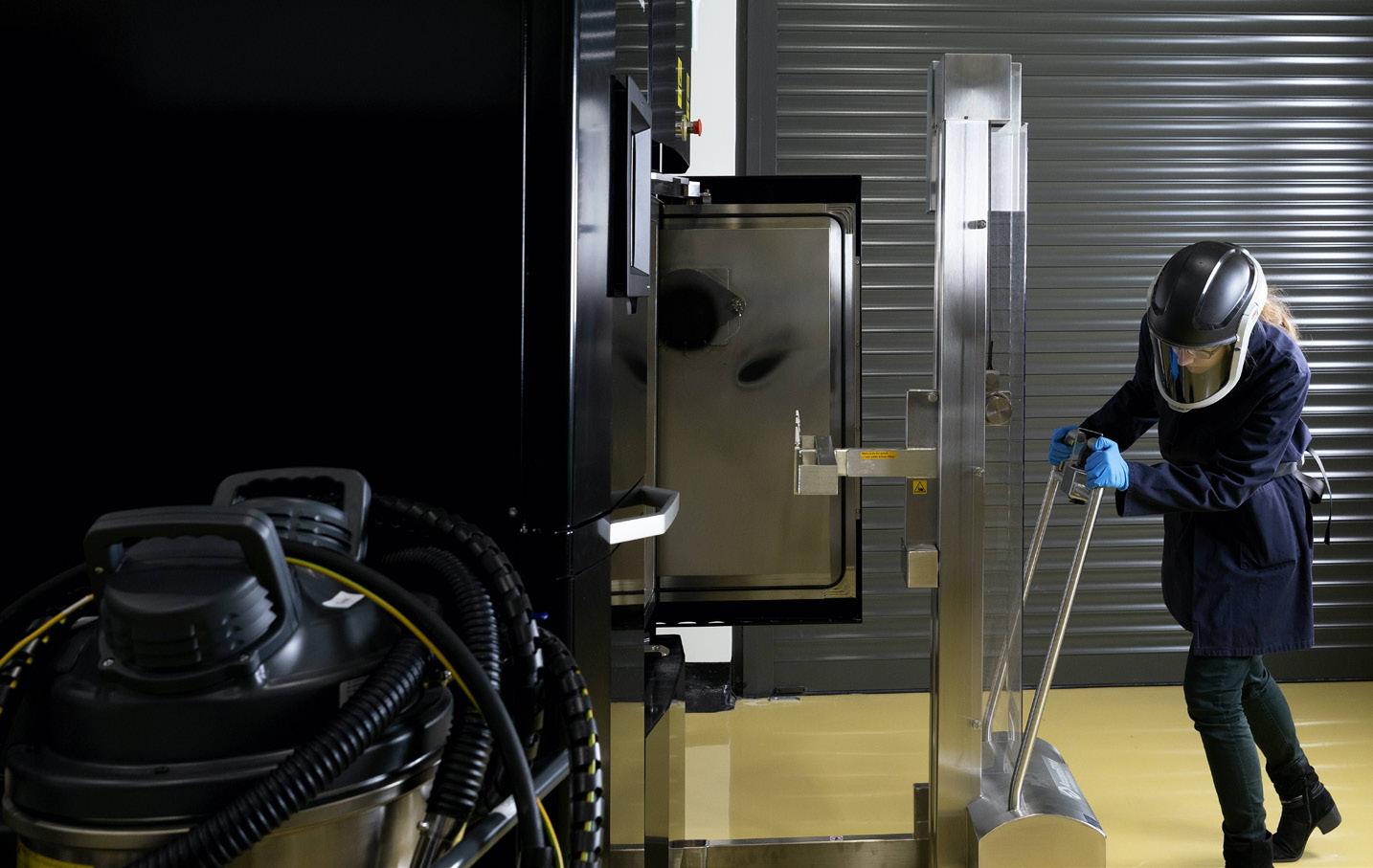
Join us at the Modern Manufacturing Expo at Sydney Showground on the 20th & 21st September. WIN - A 2 hour strategic review with Coleman Greig Lawyers, William Buck Accountants and Advisors and St. George Bank.
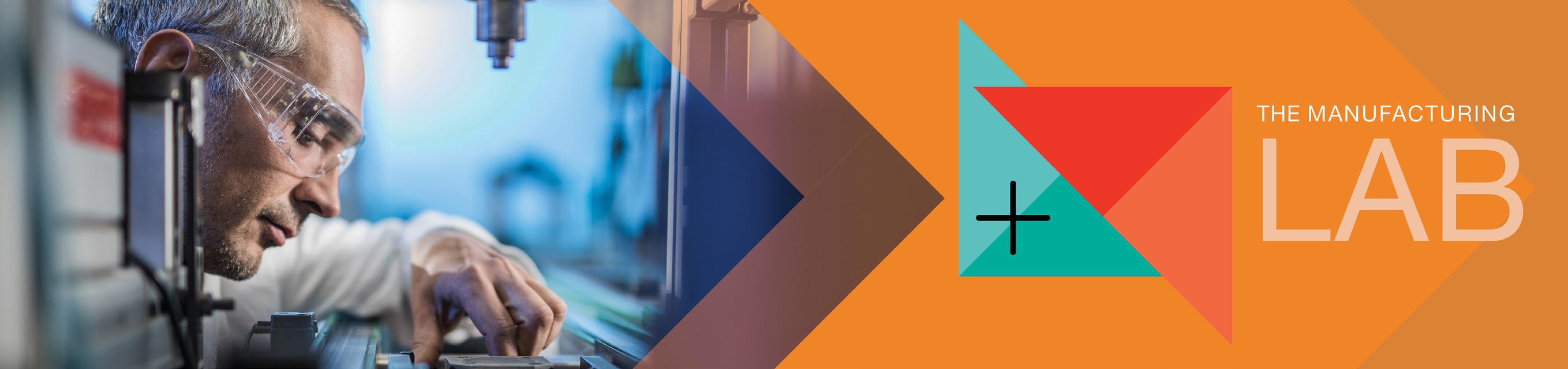
PRESENTED BY

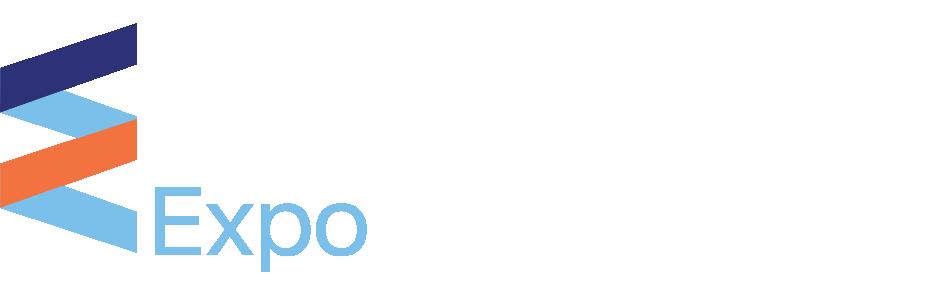
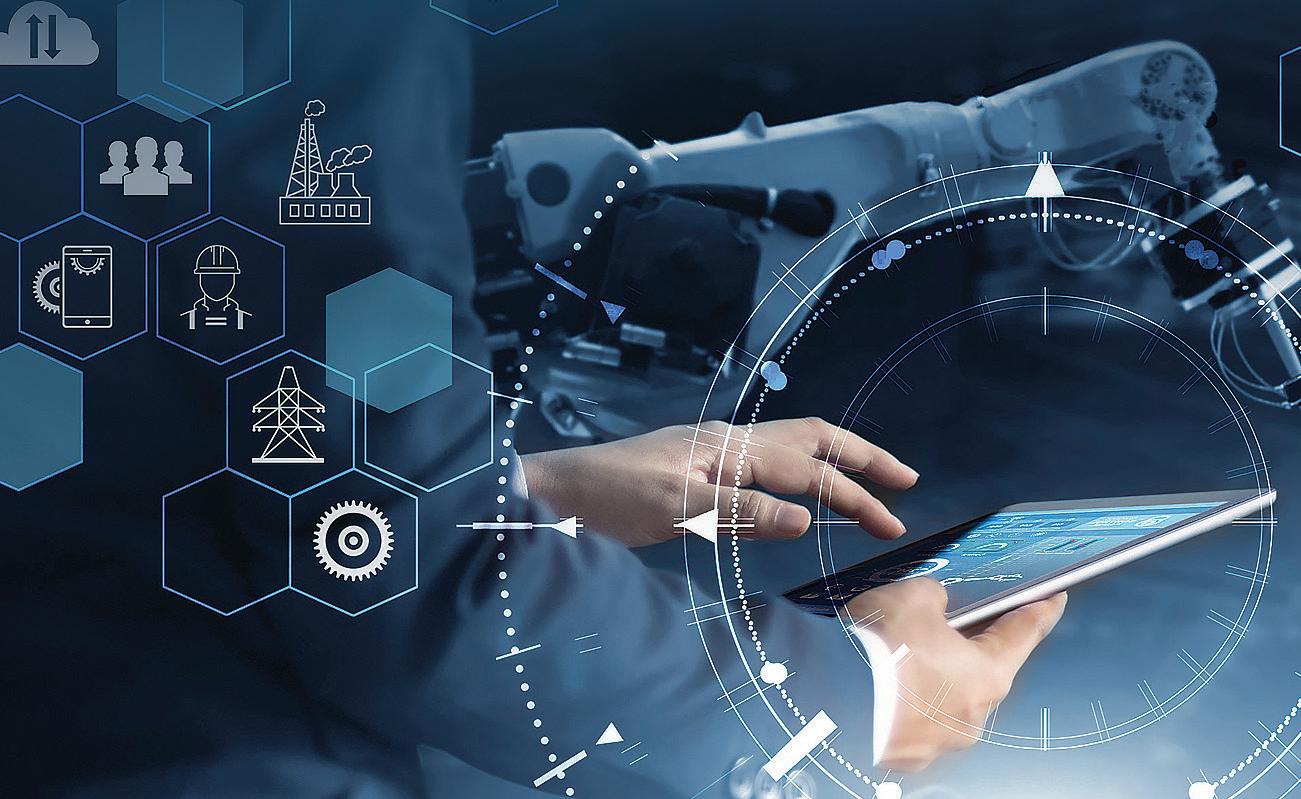
September’s Modern Manufacturing Expo puts focus on collaboration and implementation
Modern Manufacturing Expo, on at Sydney Showground in September, is being expanded with a one-day conference on smart manufacturing on 20 September. The Smart Manufacturing Conference will include thought-provoking presentations from experts on future-focused and practical topics such as smart-sourcing new technologies and equipment, the benefits of deep learning AI in the automated process and navigating the additive manufacturing landscape in highly regulated industries.
Modern Manufacturing Expo will be opened by Commonwealth Minister for Industry and Science, the Ed Husic who will give a government address at the Expert Arena on 20 September 2022.
