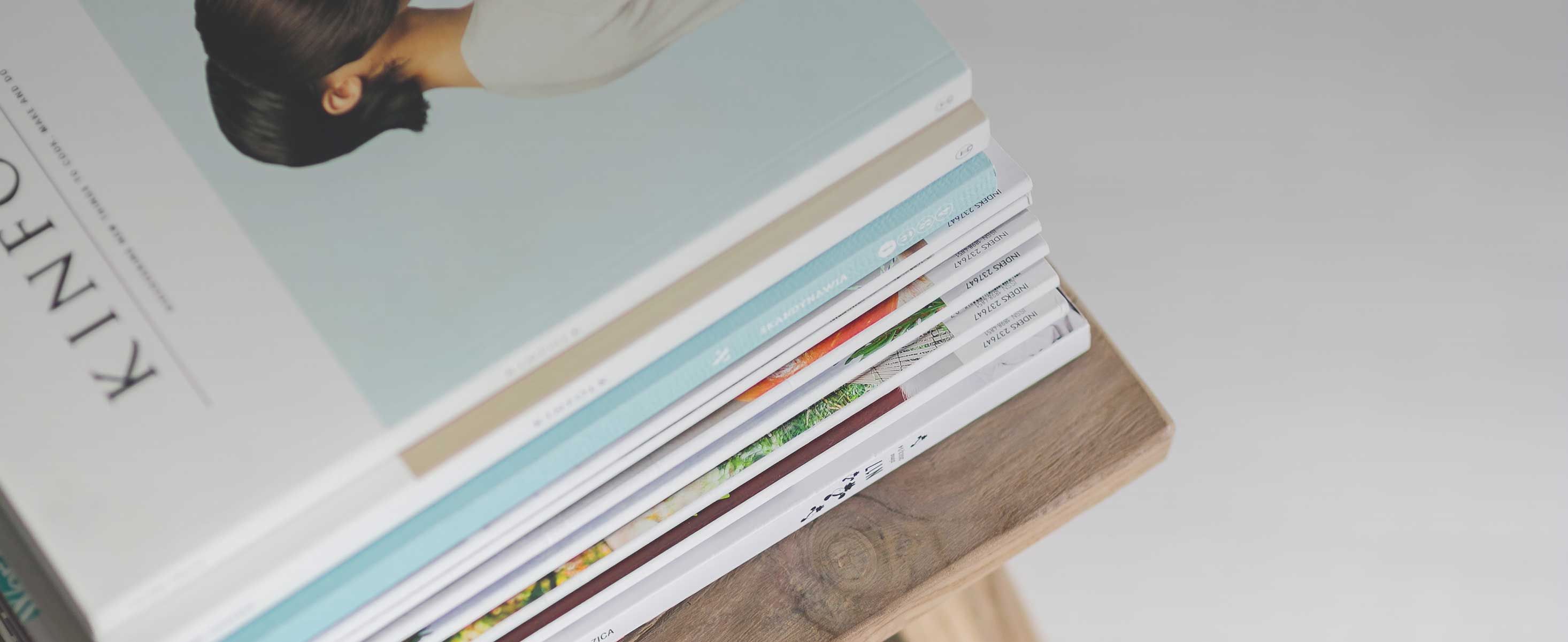
6 minute read
Our last edition
Did you miss our February 2023 edition? If so, don’t panic!
You can still read all of the great quality content that we published last month on our App – which you can download from Apple Store, Google Play or online at: https://magstand.com/petfood – with the latter platform granting you the opportunity to see all of our back editions on the screen of your desktop computer.
What you may have missed…
which we report upon in this edition.
Both Thai expo centres are exceptional and the ’Sky Train’ (which should be completed to the Impact Centre by 2025) ensure that visiting Bangkok is a must for everyone working in the petfood manufacturing sector. Note: Please don’t overlook the Victam Asia event, which also includes Health and Nutrition Asia, at this time next year - from March 12-14, 2024.
In this edition
I’m pleased to see our Petfood Tech Editor Joseph Kearns focuses his editorial on the IPPE event from January in Atlanta, USA which gave him an opportunity to meet with extruder manufacturers and his attendance at GEAPS (The Grain Elevator and Processing Society) which took place in Kansas City in the USA in the closing days of February to meet with those in the grain sector handling materials that eventually end up in petfood processing.
Our Petfood Nutrition Editor, Professor Simon Davies has also been travelling extensively and joined our team at VIV Asia 2023 this month.
His editorial focuses firmly on the importance of the amino acid Taurine, a crucial ingredient in maintaining eye health in cats.
Professor Davies’ contributions each month are greatly valued by those who formulate petfood diets, especially when it comes to managing not only the health of our pets but also the avoidance of likely conditions that could come about if overlooked in the formulation process.
Besides our news section we carry features on Vegan Dog Foods, Insect-based Petfood and reasons to include soy in pet diets before reviewing the right nutrition of pet rats.
We have our regular training and troubleshooting pages followed by our Production Focus Sector and Industry Profile - this time it’s the PLP company, which specialises in powder and liquid applications in the production process, that we feature from Italy.
We have our show report section and Victam Insights before concluding with an interview featuring Thomas Kaeser of the 100-year-old German company Kaeser Kompressaren. It’s fascinating to learn about this important company and the man at the helm!
Enjoy this edition!
puppies are small balls of adorable nightmares. The teething process for puppies varies from each breed and their individual health but the average timeline begins and ends roughly between the ages of 3 to 8 months. This article looks into the discusses about best ways to feed puppies when they are teething.
