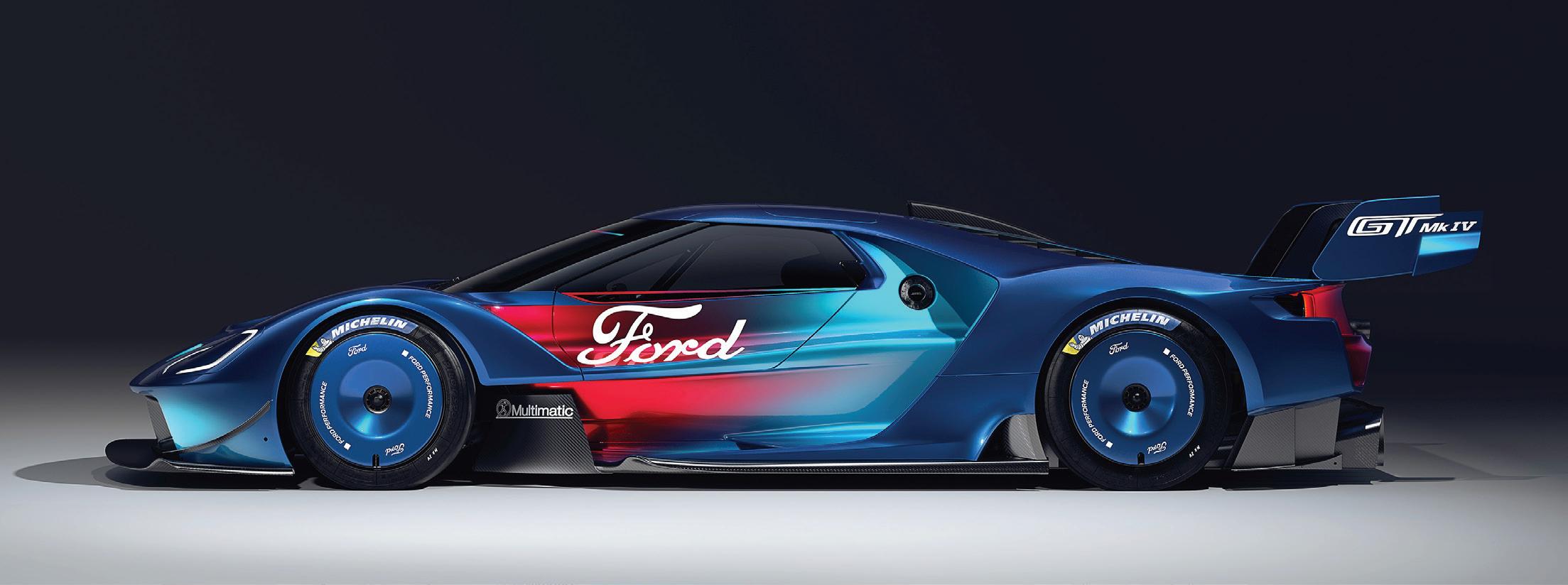
11 minute read
CHALLENGES
My father used to regularly say, “I think that you may have bitten-off more than you can chew, young man.” He used it quite a lot back in my early teens, most often directed at overly optimistic mechanical modification / repair projects that I had chosen to tackle. Some of those undertakings were purely aimed at fixing shit that I had broken, like the chain tensioner of my Artic Cat 292 Lynx snowmobile back in the very early 1970s. That undertaking was the first proper usage of ‘my first toolbox.’ Not the Fisher-Price toy, but a Craftsman ‘beginners set’ out of the Sears catalogue (Simpson-Sears in Canada), that massive mail-order tomb that preceded Amazon by a century, at one time selling everything from hammers to houses. It also contained a substantial lingerie section which was all we had access to in those times, considerably more wholesome than what’s now accessible on every young man’s cell phone. That shiny red toolbox was under the tree the Christmas that I was 12 and some of the contents are still in my roller cabinet today. I learned a lot about CVT belt drives working on that snow machine, as well as how much power was consumed that ultimately never made it accelerate (a staggeringly inefficient power transmission system). The retaining bolt in the eccentric tensioner had stripped, causing mechanical mayhem in the chain case whenever the throttle was applied, so I drilled it out and used a bigger bolt to cut a new thread… it unfortunately worked (without any thought to using the correct tap drill size, or for that matter a tap), despite my father using his favourite discouragement line at the most critical time. All of which contributed to a lifelong confidence in my ability to ‘bodge’ a field fix in the face of disaster (rule No. 1…never, ever panic). I recently successfully applied the approach at the debut test of our new Mustang GT3 car with equal success!