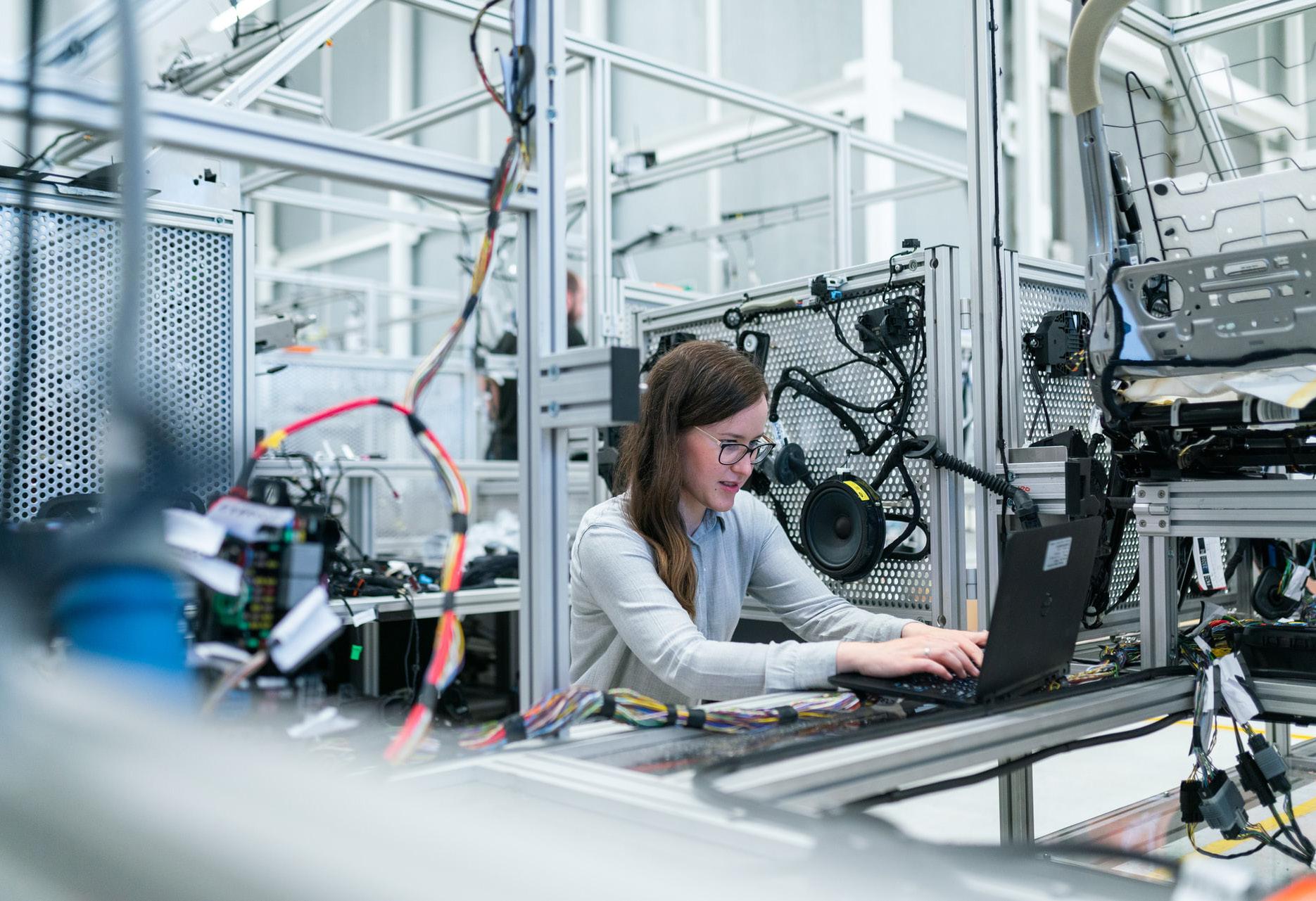
Other Events at the Modern Manufacturing Expo
Manufacturing Industry Leaders Breakfast
Kick-starting the Modern Manufacturing Expo, attendees of the networking breakfast will hear NSW Minister for Enterprise, Investment and Trade Stuart Ayres discuss the future of manufacturing in NSW.
Innovation & Collaboration Zone
The Expo will feature a special dedicated Innovation & Collaboration Zone where universities, manufacturing hubs and CRCs showcase exciting developments for the manufacturing sector. This is a great place for manufacturers to connect with innovation creators and learn how these organisations can support their advanced manufacturing goals.
Expert Arena
All registrations for the free Modern Manufacturing Expo will include complimentary access to the Expert Arena, which will be scheduled across the two days. Here, attendees can access live demonstrations of the latest in manufacturing technologies and hear expert presentations on topics such as 3D printing, a manufacturer’s guide to Cloud Software, AI, robotics, machine learning and digital manufacturing.
Modern Manufacturing Expo visitors can register for all events at the following link
R&D support for innovative businesses
Looking to access the R&D tax incentive but not sure where to start?
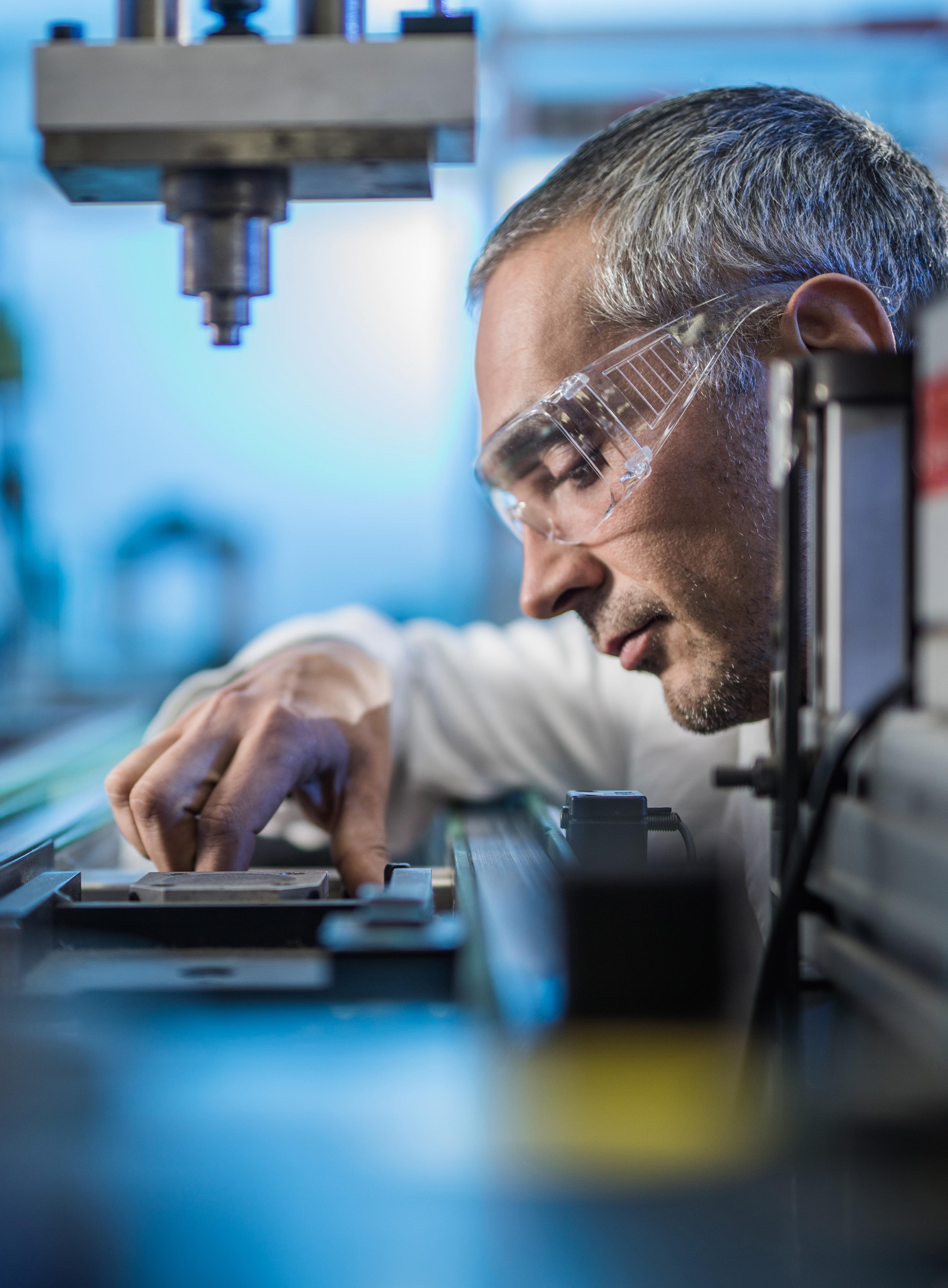
Our experienced team of advisors can help you assess eligibility, maximise your claim and remain compliant. Our advisors can help you: — Identify and document R&D activities — Conduct a feasibility review — Assess whether you’re eligible for the R&D incentive — Prepare and lodge your claim — Track expenditure against your budget — Ensure your ongoing compliance
Delivered by experienced accountants and tax advisors, our team takes a commerical and holistic view of your affairs. Get a free assessment from one of our R&D consultants today.

Your questions about cobots answered
Collaborative robot—known as cobots—are widely used for palletising applications. Dubbed ‘palletising robots’, these cobots help automate packing and stacking onto pallets.
Their ability to automate dull and potentially dangerous tasks is the main reason for their popularity around the globe, as Masayuki Mase, Country Manager for Universal Robots Oceania explains. “Cobots are not designed to take people’s jobs, they are designed to change the way work is done. They free up workers’ time so that they can focus on tasks that add value to the business.”
He believes cobots’ ease of use and efficiency in palletising is what truly sets them apart. “Universal Robots is focused on maximum productivity, the reduction of errors and improved quality. All our cobots are designed with these mandates in mind.”
In fact, Universal Robots’ latest addition to its portfolio, the UR20, features an entirely new joint design that allows for even faster cycle times and the ability to handle heavier loads. With a reach of 1750mm, it’s been designed to work to the full height of a standard pallet.
“Palletising is one of the final stages of production and takes place at companies big and small. The likes of fast-moving consumer goods and pharmaceutical industries commonly make use of palletising to pack, seal and transport goods to outlets,” says Masa.
Masa answers the most common questions from manufacturers to Universal Robots about using cobots for palletising as follows:
How can a palletising robot be customised?
“Palletising is a broad category,” explains Masa. “Businesses use palletising robots for a host of tasks, including handling extremely delicate items like glass, oddly shaped or tricky-to-grab items, products that can be damaged by a human touch or even hazardous materials. To meet a wide range of needs, there are various end effectors called ‘grippers’ that allow you to customise your cobot palletiser. You’ll find a gripper for virtually every sort of palletising task.”
What software and hardware do I need for a palletising system?
If you’re planning on using a cobot for palletising, you’ll need to start with a few hardware essentials – such as the cobot arm. “Generally, an arm with a higher payload will be better suited to some palletising tasks as it enhances movement capabilities.”
“For other tasks, you may require a longer reach rather than a higher payload, so make sure you choose the right cobot model. You’ll also need to choose an appropriate end effector (also known as end-of-arm tooling, or EOAT) based on the items you’re going to be moving.”
To ensure your cobot can automatically complete tasks, you will require the right software provided by Universal Robots.
Does a palletising robot have limitations?
“Yes, the technology does have some limitations,” says Masa. “However, the UR20 cobot from Universal Robots is a game-changer. While in the past we only offered a payload of up to 16kg, we now offer a 20kg payload which means that we can service almost any palletising application.” A robot palletising system can transform efficiency and productivity for smaller businesses. “With a limited number of employees on the line, SMEs are more vulnerable to staff being sick or unavailable,”says Masa.
“Engaged and satisfied employees are less likely to leave their workplace than those who are bored. Automating a tiresome task like palletising will free your people up for more purposeful work. By making employees’ roles more engaging, you can hold on to great talent.”
Add to the mix the worsening global skills shortage. A McKinsey survey has found that 87% of global companies are either currently or are imminently about to experience skills shortages and it’s clear that palletising robots are a good investment to future-proof a business.
Since introducing one of the world’s first commercially viable cobot in 2008, Universal Robots has developed a product portfolio including the UR3e, UR5e, UR10e, and UR16e, reflecting a range of reaches and payloads. Each model is supported by a wide selection of end-effectors, software, accessories and application kits. This allows the cobots to be used across a wide range of industries and means that they can be used for diverse tasks.
The company, which is part of Teradyne Inc., is headquartered in Odense, Denmark, has installed over 50,000 cobots worldwide. A utomating and digital transformation in manufacturing are not the easiest of tasks. It takes a strong strategic plan, the right advice, the right suppliers and most likely an evolution of company culture.
This is especially true in the Food & Beverage sector where the modernisation of traditional production lines can be expensive and difficult but reap great rewards.
At the Smart Food & Beverage Manufacturing Panel session, co-hosted by Investment NSW and Food Innovation Australia Ltd (FIAL), hear from Food & Beverage industry leaders and technology providers as they discuss successful adoption and lessons learnt in I4.0, automation, digitalisation and other modern manufacturing methods, models and processes.
Universal Robots universal-robots.com
Hear from Food & Beverage industry leaders at the Smart Manufacturing Conference
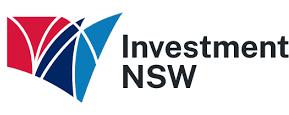
Smart Manufacturing Conference
Tuesday 20 September
Co-hosted by Investment NSW & Food Innovation Australia Limited - FIAL
Ray Hanly, Group CEO & Managing Director, Beak and Johnston
SMC Corporation ANZ
Metal 3D printing now coming to your desktop with Raise3D, BASF Forward AM and Bilby3D
3D Printing has come a long way. The use of thermoplastics has opened up low cost production, and the process has developed to reinforce high strength materials such as Nylon + Carbon Fibre.