Soothing your Puppy – Teething and Dental by Shannon Parsons, magazine With sharp little teeth and their playful attitude,
International Petfood
To read more, go to: https://flickread.com/edition/html/index.php?pdf=63c7dd25c3c64#18
The year is continuing with a fever regarding attendance at trade shows. Already this year having attended the IPPE in Atlanta and the GEAPS show in Kansas City it appears the attendance is up as people are excited to be out and moving among friends and colleagues.
The IPPE show or poultry show as well as the GEAPS show covers many areas for grain and material processing and handling, many used in the petfood industry. Visiting with a number of suppliers it became obvious that new innovations and interest are at an elevated level. Some of the companies visited with possible follow up articles about their advancements in future issues include AGI: supplier of solutions and systems for storage, handling, structures, processing and controls for all types of feed and food industries. They have announced supply and design of the complete lines for pet food production. Extruder suppliers included Marel (Wenger and Extru-Tech), Famsun, Andritz, Ferraz and Buhler were pleasant to meet and see what is new. Other suppliers with related goods such as lab equipment, plant cleaning services and products, roller mill grinding and many others were on display. Specific follow up articles are intended. GEAPS being a material handling show had many interesting exhibitors from magnets, sifters, pneumatic systems, buckets, belts and many others of which most are in your standard pet style feed plant. Follow future issues for articles on these exciting topics as well.
Joseph P Kearns Editor, International Petfood Magazine
No set regulated levels of fresh meat protein or fat for these different styles of products. It is known that increases in liquids and or fats in the extrusion process reduces friction in the extruder barrel thus less expansion and less cook. This is where the shear parameters come into play, also discussed as the specific mechanical energy inputs into the system for that formula style. The other factor is the thermal energy inputs also being modified when petfood fat and meat inclusion levels change.
Topics of the month center around flexibility, vacuum coating, extrusion shear parameters and baked treats. With regards to baked treats, their basis goes back to some of the originally sold cooked petfoods which were typically baked scraps from the various baking industries, bread, cookies and crackers. The other topics amazing fit nicely together as they interrelate. If you don’t have the flexibility to control the shear parameters or energy input then getting the right cell structure for vacuum coating is doubtful.
When discussing flexibility in petfood production product appearance and formulation immediately come to mind. When walking down the petfood aisle what do you see? A wide arrange of product shapes and formulas for various dogs, cats and other pets and their stages of life. Formulas having a big impact on the petfoods for various dog and cat conditions. What is the major function of the extrusion process, cook the formula and as formulas vary the style and type of cook also can vary. You might have to get extreme in formula changes but usually some sort of mechanical change or running conditions are needed for a flexible processing facility to make a wide range and styles of product. Larger producers might have a line for each product they sell while the mid-range and smaller producers need production line flexibility.
Making a simple brown and round kibble is usually the easiest to produce as they would have a lower protein higher starch content thus easy to expand and coat. In this case a basic barrel with lower restriction and high production. As formulas change and more meat and fats are added in the formula and passed through the extruder, single or twin, then the cook level or energy input or amount of shear needs to increase. The industry does not have a set of rules to define the different product types we see in the market, premium, supper premium or ultra-premium, it is simply advertising.
Looking at fat inclusion into the extruder for example, low level inputs or in the area of 7 to 8 percent total fat is usually just the fats existing in the ingredients selected. When adding fat as a liquid pumped in the level can be increased to about 12 percent before any effects are seen in the product. Above 12 percent in many cases the product extruded will start to get heavier in density as the amount of fat added is limiting expansion. The expansion rate reduces as the fat level continues to increase. At about 22 percent total fat in the extruder expansion starts to become more difficult. Up to this point most changes to the extruder would to be restrict the die flow yielding more pressure in the extruder barrel. Development of flow restriction valves at the discharge end of extruders have allowed for this to occur while running. If expansion or the cook desired is not achieved as fat and meat levels increase, then extruder components can be changes to increase shear and retention time in the barrel. Keep in mind restriction to flow increases the shear or SME input in the extruder barrel. In single screws these include screw design and or segmented lobes. Twin screws are similar but designed for twins, 2 sets of lobes or cut flight screws and other possible elements. High meat and fat inclusion levels might require multiple disruption zones along the barrel greatly assisted by variable frequency main drives.
Thermal energy inputs started out by simply preconditioning ingredients to bring them up to temperature and moisture before the extruder barrel. Years of development has shown this to be an important step in the process for high-capacity high yield production over many hours without any ill effects. As formulas changed so did preconditioning to improve mixing, retention time, meat inclusion, cook levels, consistency and controlled temperature at the discharge before the extruder as well as total control of liquid inputs.
Let’s review the use of vacuum coating. First used in aquatic feed production so as to increase the total fat in finished pellets. The situation soon developed that the increasing coated oil did not stay in the kibbles. This is when the technology and understanding of SME and or friction in the extruder barrel coupled with all the other production aspects including water and steam added so as to control the kibbles cell structure to hold the oil. Large cells give up the oil easier than a fine cell structure kibble.
As a final note, systems now exist that take all of these years of developments and technology into account and build production equipment that fits the needs of today’s market, less cereal grains, higher meat, fat and vegetables with controlled cook levels for bacteria control. This is the approach for balancing of thermal and mechanical energy inputs for the modern day petfood production requirements.
Professor Simon Davies Nutrition Editor, International Petfood