I got the same reaction from Dad when I removed the shocks from my 1973 Can-Am MX-1 motocross bike (I believe that they were Girling but I have also been told S&W…can any readers enlighten me on that?), stick-welded some new upper mounts on a diagonal frame member that was obviously not designed to take the load (in bending), with a matching pair of nicely made brackets identically attached to the swing arm, creating the ‘laid down’ configuration becoming popular in 1975. I was trying to copy the new MX-3 “coming soon” from Bombardier (not for the last time using a photograph as my engineering drawing). The early teaser advertising blurb boasted double (or more) the three inches of rear travel that my first generation Can-Am offered. That bike had great power from the rotary valve, two-stroke Rotax motor but all my buddies with Honda CR Elsinores and Yamaha YZ’s (which came with the first version of monoshock in ‘75) smoked me in the rough stuff. Unfortunately, they continued to do so against my home-grown setup because the overdriven dampers ‘sacked out’ trying to keep up with the highly adverse motion ratio (as well as some potential ill effects from inverting them). Live and learn…or not.
So, have I figured out that I shouldn’t bite off more than I can chew? Nope! In fact, the group that I’m responsible for at Multimatic (Special Vehicle Operations…MSVO) has never been busier, with more projects underway than ever before. As the Australian racing legend Peter Brock contrastingly used to state, “Bite off more than you can chew and then chew like hell.” And everybody at MSVO is presently chewing as hard and fast as possible. It makes it easier that everything we are working on is super cool stuff, but on the other hand massively challenging. I can’t discuss all of it due to confidentiality, but here are a few of the projects that I can.
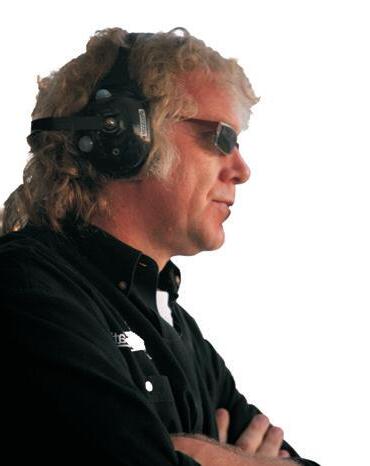
Many of you will have caught the recent press and YouTube videos of our first test with the new GT3 Mustang at Sebring (check out https://www.youtube.com/watch?/v=16BJKlof9GE). By all accounts it was the best initial run of a new race car in our history (touching wood with the hope that it continues to go so positively). Despite the fully cooked prototype appearing to magically appear in Florida, a mere six months after a CGI version was shown at the launch of the Generation 7 Mustang in Detroit, those three days were the culmination of well over a year of intense engineering and development. Saying that it was amazing the number of people that asked me how the testing was going last September when the animated version was shown hot lapping in company with its Mustang racing siblings (for sure it was an excellent computer-generated video, but REALLY? I guess all the virtual racing is altering people’s perception of reality). The GT3 Mustang project has the same level of focus as the Ford GT did when we were chasing the 50th anniversary win of the original GT40 at Le Mans. But this time the target is to win with a Mustang. The wholesale global adoption of the GT3 formula now accommodates this aspiration as well as opening all the other classic endurance events (Daytona, Sebring, Bathurst, Nürburgring and Spa) to our third kick at the can for this class of Mustang (I won’t discuss the first two, they weren’t fully supported by the blue oval but this one is, in fact, is their program).
The project is a totally cooperative three-way partnership between us, Ford Performance and M-Sport…yes, Malcolm Wilson’s legendary WRC outfit are developing the engine.