Now MIM technology brings a new paradigm to small additive manufacturing machines.
MIM (Metal Injection Moulding) is an established technology for making solid metal parts in medium-to-large lots.
A metal powder combined with a binder is forced into a mould with pressure and heat. Then the part is ejected, and injection ports removed. From there the ‘green’ part is put in a debinding station, and most of the binder removed. The ‘brown’ part is then carefully moved to a sintering oven, the last of the binder burns out and the metal particles fuse together to produce a solid metal part.
The cutting edge development is to take that process and adapt it to incorporate the safer procedure of filament-based 3D Printing (instead of volatile powders) and print on a ruggedised industrial 3D printer. This produces simple or complex shapes without the limitations of moulding. In the fourth quarter of this year, Raise 3D will release its MetalFuse system of ruggedised 3D printer, debinding station and sintering furnace, optimised for BASF’s Ultrafuse 316L and 17-4PH. 316L Stainless Steel is well known, and the new 17-4PH provides an outstanding combination of high strength, good corrosion resistance and good mechanical properties as well as being magnetic. Through precipitation-hardening, a heat treatment technique, the material can be made even harder and stronger.
Bilby3D has been distributing the BASF Ultrafuse range for over 2 years, and will soon add a Raise MetalFuse System to its new Sydney headquarters. This will enable Bilby3D to offer the debinding and sintering stages as a service to allow businesses to access the technology with minimum upfront cost.
The launch of the Raise Metal Fuse system later this year will open up incredible manufacturing possibilities for Australian companies.
Bilby 3D is excited by the possibilities and is ready to discuss how this integrated solution can expand your manufacturing portfolio.
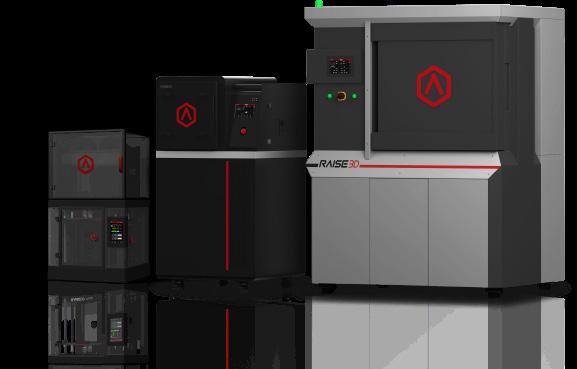

Bilby3D
bilby3D.com.au
Make Laser light work for you
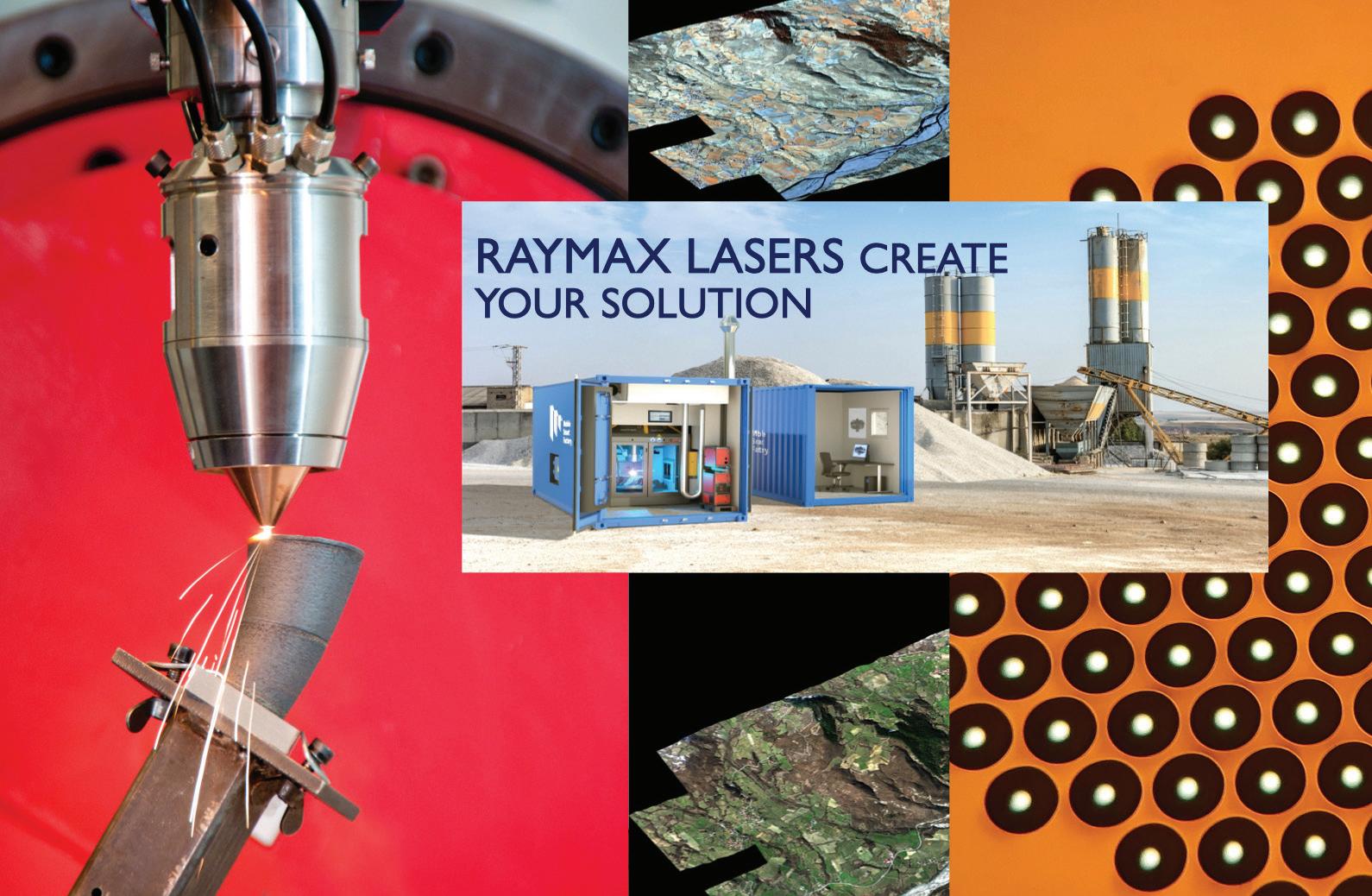
Discover what is possible with our advanced Laser and Photonics Solutions
• Advanced Manufacturing & Industrial Laser Processing • Micromachining & Microstructure Engineering Applications • Hyperspectral Imaging, Custom Optics, Lithography • Product Marking and Perforation Lasers • Laser safety products and Fume Extraction • Material Interaction Research • Solutions for Scientific Research • Laser Consulting & Engineering
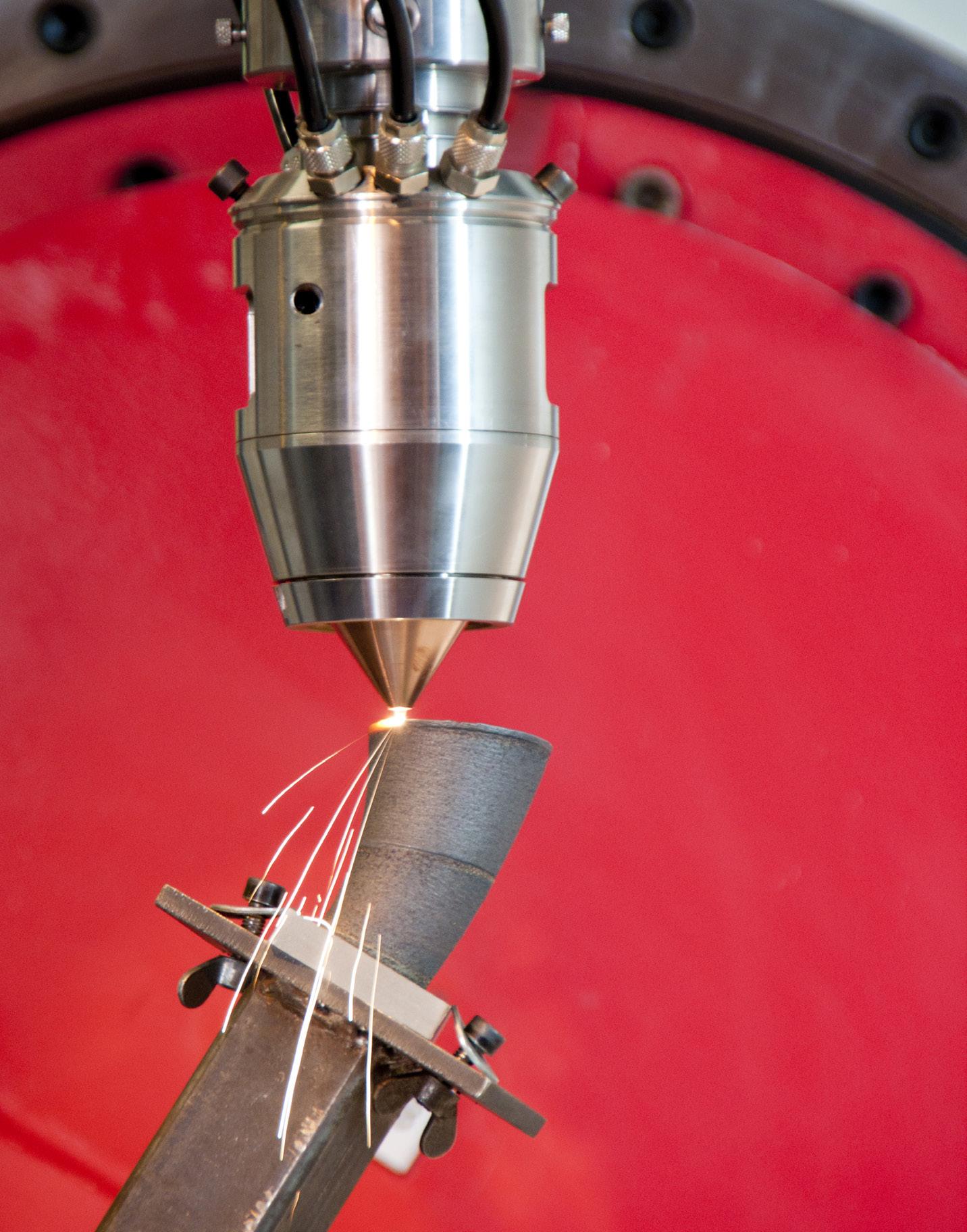
Innovation in Laser Technology
BeAM machines, which are now part of the AddUp group, design and produce industrial metal additive manufacturing machines that apply Directed Energy Deposition (DED) technology.
DED is an Additive Manufacturing process where focused thermal energy is used to fuse materials by melting them as they are deposited.
The real advantages of the DED process can be found in the wide variety of industrial applications.
These include, but are not limited to, extending the life of parts by providing wear resistant coatings, repairing damaged or broken parts, using multi-materials in one application and creating additional structures on pre-existing parts to provide different or improved functionality.
Building precise complex geometries is a feature of the DED process. An example of a repair can be found in a worn labyrinth seal from an aircraft with a finish that met qualification standards.
Here, advantages of DED processes are gained through accurate repeatability compared to a manual welding process and the result is high mechanical strength due to very fine microstructures with no cracks or bonding failures.
The process benefits from being conducted in a controlled environment that ensures high-quality in the final material, while the operation is conducted within exceptional safety standards.
BeAM joins AddUp
First developed in France, BeAM machines have now joined AddUp with operations commencing in Cincinnati USA.
This move strengthens the offerings to customers, as AddUp provide a complimentary technology of Laser Powder Bed Fusion (L-PBF).
BeAM machines include the Modulo 400 and Magic 800. Both machines use a custom-built nozzle mounted on the Z-Axis of a CNC machine, providing a simultaneous 5 axes process. The co-axial nozzle is moved in 3 linear axes while the build platform works in 2 rotational axes operating in a controlled atmosphere.
This set-up allows 5 continuous axes of freedom, to build or repair components layer by layer. By utilizing traditional CNC controls and using ISO G-code customers are provided tools to which their skilled workforce is already accustomed.
