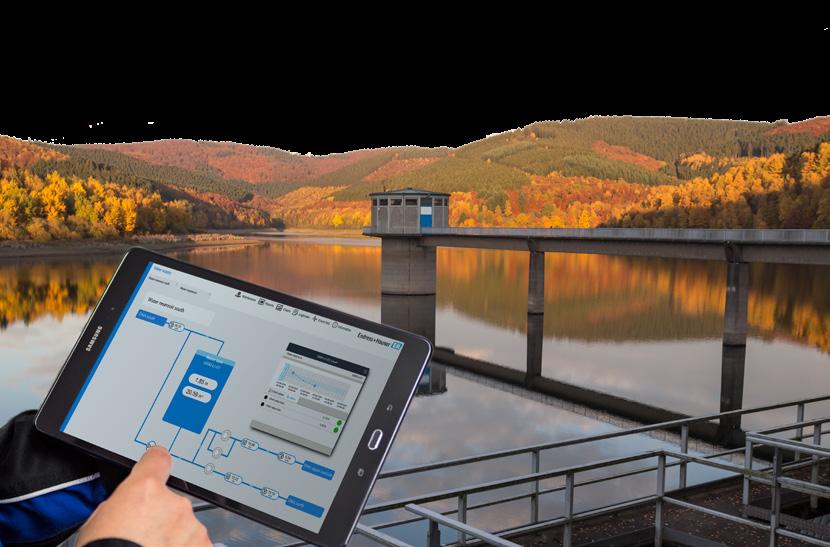
3 minute read
OPTIMISING POWER CONSUMPTION OF WASTEWATER TREATMENT PLANTS
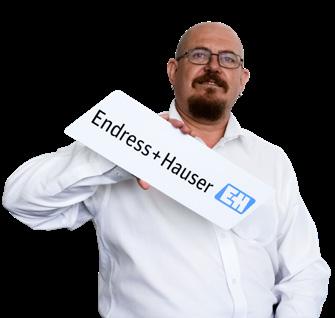
In the 2022 Green Drop Report, proof of energy-efficiency management must be provided by specific power consumption (SPC), energy unit cost (R/kWh), and express energy treatment cost in (R/m3).
The 2022 Green Drop Report noted that that very few water services authorities (WSAs) conducted a baseline energy audit or could account for their wastewater treatment plants’ CO2 footprint. The few WSAs that did provide a baseline energy audit released concerning results.
The SPC values range from 0.002 kWh/m3 to 1418 kWh/m3 – outliers were removed to keep approximately 80% of the original data set. The data indicates:
• There is a marginal difference between the basic and advanced systems –0.90 kWh/m3 and 0.94 kWh/m3
• The median values differ slightly –0.76 kWh/m3 for advanced systems and 0.53 kWh/m3 for basic systems.
• This is notably higher than the international standard of 0.177 for trickling filter and 0.412 for advanced activated sludge technologies.
• The average SPC for advanced systems varies from 0.289 kWh/m3 to 2.37 kWh/m3 and is between 0.07 kWh/m3 and 2.94 kWh/m3 for basic systems.
Route to improved energy efficiency
The first step to improve a wastewater treatment plant’s efficiency, including energy efficiency, is to capacitate operations and maintenance staff and managers with adequate training relevant to plant and process efficiency. The second step is to measure, capture, and monitor data in real time. Utilising this data will present the WSA with opportunities to reduce costs through process optimisation and improved energy efficiency, and beneficial use of sludge and other energy resources.
One of the important topics is to make the use of energy more transparent by calculating key performance indicators (KPIs), highlighting overall energy consumption, and assisting operators to identify energy-saving potential.
Analysing the performance and energy consumption of a wastewater treatment plant helps to:
• detect saving potential through constant monitoring of energy relevant areas of the treatment plant
• benchmark efficiency of treatment plants with similar plants to create transparency and define further activities
• track energy usage and determine the cost of wastewater treatment
• evaluate equipment, system, and control performance to find the ideal point of operation, avoid downtimes, and ensure plant safety
• quantify benefits of system modifications and improvements
• verify predicted performance
• improve KPAs in Green Drop audits. In an advanced level wastewater treatment plant, the energy cost hovers around 25% to 40% of the operations and maintenance budget.
Measurement values required for the plant’s overall power consumption are:
• the inlet flow
• COD (chemical oxygen demand) at inflow (lab result input)
• total plant power consumption from the electricity meter.
This provides the plant operators with the amount of power required to treat a certain volume of wastewater at a certain biological loading.
Aeration performance
Depending on the type of aeration in the bioreactors, the power consumption of the aerators/blowers can be up to 50% of the plant’s power consumption. Typical causes for inefficiencies of blowers relate to pressure loss through leaks in piping, blockages in air piping, or blocked aeration elements. Through monitoring pressure, air flow, and power consumption measurements, this will indicate the optimum operational point of the blowers and when maintenance is required on the aeration elements.
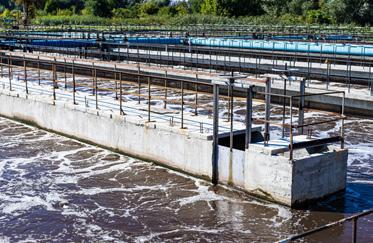
single processes but to monitor the complete system to discover related effects of interactions between processes. For a CHP plant to optimally produce heat and electricity, the CHP efficiency and sludge gas production efficiency must be analysed and optimised.
To calculate this KPI, it is necessary to measure and monitor the blower air flow, air pressure, COD value, inflow into aeration basin, and blower power consumption. By using in-line dissolved oxygen and ammonia measurements, we can determine the optimum air required for nitrification to take place, which supports energy-efficiency gains within the process.
Electricity generation
Increased electricity production is often easier to achieve and less expensive than undertaking electricity savings measures. Key process parameters such as gas to COD ratio or electrical and thermal efficiency of combined heat and power (CHP) plants are essential parameters for the optimisation and verification of electricity production or quantifying the effects of co-fermentation.
In this context, it must be pointed out that it is necessary to focus not only on

The following measurements would be required to optimise CHP and sludge gas production efficiency:
• sludge flow into digesters
• COD value
• biogas volume flow
• biogas pressure
• biogas temperature
• power production
• total power consumption.
Pump performance monitoring
Benchmarking based on power consumption, flow and pressure are useful to discover weak performance and maintain pumps in-time. For example, centrifugal pumps require regular impeller adjustments to avoid significant efficiency loss.
In some of the more advanced wastewater treatment plants, most of these process measurement points might exist, which decreases the capital cost for this investment. Endress+Hauser can assess existing instrumentation and analyse what additional measurement points are required to achieve efficiency goals and gains to improve the plant’s Green Drop rating. A simple solution could be to centralise these KPA calculations on an RSG45 data manager or create a dedicated SPC monitoring system solution hosted in our Netilion ecosystem. Endress+Hauser understands the importance that efficiency and sustainability plays in the Sub-Equatorial Africa wastewater industry and remains committed to supporting you in achieving these goals.
CASE STUDY Location: Umhlanga, KwaZulu-Natal (KZN), South Africa