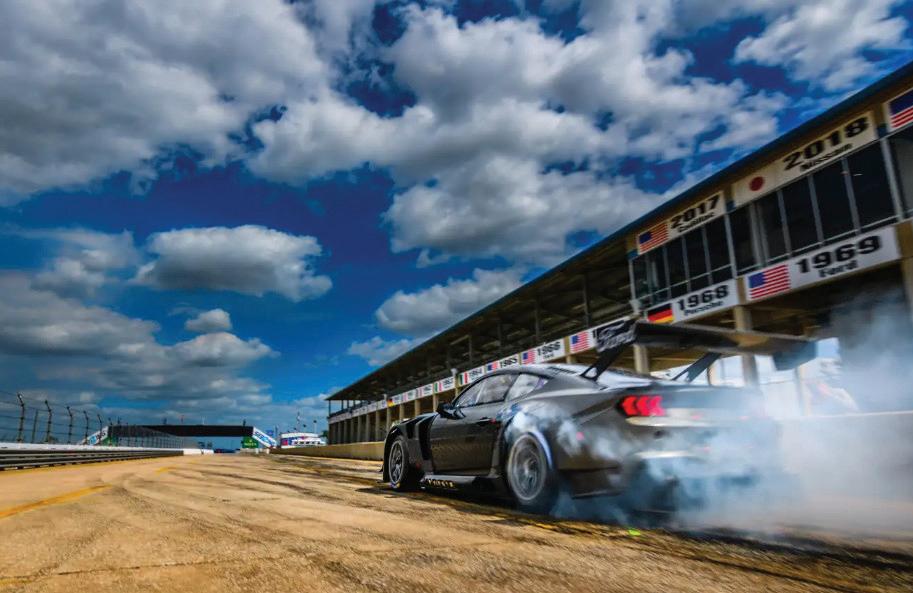
Months of engineering simulation (engine, aerodynamic, chassis / suspension and myriad sub-systems) led to a first round of physically testing aspects of the engine, as well as running over a hundred body configurations with a 40 percent aero model in a moving ground plane wind tunnel, backed-up by endless Driver in the Loop simulator sessions with real drivers evaluating everything from vehicle dynamics performance to power curve configurations, not to mention where shit should be placed on the steering wheel (completely new and bespoke for this program). With all of it about 80 percent nailed down, the tooling phase had to be kicked off to meet the demanding program timeline. Jigs and fixtures for the steel structure modification and safety cage installation, carbon composite tooling for the body (some 125-plus individual pieces), engine component manufacturing, suspension machining / welding fixtures and a load more. And with the GT3 rules now including Pro-Am categories everywhere (in fact the World Endurance Championship, WEC, and Le Mans will only include that single class next year) the team has had to construct tooling to handle building dozens of customer cars (in contrast to the total of seven racing GTs that were ever made). It is a staggering undertaking only made possible by total commitment and incredibly tight cooperation from the three partner companies. And so, was it truly a trouble-free first three days? No, and that is not what I stated above, what I wrote was that it was the best initial run we have ever had, but the first day was a shit fight that saw Sean Mason and I heading to the Sebring TSC (Tractor Supply Co.) for some steel plate, tubing and a fist full of threaded rod (Sean actually went twice, the second time with our Team Manager, Charlie Cadieux, to buy a MIG welder and more steel as our TIG wasn’t up to the fabrication project). There really were no fundamental engineering issues, just details that needed a little temporary ‘bodging’ to create a bit of robustness, skeptically overseen by our Motorsports
Engineering Technical Director, Julian Sole. I was up to my elbows in it all with dad’s words ringing in my ears. Although he passed ten years ago the influence, or my disregard for it, carries on.
We ran the final two days trouble-free and accumulated a couple of hundred laps which was right on our target. I’m now writing this on a London-Orlando flight two weeks after that first test, this time for an endurance / durability run with five drivers. In the interim our team has designed proper production fixes for the issues, had them tooled and made parts which are on the car with spares in the trailer. Some of it is being undertaken in our UK facilities. Oh, and the test car was in a full-scale moving ground plane wind tunnel just a week after leaving Sebring, correlating and verifying all of the simulation and scale model work. All undertaken by a truly amazing group of people!
At the same time as the full-court press development of the GT3 we have also been working on, and just put the finishing touches to, a GT4 version of the new generation Mustang. This is a Newmarket, ON-based project run by Sean while the GT3 development, build and ultimately race operations (in the 2024 IMSA WeatherTech SportsCar Championship) is undertaken in Charlie’s Mooresville, NC facility. The GT4 is far less radical than its big brother and very much derived from the Gen 6 based car that has been successfully campaigned around the world by Multimatic Motorsports and our customers for the past six years. We got oh-so-close to winning the British GT Championship back in 2019 with it, finishing runner-up by a handful of points. Two of our customer’s cars that presently run in that series just finished P1 and P2 in the opening round at Oulton Park over the Easter weekend (the beginning of the car’s seventh year of competition and still fully competitive!).
However, my statement that it is based on the previous car (the project’s original plan) might sound like a stretch when I list the incremental changes. Although we didn’t start from scratch, it is a pretty significant “evolution:” New fourth generation Coyote 5.0 litre V8, now with a twin plenum intake manifold and dual throttle bodies, a completely new lightweight high strength FIA roll cage, trick Alcon pedal box, bespoke racing steering wheel, myriad electronic upgrades, a totally new aero package, and a selection of ‘sustainable’ composite bodywork (roof, doors, hood, rear wing) made from hemp-based fibre (I won’t crack the most obvious joke, its getting old within the team). The really solid stuff remains, the Hollinger paddle shifted dog box, fuel system, Motec data, and DSSV adjustable racing dampers.
We just shook the car down over two days in Sebring (during the second test of the GT3, time is passing as I write this) and it was the second best initial run of a race car in our history, the only issue being a problem with the dry sump tank puking oil out all over the place (only a very slight change to the configuration from the previous car but enough to cause an issue). Took half a day to sort it out and then Jeff Ripley (the father of the car) and his guys started matching the GT3 lap accumulation! By the time you read this I’m sure that there will be images all over the internet, but I’m not at liberty to show anything right now.
