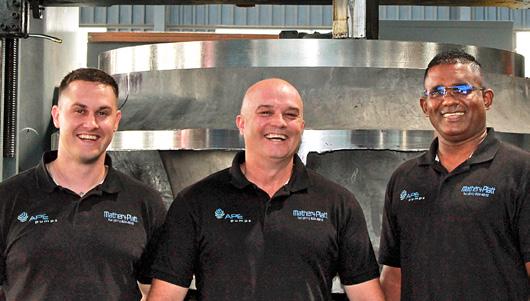
6 minute read
MOVING TECHNOLOGY WITH
A proudly South African original equipment manufacturer (OEM), the APE Pumps and Mather+Platt Group uses technology and its expertise to extend every pump’s life, repairing components where practical. WASA catches up with a few Group team members about some of their recent equipment acquisitions and their commitment to quality control.
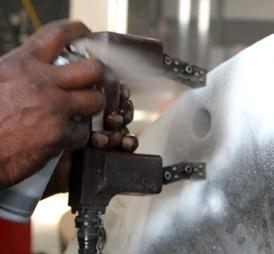
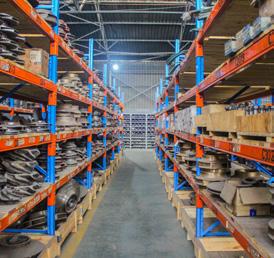
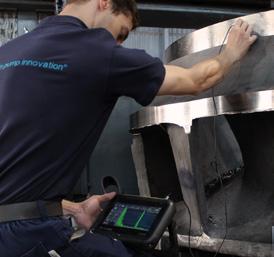
Retrofitting pumps for water systems can lead to significant energy savings, improved performance, extended lifespans, and enhanced functionality through advanced monitoring and control features. But what happens if there are no technical drawings of a pump, or a pump model has been discontinued? What if the pump manufacturer no longer exists or has exited the country?
First off, if it’s an APE Pump, it is reassuring to know that technical drawings for every single pump ever produced since 1952 are kept in a vault system. These technical drawings can be used to execute assessments, repairs, refurbishments, or a complete rebuild. The drawings contain details like metallurgical materials, type of liquid handled, casing, and impeller trims.
“Our recordkeeping is a vital service for our public and private sector endusers, some of whom may no longer have any institutional knowledge of our pumps due to organisational and/ or ownership changes. We also keep records of legacy products we inherited as a Group prior to our formation in 1952,” explains John Montgomery, GM for APE Pumps and Mather+Platt. This contrasts with large parts of Asia, Europe, and the USA, where many pumps are considered obsolete after five years of service. “This is not at all common in South Africa, or the rest of Africa for that matter. There are countless pumps that have been in operation on this continent for decades and decades. All they need is a new part or a retrofit in order to operate for another couple of decades,” says Neil Richards, sales engineer at APE Pumps.
3D scanning
In these circumstances, for all other non-APE pumps, a 3D scanner is used to produce a complete model of pump parts in minutes, taking geometric accuracy and on-site lidar surveys to an unprecedented level.
“With this data, we then reengineer and manufacture the pump parts in our pattern shop. The 3D scanner has drastically increased our turnaround time for pump repairs and retrofits,” says Richards.
It is important to remember that a pump works within a system, he adds. Often, if a new pump is installed, the piping around the pump, as well as the plinths and motors, usually need to be replaced too, which is costly, timeconsuming and can cause a prolonged shutdown of operations. In these instances, 3D scanning can be used to take dimensions of the pump that must be replaced, and then manufacture a new pump to fit into the manifolds.
If it is a complete rebuild, the manufacturing team can scan the original, make a pattern, manufacture it, scan the new one, and then compare the two in a digital overlay for verification.
Last year, the company scanned an entire pump station, where the model of the pump that was to be installed was attached to the 3D scanner. This put the pump in a virtual world and enabled APE to make sure the flanges were matching and fit perfectly into the casing. The scanner also helped to plan how the pump would be installed. This is valued by clients who do not have up-to-date plans of their pump stations.
According to Thorne Zurfluh, mechanical engineer at APE Pumps, one of the biggest benefits of 3D scanning is quality control. “At APE, 3D scanning is used over and above the traditional quality control methods. It is an additional aid to prevent the misalignment of pumps by verifying pump geometries (concentricity, parallelism, perpendicularity, and shaft runouts) during manufacturing, assembly, and even commissioning. All pump parts are scanned to confirm that they meet the specifications of the manufacturing drawings. The 3D scans also generate digital reports indicating that the pump and pump parts meet (or fail to meet) certain specifications and tolerances. These reports are often supplied to customers.”
Patternmaking
Dovetailing tried and tested techniques with modern technologies is a hallmark of the success of APE Pumps and Mather+Platt. Today, for example, the Group is one of the few OEMs that still has a patternmaking shop, headed by a master artisan.
Traditionally, 2D drawings were used – with the measurements painstakingly replicated by hand by the G roup’s patternmakers – to create the casting mould. Now, the 3D scanning method has produced more rapid results.