All BeAM machines offer automated quality assurance software displaying real-time data on a screen, which is compatible with 4.0 platforms. Some 80 different parameters can be monitored including gas flow, torque, powder consumption, porosity, and so on. Should a spike in the data output be observed, the print can be halted, and the problem fixed. This innovative use of sensors acts as a monitoring device in real time.
Machines designed to meet customer needs
These 5 axis machines have been designed and manufactured for industrial purposes to meet customer requirements.
Each BeAM machine is modular, upgradable and offers high performance. Modulo 400 for example, has a 640 x 400 x 400 mm build volume, (the Magic 800 has an 800 x 800 x 1200 mm build chamber), a process module with 5-axis kinematics, the DED deposition nozzle, ‘powder tight’ enclosure, an air extractor and a filtration unit that provides exceptional operational safety standards.
Additional peripherals can be added, but the whole system fits into a shipping container, enabling transportation and operation to remote locations.
BeAM provide a range of industrial nozzles for the deposition process that offer precise, variable deposition widths from 10Vx, single gas follow, or 24Vx, dual gas flow, that varies the deposition volume depending on your needs.
The laser beam is employed as a heat source to melt the metal powder that is deposited on a substrate layer by layer for the generation of a desired component. All deposition parameters are modifiable - powder mass flow, deposition speed, and laser power.
The nozzles are powered by a high-quality reliable fiber laser source of 500 W or 2 kW. The heat source melts the metal powder that is deposited on a substrate, layer by layer. This unique capability enables new sections to be added to parts using ‘near net shaped’ geometries.
These can comprise large dimensions, complex shapes, embrace multi-material builds and most often do not require supports to ‘hold’ the part during the DED build.
Innovative manufacturing
‘Near net shape’ refers to building a component to be close in size and shape to the desired finish, providing an innovative method of manufacturing with high-value materials.
While the advantage of this process means less post-processing and less material waste, a key advantage is that new sections or additional features can be added to an existing part.
A recent development in-house used a rocket nozzle made from 304 Stainless Steel and ‘over-printing’ an Isogrid in Inconel 625 using a Magic 800 DED machine.
Following this a top structure was built using a layering process. The completed product was finished within 18 print hours.
Technologies combine to innovate
The success of the relationship between AddUp and BeAM recently resulted in a concept part created across both platforms, Laser Beam Melting and Directed Energy Deposition.
A hybrid piston head was constructed to demonstrate the technology can produce high performance parts by introducing lattice structures to reduce weight, with internally positioned oil channels that would serve to increase performance.
First, the piston core was built using a FormUp 350 laser printer. The piston core was then placed in a BeAM DED machine where rings were created on the top section using a different material (Inconel 625).
The 5 axes build platform in the BeAM Magic 800 deposited the rings to increase wear resistance and better performance under high temperatures.
The final product demonstrated the effective combination of both technologies paving the way for innovation in manufacturing.
If you would like to discuss DED technology with BeAM machines or and AddUp LBM systems come and meet Dr Cédric Chaminade, Technical Director at Raymax Applications Pty Ltd on our stand at Modern Manufacturing.

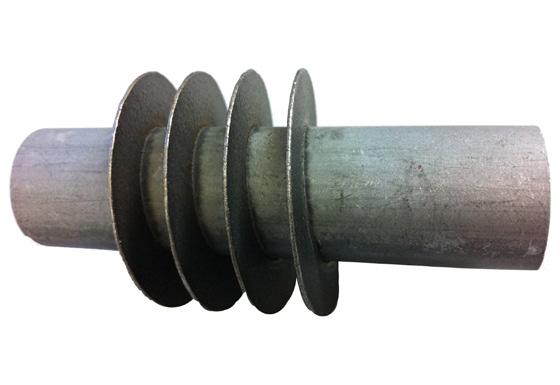
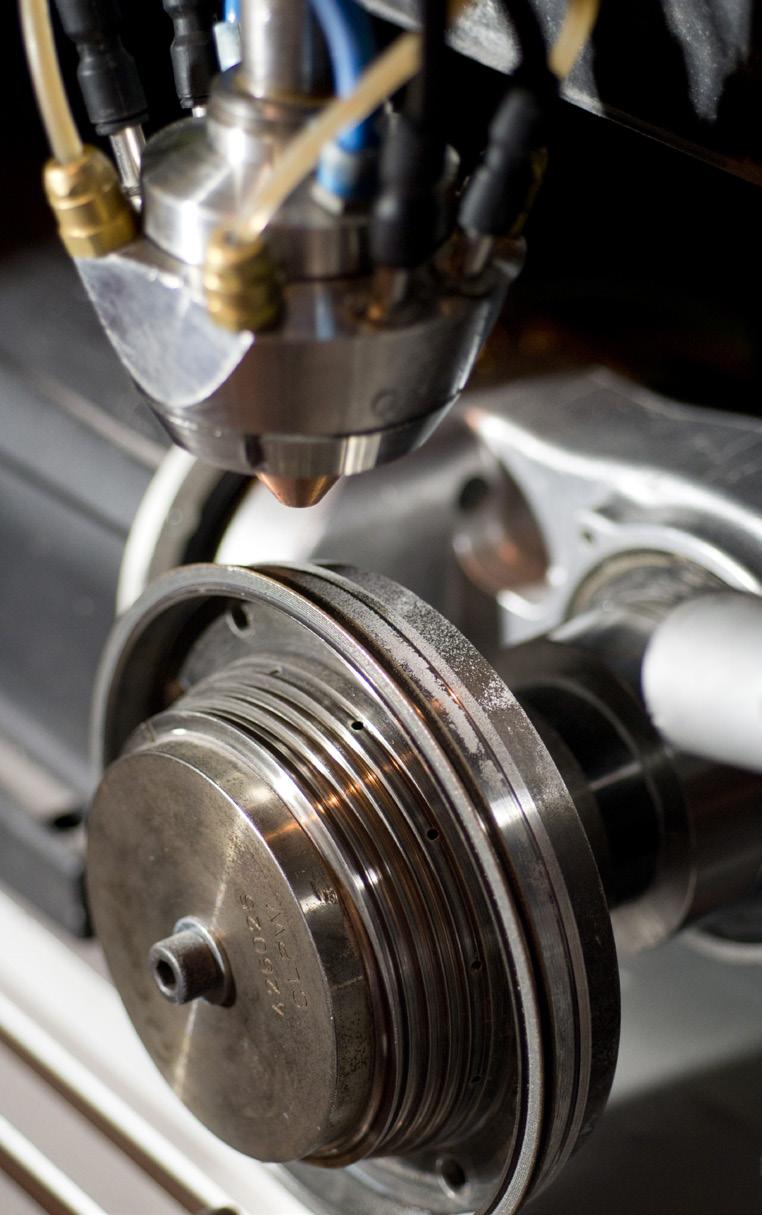
Raymax Lasers
Gain a competitive edge by implementing the latest digital tools for rapid prototyping and small batch production
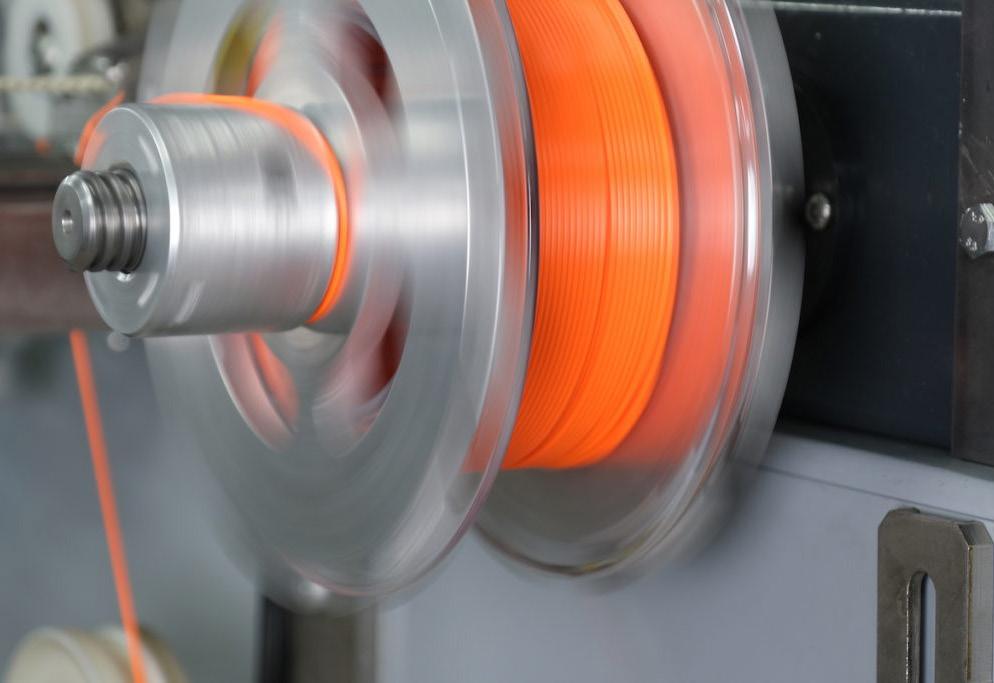
Bilby3D have offered industry-leading tech support to diverse businesses from solo professionals up to Defence and Aerospace for over a decade. We consult for companies to find the materials and machinery that will best meet their needs. We action real and cost effective manufacturing workflows.
Brands we represent: Raise 3D-Industrial 3D Printers, Photocentric Resin Manufacturing solutions, Thor3D and Shinging3D 3D Scanners, Mayku Thermoformers. Spectrum, 3DXtech, ProtoPasta, Kimya by Armor. BASF and Zetamix by Nanoe Industrial Filaments.
Raise3D is leading Fused Filament Fabrication (FFF) 3D Printing with high reliability and output quality. Raise3D’s printers are easy-to-use, durable, ready to improve precision standards, scale production, and add a powerful new additive manufacturing resource. Raise3D also has a well-earned reputation for premium materials, providing impressive tensile strength and surface quality. Stronger materials launching within their range are being made available with the new industrial machines.
Photocentric - inventors of 3D LCD Printing. A winner of 3 Queen’s Awards, patent holders in visible light curing technologies and specialising in photopolymerisation, Photocentric is an award-winning specialist resin and LCD printer manufacturer based in the UK and Arizona, USA. They manufacture an innovative range of photopolymer resins compatible with any printer operating from 355nm to 460nm, and a range of innovative 3D printers using LCD screens.
Materials - Having a great, reliable machine is only part of the process. Most of our machines are open materials - so you are not locked in to materials from one supplier, and can adapt to new materials as they come along.
We scour the world to bring you the best materials with real-world applications.
For FFF we have not just various Nylons embedded with Carbon Fibre, but many different matrix and reinforcing materials, including ABS with Kevlar.
BASF has been working with Raise3D to bring to market a solution for printing filament with metal powders within a binder, which can then be sintered to give a full-metal part with low porosity. Nanoe in France also has ceramic filaments.
We also have a range of flexible materials of different shore hardnesses, from very soft to high durability.
Due to the nature of thermoplastics, their temperature resistance is low. Combined with the printing process of FFF printing, that means sometimes we need a different solution. Resin printing is a chemical curing process, so that items with higher temperature resistance, such as small run injection moulds, can be produced. As can items with high levels of flexibility.
Bilby3D are proud of the solutions we have helped establish with Australia’s medical, military, and manufacturing industries; drawing on our engineering and material sciences knowledge to develop world first applications in Additive Manufacturing across Australia and New Zealand.