And if Mason and his team didn’t have enough on the go, they are in the middle of building the first Ford GT MkIV pre-production test car. This is the final evolution of the legend that we started work on almost ten years ago. The MkIV, which takes its name from the 1967 Le Mans winner (driven by Dan Gurney and AJ Foyt) and will have a limited production run of 67 (see what we did there, and it was code named ‘Gurney’ during its engineering phase). We have had far more than 67 people wanting to buy the car and are now working through the allocation process, top of the list being our regular customers (loyalty begets loyalty). Like the MkII it is a track only weapon. The MkII being my all-time favourite performance vehicle, absolutely outstanding to drive with an amazingly tame manner, making it easy to hustle to a good lap time without drama. The MkIV has turned it all up to 11. I won’t go off the rails on the specifications but the highlights are 800-plus horsepower (100 more than MkII and 150 more than the road car); a totally new body returning 2400 lbs of downforce (at 150mph), 600 lbs more than the MkII; 50 mm longer wheelbase than the road car/MkII which improves weight distribution, rear diffuser performance and accommodates an Xtrac racing gearbox that replaces the Getrag DCT of its two sisters. Suspension has been considerably lightened, geometry optimized, and the uprights now utilize centre lock hub retention for the 18inch wheels (down from 19 inch on MkII and 20 on road car) which accommodates the latest technology slick racing tires. To control all the increased input from the suspension, Multimatic’s Adaptive Spool Valve (ASV) dampers provide a constantly variable control of overall vehicle transient modes, with the capability of choosing from several different levels of response (using a knob in the cockpit). These replace passive adjustable DSSV dampers on Mk II and selective DSSV on the Ford GT. I didn’t get into the engine details because I’m a chassis man, so the only important point was the power increase… but it’s an entirely new piece, although still an Ecoboost. I’m not sure how amazingly tame this car will be (a reference to the MkII) but it will definitely be the ultimate interpretation of the GT…an appropriate swansong for one of the greatest Fords in history.
And to top the Ford story off, we are now starting to build customer Bronco DRs…also a limited volume run, just 50 of them. Again, not for the road, but a production-based off-road racing truck that can compete in numerous classes specifically created for this type of vehicle (including Baja). The production V6 turbo motor is gone (the biggest engine available in the Bronco), replaced by a Coyote V8 (same as the basis of the Mustang GT3 and GT4 car’s powerplants). The body is lifted on a highly strengthened chassis, the full safety cage integrates the production Multimatic manufactured ACCRA upper structure and, an all-new technology, Positional Selective DSSV damper are utilized (zone adjustable from within the cockpit via a Bluetooth device) with a whopping 17 inches of wheel travel. It rides on 37-inch BF-Goodrich Mud-Terrain T/A KM3 tires nailed to bead lock rims. The front lower control arms are massive billet machined parts, but a great deal of the production truck remains including the upper control arms and much of the body and chassis structures. It is an amazingly capable off-road racer which has spent half a year running durability testing in Johnson Valley, CA, home of King of the Hammers (we’ll never get the sand out of our race trailer). Once again, way more people want them than the 50 that we are building so another allocation process is underway to identify potential owners, with preference to those who will actually race them.
I’m worn out just writing about all the stuff that we’re presently working on, and it is only four of the ten major projects that we have on the go (and there is also a load of smaller things that are ongoing). For sure Jim Holt would consider our activities more than MSVO could possibly chew, but he would be wrong because it is all happening and in a really impressive way. In no disrespect to his regularly asserted commentary, I gotta go with Peter Brock’s adage and just keep “chewing like hell” because it’s pretty exhilarating to be able to create the products and technology that we are with such an amazing group of people. And it’s not a big group, just a massively talented and highly motivated one. Thanks to them all. IT
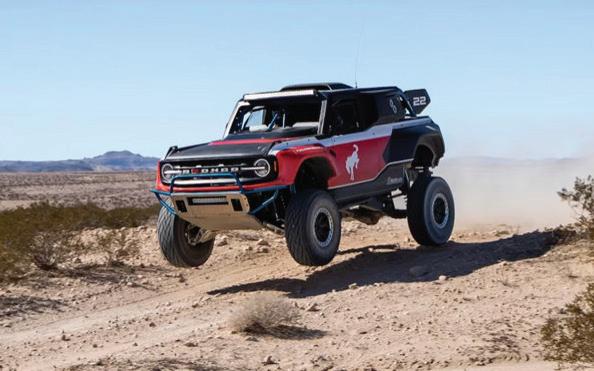