“A patternmaker cannot be replaced by technology. For a pattern to be milled out of a block of wood, one needs a person that is a patternmaker, draughtsman, and machinist. That patternmaker must understand a bunch of other complexities such as shrinkage rates of different materials. Only then can that person operate a computer numerical control (CNC) machine correctly,” states Montgomery.
Non-destructive testing
Another technology adopted by APE Pumps is non-destructive testing (NDT), which detects the presence of defects damaging or destroying the material being examined.
“NDT gives our clients total quality assurance. Examples of NDT processes include ultrasonic examination, magnetic particle inspection, and dye penetrant (DP) testing. An ultrasonic examination uses soundwaves to identify cracks and a material’s thickness based on the rate of response. Magnetic particle inspections are used to check for surface or subsurface cracks in pumps made with ferrous metals. Another common NDT technique employed by the Group is DP inspection – used to detect any hairline cracks in the surfaces of pump parts. All three tests must be done by qualified, trained professionals,” explains Zurfluh.
According to Richards, NDT has been used on many old pump shafts, as flaws are difficult to detect with the naked eye. “This is another preventative measure that we offer clients, as a broken shaft can cause a catastrophic pump failure.”
Remote monitoring
Some APE customers such as water monitoring. Systems can be set up for either APE or the client to monitor pump performance. “The need for remote monitoring is driven by the demand for improved energy efficiency, as well as enhanced maintainability and serviceability of pumps. Variable-speed drives (VSDs) provide a much higher level of monitoring and protection,” says Zurfluh.
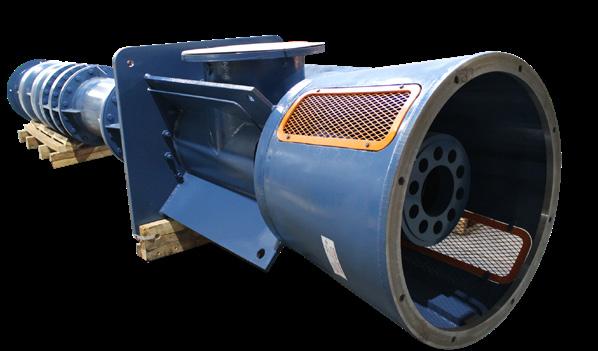
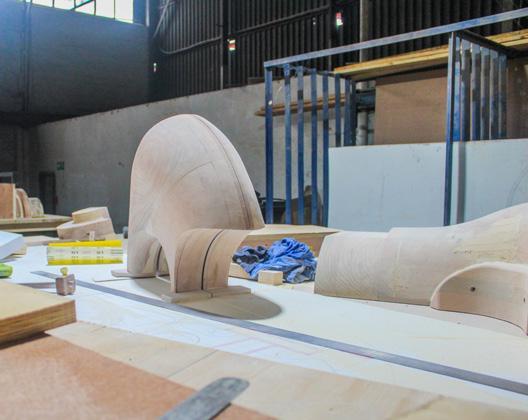
He adds that remote monitoring assists with predictive maintenance and further improves service levels.
“Bearing temperatures, output, vibrations, and energy consumption are a few of the parameters that can be monitored. This enables APE to identify any pump issues in advance, make sure the pump is operating on the right curve, and conduct more proactive maintenance – to prevent clients from running pumps to failure. We are also seeing an increasing shift towards outsourced operations and maintenance, which is a key growth area for the Group, working with clients to optimise their systems.”
Recently, the Group has made significant technological investments, including:
• a centre lathe equipped to handle jobs ranging in lengths of up to 8 m and in varying diameters for components such as columns, shafts, and impellers (specifically for circulating water pumps)
• a key slotter for keyway cutting (a drive system feature on one of the Group’s impeller lines to enable rotation around the shaft)
• a 12 tonne CNC horizontal boring machine for the final machining of larger impellers, which typically measure around 3 m in diameter
• a vertical boring machine for the machining of larger components with a Ø3 500 capacity.
The nexus of technology and talent
“All of this technology must be used and operated by people. Clearly, no pump engineer, specialist technician, or artisan is born overnight. The baseline skills are essential, but the experiential, applied learning is what defines master craftsmen, engineers, and project managers in all our interrelated disciplines. That is why our business is dedicated to attracting and mentoring the best talent available. We like a two-way mentorship approach, where the old teach the young and vice versa, in modern versus tried and tested techniques. Every member of the group is a highly valued team player who contributes to our collective success. We have exceptionally high employee commitment levels, which is why so many of our staff stay with us through to retirement,” explains Montgomery. www.apepumps.co.za www.matherandplatt.com
It is evident that technology plays a big role in APE’s business and is leveraged to improve APE’s service offering. “APE Pumps offers far more than the traditional services of an OEM. We can even stock brand-new units for a client so that we can implement a service exchange. The client will provide APE with an old pump to bring to OEM specifications and APE will give the client the new pump. Many companies are no longer keeping critical spares in stock, so we do this for them. If well maintained, APE and Mather+Platt’s pumps will last a lifetime – across Africa, there are hundreds of working examples. APE Pumps has never discontinued a pump model since inception in 1952, so parts are always available,” concludes Richards.