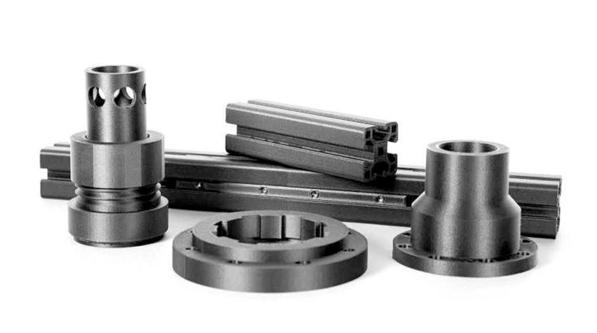
Raise3D Prints
Bilby3D
bilby3D.com.au
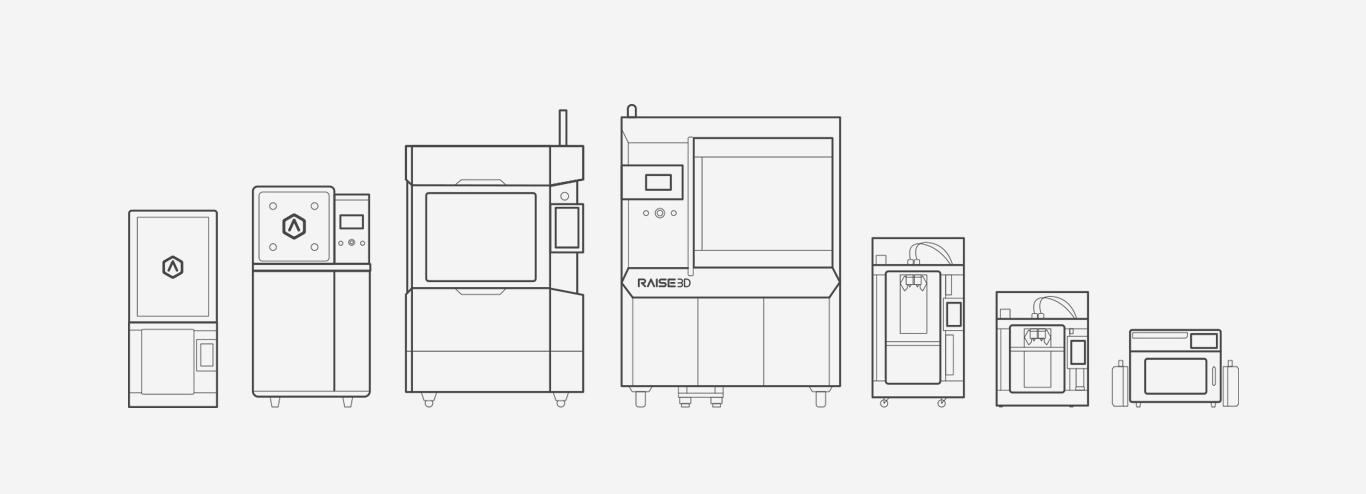
Maverick use of Lego helps Gold Coast flight simulator zero in on elite military markets
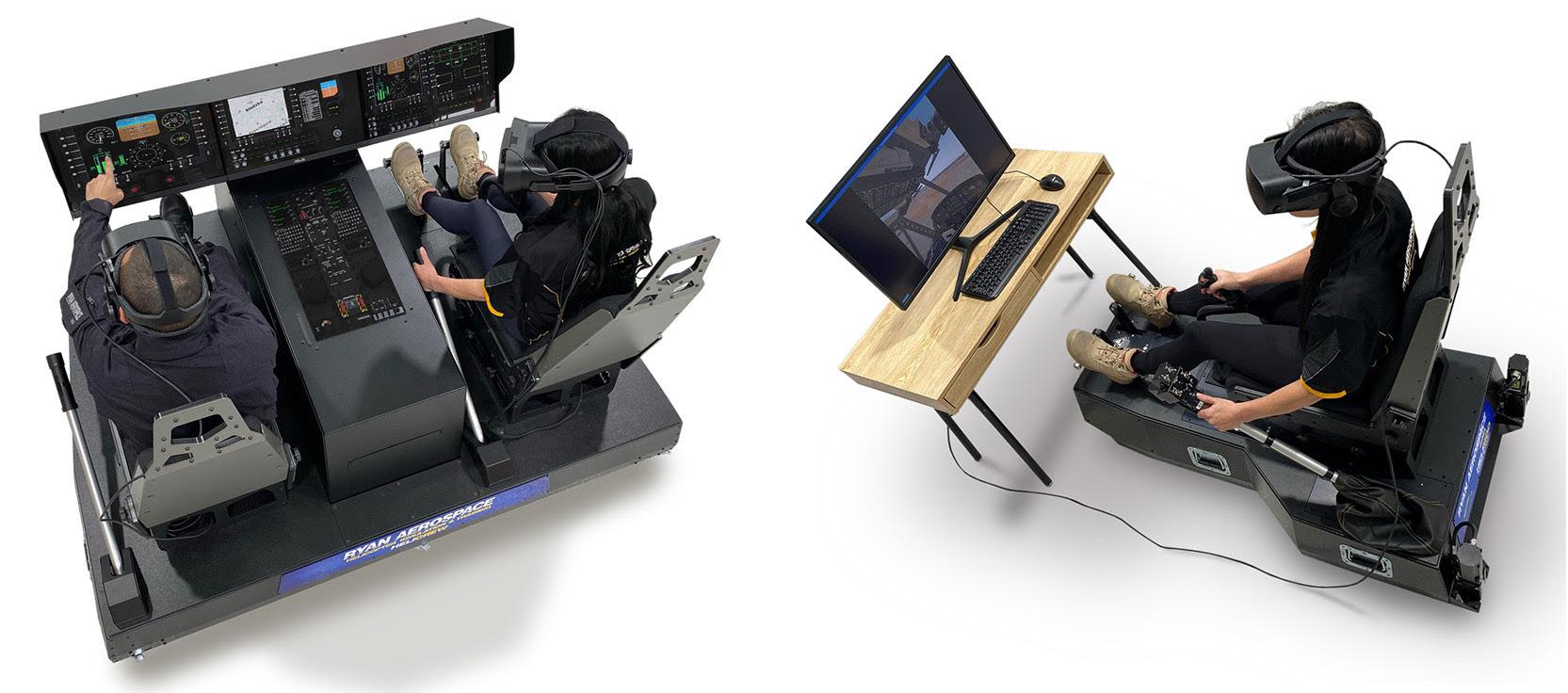
AGold Coast innovator, Ryan Aerospace, supplies helicopter and jet flight training simulators to the United States Air Force, Army and Navy, as well as England’s Royal Airforce, changing elite pilot training and revolutionising the world’s most famed fighter pilot and weapons schools.
Managing director Chris Ryan said clients across the United Kingdom, Europe, the Middle East, Asia, North America, South America and Australia were jumping aboard the realistic, robust, accurate and cost-effective helicopter flight simulators available for civil, military and emergency applications.
And it all started with a Gold Coast helicopter flying lesson, and Lego.
On a family holiday to the Gold Coast, Ryan took his first helicopter flying lesson. Returning home, he was determined to practise his skills, so invented a simulator.
He saw a need for helicopter simulators that were better than gaming equipment, but without the exorbitant costs of high-end simulators.
“The very first prototype was made with a gaming joystick that literally pulled apart, re-wired and integrated into an office chair with a lot of gaffer tape and dodgy welding,” Ryan said.
“When I wanted to design new concepts, I did use Lego which I commandeered from my parent’s place. However, as time went on, I taught myself how model using 3D Computer Aided Design (CAD) packages so now, I’m afraid, the Lego has taken a back seat and gone back to grandkids.”
Ryan Aerospace hit the afterburners when it exhibited its first virtual reality trainer at a trade show in Rome in 2012, followed by Ryan making the permanent move to the Gold Coast.
“The Gold Coast is a great location for a business like ours,” Ryan said.
“We are close to all our support services such as fabricators, laser cutters, powder coaters, electrical suppliers… It’s also close to universities which is a great place to get advice and source talent. Finally, it’s just a great place to live. The lifestyle is just fantastic.” As a pioneer in the new generation of flight training devices that leverage virtual and mixed reality technologies, the company has been on a high-speed climb ever since the move. “We could see very early on that this type of technology was going to be a game-changer and industry disrupter,” Ryan said. “One headset, worth less than $1,000, could replace many screens, projectors, projector domes and PCs, all while providing a really realistic and immersive experience.
“Something else you get with Virtual Reality that you can’t get with screens out front or projection domes is 3D stereoscopic depth perception, which provides yet another layer of immersion and realism.
“We are now working on mixed reality solutions where some of what you see in your headset is virtual reality and some of it is real. This is especially useful for allowing the trainee to interact with controls and instruments in the cockpit.”
Ryan Aerospace continues to supply a series of contracts awarded in 2021 for nearly 300 jet fighter and helicopter training simulators to the US Air Force.
The simulators form part of the innovative new program, known as “Pilot Training Transformation,” to combat the US Air Force’s shortage of pilots and flight instructors who could deliver one-on-one training to the students.
As part of a consortium, Ryan Aerospace won the job over multi-billion-dollar competitors by developing a modular and reconfigurable flight training simulator that could be modified to represent a number of different fixed wing and rotary wing aircraft.
Coupled with a learning management system, the simulators allowed the flight school to switch from a “teacher-centred” model to more of a “learner-centred” training model, or, where students, with the help of a virtual instructor, could virtually teach themselves.
Ryan said the military market had since taken off, also adding the extra bonus of trainee fighter pilot safety.
Among other contracts, Ryan Aerospace supplies more than 30 HELIMOD Mark III helicopter simulators for the US Army at Fort Rucker, Alabama, which is the world’s largest helicopter training facility.
The company also supplies virtual reality helicopter simulators for the Royal Australian Navy.
“Preparing students for flight in the simulator is proving very valuable and is seen as a way to reduce risk in the real aircraft due to the fact that students are already familiar with the cockpit, the procedures, the flight controls, the rules around the airfield,” Ryan said.
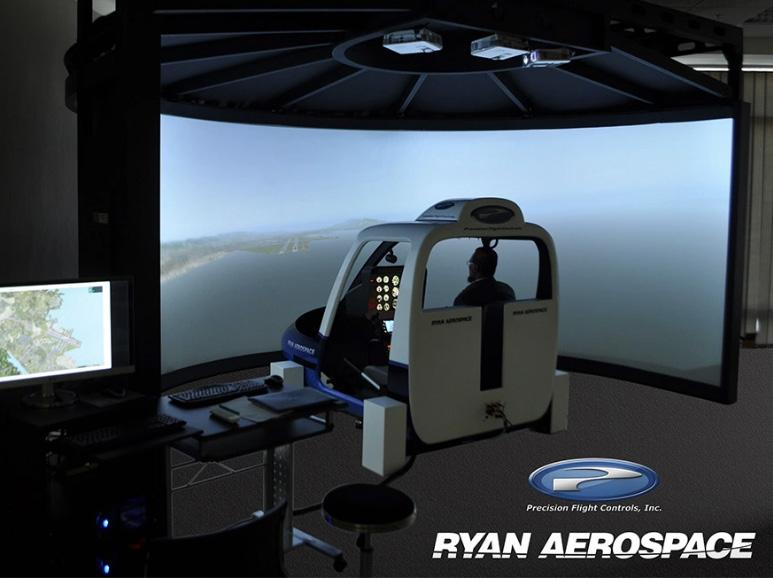
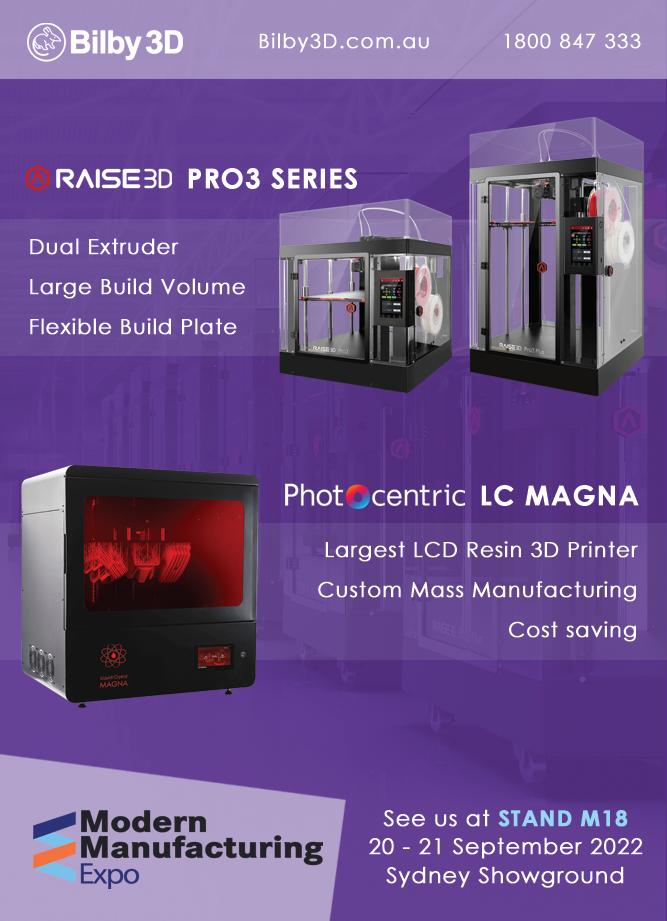
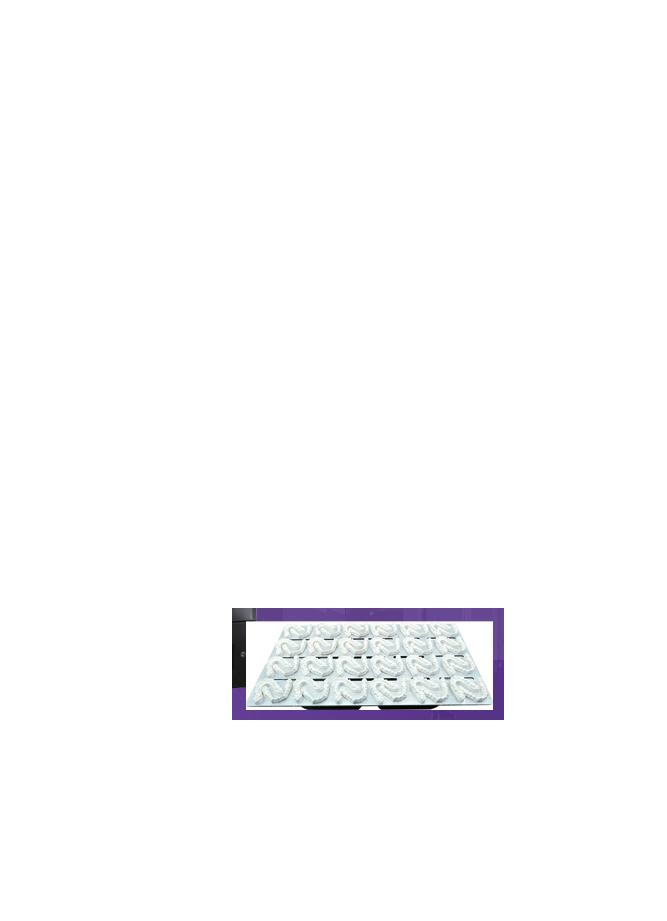
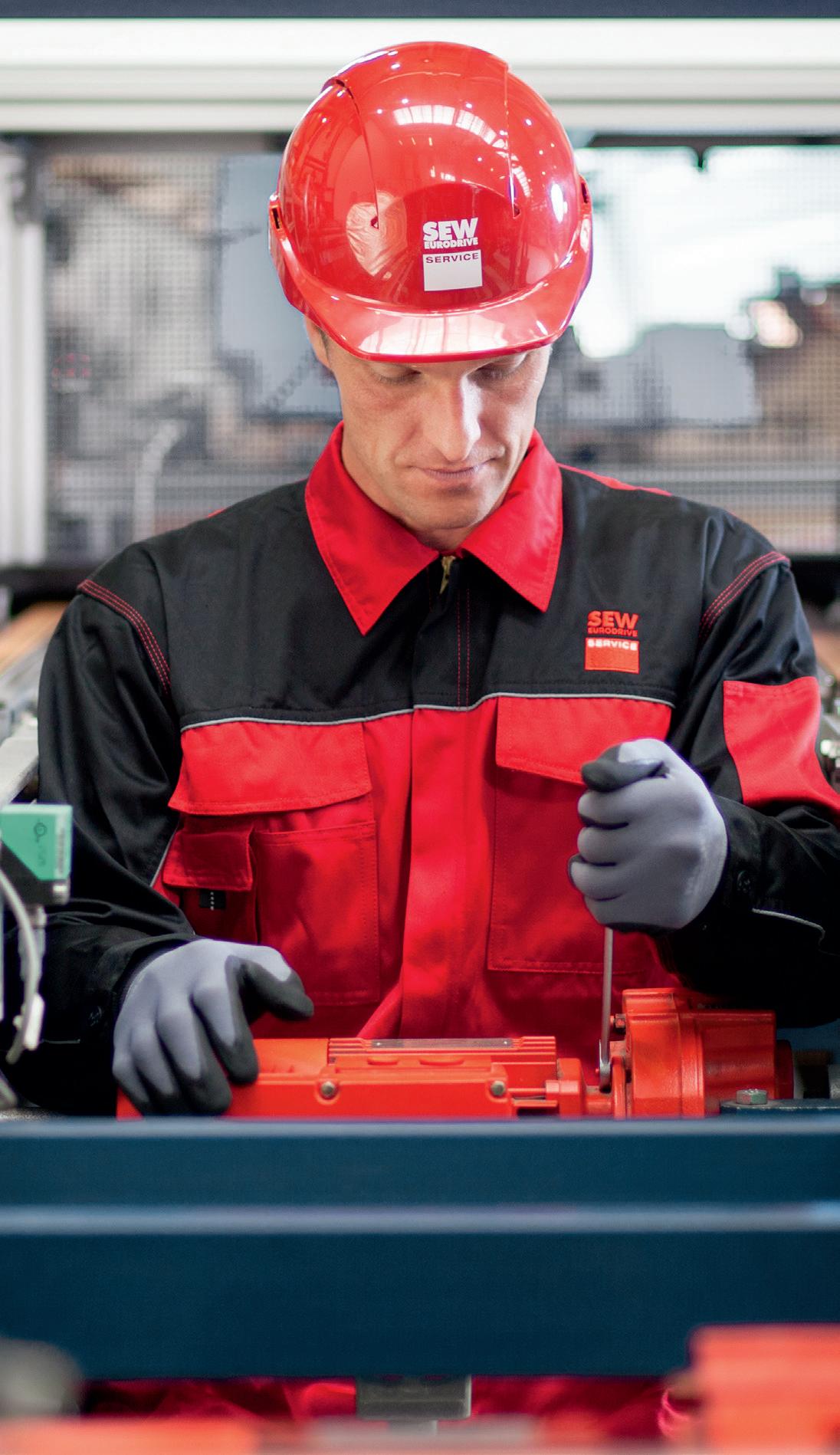
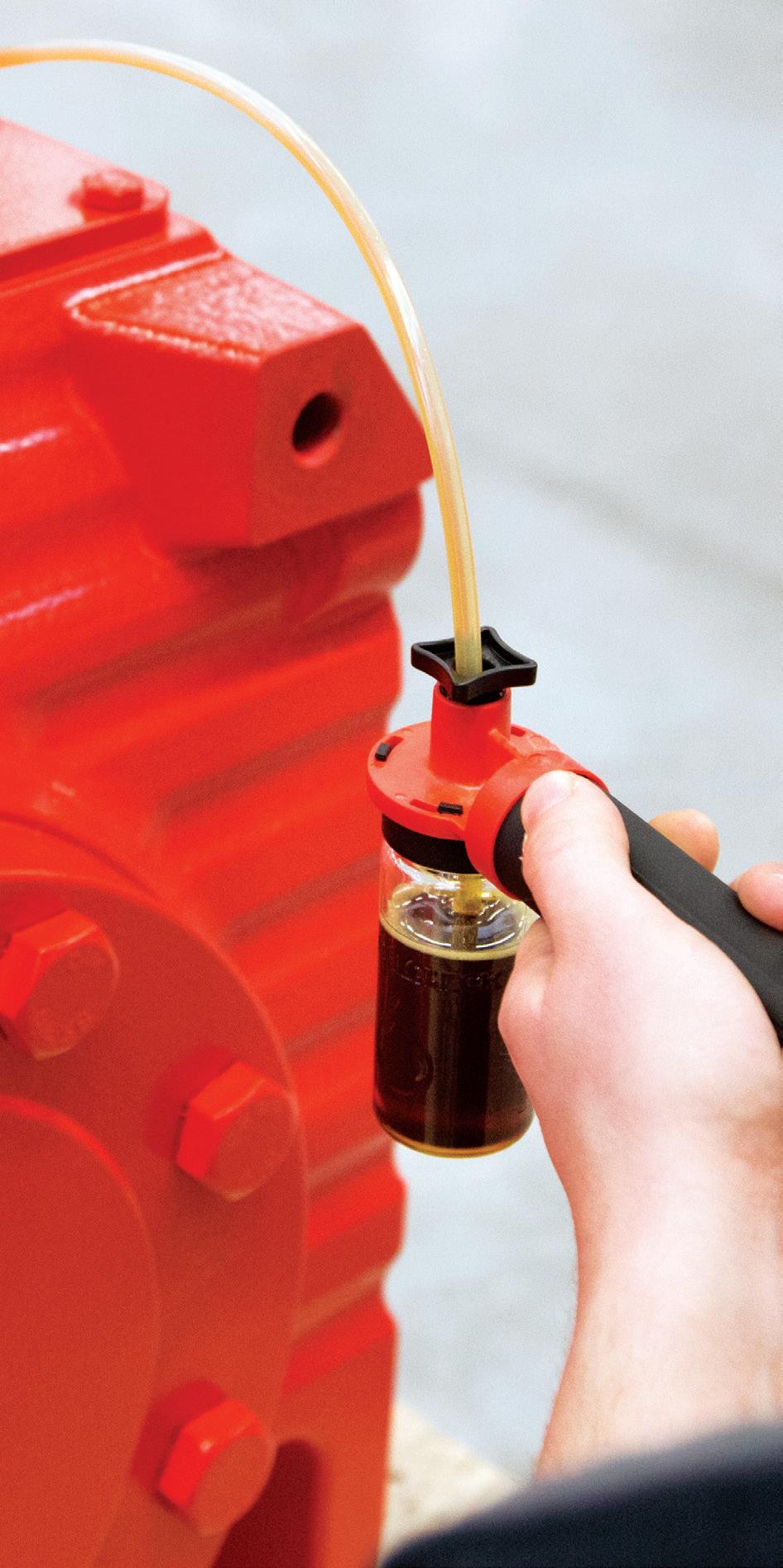

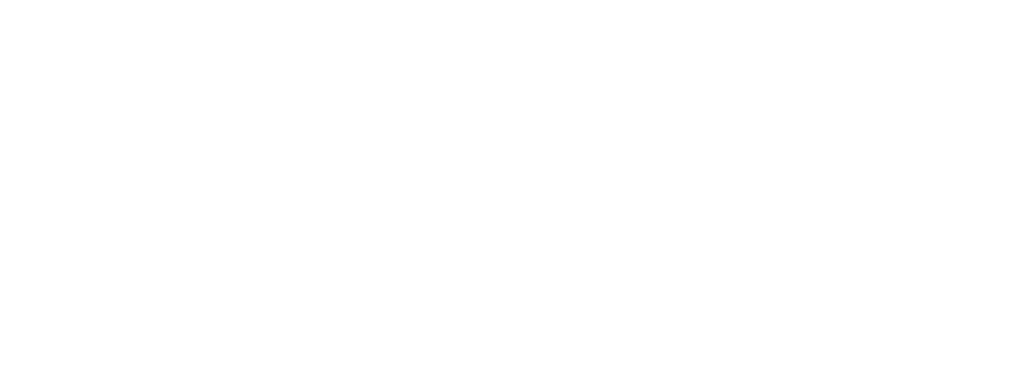

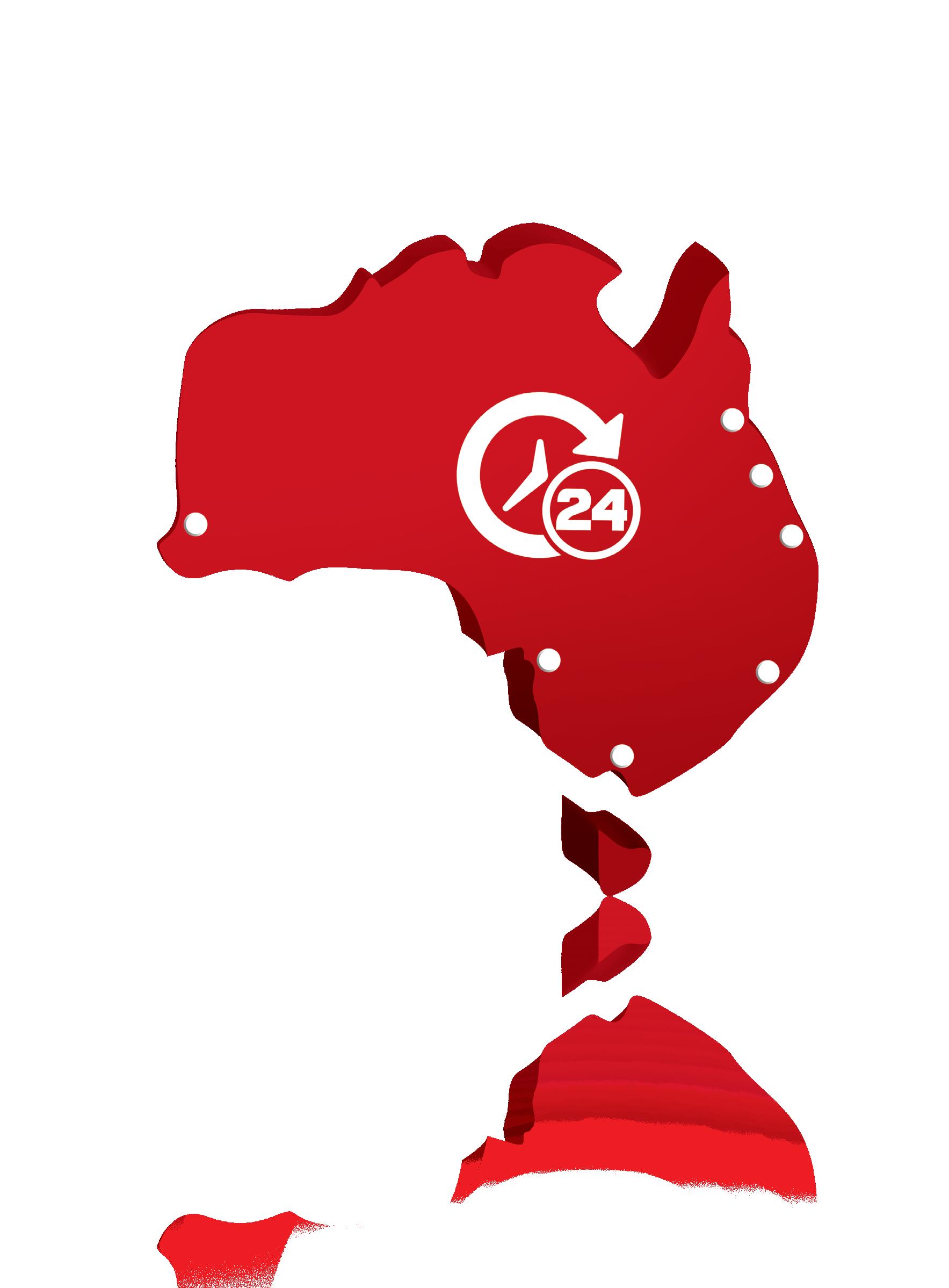
SEW-EURODRIVE Australia turns 40 How the Australian arm of the German gearmotor giant defied recessions and Covid
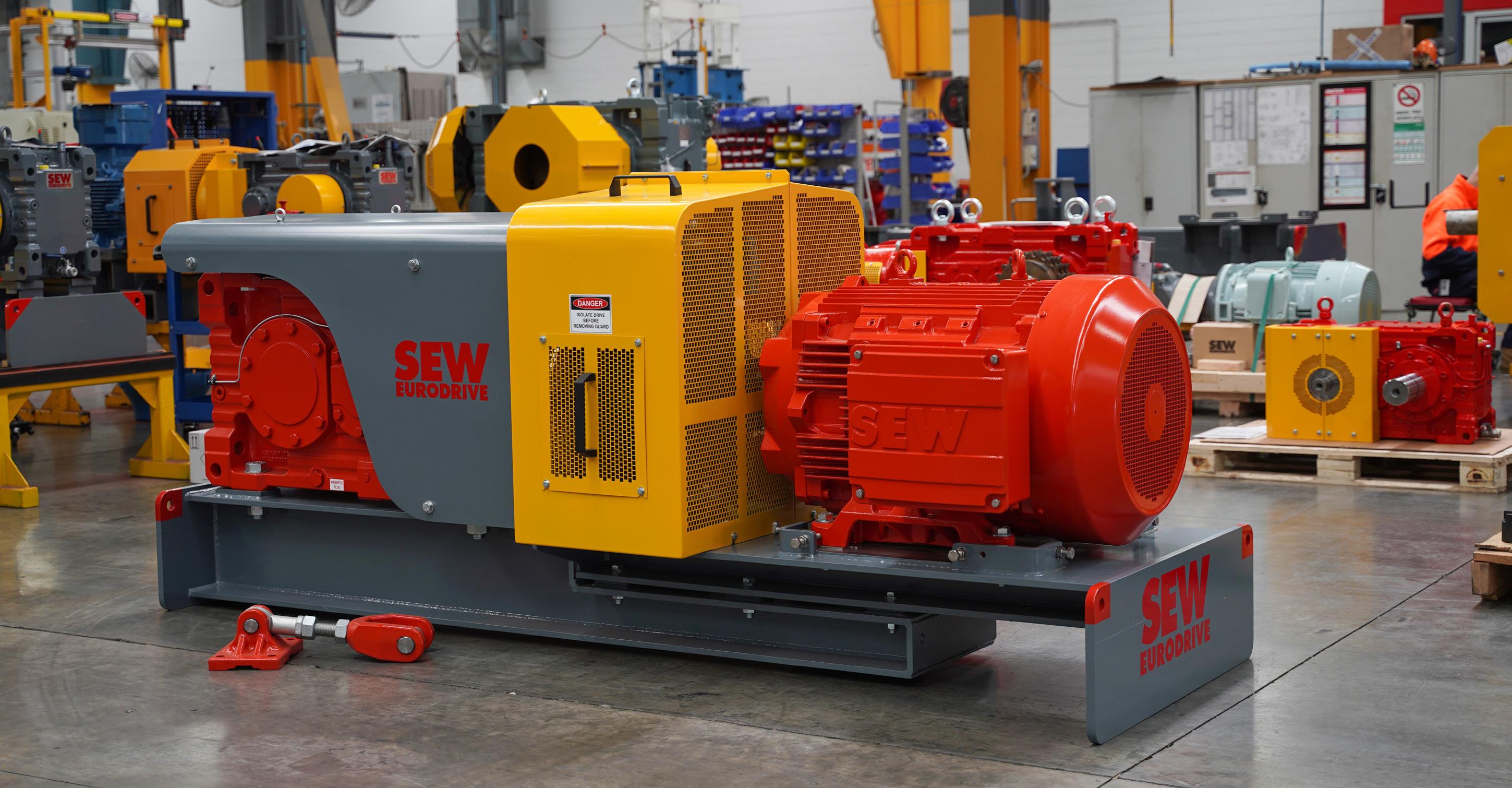
By Margie Smithurst
When Robert Merola turned up for his first day as the sales office supervisor at SEW’s new 5000 square metre Tullamarine factory in 1983, he had no one to supervise. Nor did he have a designated office.
He also had no orders. So, he set to work touching base with companies he knew from previous sales jobs, and eventually one day the phone rang - a pump company had been let down by their usual supplier and
urgently needed six units. The factory assembled the order, and they were delivered the next day. And that’s how Australia’s SEW-EURODRIVE sales kicked off.
Merola says the Tullamarine assembly centre, near Melbourne’s airport and with easy access to the port facility, went from zero to $300,000 turnover in just a few months. By the second year of operations, it had cranked up to $5.8 million, just short of the $6 million he’d predicted to his surprised German bosses. This year, Merola says the Australian company’s on track to reach $120 million.
Origins in Germany
When the Australian subsidiary was formed in August 1982, SEWEURODRIVE was an established family-owned German gearmotor company, with 3,000 employees
around the world, and a turnover of about 150m euros a year, back then in Deutschmarks (300m DM).
Now, the company employs more than 18,000 people, and turns over almost 4.5bn euros.
SEW, which stands for Süddeutsche Elektromotoren Werke, was started in 1931 in Baden, Germany by banker Christian Paehr, who had the foresight to realise the enormous potential of the gearmotor. In 1945, his son-in-law Ernst Blickle took overall responsibility, and in 1982, Ernst’s son Juergen Blickle was given the challenge of establishing and overseeing the Australian arm.
“The successful German model has always been based around centralised manufacturing and supported with de-centralised assembly,” says Merola.
“We were the furthest outpost from Germany at that time … and it was very interesting to get them to understand how vast a country Australia was.
“I remember at one stage I suggested we should consider opening another plant in Sydney, and they looked at the map and said but that’s so close, why do you want to open it there? … and I said, it’s 1000kms away. They really didn’t understand the scale and vastness of the continent.”
When Juergen Blickle relocated to the USA’s operations in 1986, Merola was then appointed General Manager.
“I thought at the time they may send someone over from Germany. Within a space of two to three years, I went from sales office supervisor to Sales Manager, to General Manager. I was in the deep end of the pool pretty quickly for someone under 30 years of age!”
And though the German head office sets the company’s overall tone, pricing and product development, Merola says the Australians “were given relatively free rein and the autonomy to do what we do best”.
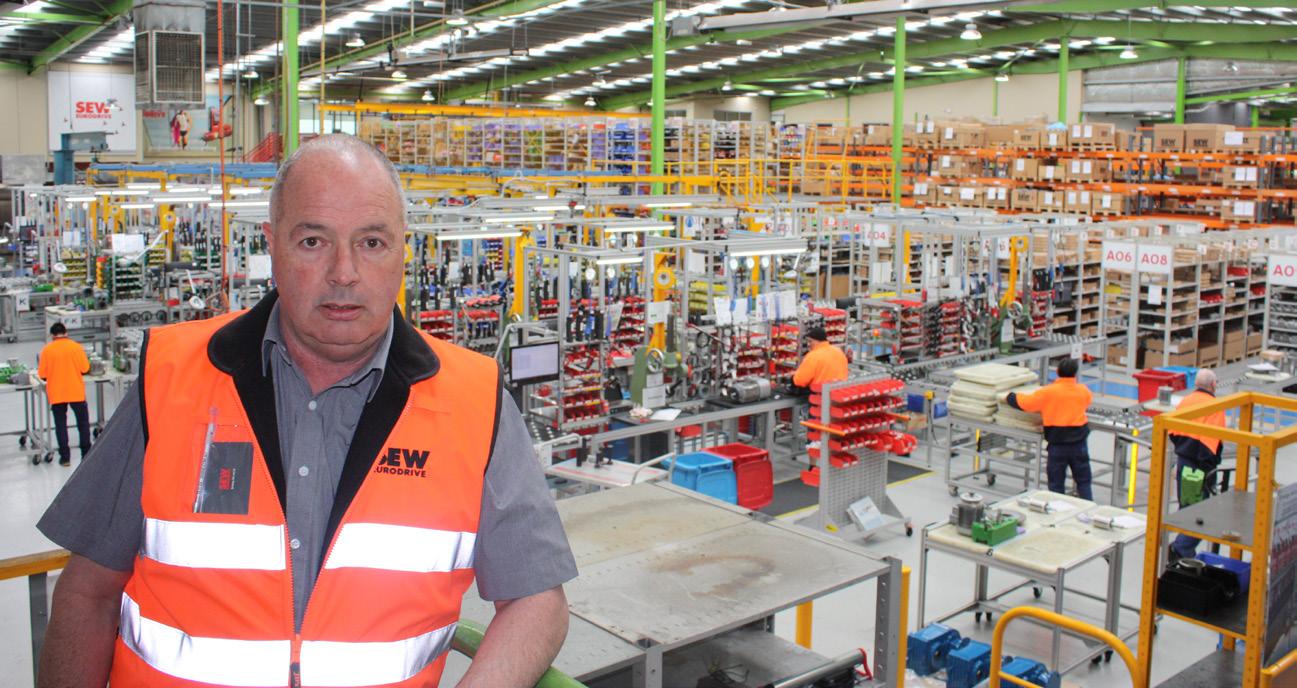
Robert Merola - Managing Director - SEW Eurodrive Pty Ltd traction in a new market. But they were hit hard by the recession of 1991.
“By then we’d grown to about $13 million turnover, well beyond what we ever thought we could achieve in Australia, and suddenly our turnover dropped 25%,” says Merola.
“So, the challenge then was keeping everyone gainfully employed. And that was my first really stressful time.”
The company managed to keep everyone in a job.
“That stood us in very good stead when the economy turned,” says Merola, “Because we already had people on board, the knowledge base we’d retained helped us gain immediate traction in the market against some competitors who’d let people go.”
The company then leapt ahead and grew to $30 million turnover in the next few years, and has ticked along consistently ever since.
Covid defied expectations
Covid would prove the next major challenge. But Merola says the last 2-3 years have ushered in a period of “incredibly steep growth”, which he didn’t expect.
“I expected to go backwards… But (the growth) was mainly because we have an enormous amount of inventory, and always have. We were well resourced, with a very capable team and well stocked, so that stood us in good stead.
“When Covid became the pandemic, we made the decision to gradually increase our stock holdings even further.
“Then, when material shortages
eventually started to bite, fortunately we didn’t feel the full brunt of that because of the amount of stock and replenishment orders we had in the system.
“Also, we were able to remain open as an ‘essential service’ because we supplied key equipment to industries and utilities including food, beverage and logistics.”
During Covid, the company grew over 20% year on year, from $70m in 2019 to the $120m budget expected this year.
“I often think and ask myself where is all this stuff going? I’ve asked that for 39 years now. But I guess everything has a use-by date, the population grows so there are more food and beverage factories - either new ones, expanding, or modernisation retrofitting being done.”
Merola points to an explosion in the number of huge logistics distribution centres just being built by companies such as Amazon, Coles and Woolworths.
“There’s been so much investment in factory automation.”
Supply chain issues are now improving globally, in particular for some electronic components.
“Because our core business is gearmotors, mechanically we weren’t really affected at all. But our electronics production was somewhat affected due to the global shortage in semiconductors and micro-chips.
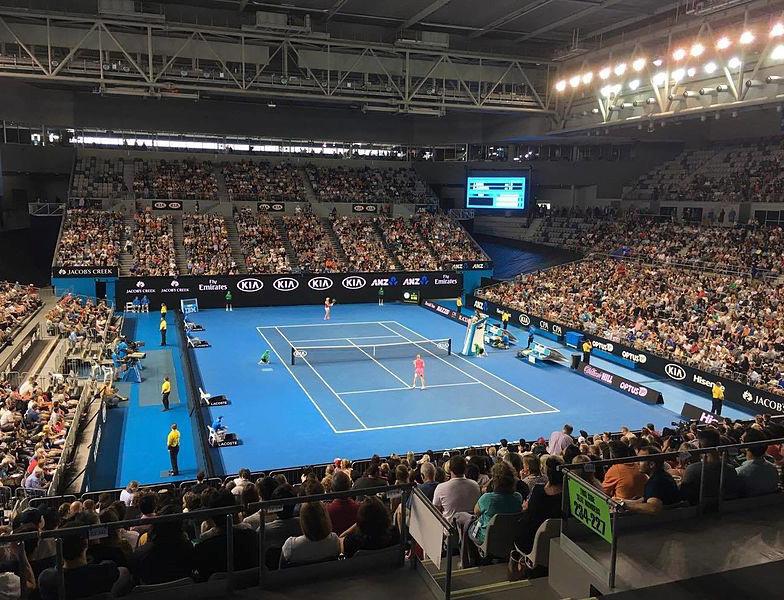
“It was very sobering to hear how small and insignificant we are in that electronics market. We spend $50m USD a year on those components to make our product. Then when you look at Apple spending $70 billion on semiconductors and microchips, it puts into perspective why we couldn’t get anything for 60-100 weeks, which were the delivery times being quoted on some components!.”
That waiting time’s now dramatically shortened, says Merola, as fears of inflation and recession in Europe and the US cause businesses to take their foot off the pedal somewhat.
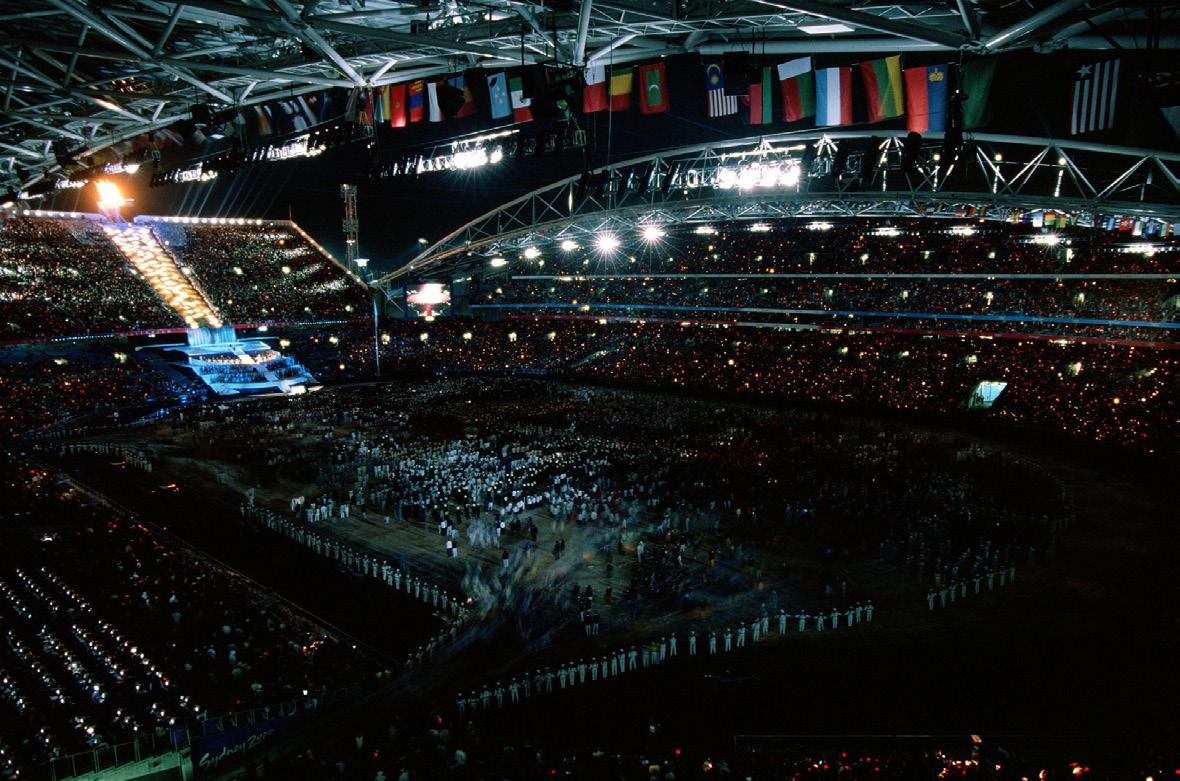
YEAR
ANNIVERSARY 1982 - 2022
lies ahead, he says SEW is currently investing more money in infrastructure than it ever has in one go in Australia.
“We’re committed to about $20million of investment at the moment”, says Merola.
That includes around $8m on a Newcastle Service Plant, and $6m on an existing Adelaide plant, which involves significant renovations to bring it up to SEW standards. The company also bought their Mackay facility after originally leasing it, and is spending about $2m on increasing floor space in their Melbourne facilities by installing 14 automated high bay storage carousels which span from floor to ceiling.
If all goes well and the Australian economy remains as resilient as politicians say it will, Merola sees the company potentially growing to $150m in annual revenue in the next few years. “One of our key strengths is that we’ve always been able to pre-plan and invest, and grow into our skin.
“It can be a guessing game, but we’re well-resourced and well prepared for the future and what it may deliver.”
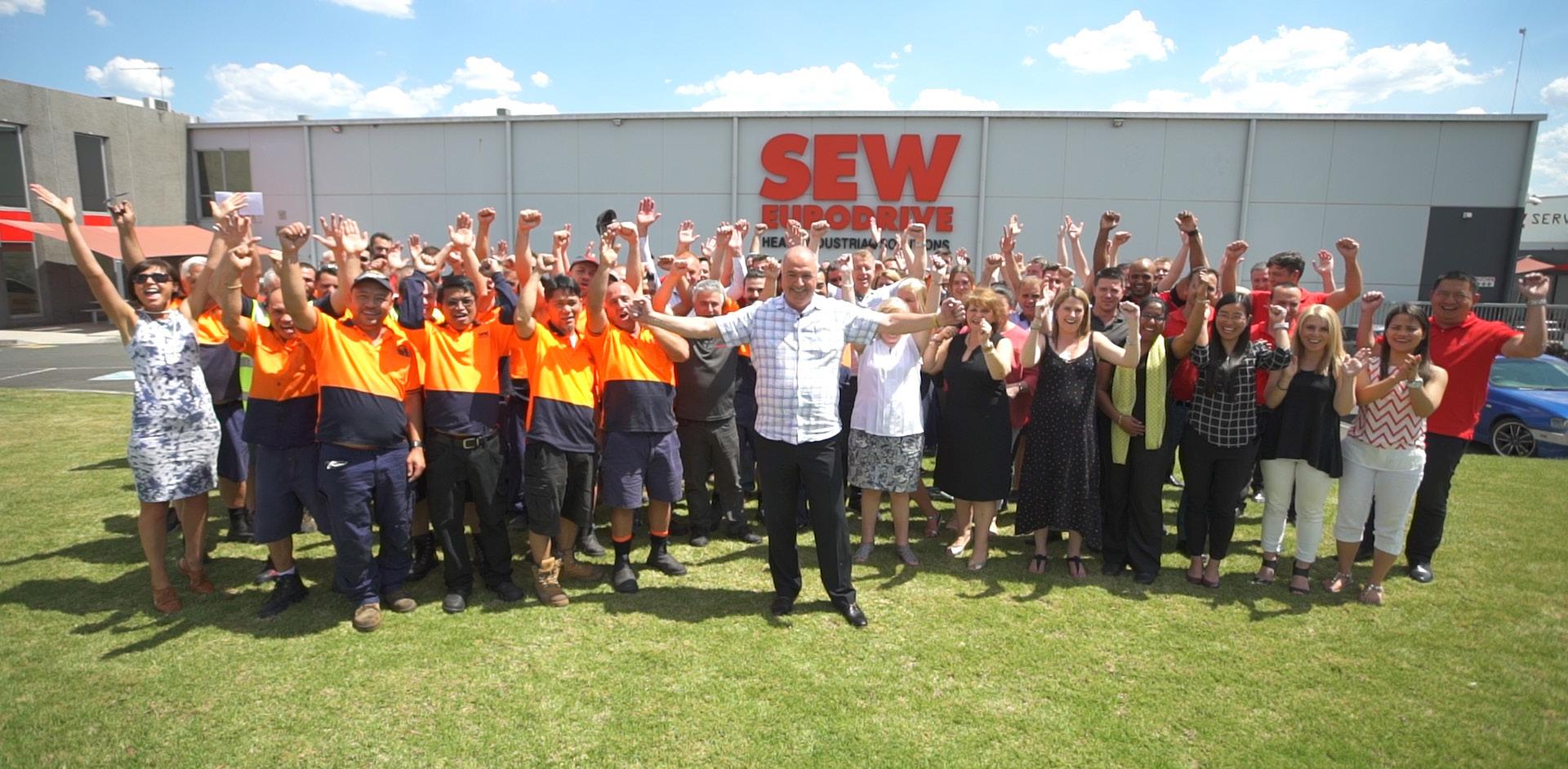
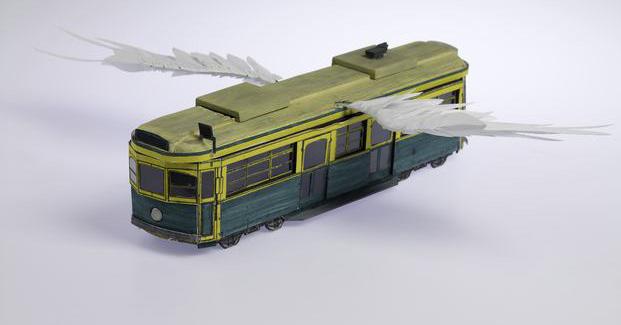
SEW Eurodrive
Significant events in SEW’s Australian history:
Sydney 2000 Olympics
Photo credit: TSGT Rick Sforza
SEW supplied the drive units that helped lift the torch up the waterfall to signify the start of the Olympic Games.
SEW provided the geared motors that open and close the roof at Hisense Arena. This was a daunting task, says the company, as at the time it was one of the only buildings in the world to be a velodrome, entertainment hall, tennis court and basketball court in one venue.
This was a centrepiece for the Commonwealth Games in 2006, and an incredibly difficult engineering feat. Although the chassis was made as light as possible, it still weighed over two tonnes. SEW provided drive solutions for the different moving tram components.